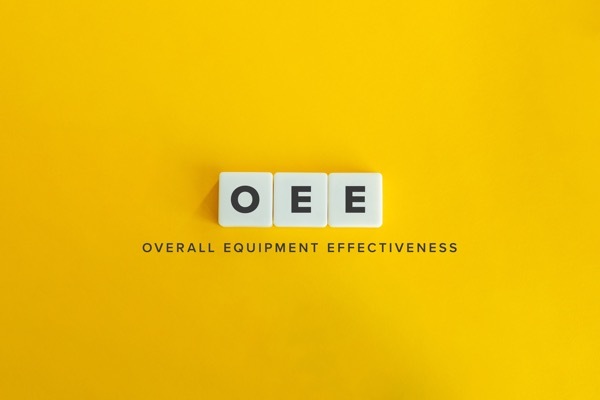
設備総合効率は、設備の効率を総合的に判断できる指標であり、主に製造業で活用されています。自社の設備総合効率はどれくらいか、また理想の設備総合効率はどれくらいなのかをご存じでしょうか。
本記事では、設備総合効率の概要や計算方法とともに、設備総合効率が低下する原因や改善方法などについても解説します。
目次
設備総合効率(OEE)とは?
設備総合効率(OEE:Overall Equipment Effectivenes)とは、設備の効率を総合的に判断する指標です。日本産業規格は、設備総合効率を以下のように定義しています。
設備の使用効率の度合を表す指標。
備考:設備効率を阻害する停止ロスの大きさを時間稼働率、性能ロスの大きさを性能稼働率、不良ロスの大きさを良品率で示すと、設備総合効率は、次の式で表される。
設備総合効率=時間稼働率×性能稼働率×良品率
出典:日本工業規格 JIS Z 8141 : 2001 生産管理用語
上記より、時間的・速度的・品質的の観点から、設備の生産性を測る指標だということがわかります。IATF16949やISO22400-2:2014などの国際基準にも定められており、国内外のさまざまな企業で活用されています。
設備総合効率の計算方法
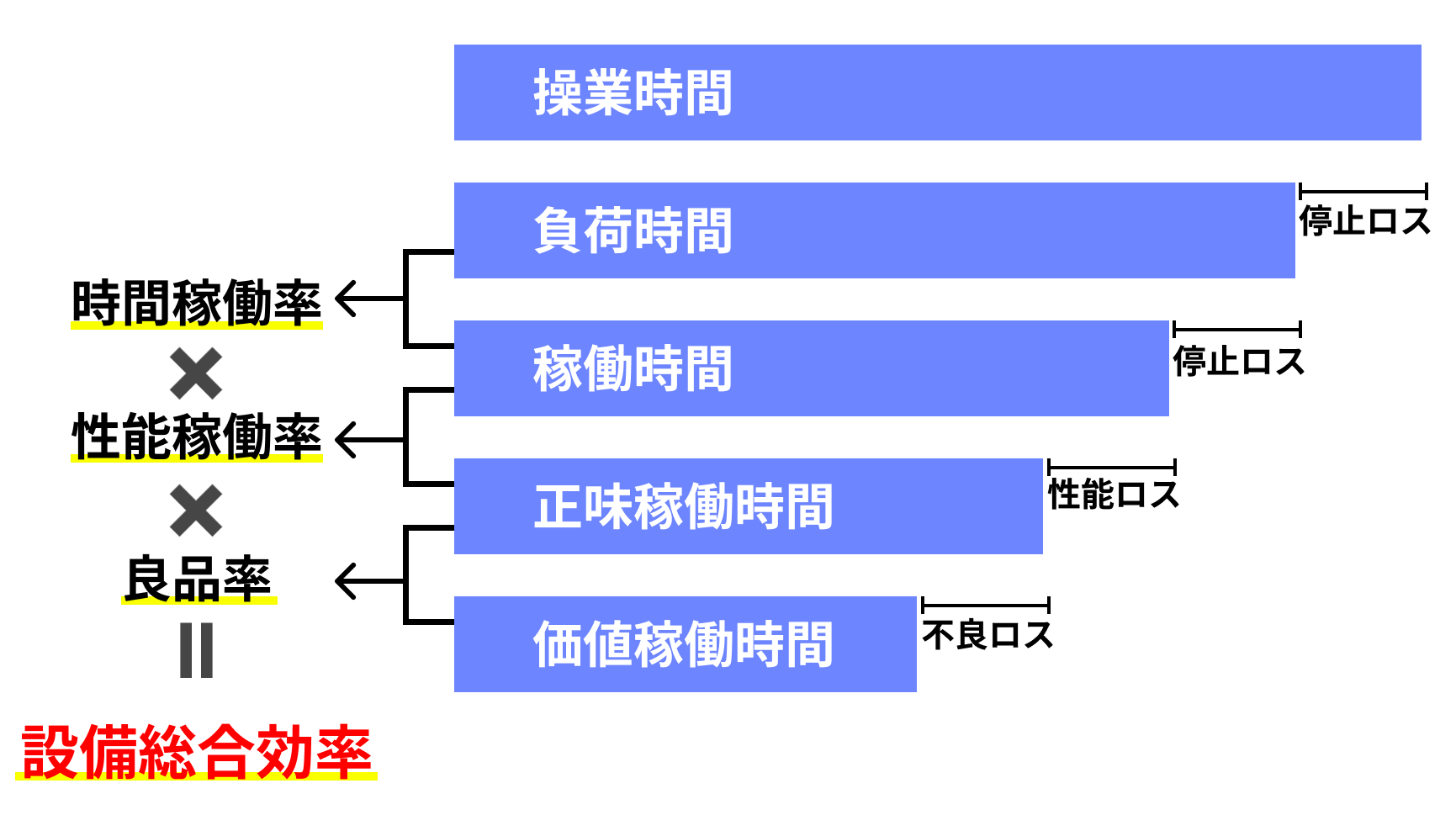
設備総合効率は、以下の計算式で求められます。
設備総合効率=時間稼働率×性能稼働率×良品率
先述の通り、時間稼働率は設備効率を阻害する停止ロスの大きさを、性能稼働率は性能ロスの大きさを、良品率は不良ロスの大きさを表しています。それぞれの具体的な求め方を見ていきましょう。
時間稼働率
時間稼働率とは、仕事を課す時間である負荷時間のうち、実際に設備が稼働している時間(=稼働時間)の割合を表します。計算方法は以下の通りです。
停止時間とは、立ち上がりまでの時間や工具を交換する時間、故障によって停止した時間などを合計した時間です。例えば、1日の負荷時間が8時間(480分)あり、1日当たりの停止時間が48分あった場合は
となり、時間稼働率は90%とわかります。
性能稼働率
性能稼働率は、稼働時間のうちどれだけの製品を製造できたかを表します。計算方法は以下の通りです。
性能稼働率の構成要素である「基準サイクルタイム」とは、1つの製品を製造するために定められた時間のことです。すなわち、理想の動きをしたときのサイクルタイムに当たります。
性能稼働率の計算例を挙げると、基準サイクルタイムが1分であり、8時間(480分)の稼働時間で432個の製品を製造できた場合は、
となり、性能稼働率は90%とわかります。
良品率
良品率は、生産数量に対する良品数量の割合を表します。計算方法は以下の通りです。
良品数量とは、生産数量から不良品の数量を引いた数のことです。良品率の計算例を挙げると、生産数量が1,000個に対して不良品が5個あった場合は、良品数量が995個となるため、
となり、良品率は99.5%とわかります。
設備機器総合有効生産力(TEEP)
設備機器総合有効生産力(TEEP:Total Effective Equipment Performance)は、全ての時間に対する生産力を示す指標です。実際の負荷時間に対する生産力である設備総合効率と密接に関係しています。設備機器総合有効生産力の計算方法は、以下の通りです。
設備機器総合有効生産力=設備総合効率×ローディング
ローディングとは、全ての時間に対する稼働時間の割合のことです。例えば、1日に12時間稼働する設備のローディングは、12時間/24時間で求められ、ローディングは0.5(50%)とわかります。
設備機器総合有効生産力は、設備を休める時間を考慮して計算するため、設備が持つ総合的な生産力を求められます。
設備総合効率を活用するメリット
設備総合効率を活用すると、以下のようなメリットを得られます。
- 故障によるロスの削減
- 保全コストの削減
- 品質の改善
故障によるロスの削減
設備総合効率は性能稼働率や良品率を考慮した値であるため、計算すれば設備の状態を把握できます。設備総合効率を利用して故障を予測し、適期に設備の入れ替えやメンテナンスを行えば、故障によるロスを削減できるでしょう。
特に、工場内に一つしかない設備の場合、停止してしまうと工場全体の生産も止まってしまいます。また、高額な設備の場合は交換に多額の資金がかかります。設備総合効率の値に応じて適切な対策を講じれば、これらのリスクを低減し、故障によるロスの削減に役立ちます。
保全コストの削減
設備総合効率は、前述の計算式に当てはめるだけで計算できます。実測値を入れるだけで機器の状態を把握できるため、保全コストの削減に役立てられるでしょう。保全にはさまざまな方法がありますが、IoT機器などを工場全体に導入すると、保全に見合わないような金額がかかることもあります。
設備総合効率の計算には、センサーを用いて求めなければならないような値は必要ありません。生産数量や稼働時間、停止時間などがわかれば簡単に計算が可能です。計算にコストもかからないため、保全にリソースを割けない企業に向いています。
品質の改善
設備総合効率は、時間稼働率や性能稼働率、良品率などから求めますが、それらの構成要素を比較することで、自社の生産性が低い箇所を容易に見つけられます。設備総合効率を目安に交換やオーバーホールなどの対応を講じれば、適切な機器を適期に導入でき、品質の改善につなげられるでしょう。
例えば、時間稼働率や性能稼働率に比べて良品率が悪い場合は、設備の劣化や従業員の技術力不足などがあると考えられます。原因を突き止めて改善すれば、生産体制や設備の状態が良くなり、安定した品質を保てるようになるでしょう。
設備総合効率低下の原因|7大ロス
設備総合効率は多くの要因によって左右されますが、主な低下の原因として以下の7つが挙げられます。
- 故障
- 段取り・調整
- 工具交換
- 立ち上がり
- 速度低下
- チョコ停・空運転
- 不良・手直し
それぞれについて、詳しく解説します。
故障
故障すると設備の交換や修理が必要になりますが、その間は生産が続けられないため時間稼働率が低下し、それに伴って設備総合効率も低下してしまいます。故障の原因は、トラブルによる緊急停止や経年劣化などです。
故障した部品を取り寄せなければならない事態になれば、その間は稼働することができず、納品遅れや機会損失の増大につながります。加えて、交換や修理にはコストがかかります。このような損失を生まないためには、定期的なメンテナンスやオーバーホールなどが有効です。
段取り・調整
段取りや調整に時間がかかれば稼働時間が減るため、時間稼働率が低下し、それに伴って設備総合効率も低下してしまいます。段取り・調整には、稼働開始時の起動時間や設備設定の修正時間が含まれます。
やむをえずに発生してしまう時間もありますが、段取りのマニュアル化や調整回数を低減するための体制作りなどの対策を行うのが有効です。
工具交換
工具を交換する際には、設備を止めなければならないことが多いでしょう。交換の時間が長引いたり交換の頻度が高かったりすると、その分時間ロスが生まれてしまいます。
とはいえ、工具交換を適期に行わなければ、故障や部品破損のリスクが高まり、大きな経済的損失を被る場合があります。適切な交換体制をとりつつも、ムダを削減して効率よく交換する工夫が求められます。
立ち上がり
立ち上がりに時間がかかれば、その分稼働時間は短くなります。これにより時間稼働率が低下し、それに伴い設備総合効率も低下してしまうでしょう。立ち上がり時間が長引く原因には、設備の温度低下や経年劣化などがあります。
立ち上がりの時間が従業員の待機時間になれば、その時間の人件費もムダになってしまいます。立ち上がりの時間を短縮できれば、生産数量の増加だけでなく、人件費のムダも省くことが可能です。
とはいえ、性質上立ち上がりに時間がかかる設備もあるでしょう。その場合は、遠隔操作により従業員が到着する前に立ち上げたり、休日を挟むなどして設備が冷えている場合は事前に室温を上げたりするなどの対策が取れます。
速度低下
設備の速度が低下すれば、その分製造速度が遅くなります。製造速度が遅くなると、稼働時間に対する生産数量が低下するため性能稼働率が低下し、それに伴い設備総合効率も低下します。設備の速度低下の原因には、部品の劣化や汚れ、経年劣化などが挙げられます。
速度の低下を防止するには、定期的なメンテナンスや、オーバーホールによる内部部品の洗浄などが効果的です。
チョコ停・空運転
チョコ停や空運転をすると、その分だけ時間のロスが発生します。その結果、時間稼働率が下がり、設備総合効率も低下するでしょう。
チョコ停とは、製造設備のトラブルによって、設備や製造が一時的に停止・空転することです。一般的に1時間以内の停止はチョコ停と言われており、1時間以上の停止はドカ停と呼ばれています。
原因には、電力不足による停止や、設備の動作不良による全体の空運転などが挙げられます。ただし、原因は多岐にわたるため、自社で考えられるチョコ停や空運転のリスクを日常的にそれぞれ潰す必要があります。
不良・手直し
不良や手直しがあると、修正に人手を割かなければなりません。修正には人件費がかかるうえ、設備の製造を止める必要が出てくるかもしれません。不良や手直しによるロスには、不良品の取り出しや設備の動作不良の修正などが挙げられます。
不良や手直しの回数を軽減するには、日々のメンテナンスや清掃、品質改善などが重要です。5S(整理・整頓・清掃・清潔・しつけ)の徹底や定期的なメンテナンスの実施など、当たり前のことを忠実に行うことが不良や手直しを減らす方法だといえます。
設備総合効率の目安
結論から述べると、設備総合効率は機器の性能や耐久性によって左右されるため、目安はありません。自社が理想とする値や実際のデータを設備総合効率の計算式に当てはめ、許容できる範囲や目標を定めてください。
また、設備機器総合有効生産力とのバランスも重要です。設備機器総合有効生産力は、全ての時間に対する生産力を示しています。すなわち、設備総合効率と設備機器総合有効生産力の値が近ければ近いほど、休みなく稼働していることになります。これでは、メンテナンスが行えなかったり、機器の休みがない状態に陥ったりします。
加えて、設備総合効率の要素である性能稼働率は、基準サイクルタイムの値によって変動するため、企業によって異なる値が出るでしょう。
ただし、良品率は高いほうがよい値です。良品率は100%を目指して、設備総合効率を上げられるようにしてください。
設備総合効率を改善するためのアプローチ
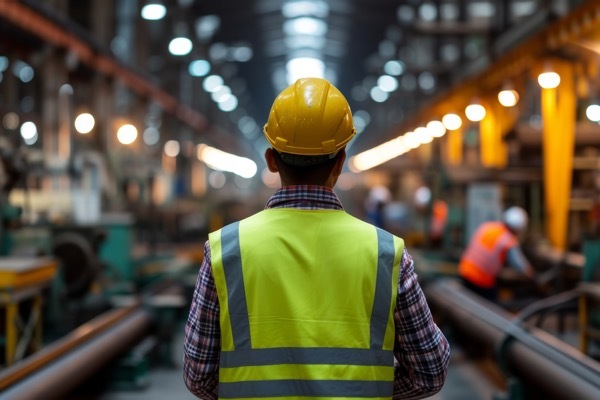
設備総合効率を改善するには、以下のようなアプローチが有効です。
- 現場での改善
- 予知保全システムの導入
- 製造実行システム(MES)の導入
現場での改善
問題があると気がついたときに、一つひとつ解決していくことが設備総合効率の改善につながります。日常的なメンテナンスや5S活動などの基本を欠かさずに行うことが、故障や機能低下などの7大ロスの防止につながるでしょう。
設備総合効率を構成する時間稼働率・性能稼働率・良品率は、簡単な方法で劇的に改善することはありません。あくまで、日常的な保守の積み重ねが将来の設備総合効率を高めます。現場の課題を洗い出し、地道に潰していくことが、設備総合効率の改善につながるでしょう。
予知保全システムの導入
予知保全システムを導入すれば、故障や不良を予測できるため、適期でのメンテナンスや設備交換が可能になります。効率や時間的なロスを低減できるため、設備総合効率の改善に有効です。
予知保全システムは音や動作などの異常を検知し、設備や機器の故障を事前に予測します。AIやIoTなどのデジタル技術が急速に発展していることもあり、機械学習によって世界中の故障を学んだ予知保全システムは、精度の高い予知保全を実現します。
工場全体に予知保全システムを導入し、それぞれのシステムの連携を図れば、スマート・マニュファクチャリングが実現し、工場全体の生産性を高めることもできるでしょう。
関連記事:スマート・マニュファクチャリングとは?実現するための取り組みや技術を紹介
製造実行システム(MES)の導入
製造実行システム(MES:Manufacturing Execution System)を導入すれば、工場全体の製造状態が可視化されるため、定量的なデータにもとづいて問題点を発見できるようになります。設備総合効率を改善する情報も見つけやすくなるため、効果的な施策が講じられるようになるでしょう。
具体的には、以下のようなことが実行できます。
- 生産資源の配分・監視
- 仕様・文書管理
- 作業スケジューリング
- 作業者管理
- プロセス管理
- データ収集
- 実績分析
- 品質管理
- 保守・保全管理
システムによって異なりますが、このほかにもさまざまな情報を可視化できます。これらのデータを活用すれば、高度な解析が必要な指標も自動で求められるようになり、工場全体の生産性向上に役立つでしょう。
関連記事:MES(製造実行システム)とは?導入メリットや11の構成機能を解説
設備総合効率は日常的な対応とデジタル化によって改善する
設備総合効率が低下する原因はさまざまあり、企業によって異なります。しかし、そのほとんどは日常的なメンテナンスによって予防できます。日々の点検や整理・整頓を確実に行えているか、今一度確認するとよいでしょう。
また、設備総合効率の改善には、デジタル化も効果的です。本記事では予知保全システムとMESを紹介しましたが、企業によってはさらに効果を発揮するデジタル技術があるかもしれません。これを機に、自社に最適なデジタル技術を導入し、設備総合効率の改善を目指してみてはいかがでしょうか。
【注目コンテンツ】
・DX・ESGの具体的な取り組みを紹介!専門家インタビュー
・DX人材は社内にあり!リコーに学ぶ技術者リスキリングの重要性
・サービタイゼーションによる付加価値の創造と競争力の強化