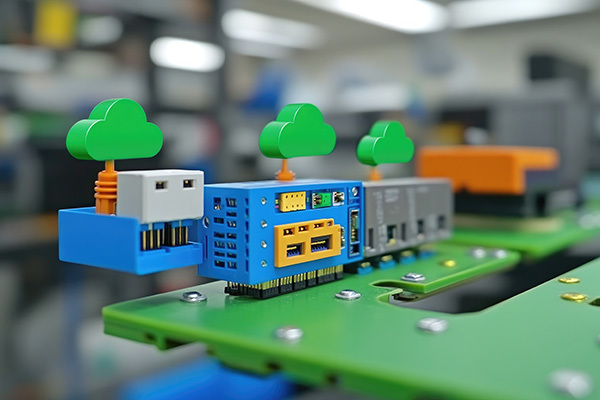
製造業のデジタル変革を加速させる鍵となっているSDN(Software Defined Networking)。
従来のハードウェア依存型ネットワークから脱却し、ソフトウェアによる柔軟な一元管理を実現するこの革新的技術は、製造現場に大きな変革をもたらしています。
複数工場の統合管理から生産ラインの効率化まで、SDNは製造業の未来を形作る重要な基盤技術として注目を集めています。
自動化による業務効率の劇的な向上、コスト構造の最適化、そして高度なセキュリティ対策の実現—これらすべてがSDN導入によって可能になるのです。
本記事では、製造業におけるSDN導入の具体的メリットを解説するとともに、国内外の先進導入事例や、成功するための段階的な導入手順まで徹底的に掘り下げます。
「つながる工場」の実現に向けた第一歩として、ぜひご活用ください。
目次
SDNとは?
SDN(Software Defined Networking)とは、ネットワークの制御機能をハードウェアから分離し、ソフトウェアで一元管理するネットワーク技術です。
従来型ネットワークでは、各機器(ルーターやスイッチなど)が個別に設定され、変更作業が煩雑でした。
一方、SDNでは「コントロールプレーン」(制御部分)と「データプレーン」(データ転送部分)を分離することで、ネットワーク全体を統一的に管理できます。この仕組みにより、ネットワークの設定変更が迅速になり、新しいサービス導入も素早く行えるようになります。
製造業においても、複数拠点のネットワーク管理や生産ラインの効率化に役立つ技術といえるでしょう。
製造業におけるSDN導入の3つのメリット
製造業においてSDNを導入するメリットには、以下の3つがあげられます。
- 自動化による効率向上と人的リソースの削減
- コスト削減とROI(投資対効果)の向上
- セキュリティの強化
順番に見ていきましょう。
メリット1:自動化による効率向上と人的リソースの削減
SDNを導入することで、ネットワーク管理の多くの作業が自動化され、工場の効率が大幅に向上します。
従来のネットワークでは手作業による設定が必要でしたが、SDNではソフトウェアによる一元管理が可能になり、人的ミスのリスクも低減されます。
製造ラインの変更や新製品の導入時にも、物理的な機器の追加や複雑な設定変更なしに、ネットワーク構成を素早く変更できる点が大きな魅力です。
生産需要や資源の可用性に基づいて、工場設備の機能をプログラミングできるため、市場の需要に合わせた柔軟な生産体制を構築できるようになります。
メリット2:コスト削減とROI(投資対効果)の向上
SDNの導入は、高価なネットワーク機器への投資を抑えることができ、全体的な設備投資(CAPEX)と運用コスト(OPEX)の削減につながります。
一部のSDN製品は無料で提供されており、大きな初期投資を必要としない点も魅力的です。
SDNはレイヤー1からレイヤー3までのネットワークモデルをサポートしているため、高価なネットワーク機器を購入する必要性が低減されます。
また、ベンダーロックイン(特定のベンダーに依存する状態)から解放されるため、企業はより革新的でコスト効率の良いネットワーク構築が可能になります。
中央集権的なコントローラーと簡素化されたネットワーク設計により、高いROIを実現できる点も製造業にとって大きなメリットとなっています。
メリット3:セキュリティの強化
SDNの導入により、製造現場のセキュリティ対策が大幅に強化されます。
SDNは、マイクロセグメンテーション(ネットワークを細かく分割して保護する手法)の実装を容易にし、攻撃対象領域を縮小することでセキュリティ体制を強化します。
また、特定のネットワークトラフィックを選択して詳細な検査のためにリダイレクトする機能も備えており、セキュリティ監視の精度が向上します。
製造業では、IT(情報技術)とOT(運用技術)の統合が進む中、SDNはこれらのネットワークシロを排除し、企業全体のセキュリティポリシーを一貫して適用できる環境を提供します。
製造業におけるSDN導入事例3選
ここからは、製造業におけるSDN導入の事例を3つ紹介していきます。
順番に見ていきましょう。
事例1:自動車部品メーカーの生産設備ネットワーク構築
ある大手自動車部品メーカーが、トランスミッションなどの精密部品を製造する工場にSDNを導入しました。
従来は各設備の情報を手動で収集していましたが、SDNにより生産設備間のネットワークを一元管理できるようになりました。GUI画面でネットワーク全体の構成や通信状況を可視化し、仮想ネットワークを効率的に管理・制御できます。
また、セキュリティ階層の異なる仮想ネットワークを柔軟に構築できるため、ウイルス感染やサイバー攻撃時の被害範囲を最小限に抑えることが可能になりました。
この導入により、工場のIoT化が進み、生産性向上とセキュリティ強化の両立を実現しています。
事例2:建設機械メーカーの次世代工場ネットワーク導入
ある建設機械メーカーが、将来的なIoT活用による「つながる工場」の実現を見据え、SDNを活用した次世代工場ネットワークを導入しました。
既存のネットワーク機器を活かしつつ、SDN対応製品を部分的に導入することでコストの最適化を図っています。仮想ネットワークにより、制御系システムのセキュリティを確保し、GUI画面による容易なネットワークの設計・設定を実現しました。
また、IoT活用によるデータ量の増大に応じた迅速かつ柔軟なネットワークの拡張が可能になり、サイバー攻撃対策の自動化も実現しています。
この導入により、工場の柔軟性と安全性が向上し、競争力強化につながっています。
事例3:清掃用品レンタル企業の工場内ネットワーク刷新
全国に多数の工場を持つ清掃用品レンタル企業が、SDN技術を活用した工場内ネットワークを構築しました。
複雑化した工場内ネットワークの管理や、トラブル発生時の早期復旧が課題となっていましたが、SDNの導入により改善されました。
ネットワーク全体を物理的に統合し、本部から一元管理できるようになったため、管理の効率化やトラブル対応の迅速化が実現しました。
また、ネットワークを用途に応じて論理的に分割することで、ネットワークの遅延抑制やセキュリティレベルの変更など、柔軟な構成変更が可能になりました。
この導入により、無線モバイル機器などのデジタル技術の活用も容易になり、工場のスマート化が進展しています。
製造業におけるSDN導入の手順7ステップ
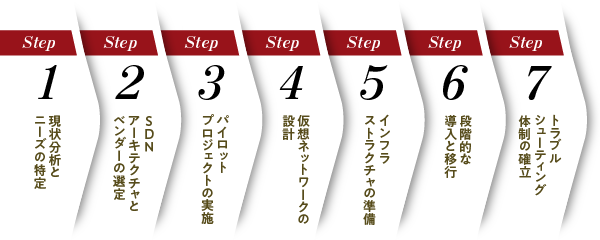
SDN導入時の手順は、以下の7ステップに分けられます。
1.現状分析とニーズの特定
2.SDNアーキテクチャとベンダーの選定
3.パイロットプロジェクトの実施
4.仮想ネットワークの設計
5.インフラストラクチャの準備
6.段階的な導入と移行
7.トラブルシューティング体制の確立
順番に解説していきます。
ステップ1:現状分析とニーズの特定
製造業でSDN(Software-Defined Networking)を導入する最初のステップは、現在のネットワーク環境を詳細に分析することから始まります。
工場内には金属工作機械、プラスチック成形機、組み立て設備、搬送関連機器、検査機など多様な設備が存在しており、それぞれの接続状況や通信要件を把握する必要があります。
SDN導入によって解決したい課題(情報収集の自動化、セキュリティ強化、運用効率化など)を明確にすることが重要です。
製造現場特有の要件(床にケーブルを這わせられないなど)も考慮し、工場環境に適したネットワーク設計を検討しましょう。
ステップ2:SDNアーキテクチャとベンダーの選定
製造業に適したSDNアーキテクチャとベンダーを選定する段階では、使いやすさと専門知識の必要性を重視します。
工場の設備間ネットワークは、製造部門とIT部門が共同で構築する必要があるため、専門知識がなくても操作できるGUIの使いやすさが重要な選定ポイントとなります。
また、海外ベンダーと国内ベンダーの対応の違いも考慮し、サポート体制が充実しているベンダーを選ぶことが望ましいでしょう。
工場の特殊な環境(ケーブルラックを使った配線など)に対応できるベンダーであるかも確認が必要です。
ステップ3:パイロットプロジェクトの実施
本格的な導入前に、小規模なパイロットプロジェクトを実施して効果と課題を評価することが重要です。
まずは工場にある特定の生産ラインにSDNを適用し、実際の製造環境での動作を確認するとよいでしょう。運用チームのスキルギャップを特定し、必要なトレーニングを計画することも重要な目的の一つとなるでしょう。
ステップ4:仮想ネットワークの設計
SDNの大きな特徴である仮想ネットワーク(VTN: Virtual Tenant Network)の設計は、製造現場のセキュリティと運用効率化に直結します。
IPアドレスの重複による設備の誤作動といった過去のトラブル事例も、仮想ネットワークによるセグメント分けで防止できるようになりました。
ステップ5:インフラストラクチャの準備
SDN導入に向けて、物理的および論理的なネットワークインフラを準備します。
製造現場では、SDNコントローラーの設置場所の選定と環境整備が重要になります。工場特有の環境条件(温度、湿度、振動など)を考慮し、機器の設置場所や保護対策を検討する必要があるでしょう。
ネットワークトポロジの再設計では、生産設備のPLCをSDNにつなげ、稼働状況などのデータを収集するサーバーへ提供する構成を構築します。
監視システムの拡張も重要で、SDN特有の指標を含めた監視体制を整えることで、トラブル発生時の早期発見・対応が可能になります。
ステップ6:段階的な導入と移行
製造業でのSDN導入は、生産への影響を最小限に抑えるため、段階的に行うことが重要です。各フェーズでは、移行計画の策定、関係者への通知、ダウンタイムの最小化、問題発生時のロールバック手順の準備を行うことが大切です。
導入時には、ケーブルをスイッチにつなぎGUIで簡単な設定を行うだけで拡張できるSDNの利点を活かし、工場でも安心して運用できる環境を整えます。
段階的な導入により、各段階での成果と課題を評価し、次のフェーズに反映させることで、より効果的なSDN環境を構築できるでしょう。
ステップ7:トラブルシューティング体制の確立
SDN環境でのトラブルシューティング手法を確立し、問題発生時に迅速に対応できる体制を整えることが重要です。
ネットワークスライス分離技術を活用すれば、問題のあるネットワークスライスを特定し、他のスライスへの影響を最小限に抑えることが可能になります。
SDNコントローラーが適用しているフロールールを検証し、意図した通りに動作しているか確認する手法も有効です。
GUI画面でネットワーク全体の構成や通信状況を可視化できるため、トラブル機器の特定が容易になり、早期復旧に向けた対策を講じることができます。
製造部門でも対応できるよう、トラブルシューティングの手順をマニュアル化し、定期的な訓練を行うことで、IT部門に頼らない自律的な運用体制を構築しましょう。
SDN導入時には運用管理できる人材の確保をしておく
製造業でSDNを導入する際、最も重要な注意点は運用管理できる人材の確保と育成です。SDNは基本設定や構築は比較的簡単ですが、運用には物理ネットワーク(アンダーレイ)と論理ネットワーク(オーバーレイ)など、幅広いレイヤーの知識が必要となります。
現時点では、SDNに関する豊富な知識やスキルのある実務経験者が少なく、運用管理のできるネットワークエンジニアの確保が困難な場合もあるでしょう。
特に製造業では、工場の設備間ネットワーク構築には設備や建屋の知識、ケーブル取り回しなどの専門的な知識が必要で、情報システム部門だけでは対応が難しいという現実があります。
製造部門とIT部門が共同でネットワークを構築し、運用および保守については基本的にIT知識の乏しい製造部門だけで対応しなければならないケースも多いため、使いやすいGUIを備えたSDNソリューションの選定が重要です。
SDNの今後の発展
SDN市場は拡大すると予測されています。この成長を支える要因として、デジタルトランスフォーメーション、クラウドコンピューティング、IoTの普及が挙げられます。
製造業においては、工場の設備間ネットワークの効率化や自動化に大きく貢献する可能性を秘めています。
今後のSDN技術は、モバイルネットワークとの融合、IoTなどのセンサー技術との連携、ビッグデータや深層学習技術との統合といった方向に発展していくでしょう。
特に注目すべきは、パブリッククラウド、オンプレミス環境、広域ネットワークを融合させるSD-WAN技術の一般化です。さらに、AIや生成AIの活用によるネットワーク管理の高度化も期待されています。
製造業では、ネットワークの仮想化によって、ハードウェアコストの削減と機能の集約が進み、設備投資や運用コストが大幅に低減する見込みです。
2025年以降は、SDNがさまざまな産業へと拡大し、ビジネスの柔軟性と効率性を向上させる基盤技術として定着するでしょう。
まとめ
SDN(Software Defined Networking)は、ネットワークの制御機能をソフトウェアで一元管理する革新的な技術です。
製造業におけるSDN導入の主なメリットは以下の3点です。
- 自動化による効率向上と人的リソースの削減
- コスト削減とROI(投資対効果)の向上
- セキュリティの強化
ただしSDN導入時は、運用管理できる人材の確保が重要です。
SDN市場は今後も拡大が予測され、製造業では工場の設備間ネットワークの効率化や自動化に大きく貢献すると期待されています。
AIやIoTとの連携、SD-WANの一般化など、さらなる技術革新により、ビジネスの柔軟性と効率性を向上させる基盤技術として定着するでしょう。
【注目コンテンツ】
・DX・ESGの具体的な取り組みを紹介!専門家インタビュー
・DX人材は社内にあり!リコーに学ぶ技術者リスキリングの重要性
・サービタイゼーションによる付加価値の創造と競争力の強化