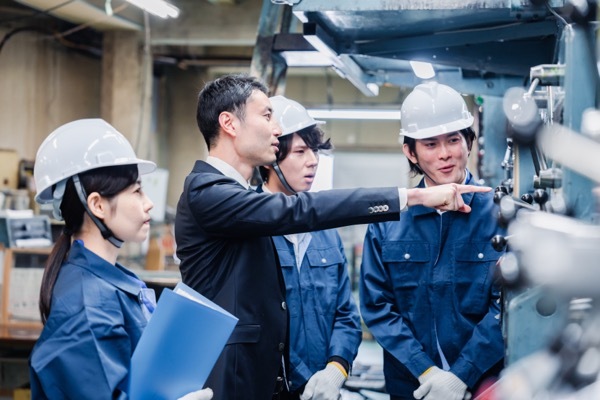
製造業では、以前にも増して省人化・省力化が重要になります。少子高齢化が進み、省人化・省力化に直結するDX(デジタル・トランスフォーメーション)も急務となっているため、自社の業務を見直した上で、課題を特定して改善を進めていく必要があります。しかし、企業や組織で具体的にどのように省人化・省力化を進めればいいかわからない経営者、担当者の方もおられるのではないでしょうか。本コラムでは、製造業に求められている省人化・省力化について解説します。
目次
省人化・省力化とは?
まず省人化の意味、省人化と省力化の違いについて解説します。
省人化の意味
省人化とは、既存の業務の改善(作業や設備、工程の見直しと改善)を行い、その業務に携わっていた人員を削減することを指します。
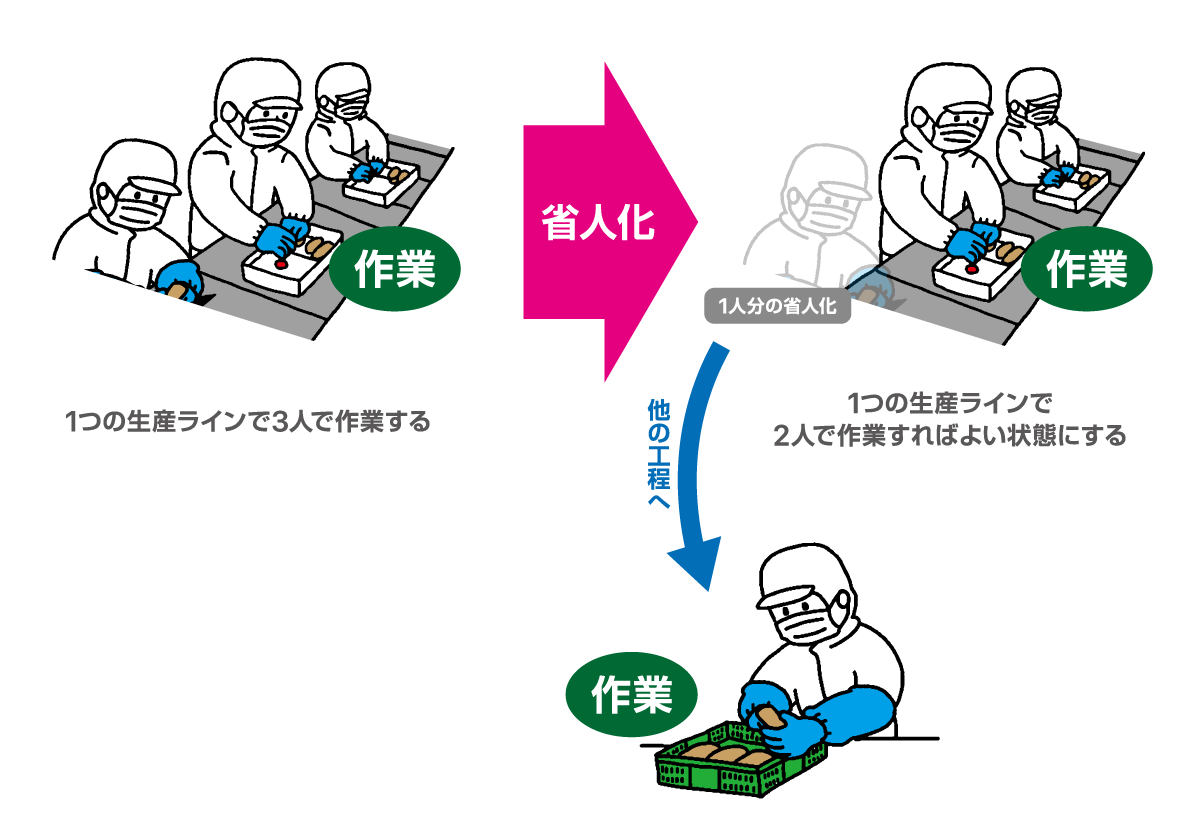
たとえば、ロボットを導入して業務を100%自動化した場合、もともとその業務を担当していた従業員を削減でき、人にしかできないほかの業務に割り当てたりできるようになります。特定の業務を担当していた人員は減りますが効率が上がり、全社的にリソースが増えます。機械では代替できないよりクリエイティブで業務を手厚く行うことが可能になります。
省人化と省力化の違い
省力化に関しても、既存の業務の改善を行う点は同じです。ただし、省力化の場合は人員の削減ではなく、1人当たりの業務負担の軽減を意味します。まとめると以下のとおりです。
- 省人化=無駄をなくして人的リソースを確保すること
- 省力化=ひとつの作業にかかる工数や労力を減らすこと
たとえば、ロボットを導入して業務を90%自動化した場合、従業員の業務負担は大幅に軽減しています。しかし、残り10%の業務は引き続き人が行わなければならないため、担当者を割り当てておく必要があるのです。
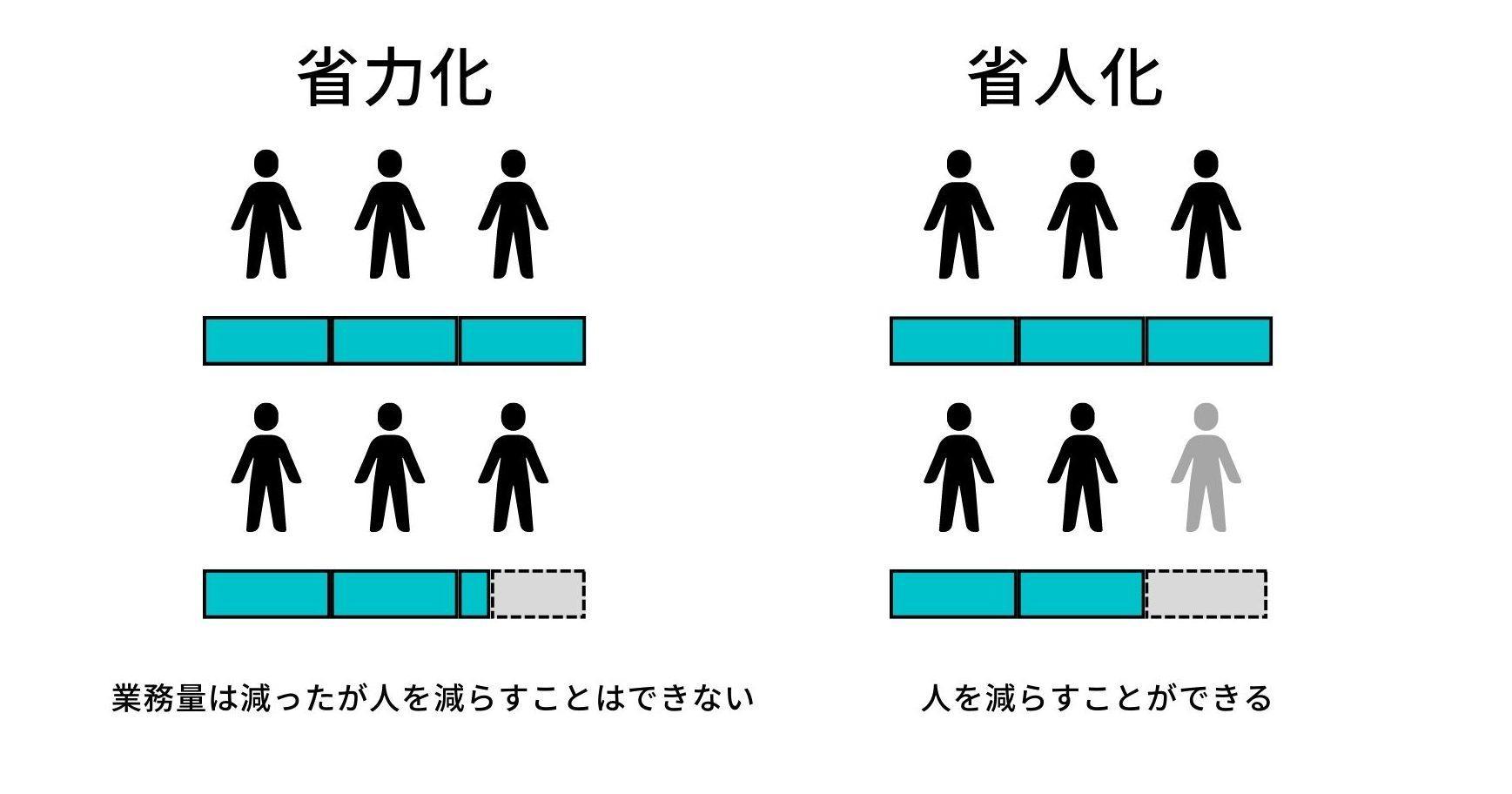
省人化と省力化は、どちらも重要な取り組みであることは間違いありません。ただし、より少ない人数で業務を回せるようになる省人化の方が、企業にとってのメリットは大きいといえます。
経済産業省による『2022年版ものづくり白書』(令和4年5月)でも省人化について言及されています。同資料では、これまで日本では非効率な生産体制のもと、一人一人が長時間労働することで生産体制を確保していたと指摘しています。しかし前述したように、今後の少子高齢化やグローバル化の影響から従来の方法では製造業やものづくりは立ち行かなくなると考えられており、国の先導でデジタルツールやシステムを活用し、省人化も含む業務効率向上を目指した取り組みが進められています。
すでに製造業では、約7割の企業がデジタル技術を活用していると経済産業省の調査に回答しています。ただ、製造業の改善活動では、省力化によって業務負担は軽減できているものの、人員を削減する省人化までは至っていないケースが多々あります。より生産性を高めるためには、省力化で終わらないよう改善を続けたり、既存の業務を抜本的に見直して省人化を目指したりする必要があるといえるでしょう。
省人化・省力化のメリットとデメリット
ここでは省人化、また省力化を実現することでどのようなメリットが得られるのか、まだ実現するための準備などでどのようなデメリットがあるのかについて解説します。
省人化・省力化のメリット
生産性の向上
省人化を進めると、業務プロセスを見直して無駄を省くことにより、一つの作業に対して投下する人的リソースを減らせます。その結果、生産性の向上が達成できます。また省人化・省力化に伴いデジタル機器の導入を行うことは必須(後述)のため、その経緯で業務自体の見直しができ、全体的な業務の改善なども進むことから、生産体制の効率が上がり、劇的な変化を生むことができます。
人手不足の解消
生産性向上により、結果的に余剰になったリソースを別の業務に充てることができます(後述)。
なお、DXの目的に関して経済産業省は「企業がビジネス環境の激しい変化に対応し、データとデジタル技術を活用して、顧客や社会のニーズを基に、製品やサービス、ビジネスモデルを変革するとともに、業務そのものや、組織、プロセス、企業文化・風土を変革し、競争上の優位性を確立すること」と定義しています。生産性向上や業務効率化、デジタル技術やAIで代替できる作業を増やして人手不足を解消して、さらにその先には従業員がより高度で創造的な、AIなどには代替が難しい領域を担うことを目指します。
省人化・省力化のデメリット
機械導入による投資コストが必要
お金をかけずに省人化・省力化も不可能ではありません。しかし、抜本的な工数削減、生産性向上を目指すのであれば、一定の設備投資は必要です。また後述する企業全体のDXへの取り組みには、スマートファクトリーか、AIの導入などへは、ある程度のコストをかけていかなければ、レガシーシステムからの脱却は難しいでしょう。
ただ、いきなり全てをデジタル化すると、莫大なコストもかかりますし、社員が新しいシステムを使いこなせないなどのリスクも生じ、無駄な投資だった…ということになりかねません。スモールスタートを意識しつつ、アウトソーシングもうまく活用しながら進めていく必要があります。
DX人材の獲得・育成が必要
企業や組織でデジタル化を進める過程で、DX・IT人材の確保、育成も課題となります。古いシステムが新しくなるだけでなく、業務プロセスもこれまでと変わるため、一定の教育コストが必要です。
なおIT人材は不足しており確保は現在難しくなっているため、自社で教育するとなるとある程度時間がかかることも見越しておかなければなりません。対策として、最初から自社で雇用するのではなく、外部の専門家をうまく活用する方法もあります。
製造業で省人化・省力化が求められている理由
あらためて、なぜ製造業で省人化・省力化が求められているのか、その理由を4つ解説します。
【理由1】深刻な人手不足
日本では少子高齢化が進行しており、労働人口が減少しています。すでに多くの企業が人手不足に陥っていますが、今後はさらに深刻化していくでしょう。一方で、企業が成長し続けるためには、業務量を減らすわけにはいきません。省人化・省力化に取り組まなければ、従業員1人当たりの業務負担が増えてしまい、事業を継続できなくなる恐れがあります。
【理由2】働き方改革
昨今の日本では、「年次有給休暇の時季指定」や「時間外労働の上限制限」といった働き方改革が推進されています。製造業にとっても働き方改革は重要なテーマであり、従業員1人1人がより働きやすい職場環境を作るための取り組みが求められている状況です。そのため、省人化・省力化によって従業員が休みやすいようにしたり、残業をなくしたりする必要があります。
【理由3】コスト削減
近年のグローバル化によって、製造業では国際的な競争が激化しています。競争力を維持するためには、コスト削減や生産性向上を継続的に実施していかなくてはなりません。省人化によって人員を削減できれば、余分な人件費を削減できます。また、省力化による業務負担の軽減は、生産コストの減少や生産量アップにつながるでしょう。こういった観点から、省人化・省力化が求められているのです。
【理由4】技能継承の課題
省人化・省力化は、技能継承の課題を解消するのにも役立つと考えられています。これまでの日本の製造業は、熟練技術者のスキルや経験によって保たれていました。日本が世界に誇るものづくりの伝統も少子高齢化に伴う継承者の問題や、一流の技術者になるまでのプロセスも属人化な一面があり後継者が育つまでに時間がかかるという課題があります。現在では、技術そのものが消滅するリスクももっています。教育の手間やコストもかかり、それでいて確実に後継者が育つ保証もありません。
省人化を進めると、既存の業務を改善する過程で、ロボットによる自動化や標準化を図ることになりますし、技術をデータ化・可視化することで熟練従業員という「個人」のスキルに依存せず、誰でも近い精度で業務を遂行できるようになります。
製造業が省人化・省力化を実現する方法
製造業が省人化・省力化を実現する方法は、大きく3つのパターンに分けられます。
【方法1】業務の見直し|7つのムダの排除
省人化・省力化の基本は、「ムダをなくす」ことです。後述する2つの方法を検討する前に、まずは既存の業務を見直してそのまま改善できないかを検討しましょう。
たとえば、トヨタ生産方式で有名なトヨタ自動車では、製造現場における「7つのムダ」を排除する取り組みを行っています。
- 加工のムダ
- 在庫のムダ
- 造りすぎのムダ
- 手待ちのムダ
- 動作のムダ
- 運搬のムダ
- 不良・手直しのムダ
こういったあらゆるムダを排除する取り組みは、省人化には直接つながらないかもしれません。しかし、省力化の観点では十分な効果が見込めます。製造現場以外の業務でも、二重作業になっていたり、不必要なやり取りが発生していたりと、至る所にムダが眠っているものです。既存の業務の手順や内容を細かく見直してみることをおすすめします。
関連記事:業務効率化への一歩を踏み出すアイデア「5S」を解説
【方法2】自動化設備の導入によるファクトリーオートメーション
製造現場での省人化・省力化においては、ロボットを始めとする自動化設備の導入によるファクトリーオートメーションが効果的です。従来は人が行っていた作業をロボットに置き換えることができれば、大幅な省人化・省力化を実現できます。
昨今の自動化設備にはAIやIoTなどのデジタル技術が活用されており、従来は人でなければできなかった複雑な作業も自動化できるようになってきました。生産ラインが完全に自動化されており、人は稼働状況をモニタリングするだけといったスマートファクトリーも実現しつつあります。
ファクトリーオートメーションの課題としては、高額なコストがかかることと、自動化設備やデジタル技術に精通した人材が少ないことが挙げられます。費用対効果をしっかりと測定し、必要に応じて外部企業からのサポートも受けながら、自動化を進めていくことが重要です。
【方法3】業務のデジタル化による自動化・効率化
製造業が省人化・省力化を実現するもう一つの方法は、業務のデジタル化です。たとえば、次のような取り組みによって、業務の自動化や効率化を目指します。
- ホワイトボードやエクセルで行っている生産管理をシステム化する
- 紙での在庫管理をシステム化する
- 手書きや紙の図面を2Dデータや3Dデータ化する
- IoTで設備からデータを取得し、生産ラインの状況を見える化する
- 紙の帳票をデジタル化し、文書管理システムで一元管理する
- 解析・シミュレーションによって設計や製造における手間を軽減する
こういった業務のデジタル化は、近年注目されている製造業DXの観点からも重要な取り組みとなります。省人化・省力化を進める過程で業務をデジタル化していき、データが蓄積されるようになれば、新たな製品やサービス、ビジネスモデルを創出するDXに大きく近づくでしょう。
DXによる省人化・省力化を目指すためにすべきこと|積極的なDXの推進
前述したように、省人化・省力化を実現するためには、DXによる取り組みが重要です。例として以下のようなものがあります。
業務プロセスの自動化
IT化により業務の自動化を進めることで、人的な手間や時間を削減できます。たとえば自動倉庫システムや自動組立ラインなどを活用すると、生産プロセスの省力化を実現します。
データの活用
ビッグデータやAI、機械学習を活用して、データを蓄積・分析し、効率的な生産計画や在庫管理、保守計画の策定などが可能になります。ミスや無駄な作業が削減できるので、業務効率が可能になります。
スキル習得と教育
DXによる省人化・省力化では、従業員のITスキルを向上させる教育も重要です。新たな業務領域や技術に対応できるよう、継続的な教育機会を設ける必要があります。
これらに加えて、DXによる省人化・省力化には経営層のリーダーシップや企業文化の変革が欠かせません。これらの取り組みを継続することで、省人化・省力化を実現し、生産性向上や競争力強化を図ることができるでしょう。
まとめ|デジタル化による省人化・省力化を目指す企業の方へ
今回は、製造業での省人化・省力化についてご紹介しました。以前から省人化・省力化に取り組んでいる企業は多いと思いますが、技術の発展によって今まで以上に大きな成果が挙げられる可能性が高まっています。改めて自社の業務を見直し、省人化・省力化に取り組んでみてはいかがでしょうか。
【こんな記事も読まれています】
・【会員限定動画】サプライウェブで実現するマスカスタマイゼーション時代の企業戦略
・製造業における購買・調達業務とは?課題の解決方法も紹介
・ビジネスや技術のトレンドに反応しながら進化を続けるCRMの事例を紹介