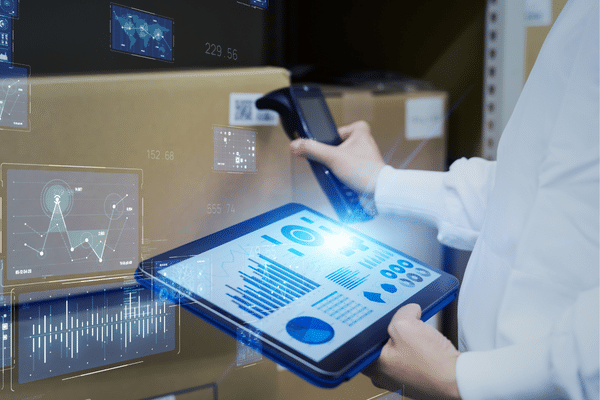
トヨタ自動車をはじめNECなど、近年ではモノづくりの世界をメインにさまざまなデジタル技術を駆使したデジタルエンジニアリングの導入例が増えています。
デジタルエンジニアリングでは、実際にモノを作る前に、デジタル技術によってコンピュータで商品の試作ができるため、それをクライアントなどと共有して要望のすり合わせを行いながら、試作を元にシユレーションと検討を重ね、解決すべき課題をクリアしていくことができます。そのため実物ベースより時間を短縮でき、コストも抑えられます。
デジタルエンジニアリングはDXを進める上でも重要な考え方であり、その波はあらゆる業界に広がると考えられます。なぜ現代ビジネスで必要とされるのか、導入背景やメリット・デメリットを確認していきましょう。
目次
デジタルエンジニアリングとは?現代ビジネスにおける必要性
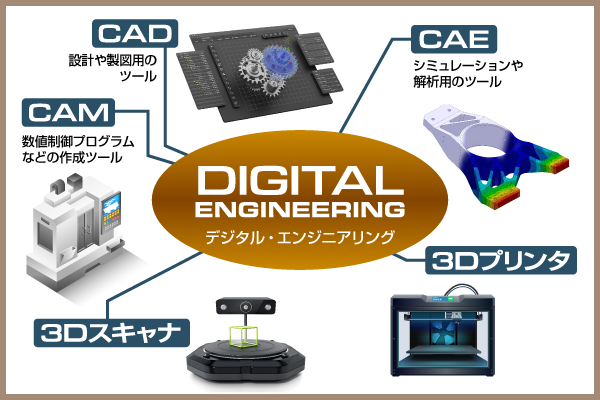
デジタルエンジニアリングとは、製造業を例に説明すると、設計ツールとして使われているCAD(Computer Aided Design)や、強度や機構検証を行うCAE(Computer Aided Engineering)、切削加工用のプログラムを作成するCAM(Computer Aided Manufacturing)、他に3Dプリンタや3Dスキャナーといったさまざまなデジタル技術を駆使してモノづくりを行うことです。
モノづくりの世界では、3D技術を用いて、設計物の形状をコンピュータ上に立体物としてデジタル試作し、組み立て検証や干渉チェック、質量や重心の確認、強度検証や熱解析などのシミュレーションを行います。そうすることにより実物を作ってからの手直しをできる限り少なくし、コストと時間を削減することが可能となります。それにより業務の効率化と品質向上が図られるのです。
<図>
・3Dプリンタ
・3Dスキャナ
・CAD(設計や製図用のツール)
・CAM(数値制御プログラムなどの作成ツール)
・CAE(シミュレーションや解析用のツール)
デジタルエンジニアと聞くと、大企業や最先端ビジネスをイメージするかもしれませんが、今やデジタルエンジニアリングは製造業に限らず、重要文化財を3Dスキャンしてデジタル保存したり、人体を3Dスキャンして、その患者にぴったりと適合した義肢装具を設計したりなど、さまざまな分野で幅広く活用されています。デジタルエンジニアリングを導入しない組織は競争力を失うリスクがあると言えるでしょう。
デジタルエンジニアの役割
デジタル技術の発展によって、製造業では業務を最適化できるようになりました。技術革新が進む中、モノづくりにおいて切望されているのが、デジタル技術を自在に駆使し、QCD(Quality:品質、Cost:コスト、Delivery:納期)を向上させて、安全で購買意欲をそそる製品を生み出せる「デジタルエンジニア」です。
デジタルエンジニアの役割は、先述したようなデジタル技術を使用して製品を設計および開発することです。これにはモデルとシミュレーションの作成、データのキャプチャも含まれます。デジタルエンジニアは、新しいソフトウェアプログラムやアプリケーションの開発を担当する場合もあれば、製品の製造に関わることもあります。
デジタルエンジニアの業務には以下が含まれます。
- コンピュータ支援技術を駆使した製品の設計と開発
- モデルとシミュレーションの作成
- データのキャプチャ
- 新しいソフトウェアプログラムまたはアプリケーションの開発
- 場合によっては、製品の製造
日進月歩のデジタル技術によって、デジタルエンジニアが取り組むべき業務や期待される役割も日々拡大しているのです。
製造業以外にも広がるデジタルエンジニアリングの波
先述したように、デジタルエンジニアリングの波は、すでに製造業以外の業界にも広がっています。
・ドローンを使った交通インフラのデータ収集や整備
・3Dスキャナによる医療器具の設計
・3Dプリンタによる服飾や菓子製品の型製作
近年では価格競争が激化した影響で、ドローンや3Dプリンタなどの低価格化が進んでいます。他のIoTや3D技術についても、低価格化が進むことは十分に考えられるでしょう。
つまり、ビジネスに導入するハードルが下がっているので、デジタルエンジニアリングの波はさらに広がる可能性があります。
デジタルエンジニアリングに欠かせない「3D CAD」
数あるツールの中でも、「3D CAD」はデジタルエンジニアリングに必須と言われます。前述のCAMやCAEをはじめ、現代ビジネスでは3D CADで作成したデータをもとに使用するツールが多いためです。
3D CADは設計または製図用のツールとして有名ですが、細かく見るとさまざまな活用方法があります。
・仕様書の作成
・製品の構想設計
・製品の詳細設計
・加工方法のシミュレーション
・CAEを活用した検証やテスト
上記のように、3D CADは製品の構想段階から設計、開発、加工、検査まで活用できるツールです。導入範囲は企業によって異なりますが、業務効率化はもちろん品質向上やトラブル防止、コストカットなどにも役立つでしょう。
そのため、モノづくりにデジタルエンジニアリングを導入する企業は、3D CADに関する知識をつける必要があります。
3D CADの導入は人材育成が最優先
3D CADは活用シーンが多いツールですが、使いこなすには高度な知識とスキルが求められます。 専門の人材育成サービスや産学官連携の講座があることから見ても、知識・スキルの習得は容易ではありません。
そのため、3D CADの導入では「人材育成」に力を入れる必要があります。どのような育成方法があるのか、以下で一例を紹介しましょう。
・従業員にセミナーや講座を受講させる
・専門のサービスでカリキュラムを組んでもらう
・外部から講師を招へいする
・すでに知識やスキルを備えた人材を採用する
参考として、3D CADの通信教育は短いもので2ヵ月程度のカリキュラムです。実務レベルの知識をつけるには、さらに多くの勉強時間がかかる可能性もあるので、人材育成には最優先で取り組みましょう。
デジタルエンジニアリングを実現させるポイント
デジタルエンジニアリングを導入するには、生産プロセスを根元から見直す必要があります。従来のプロセスにツールを組み込む方法はありますが、モノづくりの仕組みが複雑化するとかえって負担が増えてしまいます。
業務のムリ・ムダ・ムラを省くためにも、プラン策定の前に実現のポイントを押さえておきましょう。
ポイント1. 従来のプロセスにこだわらない
従来のプロセスにこだわると、デジタルエンジニアリングを導入しても業務効率は上がりません。例えば、製品の構想設計を2D技術で行い、詳細設計を3D CADで行う場合は、3Dデータへの変換が必要になります。
このような状態では従業員に負担がかかるため、生産プロセスは徹底した見直しが必要です。 3D技術への完全移行が難しい場合であっても、変換が容易な2Dデータを用いるなどの工夫を考えましょう。
ポイント2. 導入目的を明確にする
業務のムリ・ムダ・ムラを省くには、最初に導入目的を明確にする必要があります。分かりやすい目的設定をするために、以下の2W1Hをベースとして考えましょう。
What:導入によって何をつくりたいのか、何を達成したいのか?
Why:なぜつくる必要があるのか、達成する必要があるのか?
How:どのような方法で目的を達成するのか?
また、生産プロセスが大きく変化すると、従業員は不安を抱えることが予想されます。そのため、以下の項目も明確にし、しっかりと現場に共有することも重要です。
効果:ミス削減や品質アップなど、具体的にどのような効果があるのか?
役割:どの業務に導入し、それによってプロセスがどのように変わるのか?
運用:誰がどのタイミングで、どのように評価をするのか?
ここまで明確にすれば、導入すべきツールや範囲を見極めやすくなります。
ポイント3.「全体最適」をベースに計画を立てる
一つの生産プロセスを変えると、現場だけではなく他部門にも影響が生じます。例えば、設計部門に3D CADを導入する場合は、製造部門も3Dデータに対応しなければなりません。
つまり、デジタルエンジニアリングに他部門との連携は欠かせないので、全体最適のプランを立てる必要があります。 オフィスも含めたすべての業務を見直し、部門間で情報・データをスムーズに伝達できる環境を整えましょう。
ポイント4.「4Cサイクル」の連携を意識する
4Cサイクルとは、4つのツールを活用したモノづくりのことです。3D技術を活用したデジタルエンジニアリングでは、以下のツールを軸としたプロセス設計が有効とされています。
CAD(Computer Aided Design) :設計や製図
CAM(Computer Aided Manufacturing):制御プログラムの作成
CAE(Computer Aided Engineering) :シミュレーションや解析
CAT(Computer Aided Testing) :製品性能や特性の検査
当然ですが、すべてのモノづくりに対応できる生産プロセスはありません。製品ごとに生産プロセスを分けたり、複数の工場で対応したりする例もありますが、これらの方法では莫大なコストがかかってしまいます。
その点、4Cサイクルの連携を調整する方法は、低コストで一定の効果を期待できるため、中小企業にとっても現実的な手段です。 見直すことが難しい生産プロセスが存在する場合は、使用するツールや人の連携強化に取り組みましょう。
デジタルエンジニアリングの事例
不安定な国際情勢や自然災害、働き方改革など、不確実性が高まる環境変化の中において、日本の製造業はデジタル技術の徹底的な推進が不可欠となっています。こちらでは、注目すべきデジタルエンジニアリングの事例をご紹介します。
デジタル化で長い待ち時間と注文の煩雑さを解消〜マクドナルドの事例
世界各地で3万6000店舗超を展開する飲食チェーン・マクドナルドでは以前から、注文システムが国や地域ごとに異なり、利用者にわかりにくい仕様であることが悩みの種でした
マクドナルドがデジタル技術の導入に乗り出すことになったのは、競合他社がデジタル活用を推進したことで多大な成果を遂げていることに加え、UberEatsなどのデリバリープラットフォーマーが台頭したことで、飲食業の競争環境が劇変したためです。
そこでマクドナルドは、デジタルエンジニアリング企業のGlobalLogic社(本社・米国)と組んで、全店舗で一貫性のある顧客体験を提供するために、利用者の購入態度や店員の対応について世界各国で調査を実施しました。その結果、利用者は長時間待ったり店員に詳しく説明せずに、どこの店でも自分のペースと好みで商品をカスタマイズできるサービスを求めていることが判明したのです。
結果を受け、マクドナルドは世界共通の注文ルールを設定し、それに基づいたモバイルアプリや店内のキオスク(セルフオーダー端末)を世界中の店舗に設置しました。デジタル機器に蓄積した過去の注文情報を基に、AIがパーソナライズしたメニューを提案するなど利用者に選ぶ楽しさを提供しつつ、接客のオペレーションも改善することができたため、結果的に、デジタル化に着手した2017年以降、売上減少には歯止めがかかっています。
AI技術で学習者の習熟度に適したコンテンツを提供〜ピアソンの事例
教科書出版事業を手掛けるピアソン(本部:英国)は、デジタル技術の発展により、紙の本の販売だけでなく、デジタル技術を駆使した新サービスを提供する企業が台頭する状況に直面し、その流れに乗り遅れまいと感じていました。競争力向上のためにはデジタル化への舵取りが必須と考えた同社は、ビジネスモデルの再構築に着手しました。
提携したGlobalLogic社がピアソンのステークホルダーと議論を重ねた結果、「利用者の習熟度に応じた教育コンテンツを提供する」事業が待たれている。これによりピアソンは学習プラットフォームへの改修に取り組み、機能の変更や追加を迅速かつ柔軟にできるマイクロサービスベースという開発技法でそれを実現させました。
具体例を挙げると、ピアソンが提供しているAI技術を活用した英語テストは個々の学習者の進捗状況や習熟度を追跡し、リアルタイムでフィードバックを与えることで、利用者に合わせたテスト対策を行い、より良い結果を出しています。加えて学習者が好きな時に好きな場所で学べる教育サービスを提供することで、ピアソンは成長を果たしたのです。
デジタル推進でモノづくり全体のプロセスを効率化〜北川鉄工所の事例
北川鉄工所(本社・広島)は、金属素形材事業、産業機械事業、工作機器事業の3本柱で、日本のモノづくりを支える企業です。グローバルかつ持続的な成長に向けてDXを推進しており、製品開発・設計から製造に至るまで3D CADを起点とする変革に取り組んでいます。
同社は3D CAD以外にも、CADデータ管理用PDMを採用し、技術情報を全社で共有するためのPLMはNECのObbligatoを最新版にバージョンアップすることに決定しました。モノづくりの基準を「図面」から「3Dモデル」へ変更し、すべてのプロセスの効率化を図っているのです。
得られた成果の一つとしては、顧客と細かな要件のすり合わせが必要で受注までの過程が長期化しがちな産業機械事業で、直感的に仕様を把握できる3Dモデルを使ってコミュニケーションを取り合うことで、顧客と認識を合わせやすくなり、受注までのリードタイムを短縮できるようになりました。
それ以外にも、ベテランでも約4日かかっていたプログラミングが3Dモデルを基にすることで自動化が進み、若手が約4時間で完了できるようになるなど製造プロセスの短縮にも貢献しています。
デジタルエンジニアリングチェーンの構築が成功を左右する
デジタルエンジニアリングは、社内連携だけを強化する方法では実現できません。各部門はもちろん顧客などのステークホルダーとも連携を取りながら、全体で「デジタルエンジニアリングチェーン」を構築し、モノづくり・提供サービス全体を効率化する必要があります。
例えば、製品の金型を外注している場合は、外注先に3D図面データを共有するだけで、コミュニケーションの質とスピードが上がり、ひいては金型の生産スピードや品質も上がるのです。販売店に対しても、機能のシミュレーション結果を共有すれば、消費者へのアプローチ方法が変わるかもしれません。
また、学習プラットフォームの場合は、AI技術を活用したテストで各学習者の理解度を追跡し、紙の教科書では不可能なリアルタイムでのフィードバックを与えることで、利用者のテスト対策を行い、より優れた学習効果を生み出しています。
デジタルエンジニアリングチェーンはただ構築するだけではなく、情報共有の流れやスピードまで意識することが重要です。ステークホルダーの環境も意識しながら、スムーズに情報のやり取りができる仕組みを考えましょう。
デジタルエンジニアリングで導入を考えたいツール
上記で紹介した4C(CAD・CAM・CAE・CAT)以外にも、デジタルエンジニアリングに役立つツールはあります。例えば、製品ライフサイクルの管理ツールを導入すると、プロジェクトのスケジュールや部品表、法規制などの関連情報をデータとして一元管理できます。
具体的にどのようなツールがあるのか、4C以外で検討したいものを確認していきましょう。
モノづくりのあらゆるデータを一元管理する「PLM」
PLMは、製品ライフサイクルで発生する情報をデータ管理できるツールです。導入するものにもよりますが、設計や生産、調達、物流、販売などが対応領域に含まれます。
1990年代にはすでに国内でも導入されており、モノづくりにおけるデータ収集や追跡、データ同士の連携などに活用されています。製品情報や取引先情報はもちろん、ツールによっては要件や法規制に関するデータも管理できるので、ビジネスリスクを抑える効果も期待できるでしょう。
開発・設計に特化したデータ管理ツール「PDM」
PDM(Product Data Management)は「製品情報管理システム」とも呼ばれる、開発・設計プロセスに特化したデータ管理ツールです。PLMに比べると対応領域は狭いものの、モノづくりに関する専門的なデータを管理できます。
・企画データ
・仕様書
・3D CADで作成した図面
・部品表(BOM)
・最終設計データ など
一般的なPDMには検索機能が備わっており、 システムに保存されているデータを瞬時に参照できるため、図面や仕様書などの再利用も可能です。また、事前にアクセス権限を設定しておくと、データ共有の必要がある人に対してのみ公開ができます。
社外との連携強化に役立つ「GIS」
地理情報システムとも呼ばれるGIS(Geographic Information System)は、地域ごとに顧客情報などをマッピングできるツールです。導入するものによっては、ほかにも以下のようなデータを管理できます。
・顧客や取引先の住所
・地域ごとの販売データ
・天候に関するデータ
・事業に活用できる物件の情報
・仕入れや発注に利用できる店舗データ など
GISは社外との連携に利用できるため、デジタルエンジニアリングチェーンの構築に役立ちます。また、顧客データを分かりやすく登録しておくと、エリアマーケティングにも活用できるでしょう。
製品が安全で故障しないことを保証する「FEA」
FEA(Finite Element Analysis)は「有限要素解析」と訳され、製品やシステムの構造または性能における潜在的問題・既知の問題を見つけ出して解決することを目的にバーチャル環境で行われるモデリング手法です。
FEAソフトウェアは、製品が安全でストレスを受けても故障しないことを保証するのに役立つため、デジタルエンジニアにとっては欠かせないものとなっています。FEAが最も利用されているのは航空、生体力学、自動車業界ですが、ほかのさまざまな業界でも広く活用されています。
立体モデルを再現しより良い建物づくりに活用するシステム「BIM」
BIM(Building Information Modeling)は、コンピューター上に現実と同じ建物の立体モデル(BIMモデル)を再現して、図面に慣れていない人にもわかりやすく「見える化」し、コミュニケーションや理解を向上させ流ことで、早期の合意形成だけでなく、関係部門とスムースに共通認識を保てるよう活用するシステムです。
BIMモデルは、壁や柱といったオブジェクトの集合体なので、建材パーツには幅や奥行き、高さに加え、素材や組み立てる工程などの情報も盛り込め、図面以外の多くのデータを引き出すことが可能です。構造体の入力、設備機器も再現可能で、設備機器には品番、メーカー、価格などの詳細情報も入れられるため、メンテナンスや資材管理にも役立ちます。
デジタルエンジニアリングで注意したい3つのリスク
デジタルエンジニアリングの実現を急ぐと、かえって業務効率の低下やコスト増を招きます。新たなツールの導入にはメリットがある反面で、デメリットやリスクも潜んでいるため、慎重に計画を立てなければなりません。
ここからは、デジタルエンジニアリングで特に注意したいリスクを解説します。
デジタル人材の獲得競争をする覚悟が必要
IT人材の中でも、IoTや3D技術に長けている人材は数が限られます。日本はすでにIT人材不足に直面しているため、デジタルエンジニアリングを目指す上で人材獲得競争は避けられません。
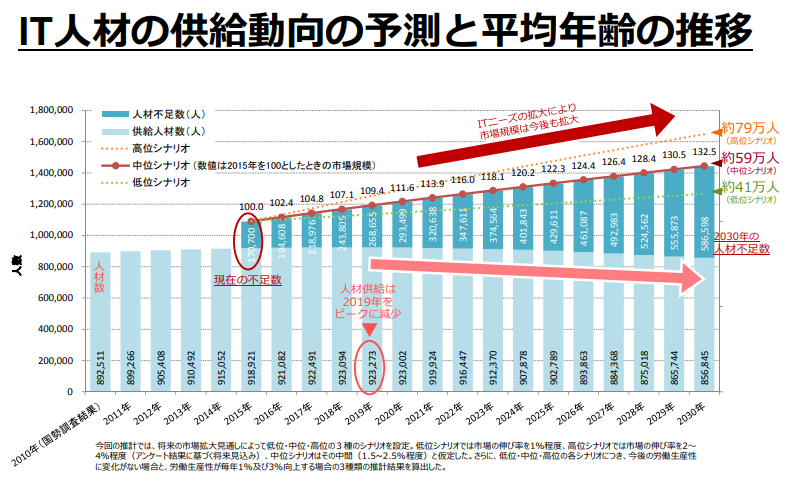
効率的にデジタル人材を獲得するには、年功序列のシステムを撤廃し、実力主義の人材評価システムを導入するなどの施策が必要です。また、獲得した人材が離職しないように、労働環境や社内コミュニケーションの改善も求められるでしょう。
人材不足によって内製化が難しい場合は、外部パートナーや人材派遣サービスを利用する方法も一つの手です。コストはかかりますが、現在では高度なシステムエンジニアやプログラマーなどの派遣も受けられます。
ただし、これらの方法はあくまで一時しのぎなので、自社でデジタル人材を獲得・育成する施策も考えましょう。
デジタル化を進めるほど情報漏えいのリスクは高まる
デジタルエンジニアリングチェーンの範囲を広げるほど、情報漏えいのリスクは高まります。ステークホルダーとの連携強化は重要ですが、企画案や機密情報などが流出すると、大きな損失を被るかもしれません。
総務省の情報通信白書(令和2年版)によると、調査対象となった組織のうち半数以上でセキュリティ事案が発生しています。
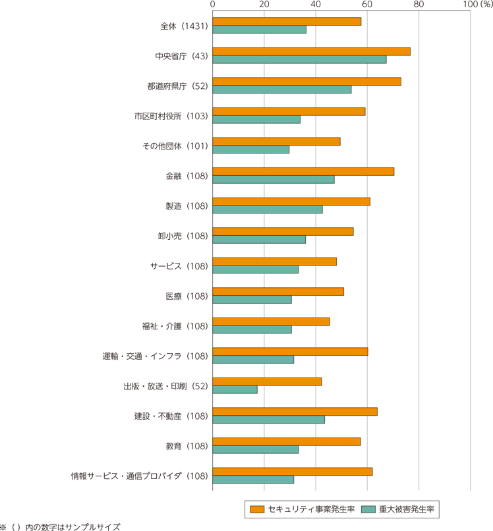
情報漏えいは珍しいリスクではないため、以下のようなセキュリティ対策を徹底しましょう。
・システムにパスワードを設定する
・保存するデータを暗号化する
・アクセス権限を設定する
・アクセスログが記録されるツールを選ぶ
・セキュリティ対策ソフトでサイバー攻撃を防ぐ など
上記のほか、ステークホルダーに提供する情報を減らしたり、信用できる取引先に絞ったりする方法も効果的です。取引先などとコミュニケーションを図りながら、デジタルエンジニアリングチェーン全体のリスクを抑えましょう。
アナログ的なアプローチが求められるシーンもある
モノづくりの生産現場では、アナログ的なアプローチが必要になるシーンも多くあります。
例えば、在庫の整理や整頓、設備の清掃が行き届いてなければ、いくらデジタル技術があっても業務効率は上がりません。 ビジネスモデルを練る際にも、アイデアを従業員に聞き回ったりメモを取ったりなど、デジタル面以外でのアプローチが必要になるでしょう。
この部分を誤解していると、重要な意思決定までデジタル技術に任せてしまう恐れがあります。特にデータ管理は、セキュリティリスクを防ぐためのルール作りや共有、社内での意識統一をしていることが前提です。
アナログ的な課題をデジタル技術で解決することは難しいので、どのようなトラブルにも対処できるチームや仕組み作りにも取り組みましょう。
デジタルエンジニアリングは社内外の協力が欠かせない
デジタルエンジニアリングの実現には、従業員を含むステークホルダーからの協力が欠かせません。社外も含めた全体最適が求められるため、従来のプロセスにこだわらず、新しいモノづくりの形を構築するという意識を持つことが大切です。
また、効率的に生産プロセスを変革するには、3D CADなどのデジタルツール導入は必須なので、どのくらいの予算を割くのかも十分に検討しなければなりません。加えて、IT人材不足の日本においてIT技術や3D技術を熟知した人材の獲得は困難です。そのため、社内での育成も意識しながら、育成プランを考える必要もあるでしょう。
【こんな記事も読まれています】
・国内製造業の再生を狙うINDUSTRIAL-Xが推進する[ESG×DX]時代の戦い方
・製造業における購買・調達業務とは?課題の解決方法も紹介
・サプライチェーン排出量はなぜ注目される?算定方法も含めて紹介