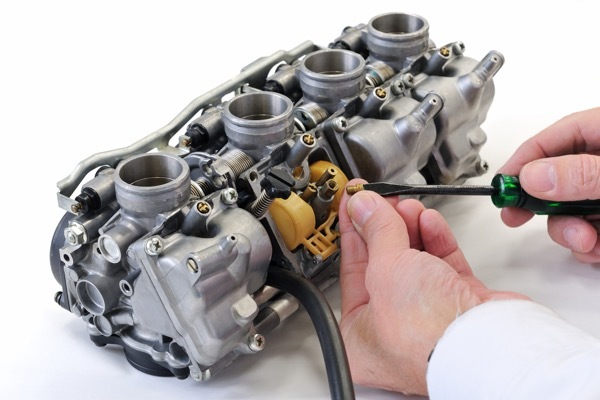
オーバーホールを適期に実施できれば、機器の寿命を延ばしたり精度を回復したりすることができます。新たな機器を購入せずに済むため、経済的な恩恵を受けられるでしょう。
本記事では、オーバーホールを行うメリットとともに、デメリットや具体的な手順について解説します。デジタル技術を用いてオーバーホールを効率化する方法も紹介していますので、導入の際は参考にしてください。
目次
オーバーホールとは?

オーバーホールとは、設備や機器を分解して行う大規模な点検のことです。日常的に実施する点検とは異なり、設備を細かく分解して洗浄したり劣化した部品を交換したりして徹底的に点検します。
オーバーホールを行うのには手間がかかりますが、適切に実施することで設備の寿命延伸や精度回復などの効果が得られます。
オーバーホールというと時計のメンテナンスを指すことも多いですが、本記事では製造現場の設備点検に焦点を当てて解説します。
修理との違い
オーバーホールと修理の大きな違いは、故障の前に行うものか、後に行うものかという点です。
基本的に、修理は故障した後に行います。修理の目的は、機能しなくなったものが再度役割を果たせるように直すことです。一方、オーバーホールは故障する前に行います。オーバーホールの目的は、現在機能しているものが、継続して役割を果たせるようにすることです。
メンテナンスとの違い
オーバーホールとメンテナンスの大きな違いは、点検の規模です。どちらも故障を防止するための予防保全であることに変わりはありませんが、頻度や工数が大きく異なります。
一般的にメンテナンスは、部分的な修理や点検のため日常的に行います。設備の規模や特性にもよりますが、メンテナンスは毎日行うこともあります。メンテナンスでは、消耗品の交換や設備の動作確認などを実施します。
それに対してオーバーホールでは、日常的にはできないような項目まで細かく点検します。一回のオーバーホールには大きな労力とコストが必要であるため、メンテナンスのように頻繁には行いません。オーバーホールでは、設備内部の部品交換や洗浄、精度回復のための加工などを実施します。
オーバーホールと設備保全
設備保全は大きく「事後保全・予防保全・生産保全・改良保全」の4つに分類できます。オーバーホールは、その中の予防保全に該当します。それぞれの目的や保全方法は以下の通りです。
・事後保全
故障した設備や機器を直す保全方法。故障を予防することが逆に非効率であると判断される場合は、事後保全が採られる。
・予防保全
故障や停止を予防する保全方法。故障や停止を予防したほうが利益につながる場合に採られる。メンテナンスや消耗品の交換が挙げられる。
・生産保全
設備の設置から廃棄までの損失を最小限にする保全方法。故障による損失と保全費用の合計が最も小さくなるように保全方法を使い分ける。
・改良保全
設備を改良して故障や劣化を防ぐ保全方法。故障を繰り返す原因究明や材質改良により、設備自体を強化する。
事後保全は故障が起きてから対処する保全方法なのに対して、予防保全・生産保全・改良保全は故障が起きる前に対処します。一見、故障を予防する保全方法が優れていると感じてしまいがちですが、事後保全は予防コストがかからなかったり、寿命まで利用できたりするメリットがあります。
しかし、事後保全をすると突発的な対応が必要になります。予防ができないため、予期せぬタイミングで生産ラインが停止することもあるでしょう。このような特徴から、予知保全であるオーバーホールは、機能の停止が大きな損失につながる設備や機器で実施される傾向にあります。
オーバーホールを行うメリット
日常的なメンテナンスに加えて、オーバーホールを行うメリットは以下の2つです。
- 設備交換などのコスト抑制
- 使い慣れた設備・機器を継続的に使用できる
設備交換などのコスト抑制
オーバーホールを行うことで設備や機器の寿命が延び、設備交換などにかかるコストを低減できる可能性が高まります。コスト抑制によるメリットを享受しやすいのは、高額な設備や機器です。
一般的に、設備が高額になればなるほど故障による経済的な損失は大きくなります。オーバーホールを実施すれば、故障や停止の回数を低減できる可能性が高まるため、設備交換にかかる長期的なコストを抑えることができます。
使い慣れた設備・機器を継続的に使用できる
オーバーホールにより機器の寿命を延伸できれば、従業員は使いなれた設備を長く使い続けられます。設備を変更すると、システムの仕様や使い方も変わるため、従業員が覚えなければならないことが増えます。使い方が難しければ、生産性の低下も考えられるでしょう。
オーバーホールを行えば、設備や機器の寿命を延伸できるため、従業員が使用するシステムの変更は最小限に抑えられます。これにより、従業員が覚えるべきことは減り、教育コストも低減できます。
オーバーホールを行うデメリット
オーバーホールは寿命の延伸に効果的な予防保全ですが、実施することで以下のようなデメリットを被る可能性があります。
- 作業に時間がかかる
- 想定以上にコストがかかる
- 実現困難なケースがある
作業に時間がかかる
オーバーホールは設備を部品レベルまで分解して洗浄やパーツ交換を行うため、作業に時間がかかります。設備の規模や在庫の有無によって異なりますが、数ヵ月かかる場合もあります。
繁忙期にオーバーホールをしていては、生産効率の低下により経済的な損失を被ることもあるでしょう。メンテナンスのように短時間でできる作業ではないため、注意が必要です。
想定以上にコストがかかる
オーバーホールを行うのには部品の交換や大規模な洗浄が必要なため、高いコストがかかることがあります。多くの部品の交換や特殊な洗浄をした場合は、想定以上のコストがかかるかもしれません。
また、オーバーホールの実施にあたっては整備工場への搬出や精度出しなどの工程も必要です。これらの費用は、工場までの運搬コストや求める精度によって異なります。予算が限られている場合は、全ての工程を足し合わせた見積もりを取るようにしましょう。
実現困難なケースがある
必要な部品の生産が終了していたり、必要な技術力がなかったりする場合は、そもそもオーバーホールを実施できません。また、工期が想定上に長く、生産ラインを止められる期間を超えてしまった場合も実施できません。
古い設備や、特殊な部品が必要な機器をオーバーホールする場合、まずはメーカーに対応可能かどうかを確かめてみるとよいでしょう。他社にアフターサービスを引き継いでいる企業もあるため、オーバーホールの発注先には注意が必要です。
オーバーホールの頻度は4〜5年に一度
設備の規模や種類によりますが、オーバーホールは4~5年に一度の実施が一般的です。比較的容易に分解できる場合や、機器が古い場合は、3年ごとに行うこともあります。オーバーホールの実施を考えている場合は、前回の実施から4~5年を目安にしてみてください。
また、精度が低下してきたタイミングもオーバーホールの適期と考えられます。オーバーホールでは、劣化した部品の交換や機器内部のゆがみ調整を行うため、基本的に精度は向上します。最終工程で精度検査を実施している企業に依頼すれば、オーバーホールによる精度の改善を定量的に判断できるでしょう。
定期的なメンテナンス・整備が重要
オーバーホールを実施すれば部品を一新できますが、先述の通り大きなコストや時間がかかります。そのため、オーバーホールを頻繁に実施しなくてもよいような状態がベストです。
そのためには、日常的なメンテナンスや整備が重要です。例えば、5S(整理・整頓・清掃・清潔・しつけ)活動の徹底が挙げられます。5S活動は製造業で広く取り入れられていますが、時間の経過とともに従業員の認識が甘くなることもあります。
大規模な設備の場合、いずれはオーバーホールが必要になります。しかし、コストを抑えるためにも、日常的なメンテナンスや整備を徹底し、可能な限り頻度を抑えられるようにしましょう。
オーバーホールの基本的な手順
オーバーホールの基本的な手順は、以下の通りです。
- 分解
- 点検
- 洗浄
- 修理・交換
- 注油
- 組み立て
- 運転調整
手順1. 分解
まずは、設備や機器を分解します。部品レベルまで分解することで、日常的に行うメンテナンスでは見ることのできない内部の状況を確認できるようになります。
手順2. 点検
分解した部品に劣化や損傷がないかを確認します。劣化の原因が錆びや汚れであれば後述する洗浄の対象になりますが、激しい摩耗や修復不可能な損傷があれば新しい部品に交換することになります。
基本的には点検の結果をもとに必要な部品を判断するため、必要な部品の在庫がなければこの段階で発注します。在庫がない部品が必要になった場合、オーバーホール後の設備の納品が遅れる可能性があるため、注意が必要です。
手順3. 洗浄
分解した部品や機器の内部を洗浄します。年単位で蓄積した錆びや汚れは簡単に落ちないため、洗浄時には専用のブラシや化学薬品を使用します。汚れの度合いによっては、洗浄しなければ点検できない部品もあるため、分解後すぐに洗浄する場合もあります。
手順4. 修理・交換
洗浄後に加工が必要な部品は修理し、摩耗や劣化が激しい部品は新品へ交換します。修理の内容は設備の用途によって異なりますが、肉盛りや研磨などを行って設備の性能を高めます。
修理や交換にはコストが伴うため、企業によっては顧客の要望を聞いてから実施する作業を決定します。修理や交換にかかるコストが予算を超えてしまうことを防ぐためにも、点検や洗浄後に部品の交換リストを提示してもらうようにしましょう。
手順5. 注油
部品の修理や交換が終わったら、注油を行います。注油すると、摩擦による損傷や錆びを防止できるため、スライドや回転を生じる部品の寿命延伸に効果的です。
手順6. 組み立て
全ての部品が揃ったら、分解したパーツを組み立てます。組み立ての段階で注油が必要であれば、該当部分に油をさします。基本的には、配管や電装などのユニットごとに組み立てを行い、最後にパーツの全てを組み立てます。
組み立ての最終工程では、組み合わせる部品が多くなるため、それぞれの部品やパーツが持つばらつきが累積されて大きな誤差がでます。これを解消するため、高い技術力を持った熟練技術者が「精度出し」と呼ばれるミクロン単位の調整を行い、精度を向上させます。
手順7. 運転調整
組み立て後には、運転調節や試加工を行い、機器が正常に動作するかを確かめます。動作が確認できれば、顧客が求める精度で作業ができるかを検査します。運転調節で動作不良や精度不足があれば、原因を究明して修正を行います。
以上の工程が全て終了すれば、立会検査・搬出・設置を経てオーバーホールは完了です。企業によっては、オーバーホール後に一定期間の保証を設けています。万が一に備えるためにも、アフターサービスが充実している企業に依頼するとよいでしょう。
IoTやAIでオーバーホールの効率化が可能
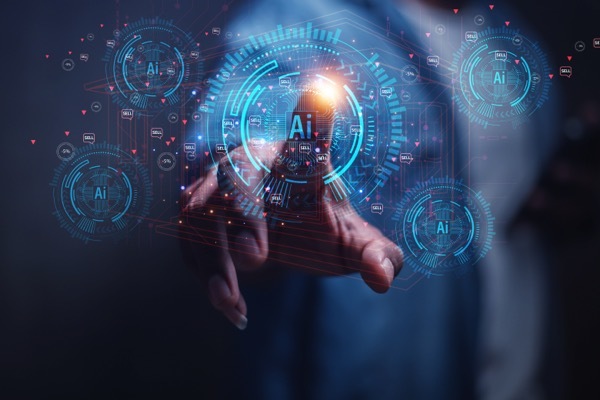
オーバーホールを行えば、設備や機器の寿命延伸や精度の向上に役立てられます。とはいえ、先述の通りオーバーホールを実施するには、大きなコストと長い時間が必要です。そのため、オーバーホールは適期に行う必要があります。
そこで有効なのが、IoT(Internet of Things)やAI(Artificial Intelligence)などのデジタル技術の活用です。IoTとは、あらゆるモノにインターネットを接続することを指します。AIとは人工知能のことで、人間の脳に近い機能を持った、学習能力を持つプログラムのことです。
IoTやAIなどのデジタル技術は、2006年頃に始まった第3次AIブーム以降、飛躍的な進歩を遂げてきました。2022年11月には、OpenAIが公開したChatGPTにより、AIが世間にも知れ渡りました。これを機に、事業へのIoT・AI活用を考えた方も多いのではないでしょうか。
IoTやAIは、すでにオーバーホールの効率化にも用いられています。これらの技術を活用して機器の故障時期を予測できれば、適期にオーバーホールを行えます。具体的には、以下のような活用例が挙げられます。
- 振動・音・温度などのセンサーによる故障前兆の判定
- 配管減肉量の推定システム導入による交換適期の判断
- 複数センサーの相互関係から破損の兆候を検知
このように、IoT・AIなどのデジタル技術を活用すれば、故障の時期が予測できるため、オーバーホールの効率を高められます。デジタル技術によって経済的な恩恵を享受できれば、さらなる設備投資が可能になり、「設備投資→経済的恩恵の享受→設備投資」の好循環が生まれるでしょう。
逆に、デジタル技術を取り入れなければ企業は競争力を失い、経済的損失を被ります。経済産業省はこれを「2025年の崖」として問題視しています。もしデジタル化が進まなければ、2025年以降には日本全体で年間12兆円もの経済的損失を被ると予測しています。
年間12兆円はあくまでも国全体の損失額ですが、経済産業省は2025年の崖を放置した企業はデジタル競争の敗者になると警鐘を鳴らしています。このような損失を生まないためには、早い段階でのデジタル化が必須です。
適切なオーバーホールは経済的なメリットにつながる
オーバーホールを適切に行うと、さまざまなメリットを享受できます。実施にはコストが伴いますが、長期的に見ると利益になる場合も多くあります。予知保全を行っている設備がある場合は、オーバーホールによって経済的な恩恵を受けられないか確認してみてください。
また、メンテナンスやオーバーホールは、AIやIoTなどの技術を活用することで効果を上げられます。工場全体のデジタル化も視野に入れながら、自社で高度な予知保全を実施できないか考えてみてはいかがでしょうか。
【注目コンテンツ】
・DX・ESGの具体的な取り組みを紹介!専門家インタビュー
・DX人材は社内にあり!リコーに学ぶ技術者リスキリングの重要性
・サービタイゼーションによる付加価値の創造と競争力の強化