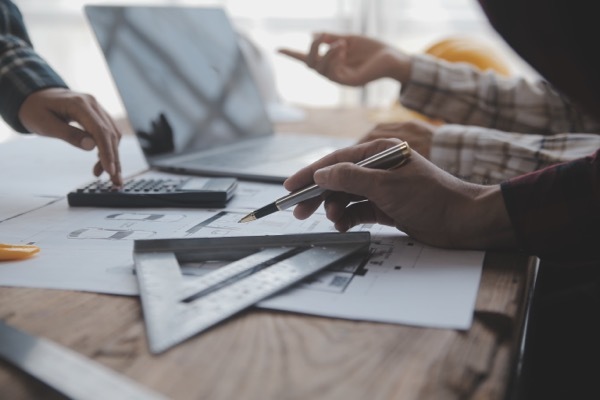
「製品のコストや品質は、設計で8割が決まる」と言われています。しかし、設計をおざなりにしてしまい、後工程で多額のコストをかけて修正しなければならない場合もあります。本記事では、設計の精度を上げる手法について解説します。
目次
フロントローディング
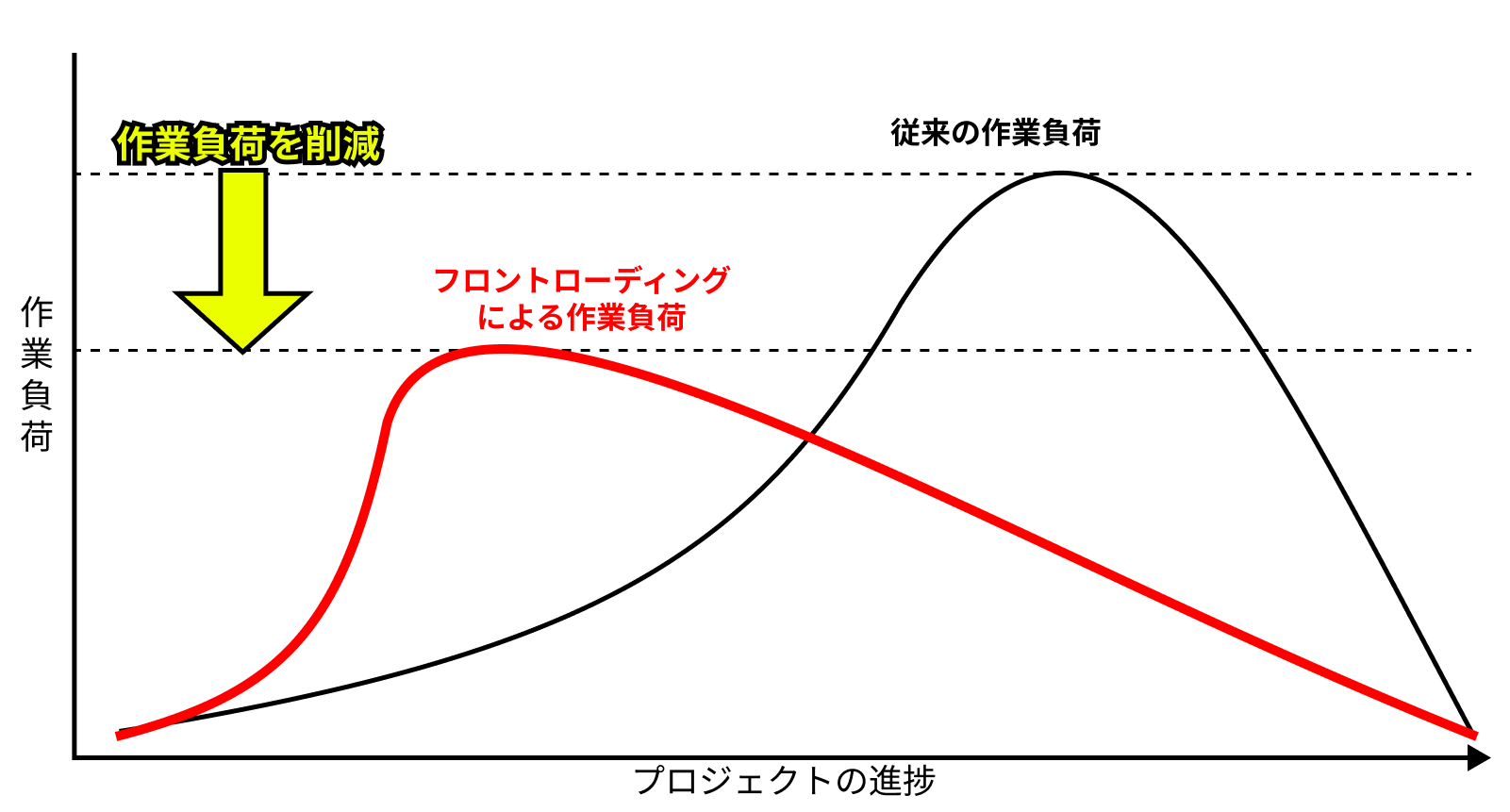
フロントローディングとは、初期段階である企画や製品設計に負荷をかけ、作業を前倒しで進めることを指します。具体的には、開発段階での緻密なシミュレーションや後工程を想定した企画などが挙げられます。
設計段階における設計変更の自由度と変更コストは、上の図のように変化します。一般的に、工程が進むほど設計変更の自由度は低くなり、変更コストは高くなります。プロジェクトが進めば進むほど設計変更は難しくなるのです。
フロントローディングを実施すると、企画や設計の段階で製品を作り込むため、後工程や製造段階での設計変更が減り、変更にかかる労力やコストを削減できます。
DR(デザインレビュー)
DRとは、設計段階を見直すことで後工程をスムーズに行えるようにする取り組みです。「設計審査」とも呼ばれています。中小企業基盤整備機構は、DRを以下のように定義しています。
デザインレビューとは、設計開発活動をこのまま進めることにより、品質・納期・コストなどの設計開発の条件を満たす設計開発活動の結果を出すことができるかどうかを、設計開発活動を担当する人だけでなく複数の人で判断することをいいます。
引用:製品開発手順のデザインレビューについて教えてください。「中小企業基盤整備機構」
DRは、商品の企画や設計、試作評価の段階で実施され、製品の変更にかかる労力やコストを削減し、納期遅れのリスクを低減する効果があります。ここでは、それぞれの段階で行われるDRの目的や見直す項目を解説します。
DR1(商品企画フェーズ)
DR1は、商品の企画をまとめる段階です。自社の技術力で実現できるのか、目標を達成するために必要な資金や時間はどれくらいかを判断するために行われます。具体的には、顧客のニーズや市場動向から、商品に必要な性能や機能を確定します。
DR1で確定した商品企画はDR2以降の基盤となるため、正確な目標設定が必要です。ニーズ把握に誤りがあると必要性の低い商品ができ、商品設計にミスがあると製造工程で修正が必要になります。
DR1では、主に以下の項目を見直します。
・ユーザー要求
・機能目標
・信頼性目標
・コスト
DR2(構想設計フェーズ)
DR2は、DR1で考えた商品企画と設計の整合性を図る段階です。企画を基に、商品の要件や採用する技術を確定します。この際、QCD目標が用いられます。QCDとは、Quality:質、Cost:価格、Delivery:納期の3つの要素の頭文字を合わせた言葉です。これらの要素の目標を明確にすることで、製品の総合的な価値を向上できます。
DR2では、主に以下の項目を見直します。
・設計図面
・部品
・ソフトウェア
DR3(詳細設計フェーズ)
DR3では、機能性や生産性、コストなどの観点から試作に進められるかを判断します。具体的には、企画や構想で設計した製品が商品開発の目的を達成できるかを確かめたり、構想データを基に信頼性を評価したりします。
DR3では、仮想空間上でのシミュレーションも有効です。例えば、3D CADやCAEを活用すれば、実際に製品を作らなくても、システム上で強度や耐久性を検証できます。おおよその製品情報の把握や、問題点の発見がシステム上で行えるため、高度なレビューが可能になります。
DR3では、主に以下の項目を見直します。
・機能性
・生産性
・信頼性
・コスト
DR4(試作評価フェーズ)
DR4では、DR3を通過した製品を試作し、性能の評価を行います。定められた評価基準を達成していれば、DRの完了です。目的に応じた品質が得られていなければ、それを満たすために改善を行います。
シミュレーションで問題がなくても、実際に製品を作ることで問題が発生する可能性もあります。DR4では、性能や機能だけでなく、製品化や量産化できるかなどの視点でも評価します。
コンカレントエンジニアリング
コンカレントエンジニアリングとは、複数のフェーズを同時に進めることを指します。従来の開発手法では、それぞれのフェーズが完全に終了した後に、次の工程に入っていました。その点コンカレントエンジニアリングは、部門間で情報共有しながら複数のフェーズを同時並行で進めるため、短期間での開発が可能です。
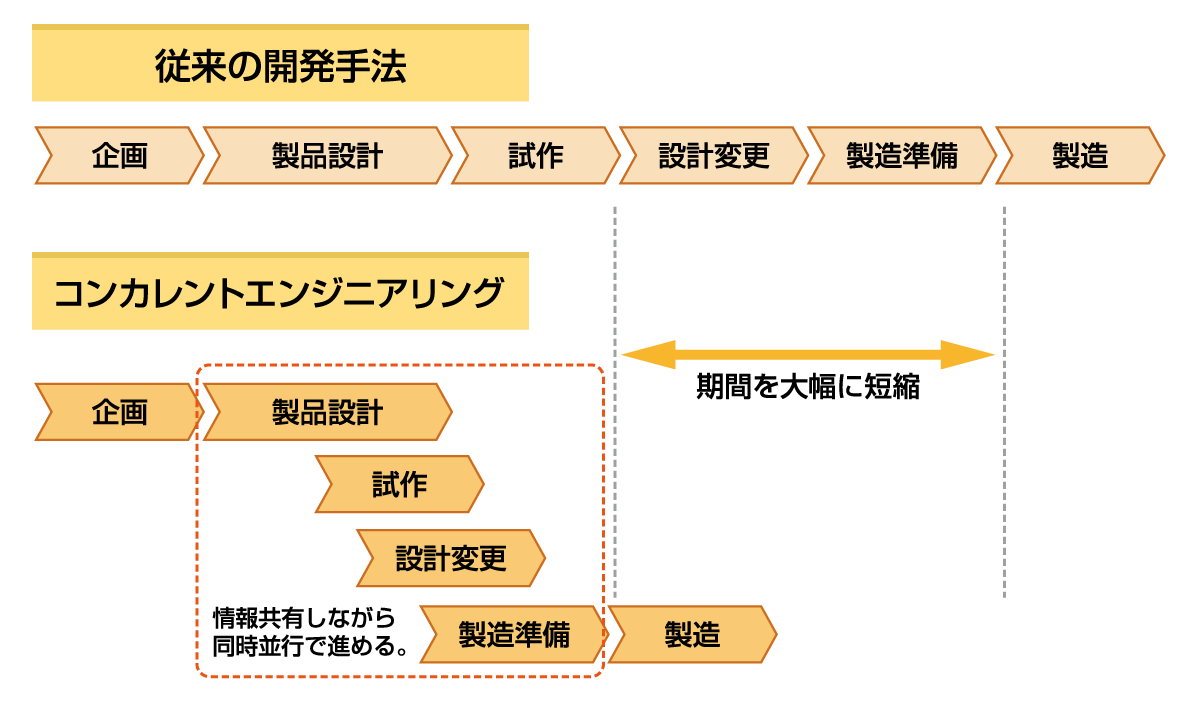
コンカレントエンジニアリングの実施は、開発期間の短縮のほか、多品種少量生産への対応や顧客満足度の向上に有効です。しかし、部署間の連携が不足すると、QCDが悪化するリスクがあります。例えば、問題点を迅速に共有できないと、無駄な試作品の製作リスクが高まります。
また、コンカレントエンジニアリングは、詳細な企画があって成り立ちます。よって、初期段階に負荷をかけるフロントローディングが欠かせません。コンカレントエンジニアリングを実施する際には、綿密な情報共有だけでなく、フロントローディングも意識しましょう。
関連記事:製品開発を進化させるコンカレントエンジニアリングとは?
検図
検図とは、設計図から不良がないかを確認する作業です。DRの実施前に検図を行い、設計に問題がないかを確認することもあります。検図では、設計者が行うセルフチェックのほか、ダブルチェックやクロスチェックを行い、ミスや不良のリスクを低減することもあります。
設計図にミスがあると、試作をスムーズに製作できなかったり、修正の時間が必要になり納期遅れが発生したりします。フロントローディングの一環として、企画や設計などの早い段階で検図を行うことにより、作業が後戻りするリスクを低減できます。
フロントローディングを行うメリット
フロントローディングを行うメリットは、主に以下の3つです。
・QCDの向上
・コストの削減
・工期の短縮
QCDの向上
先述の通りQCDとは、Quality:質、Cost:価格、Delivery:納期の3つの要素のことです。フロントローディングを実施すると、これらの要素を向上できます。
まず、企画や設計の段階で「目的に合致した商品であるか」「機能性・信頼性は十分か」などを徹底的に判断するため、商品の質を向上できます。また、初期段階で後工程の検証まで行うため、後戻りをして設計をやり直すリスクを低減できます。
後工程での設計の修正がなくなると、後戻りする必要がなくなるため、開発コストを抑えることができます。加えて、修正がなくなると開発段階の手間が省けるため、納期遅れのリスクも低減できるでしょう。
コストの削減
フロントローディングを行うと、後述の通り工期を短縮できるため、人件費を削減できます。これは、企業のメリットとなるだけでなく、従業員の労力も削減できるため、労働環境の改善にも役立ちます。
また、フロントローディングの一環として、試作をデジタルツインで行うことにより、現実の環境で試作をする回数を低減できます。試作するには人件費や材料費のほか、外注費がかかることもあります。
デジタルツインで試作をするにも人件費はかかりますが、材料費が必要ないことに加え、短期間でシミュレーションを行えます。また、さまざまな環境に設定できるため、高度なシミュレーションも費用を抑えて実施できます。
工期の短縮
フロントローディングを行うと、後工程がスムーズになるため、工期が短くなる傾向があります。これにより、短期間での納品や納期の遵守が可能になります。
新製品の開発プロジェクトは不明点も多く、不測のトラブルが多発することもあるでしょう。フロントローディングを実施すれば、問題が顕在化する前にリスクを取り除くことができ、予期せぬトラブルによる納期遅れのリスクを低減できます。
また、最も負荷のかかる工程を早い段階で終わらせることができるため、比較的早い段階で納品の目処を立てることができます。これにより、スケジュール管理が容易になり、納品が遅れそうな製品への対処が早期から可能になります。
フロントローディングのデメリット
フロントローディングの実施には多くのメリットがありますが、次のようなデメリットもあります。
・設計者の負担が増加する
・各部門の協力が必要
設計者の負担が増加する
フロントローディングでは設計に負荷をかけるため、設計者の業務が増加します。また、開発の技術的水準や製品が抱えるリスクによっては、経営陣の判断が必要な場合もあるでしょう。このように、企画や設計段階の業務が増えるため、場合によっては増員やツールの導入などの対処が必要になることもあります。
また、企画や設計の工数が多くなるため、該当部門の納期を伸ばすなどの工夫も必要になる場合があります。フロントローディングを実施する際には、特定の部署や社員に負担が偏らないように注意しなければなりません。
各部門の協力が必要
フロントローディングでは、綿密な情報共有が重要です。例えば、DRを行う場合は、フェーズごとに機能性や生産性を確認しなければなりません。これらを1人で判断できれば問題ありませんが、専門的な内容は担当する部署の人間が確認する必要があるでしょう。
また、コンカレントエンジニアリングを行う場合には、リアルタイムでの情報共有が必要です。設計変更や試作品の検証結果などの情報共有が滞ると開発期間が長くなり、コンカレントエンジニアリングのメリットが小さくなります。
フロントローディングを行う場合は、最大限の効果を出すためにも部門間の連携を高め、協力し合える体制を築くようにしましょう。
フロントローディングに効果的なツールやシステム
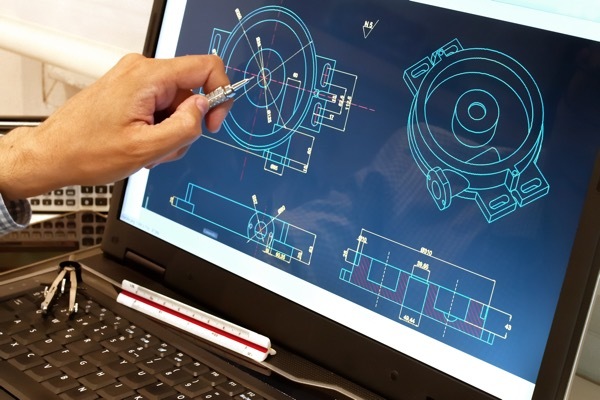
フロントローディングでは、以下のツールやシステムの利用が効果的です。
・CAD
・CAM
・CAE
・PLM
・BIM
CAD
CAD(Computer Aided Design)は、コンピュータで設計を行うためのツールです。図面をコンピュータ上に描き、保存や共有をすることができます。紙に描く図面と比べると、修正が簡単というメリットがあります。
CADには2D CADと3D CADがあります。2D CADは線や点を用いて2次元上に3次元のデータを表現します。一方、3D CADはコンピュータの仮想3次元空間に3次元のデータを表現します。
CADを活用すれば、設計の速度を上げることが可能です。また、3D CADを活用すれば、設計に詳しくなくても直感的に形状を理解できます。このようにCADは、設計の短時間化に加えて、形状をわかりやすく伝えることにも活用できます。
CAM
CAM(Computer Aided Manufacturing)は、CADのデータを、加工機器が理解できるコードに変換する役割を持っています。CADと一体型になっているCAD/CAMというシステムもあります。
CADで設計したデータを活用するのであれば、加工機器が理解できるようなプログラミングに変換するCAMはほぼ必須といえます。そのため、フロントローディングを目的に設計をCADで行うのであれば、CAMかCAD/CAMを導入しましょう。
CAE
CAE(Computer Aided Engineering)は、CADで設計した製品のシミュレーションを行うシステムです。CADのデータを活用して、材料や製造工程が適切かどうかをシミュレーションによって確認できます。
CAEは、製造過程と製品が特定の環境下で起こす状態変化をデジタルツインでシミュレーションできます。広く活用されているのは、状態変化のシミュレーションです。構造解析や熱流体解析などを用いて、製品がどのような変化を起こすのかを仮想空間上でシミュレーションできます。
製造過程のシミュレーションは、製造中にどういったトラブルが起こるかを予知できます。CAEで事前にシミュレーションすることで、製造工程のトラブル防止策を講じることができ、納品遅れなどを防ぐことができます。
PLM
PLM(Product Lifecycle Management)は、業務プロセスや設備、コストなどの製品ライフサイクルに関わる情報をITで一元管理するシステムです。製品の企画からアフターサービスまで広い範囲の業務を対象としています。
PLMでは、製品ライフサイクルを俯瞰した上で、最適な製品開発を行えるよう管理します。PLMにより、企画段階から製品の廃棄まで見据えて開発活動を行うことは、自然とフロントローディングを実施することになります。
フロントローディングに加えて、情報の一元管理も目指している方は、PLMを実施することでどちらも達成できるかもしれません。
BIM
BIM(Building Information Modeling)とは、3次元の形状情報に加えて、部位の属性情報などを併せ持つ建物モデルを構築するシステムです。建物だけでなく、部位の役割や性能、仕様などをモデルに付与できます。
BIMでは、形状情報だけでなく、役割や仕様などの属性情報が付与できるため、企画段階で細かな設計が可能です。属性情報を基にシミュレーションや最適化が実施できることから、後工程をスムーズに進められるようになります。
フロントローディングで品質やコストを改善できる
品質やコストの8割が決まると言われている設計段階に力を入れることで、製品の機能性や信頼性を向上しながら、工期やコストを削減できます。設計部門の労力は増加しますが、部署ごとの期限を設定し直すなどの工夫をすることで、全体の効率を高められるでしょう。
また、フロントローディングは製造や試作段階の後戻りを削減できます。設計が原因で後戻りが多く発生している、想定していた品質を達成できていないといった場合は、フロントローディングを実施して解決を目指してみてはいかがでしょうか。
【こんな記事も読まれています】
・【会員限定動画】サプライウェブで実現するマスカスタマイゼーション時代の企業戦略
・製造業における購買・調達業務とは?課題の解決方法も紹介
・ビジネスや技術のトレンドに反応しながら進化を続けるCRMの事例を紹介