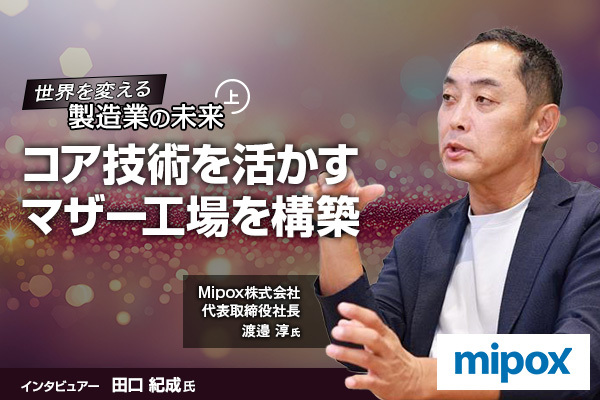
製造業のリソースが集約される、ものづくりの現場。市場や経営環境の変化を敏感に捉えつつ、絶えず改善を重ねていく場でもあります。超精密研磨分野の製品や技術を武器に躍進するMipoxはコア技術である「塗る・切る・磨く」を強みに持ち、さらなる生産性向上を目指してマザー工場の構築を進めています。
今回は、コアコンセプト・テクノロジー(CCT)取締役CTOの田口紀成氏がMipoxの本社と工場を訪問し、最先端分野である半導体の加工を行う工場の内情について渡邉淳社長にお話を伺いました。
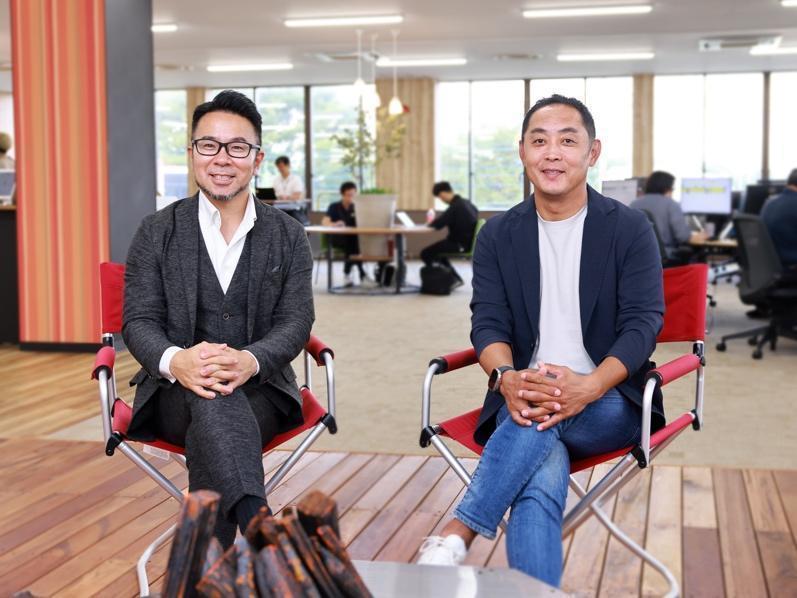
日本とアメリカの大学で学んだ後、1994年日本ミクロコーティング株式会社(現Mipox株式会社)へ入社。製造現場でキャリアをスタートし、生産技術、国内営業、海外営業を担当。その後マレーシア駐在員、米国子会社赴任を経験。主にハードディスク業界向け製品の営業に携わる。その後半導体部門長、海外支援部門長に従事。2007年取締役、2008年に先代から引き継ぐ形で代表取締役社長に就任。
2002年、明治大学大学院 理工学研究科修了後、株式会社インクス入社。2009年にコアコンセプト・テクノロジーの設立メンバーとして参画し、3D CAD/CAM/CAEシステム開発、IoT/AIプラットフォーム「Orizuru」の企画・開発などDXに関する幅広い開発業務を牽引。2015年に取締役CTOに就任後は、ものづくり系ITエンジニアとして先端システムの企画/開発に従事しながら、データでマーケティング&営業活動する組織/環境構築を推進。
コア技術「塗る・切る・磨く」で世界を変える
田口氏(敬称略、以下同) まずは、御社の事業内容をお聞かせいただけますか。
渡邉氏(敬称略、以下同) 当社は、半導体の加工に用いる精密フィルムやサンドペーパー(研磨紙)など、研磨に関する幅広い製品・サービスを提供しています。
強みにはコア技術である「塗る・切る・磨く」をベースに研磨材メーカーとして培ってきた技術とノウハウがあり、使命として「塗る・切る・磨くで世界を変える」を掲げています。このほかにも「塗る・切る・磨く」に「観る」を仲間入りさせようと、半導体測定器の開発も進めています。
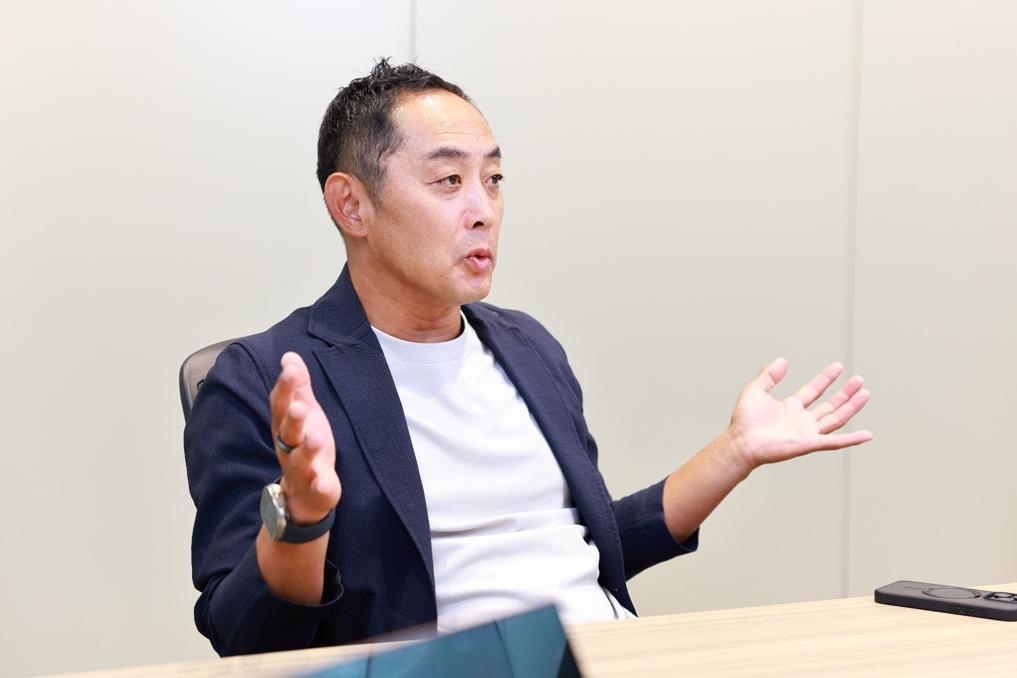
事業は、大きく分けて製品事業と受託事業があります。製品事業では研磨フィルムや液体研磨剤をはじめとする研磨関連製品を取り扱い、受託事業では製造の技術を活かして、お客様のご依頼に応じたスリット裁断や研磨加工、常温接合加工を扱っています。
製造・営業の拠点が国内外に20拠点ありまして、このうち北杜(山梨県)の工場は主に研磨フィルムの製造における「塗る」工程を、鹿沼では「切る」「磨く」の工程を行っています。2023年4月には、本社機能を鹿沼に移しました。
田口 鹿沼に工場を開設する背景には何があったのでしょうか。
渡邉 偶然、鹿沼に欲しい生産設備を見つけました。北杜事業所で使っている生産設備の「兄弟機」に当たる、「塗る」工程に使うコーターです。BCP(事業継続計画)の観点から、兄弟機を手に入れられるのは大きなメリットです。
実は、鹿沼とは全然関係ない別の地域に工場を建設する計画がありました。これまでメインの生産拠点だった北杜事業所と広島県の福山事業所が手狭になっていたので計画を進めていたのですが、ある取引先を通じて鹿沼で生産設備が売りに出されていることを知りました。最初は生産設備を移設できないか検討したのですが、無理だとわかり、工場ごと買おうとなりました。
田口 なるほど、生産設備ごと工場を引き継いだということですね。コストパフォーマンスが良かったのではないでしょうか。
渡邉 欲しかった生産設備も含め、全部で25億円ぐらいです。この工場を1棟建てようとしたら200億円でもできません。同じ生産設備を新たに購入するだけで20〜30億円かかり、設備が出来上がるまでに数年待つことになるので、良い買い物でした。
鹿沼事業所のオープン後に間もなく、本社機能も東京から鹿沼に移しました。東京には総務や人事、営業の一部を残して、20人が鹿沼に移ってきました。このほかにも北杜や福山の事業所から移ってきた従業員もいます。
「兄弟機」を発見し移転プロジェクトが始動
ここからは、Mipoxの本社に隣接する工場に場所を移し、渡邉社長と、総務担当の藤井氏に工場内を案内してもらいました。
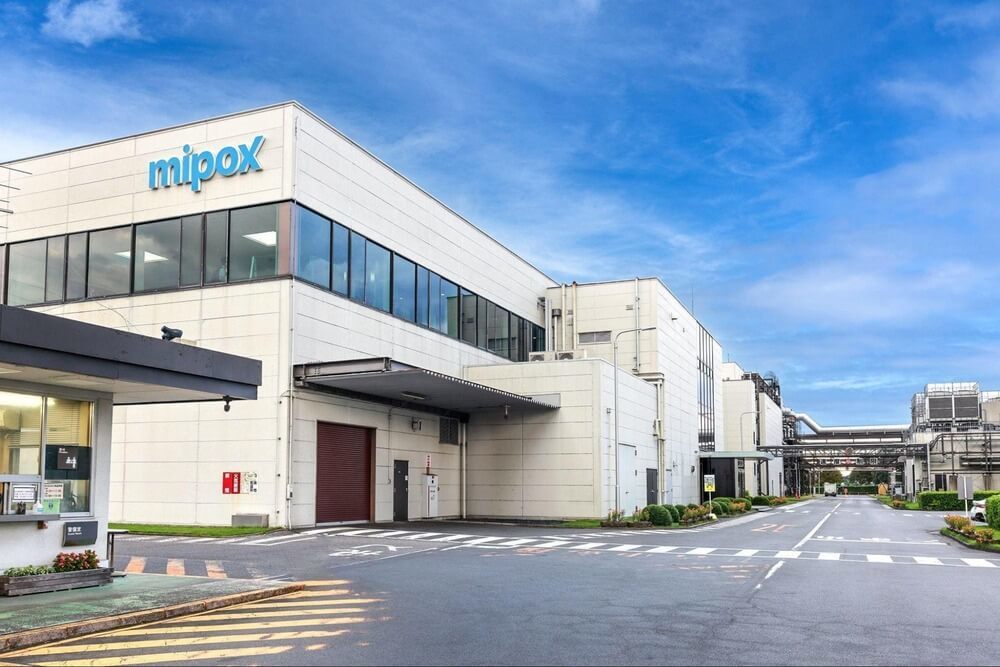
工場は東北自動車道鹿沼ICに隣接する鹿沼工業団地内にあり、工場面積は約6万平方メートル、東京ドーム1.3倍相当の広さです。2棟ある工場棟のうち、1棟にオフィスや研磨、調合・塗布・スリット工程が集まり、126人が働いています(2023年9月末時点)。
田口 高速道路のインターチェンジからも近いですし、立地も考えて移転されたのかなと思ったのですがいかがですか。
渡邉 いえ、まったく関係ないですね。ただ、下見に来たときに「あれ、俺ここ知ってる!」と驚きました。以前は当社の製品とは違うものを造っていた工場なのですが、当社製品の納入先で僕は20年ほど前に担当していて、そのときの記憶がよみがえりました。でも、鹿沼に決めた理由は兄弟機以外にはありません。
田口 探し求めているものがあったから情報が集まったのでしょう。決断したことで次の機会が生まれていきますよね。
渡邉 そうですね。細かいことよりも、遠い目標、「自分たちはここに行きたい」のほうが重要です。もうそれしか見ていません。
鹿沼事業所には、クリーンルームが設置されています。工場見学ではクリーンルームにも入るため、我々は頭を含め全身を覆う防塵服を着て顔にはマスクを着用、手にはゴム手袋をはめて、専用の靴に履き替えてエリアに入りました。
北杜事業所の兄弟機であるコーターは、ライン長約87mで、ガラスで仕切られた中に設置されています。コーターのあるエリアは、クリーンルームに入るためのエアシャワーを2度経て、到達できます。
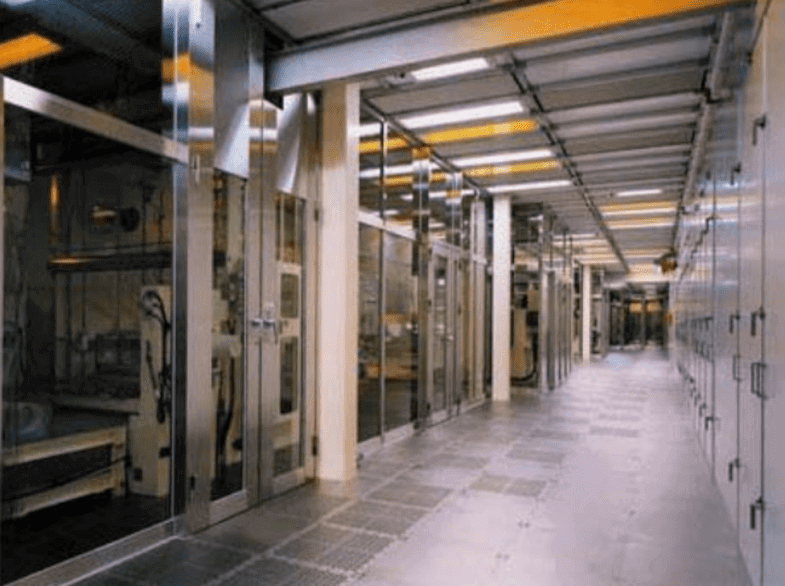
クリーンルームでは目に見えない粒子のほか、静電気も除去します。有機溶剤を扱うため、静電気の発生にも細心の注意が必要です。同機は高クリーンな環境で、製品の巻き出しから巻き取りまで、高精度の厚み制御と、低コンタミで高品質な塗布品を生産できるのが特徴です。
田口 兄弟機ということで、メリットが複数あるのでしょうか。
藤井氏(敬称略、以下同) そうですね。まったく同じ生産設備ではありませんが、同一メーカーで仕様が似ているので工程は一緒です。そのため、操作する人の飲み込みが早くなります。
エラーが出たとしても、色々なエラー事象の蓄積があるので、共通して対応できます。もし北杜とまったく違う生産設備だとしたら、BCP上はあまり意味を持ちません。このほかにも色々な使い方ができます。たとえば、量産したいときに北杜と鹿沼で同時に稼働させて、一気に短期間で作ることができます。
田口 こういう生産設備を見つけられたのは、非常にラッキーですね。
藤井 はい、そう思います。このほかにも北杜と鹿沼で連携して、当社が得意とする研磨加工や受託塗布・スリットなどの受託事業の生産能力強化にもつながります。
受託研磨や接合サービスをワンストップで提供
田口 御社の生産設備の強みは、どのあたりにあるのでしょうか。
藤井 強みは当社のコア技術である「塗る・切る・磨く」と、クリーン環境ですね。特に、半導体ウェーハのウェーハプロセッシング(研磨加工)では、各ウェーハの製造工程(研磨工程、洗浄処理、接合処理など)を一括管理した「ワンストップソリューション型サービス」を提供しています。
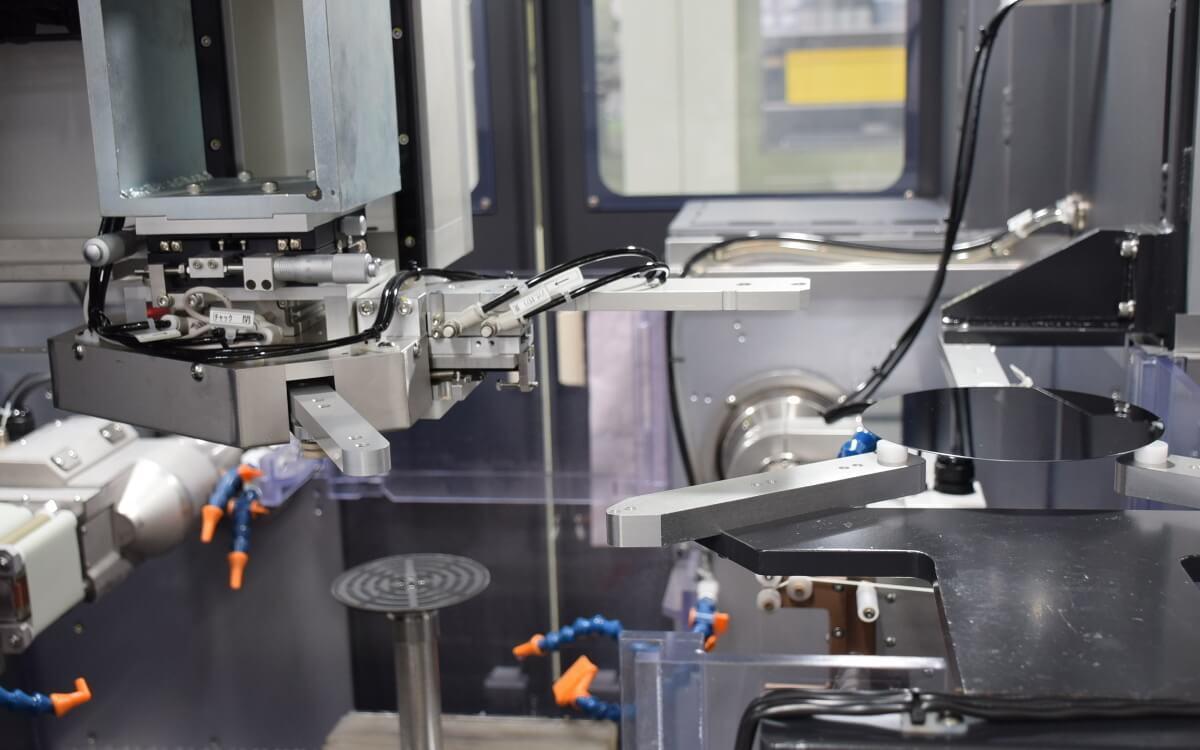
鹿沼事業所では、研磨フィルムなど自社製の研磨材や専用の研磨装置を駆使しています。単一工程のほか、半導体ウェーハの原料となるインゴットの加工からウェーハ化(基板化)まで、すべての工程に対応しています。具体的には、ポリシング(CMP)と呼ばれる研磨技術とエッジ(ノッチ)研磨、精密洗浄、常温接合です。
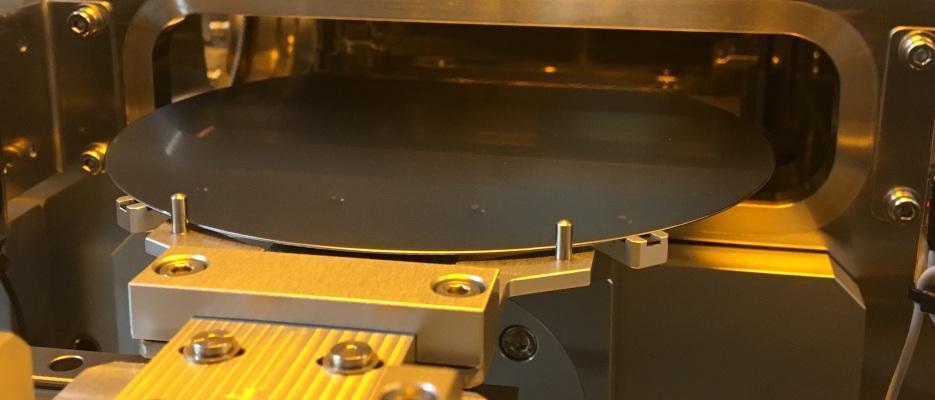
このエリアを担当するウェーハプロセス事業部の大橋氏に案内してもらいました。
田口 ウェーハ等の加工仕様は、お客様の注文に合わせるのですね。
大橋氏(敬称略、以下同) はい。そのため、案件ごとに作業の内容が違ってきます。半導体ウェーハ以外にも、他の用途向けの素材の研磨もしてほしいという注文もあります。それぞれの注文に合った加工方法をお客様に提案して、作業を進めます。表面の粗さや平坦度をいくつにしてほしいというリクエストを受け、最適な装置や加工方法を組み合わせ、仕様に合わせた形で加工しています。
田口 最適な組み合わせに至るノウハウは、御社独自のものなのでしょうね。
大橋 そうですね。装置と研磨材、それから加工の条件などが関係します。独自のノウハウや技術が当社の強みです。
田口 常温接合では、どんな作業を行うのですか。
大橋 簡単に言うと異なる素材同士を、接着剤を使わずに特殊な処理を行ってくっつける方法です。異種素材を接合して新しい特性を持つ素材を作り出します。
田口 半導体関連の工程は細かい作業がたくさんあるため、一般的なものづくりのように、目の前で最終的な製品ないしはそれに近いものが出来上がるというのとは違っています。ここでの面白さとは、どんなときに感じますか。
大橋 そうですね、半導体関連は先端技術なので、実装されるまでには長い時間がかかります。先ほど申し上げたように、鹿沼事業所では受託という性質上、使用用途が分からない製品の加工を請け負うことも多いのですが、何に使うのか想像しながら、将来の技術を一歩、先取りしているところに面白味を感じますね。たとえば、私が入社した10年ほど前に同僚が加工していた技術が、昨年くらいに花開き、大きく売り上げにつながったことがありました。
一気通貫の生産体制を支えるマザー工場を鹿沼で構築中
田口 御社が掲げるもう1つの強みであるクリーン環境は、具体的には何を指していますか。
藤井 研磨関係で同様の製品を扱う上で、当社のようにクリーンルームで作業している会社はそう多くはないと思います。研磨作業を行うのに、徹底的にクリーンにする必要性はないと考えるでしょうし、研磨するための消耗品を作るためにわざわざクリーンルームである必要はあるのか、とも聞かれることもあります。
たとえば、受託研磨で預かる製品は、お客様の工場ではクリーンルームでの作業を経ています。仮に、研磨を行う当社製品がクリーンルームを使わないことでゴミが付着していたら、お客様の製品に傷をつけてしまうことになるため、高いクリーン環境を大切にしています。
田口 なるほど。御社ではあえて、クリーンルームにこだわっているのですね。
鹿沼事業所では、各所で工事が進んでいます。クリーンルームの装置を新たに導入するための工事や、NEDO(国立研究開発法人新エネルギー・産業技術総合開発機構)の研究テーマに関わる業務を行うエリアも準備中です。NEDOの事業「グリーンイノベーション基金事業/次世代デジタルインフラの構築」に、Mipoxの研究テーマ「次世代パワー半導体に用いるウェハ技術開発」が採択されました。予算1,376億円に上る事業で、Mipoxがその一端を担っています。
すぐそばの別室では、反射材のRef Liteブランドの製造機器が設置工事されていました。
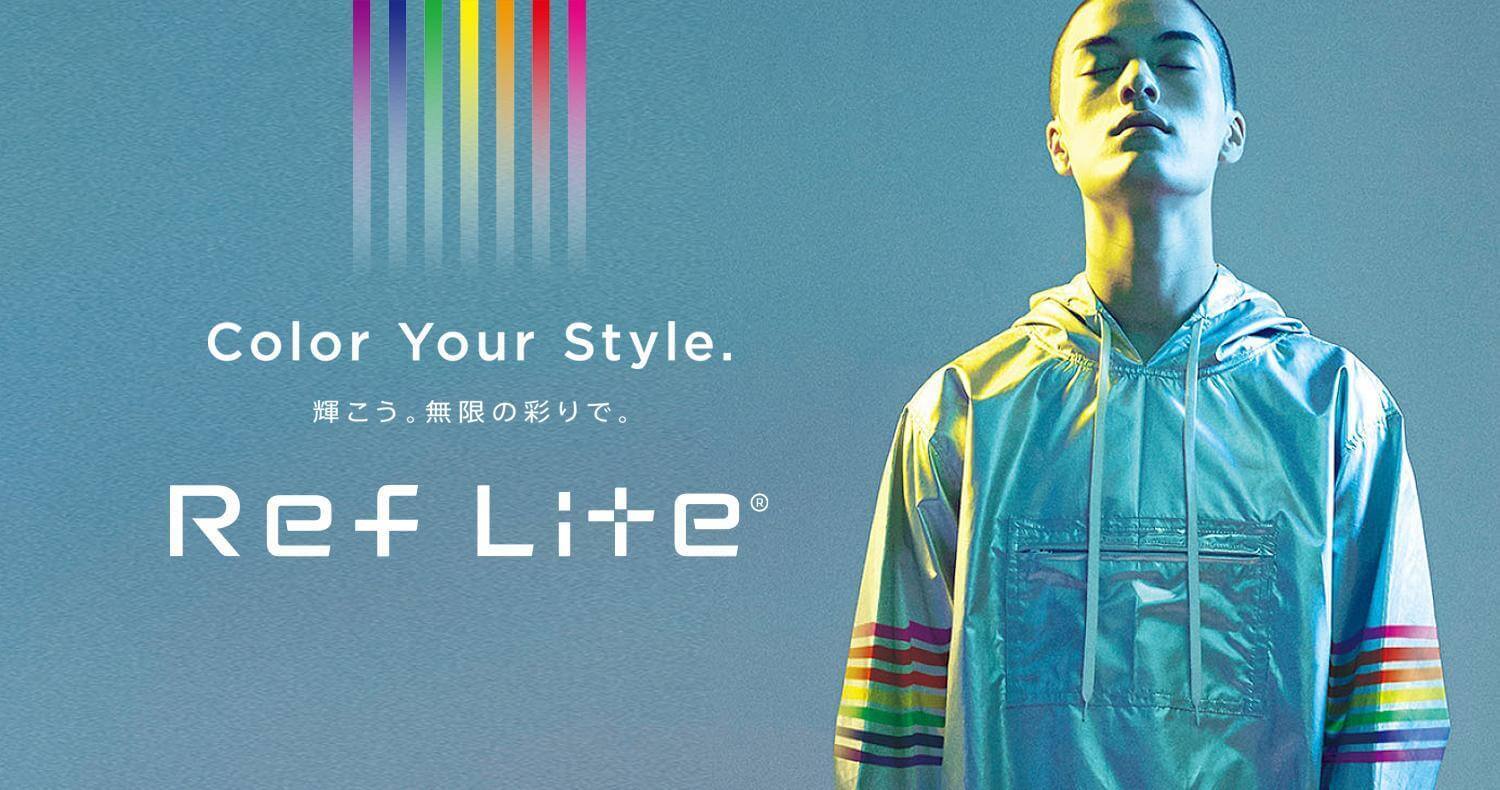
渡邉 Ref Liteは、ファッション全般に採用されることを目指しています。買収した京都の企業でやっていたものを引き継ぎました。Ref Liteを作っていた企業は、もとは研磨フィルムを作っていた当社の競合です。「塗る」技術がベースになっています。
田口 これから、鹿沼事業所に生産体制を集約していくのでしょうか。
渡邉 そうですね。将来的に、当社のマザー工場にしていきます。来年4月に向けてものづくりの技術面や体制面を支えながら、鹿沼が牽引していくという位置付けです。
田口 組織づくりや働く環境も含めて、整いつつあるのですね。
渡邉 いや、まだまだですよ。長い長い道のりです。ものすごい速さで進化していく技術や変化していく世の中に対応し、私たちも常に変化し続けるので、「完成」という考え方はないですね。
編集後記
何百もの工程があるとされる半導体製造の一部を担い、ナノの世界で加工していくため、ものづくりの現場としては地味に見えるかもしれません。一方、今後の社会インフラを支える上で半導体は不可欠で、絶えず技術革新を進めていく必要もあります。このような世界で、ものづくり企業を発展させていく要素は何なのか、後編では渡邉社長のビジョンなどを伺います。(Koto Online編集長 田口紀成氏)
【関連リンク】
Mipox株式会社 https://www.mipox.co.jp/
株式会社コアコンセプト・テクノロジー https://www.cct-inc.co.jp/
【こんな記事も読まれています】
・【会員限定動画】サプライウェブで実現するマスカスタマイゼーション時代の企業戦略
・製造業における購買・調達業務とは?課題の解決方法も紹介
・ビジネスや技術のトレンドに反応しながら進化を続けるCRMの事例を紹介