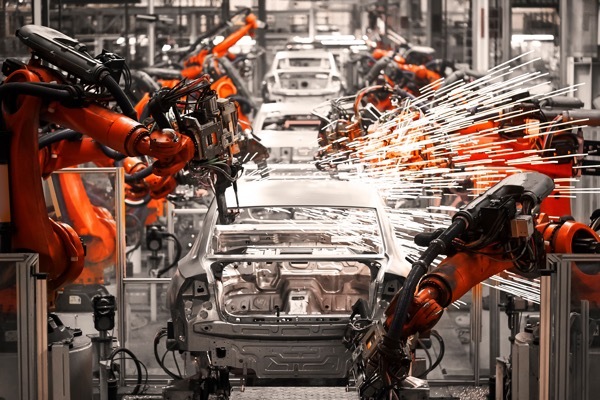
本記事は、木村哲也氏の著書『Small Factory 4.0 第四次「町工場」革命を目指せ! ― IoT の活用により、たった 3 年で「未来のファクトリー」となった 町工場の構想と実践のすべて』=株式会社三恵社、2018年8月1日発行の中から一部を抜粋・編集しています。
(1) 5つの具体的方針の立案
私が旭鉄工に転籍したのは 2013(平成 25)年です。それ以来、前述のように改善活動を進めてきました。運動は少しずつ成果をあげていましたが、なかなか好転しなかったのが、不良品・客先不具合の問題でした。
そこで現場での改善活動を振り返ってみると、2014(平成 26)年までは、
①現場でできることを実施
②過去トラブル点検がメイン
③未然防止活動が少ない
という状態であったことがわかりました。
活動のマンネリ化によって効果があがらず、その結果、発生した不具合の処置に追われてしまって未然防止活動ができないという悪循環に陥っていたのです。社員も「不良なんか減りっこないよ!」とか「客先不具合って毎月あるよね」といった極めて低い意識レベルにとどまっていました。
ここから脱却するには、目標を具体的でわかりやすいものにする必要があると考えました。そこで、2015(平成 27)年からは、「不良品や客先不具合」について、以下のような方針を立てました。
(a)客先不具合低減のために実施すべき活動の明確化
品質向上活動を活動実施単位まで細分化し、遅れ/進みを「視える化」
(b)製造部門任せではなく、品質管理部門スタッフも一緒になって活動
製造課単位で品質管理部門スタッフ一人を担当者としフォロー
(c) 未然防止活動への転化
職制による現場観察、いじわるテストの定着、異常処置対応の訓練実施による不具合流出防止
(d) 客先不具合低減のために必要なリソーセス(人員)の増員
西尾工場機械製造部の班長増員
(e) 他の事例から学ぶ
客先不具合の発生原因を一般解化し、他職場へ横展開
(2) キーワードは「見る、視る、観る」
さらに、この「不良低減活動」全体に通底するキーワードとして「見る、視る、観る」という言葉を掲げました。
「職位(立場)によって、み方を変えよう」という意味です。
①見る
作業者は、正品であること、また作業ポイントをしっかり検見する。お客様に届けるものは、製品でなく商品である。その確からしさを保証するために、しっかりと確認する。
②視る
監督者である班長・係長が、しっかりと作業者を監視する。それは、自分が教えたことをしっかり理解し、その通り作業を遵守しているかを確認してあげるといったことで、誤りがあれば教え直し、困り事があれば作業者と一緒に考え、改善していく。
③観る
管理者である社長から課長までが、今、現場で起こっていることを観察する。つまり、組織の運営がうまくいっているのか(人員の不足、指導方法の正誤等)、現場の状況を自己の目で観察する。
この3つが、ベースの「みる」です。
それまで私たちは、製品ばかりみてきました。そこから脱却し、3つの「みる」を原理原則として社内に浸透させたうえで、高い目標値を与えることで、品質風土の構築と目標達成に近づく手段を打ち出せると考えたのです。
その後、前述の「サイクルタイムモニター」を利用した可動率の確認と、「ちょっとした設備の動きや作業方法」「毎回止まる慢性的なチョコ停」などの改善により、とにかく止まらないラインを作り出そうとした結果、納入不良は 2015 年比で約 4 分の 1 以下にまで低減することができました。
結果を出すことができたのは、「サイクルタイムモニターを活用した可動率向上」運動だけによるものではありません。この「見る、視る、観る」のキーワードが全社的に浸透していったからです。
(3)「いじわるテスト」
社内では、(1)(c)で述べたように「いじわるテスト」と呼ぶ「検出力確認」を実施しています。「検出」とは、大半が正常な品物が生産される中にごくまれに発生する正常でない品物、つまり不良品を発見して取り除くことです。
「いじわる」 と言うと聞こえは悪いですが、作業者にいじわるをするわけではなく、「目視検査」といって、品物を目でチェックして不良品を見つけだす工程において、しっかりと不良品を見つけることができるかという検査を実施することです。
具体的な方法は以下の通りです。
――休憩時間に職制が 「こっそりと」 不良品を1個混ぜておきます。そして、休憩時間後に作業者がその不良品を目で見て発見できるかどうかを、これまた職制が 「こっそりと」 観察し、きちんと不良品と発見して不良品を識別する箱に入れたかどうかを確認します。それから、
OK ⇒ 合格と作業者に伝えます。「これからも正しい検査よろしく!」
NG ⇒ 不具合品を見逃していることを伝えます。
さらに、なぜ見逃したのか(判断ミス、見えなかった、見なかったなど)を作業者と職制とで確認し、是正していきます―。
このテストには、作業者の緊張感維持や、職制との信頼関係構築を促すという効果があります。また、その際に重要なのは、テスト後に見落とした理由について、作業者の肚に落ちるように話し合うことです。
「いじわるテスト」というネガティブな言葉ですが、作業者が不良を発見する力を維持・向上させるためのポジティブな活動なのです。
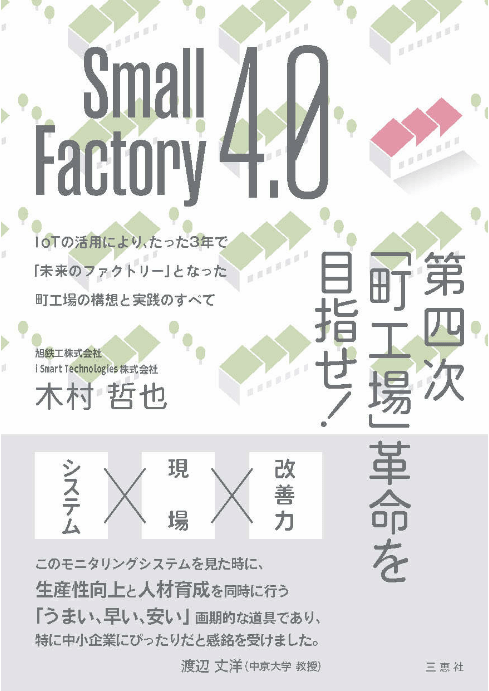
1992 年東京大学大学院工学系修士修了、トヨタ自動車㈱に21 年勤務。 主に車両運動性能の先行開発・製品開発に従事。また、生産調査部でトヨタ生産方式を学び内製工場および社外の指導を経験した。
2013 年に旭鉄工㈱に転籍、生産調査部での経験を生かし、生産性・組織や仕事の進め方など経営全般を大きく改革。その中で製造ライン遠隔モニタリングシステムを構築・運用、生産性向上と人材育成の面で大きな成果をあげる。 他の中小製造業でも同様に生産性向上を実現するため、このシステムをサービスとして提供する「i Smart Technologies ㈱」を設立した。
現在、本システムは中小企業を中心に100 社以上に導入され、「第7回 ものづくり日本大賞 特別賞」をはじめ数多くの賞を受賞した。また2018 年にはその実績が認められ、タイ王国工業省とシステム導入・発展に関する「覚書」を締結した。
※画像をクリックするとAmazonに飛びます
【こんな記事も読まれています】
・【会員限定動画】サプライウェブで実現するマスカスタマイゼーション時代の企業戦略
・製造業における購買・調達業務とは?課題の解決方法も紹介
・ビジネスや技術のトレンドに反応しながら進化を続けるCRMの事例を紹介