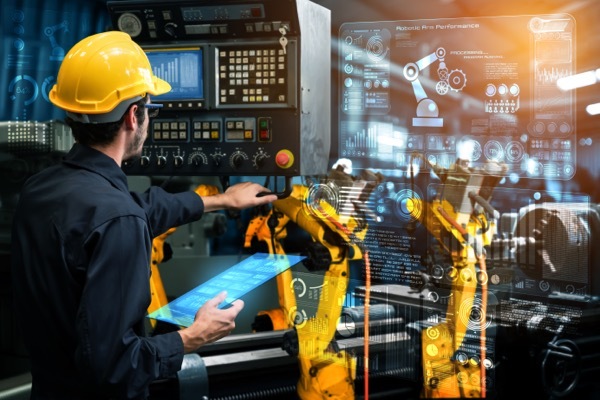
製造業でよく使われる言葉で、「チョコ停」というのがあります。チョコ停とは「チョコっと停止」ということで、製造業における短時間のライン停止を指します。これは、微細なトラブルや調整作業が必要な際に行われるのですが、チョコ停があまりに頻繁に発生すると、生産効率に悪影響を及ぼす可能性があります。
チョコ停はほとんどの場合、現場で即座に解決されて重要視されることも少なく、その影響は見逃されがちです。いつものこととして常日頃見逃していくと、長い期間でみたときに、思ったように生産性が上っていないということになりかねません。
チョコ停は原因を究明して対策をとる必要があります。本記事では、チョコ停とはなにかを解説し、原因究明方法と具体的な対策に焦点を当て、問題解決に向けたアプローチ方法までを考えます。
チョコ停とは
序文でも述べましたが「チョコ停」とは、さまざまな原因により生産ラインが短時間停止する状態を指し、その影響は小さな中断であるにもかかわらず、生産性向上の妨げとなっています。
機械のトラブル、部品の不良、作業員の操作ミスなどが原因となってチョコ停は発生します。停止時間は短くても、頻繁に発生すると、積み重なって生産全体の効率低下につながります。
「チョコ停」は、生産性向上を目指す現代の製造業においては問題視すべき現象です。本来なら達成するはずだった製品の生産スピードは度重なるチョコ停によって低下しており、結果としてリードタイムは増加します。納期の遅れ、在庫の増加を招き、ひいては企業の競争力を低下させかねません。
チョコ停とドカ停
「ドカ停」とは、「ドカっと停止」の略であり、生産ラインが長時間にわたり停止してしまう現象を指します。「チョコ停」が短時間の中断を指すのに対し、「ドカ停」はより深刻で長期間の中断のことを言います。
これは重大な機械故障、予期せぬ停電、原材料供給の混乱など、生産ライン全体に影響を及ぼすなんらかの要因が絡んでいます。そのため、復旧にはより多くの時間と手間がかかります。
ドカ停は企業にとって致命的な生産停止を引き起し、大規模な損失を生じさせます。ゆえに企業はリスクの大きい「ドカ停」に対してはなんらかの備えをしていることが多く、予備機器やバックアップ計画を策定しています。
一方で、迅速に復旧が可能な「チョコ停」に対する抜本的な対策は見逃されがちであり、生産性維持・向上のためにはもっと対策を講じる必要があるでしょう。
その他の16大ロス
16のロス
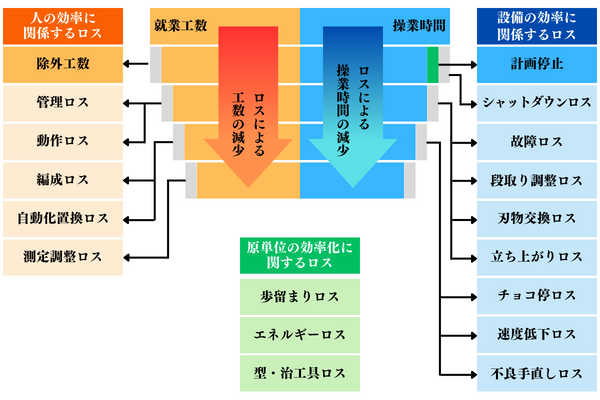
チョコ停はロスの一つですが、生産効率を上げる上での考え方の中で、製造の現場で言われる16大ロスというものがあります。チョコ停もこの中に登場しています。これらを整理してみましょう。
- 人の効率化に関係するもの
- 管理ロス
材料待ちや指示待ちなどの管理上の手待ちロス - 動作ロス
余計な動作、歩行、などレイアウトや作業者のレベル等によるロス - 編成ロス
他の工程、他の台を待っているなどのロス - 自動化置き換えロス
本来自動化できるところをしていないため生じているロス - 測定調整ロス
品質を調整するために測定が必要になったときに生じるロス
- 設備の効率化に関係するもの
- シャットダウンロス
生産が少ない場合やメンテナンスのために設備を停止した際に発生するロス - 故障ロス
設備の故障によって発生するロス - 段取り調整ロス
製品の切り替え時、準備のために要する時間のロス - 刃物交換ロス
刃物の交換に必要な時間のロス - 立ち上がりロス
機械の立ち上がり時、初期状態で品質が安定しないときに発生するロス - チョコ停ロス
意図せぬトラブルで一時的に機械を停止させたときに発生するロス - 速度低下ロス
設備のスピードが通常より低下したときに発生するロス - 不良手直しロス
不良品を修正するための時間が発生した際のロス
- 原単位の効率化に関係するもの
- 歩留まりロス
投入原料の重量に対する製品の重量減少分のロス - エネルギーロス
電力、燃料、ボイラーで発生する熱、エア圧、水などのロス - 型・治工具ロス
製品を作るために必要な治具、工具、金型などの製作補修にかかるロス
このように、製造現場には数多くのロスがあります。これらのロスは完全になくすことはできませんが、逆にいうと数多く改善の余地があり、まだまだ効率は上がるということでもあります。
次に述べるように、チョコ停1つとっても原因がいろいろあるわけであり、製造現場の改善には終わりがないと考えられます。
チョコ停が起きる原因
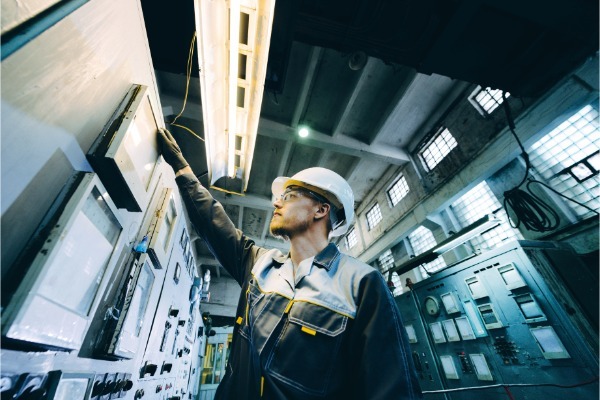
チョコ停が発生する原因を追究してみると、どれも日常的に発生している「発生して当然」の事象であることに気が付きます。こうした事象はその場ですぐに片づけられてしまい、重要視されません。「ラインが停止する」という事実は同じであるにもかかわらずです。どのようなものがあるか見ていきましょう。
清掃やメンテナンス不足
材料を切削するときに発生する木くずや金属くず、プラスチックのバリなどをそのままにしておいたために発生するトラブルがあります。機械が止まらないまでも、品質に影響が出てしまい、不合格で作り直し、あるいは修正ロスが出る場合もあり得ます。
たいていの場合、こうした修正ロスを出さないようにするために途中で清掃やメンテナンスを入れますが、この時機械を止めればチョコ停になります。頻回の実施が必要である場合、清掃やメンテナンス不足が原因というより、機械の方式や作業方法、もしくは原材料を改善したほうがよいのではないかとの考え方が浮上します。
清掃やメンテナンス不足によるチョコ停は見逃されがちですが、改善の余地があるといえます。
センサー類のエラー
センサー自体の汚れ、接点の接触不良、ケーブルの不良、センサーそのものの故障などがチョコ停につながる場合があります。センサーからのデータによって制御されている機械の場合、異常値でエラーを起こしたり、意図せぬ動作を認めて停止操作をしたりするため生産がストップするという現象です。
センサーが不正確なデータを検知したり、故障したりすると、機械は誤った情報に基づいて動作する可能性が生じます。安全性を確保するために、たいていの場合異常値を検知すれば機械は停止するようにできています。これがチョコ停となりますが、原因がセンサーの不良であるというのは、本来センサーを設置した目的にかなっておらず、センサーの設置方法やセンサーそのものを見直す必要性も生じてきます。
品質不良によるエラー
品質不良によるエラーで発生するチョコ停とは、前工程での不具合から発生します。例えば、前工程の加工が不十分で寸法がわずかに大きかったため、次工程で治具にはまらない場合、少し削ってからはめるか、前工程に戻すことになります。
一見何でもないことのように思えますが、本来ゼロであるべき手戻りや修正であり頻回に発生すると大きなロスになります。
設備や治工具の設計によるエラー
製造工程の途中で使う組み立て用の治具などは寸法公差を考慮して作られます。その治具が寸法公差のどちらかに偏っているために、はまりにくくなってしまうことがあります。あるいは機械設備の投入口や取り付け部位の寸法に合っていないといった場合、修正加工、手戻りが発生します。
こうした治具や設備の設計に問題があると、治具や設備にあわせるための修正、再加工のためのチョコ停が発生します。この時間が累積すると大きなロスとなってしまうのです。
治具や設備を外注する場合、設計時に寸法のバラつきについて十分考慮して打ち合わせておく必要があります。簡単に見られがちな箇所ですが、一度作ってしまうと作り直しが難しいものであるだけに慎重に行いましょう。
チョコ停が工場に与える影響
前段で述べてきたように、簡単に復旧できるからと言ってチョコ停は決して軽視してよいものではありません。それは、チョコ停の影響を数値として計算するとよくわかります。1回のチョコ停が長ければ長いほど、回数が多ければ多いほど、工場としてのロスは大きくなっていきます。
ここでは、チョコ停ロスを数字で把握するための計算式を紹介します。
チョコ停ロスの計算式
工場の稼働率を計算する数式は以下に示した式Aの通りです。
式A:稼働率(%)=実際の稼働時間÷本来稼働すべき時間
「実際の稼働時間」とは実際に機械設備が動いて製品を製造していた時間のことで、本来稼働すべき時間から停止時間を引いた値です。
チョコ停の影響を確かめるには、この式の本来稼働すべき時間にチョコ停の時間を加えます。これを式Bとします。
式B:稼働率(%)=実際の稼働時間÷(本来稼働すべき時間+チョコ停した時間)
チョコ停した時間があると、式Bの稼働率は式Aの稼働率よりチョコ停した時間の分だけ低くなります。つまり、式Aの稼働率と式Bの稼働率の差がチョコ停による稼働率低下の影響を表します。
例えば、実際の稼働時間が6時間30分だったとしましょう。本来稼働すべき時間は8時間です。すると工場の稼働率は式Aによって以下の通りです。
81.25%=6.5時間÷8時間
工場の稼働率は81.25%でした。工場が停止していた時間は8時間-6.5時間で1.5時間です。調べたところ、
✔ 計画的に停止した時間・・・1時間
✔ チョコ停時間の合計・・・0.5時間
でした。チョコ停を加味した稼働率は式Bによって以下の通りとなります。
76.47%=6.5時間÷(8時間+0.5時間)
チョコ停時間を加味したところ、工場の稼働率は76.47%でした。この工場のチョコ停による稼働率悪化は以下の通りです。
4.78=81.25%-76.47%
この式の結果から、0.5時間のチョコ停によって工場の稼働率が4.78ポイント低下しているということが言えます。
チョコ停への対策手順
チョコ停による影響を数値で知るための数式を紹介しましたが、実際にチョコ停の時間を調べ、その影響を評価し、原因を特定して改善するにはどのような方法論があるのでしょうか。
ここでは、ワークサンプリングという方法を用いた調査方法と、原因の特定、改善効果の確認方法を解説します。
①チョコ停のロスを可視化する(ワークサンプリング)
チョコ停が問題となっている製造ラインがあるとしましょう。どれくらいチョコ停が発生しているのか可視化する方法を考えます。しかし、稼働時間中ずっと全体を監視するのは困難です。
そこで、ワークサンプリング法という稼働分析の手法が有効です。ワークサンプリング法は、一定の時間内に回数を決め、人や機械の状態を瞬間的に観察して統計をとり確認する方法です。例えば、ある製品の製造工程を100回観測したところそのうち90回稼働していたら、稼働率は90%だろうと推定をします。
製造工程の一部分をサンプリングしてそこから全体を推定するため、ずっと監視し続けるより手間がかからず、全体の稼働状況をほぼ問題ない精度で把握できます。
②原因を特定する
ワークサンプリング法によってチョコ停の影響が明らかになったら、次はその原因を特定していきます。ワークシートを作成して、現場でチョコ停の原因別に発生回数を書いていきます。これを集めて統計を取りパレート分析を行います。
パレート分析とは、縦軸に回数、横軸にチョコ停の原因を配置して棒グラフを作る方法です。回数の多い順に左から並べていくと、どのような原因での停止が多いのかわかってきます。
チョコ停の原因がさまざまである場合は一度にすべての対策をするわけにもいきません。しかしパレート分析によって原因とその頻度が明らかになれば、優先的にどの原因の対策をとるべきかがおのずと明らかになってくるでしょう。
③改善効果の確認
チョコ停の改善に向けて取り組むべき原因が明らかになったところで、さっそく改善策を立案して取り組んでいきたいところですが、その前に果たしてその取り組みの結果どれくらいの効果が出るのか、数値で表しておきます。改善にも費用が掛かるため、費用対効果を判断する必要も出てくるのです。
チョコ停による損失額を明らかにして、立案された対策によってその損失額がなくなるのであれば、少々の費用をかけても実行する価値があると判断できます。判断を行うための計算式は以下の通りです。
損失金額 = チョコ停時間 × 時間当たりの生産個数 × 製品単価
もともとの生産能力が高く、時間当たりの生産個数が多ければ多いほど、単価の高い製品を製造していればいるほど、その損失金額も大きくなります。そのような場合、チョコ停といえども直ちに対策しなければならないことが分かってくるでしょう。
チョコ停問題の発見と解決に向けたアプローチ
ワークサンプリングやパレート分析によってチョコ停の主な原因が明らかになったとしても、原因同士が複雑に絡み合っている場合があります。このような場合、現場でもはっきりと原因を特定できず、根本原因に対する対策が取りにくい場合があります。
ここでは表面的な原因ではなく、真の原因を突き止めるための2つの方法を紹介します。
4M分析
4M分析は、Man(人)、Machine(機械)、Material(材料)、Method(方法)の4つの要素を対象に分析し、改善を行う手法です。4M分析で行う、課題の発見や問題解決方法について4つのMごとに解説していきます。
Man(人)
人にかかわる要素について評価を行います。スキルや研修状況、モチベーションなどを考慮して課題がないのか調べます。人にかかわる要素内に課題があれば、職場環境の整備、教育研修の導入などを行って改善します。Machine(機械)
機械の性能や稼働状態を評価します。故障の有無、メンテナンスの頻度などを検討します。最新の技術や機械の導入、予防保全の実施が必要となる場合もあります。故障発生時に迅速に対応できる体制も必要です。Material(材料)
原材料や部品の品質、供給の安定性を評価します。これには原材料に対する正しい理解が必要です。品質管理、サプライヤーの信頼性、在庫管理も改善項目となります。Method(方法)
作業手順やプロセスフロー、生産計画などが最適な方法なのか評価します。人、機械、材料の要件をバランスよく組み込んで全体最適を考慮するのが重要です。方法論が属人化しないよう、マニュアル化が必要な場合もあるでしょう。
なぜなぜ分析
なぜなぜ分析は、「なぜその問題が発生したのか」について問い、その答えについてもまた「なぜか」を問うという方法で5回「なぜ」を繰り返せば本当の原因にたどり着くという方法です。
なぜなぜ分析は複雑な問題を単純な要因に分解し、ひとつずつ質問していき、因果関係をあきらかにする手助けをします。たとえば、「最終工程でチョコ停が頻発する」という問題が発生したとします。それは以下のような順番で5回質問を繰り返せば、だいたい真の原因にたどり着きます。(図2)
なぜなぜ分析
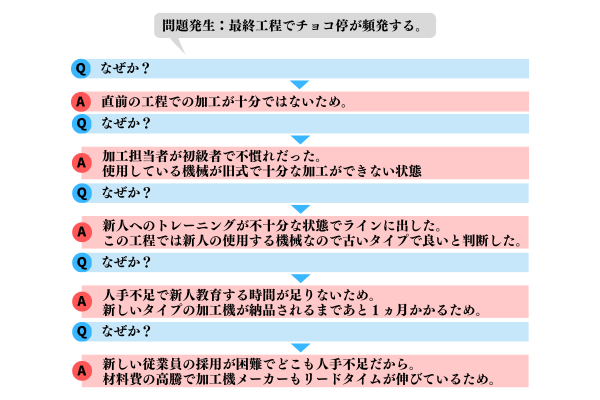
このように、なぜなぜ分析は、表面的ではなく問題を深堀することで根本原因を把握することができます。根本原因とは自社内の問題ではなく、材料の高騰や人手不足など、社会的な背景を含んでいて改善が簡単ではない場合もあります。しかし、根本原因が分かってさえいれば代わりの手段は考えられるはずです。
なぜなぜ分析は製造業にとって持続的な改善を実現し、生産効率や品質向上に寄与する重要な手法です。
チョコ停対策にはIoTが有効
チョコ停への対策手順の項でチョコ停の原因究明方法として「ワークサンプリング」のことについて述べました。チョコ停の原因を探るのに、人間が常時監視するわけにもいかないので、「サンプル」データから全体を推測するという方法でした。しかし最近では、IoT技術を活用すれば、ほぼ常時監視することも可能です。
製造ラインに監視カメラを取り付けておき、ラインに取り付けたセンサーと連動させます。センサーが異常値を感知すれば、カメラが作動し、チョコ停の現場を押さえます。さらにチョコ停時のセンサー値を記録して後で分析に使用できます。
このようなIoTを用いた方法でチョコ停の監視を行えば、チョコ停の記録は自動的にデータとなるので何らかの形で活用ができます。改善活動はもちろんのこと、将来的にはAIに機械学習をさせて故障やドカ停の予告などもできるようになるかもしれません。
【こんな記事も読まれています】
・【会員限定動画】サプライウェブで実現するマスカスタマイゼーション時代の企業戦略
・製造業における購買・調達業務とは?課題の解決方法も紹介
・ビジネスや技術のトレンドに反応しながら進化を続けるCRMの事例を紹介