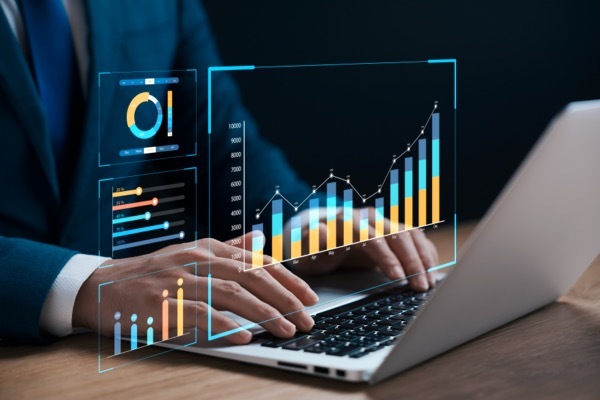
新製品を開発する際、品質の確保(品質保証)は非常に重要です。品質の確保のために策定され、主に自動車産業で利用されているものが「APQP(“Advanced Product Quality Planning”:先行製品品質計画)」です。
APQPは「設計や開発が終わってから品質の確保を行う」のではなく、「あらかじめ製品の企画段階から品質計画を盛り込む」という考え方がもとになっています。現代では、自動車産業だけでなく、他の業界などでも活用されています。
本記事では、APQPの基本的な考え方、品質管理における役割と目的・目標、IATFとの関連、5つのフェーズ、成功のために導入すべき体制やポイントについて詳しく解説します。
APQPとは
はじめに、APQPの定義や策定された背景、5コアツール・AIAG・IATFなどとの関連性について解説します。
APQPの定義
APQPとは“Advanced Product Quality Planning”の略称です。日本語で「先行製品品質計画」と呼ばれます。
APQPの名称に「先行(Advanced)」がついているのは、品質の確保に対する策定を開発が終わってから実施するのではなく、開発よりも「先に(=先行して)」品質計画を練り始めるからです。つまり「あらかじめ品質の確保も計画に盛り込んでから開発を進める」という考え方になります。
現代において、APQPは自動車産業に特化した国際規格「IATF16949」の核となる考え方であり、製品開発プロセス全体を管理するための重要なツールです。量産までの一連のプロセスにおいて「品質」の観点から計画的に管理する手法であり、製品開発における品質保証の要として多くの企業で活用されています。
APQPの歴史と発展|APQPとIATFとの関係性
APQPという「開発初期から品質を確保するための計画を盛り込む」製造手法・概念は、1980年代に米国で発展したとされています。
1988年、アメリカの主要自動車メーカーが部品提供取引先(サプライヤー)に、どのレベルの品質のものを納品してほしいかを示し、サプライヤーとの合意のもと品質マネジメントおよびその手法に関する共通仕様の手引書が作られました。これがAPQPで、マニュアルの初版発行は1994年とされます。
現在、APQPについての概要やどのように運用するかについては、AIAGが手引書を発行し策定しています。
(参考)AIAG:(APQP) Advanced Product Quality Planning
【関連用語】AIAG
(出典)一般社団法人 日本自動車工業会:AIAG リリース 仮訳「AIAG、自動車工業プロジェクト世界協力協定に調印-ODETTE、JAMA、JAPIAと」
AIAGは1982年に創立された非営利同業団体であり、およそ1,600社の自動車およびトラックメーカーとサプライヤーが加わっている。AIAGの目的は、開かれた協議の場を設けて、そこで加盟各社が解決策を開発・推進することにより、自動車業界の一層の発展を図ることである。その活動の焦点は、全体を通して取引相手を含めた事業のプロセスと慣行を絶えず改善することにある。
また、このAPQP策定と同時期ごろにAPQPと合わせて「5コアツール」と呼ばれる、品質確保のための各ツールおよび仕様書や手引書が策定されています(5コアツールについては後述)。
さらにAPQPの手引書初版が発行されたあと「QS-9000」という品質管理規格が作られ、APQPと紐づけられるようになりました。「QS-9000」は「ISO/TS16949」を経て、現在の自動車業界では「IATF 16949:2016」が品質マネジメントシステムの規格となっています。APQPは、現在もこの「IATF 16949:2016」とともに品質管理の指標となっているのです。
【関連用語】IATF 16949(自動車)
(出典)JQA:一般社団法人 日本品質保証機構
IATF 16949は自動車産業に特化した品質マネジメントシステムに関する国際規格です。
世界の多くの自動車メーカーが、自動車部品のグローバルな調達基準として採用しています。
品質管理を開発初期から行う方針は、アメリカだけでなく同じように自動車工業の盛んなドイツでも進んでいます。VDA(ドイツ自動車工業会)も同様のものを発行しており、「Design For Six Sigma(DFSS:設計開発のためのシックスシグマ)」をベースとしています。
シックスシグマは、APQPと同様に「品質を高いレベルで確保する」という考えに基づく経営理論ですが、主に経営管理のために使われる手法です。
【関連記事】
シックスシグマ(6σ)とは?統計分析を用いた経営・品質管理手法をわかりやすく解説
APQPとQC工程図の関係
APQPを用いた品質管理の中で、製造プロセスのうちどの工程でどのように管理しているかという一覧表(コントロールプラン)を作成することが求められています。これは、現在の日本の製造業で使われる「QC工程表(QC工程図)」がその内容をほぼカバーするものです。
(参考)
AIAG:(CP) Control Plan
ISO/TS16949:2009 規格要求事項/解説
【関連記事】
QC工程表(QC工程図)とは?作り方や項目例、品質管理の指標を解説
APQPと「5コアツール」の関係性|5コアツールとは
「5コアツール」とは、IATF 16949(自動車)において、特に重要な5つの手法・方法論・ツールやマニュアルのことです。APQPもコアツールに含まれますが、他の4つのコアツールもまた品質マネジメントにおいて重要なツール・マニュアルであり、それぞれにAPQPと密接に関連しています。
単純に自動車メーカーだけではなく、そこに部品を納品するサプライヤーやOEM(他社ブランド製品を製造する企業・メーカー)それぞれが守るべき規格や規定がそろっています。
・APQP(Advanced Product Quality Planning:先行製品品質計画)
新製品(主に自動車)の開発プロジェクトを成功させるための計画策定と実行に関する手法です。製品企画から量産開始までの全プロセスを網羅し、顧客の要求を満たす製品を開発するためのロードマップとなります。
・PPAP(Production Part Approval Process:生産部品承認プロセス)
新車生産に使われる「部品」が設計要求どおりに製造されていることを確認するため、また部品の製造者が規格を満たしているという承認を得るために、必要な文書や評価のための方法論が規定されたものです。顧客への納入前に、部品の品質が承認されることを目的としています。
部品提供元(サプライヤー)が、納品先(顧客)である自動車メーカーからの品質要求などに応えるプロセスや具体的な方法がわかるようになっています。また提供元自身が部品製造のために材料などを調達することもありますが、その場合、製造する部品の品質を確保しなければなりません。これに対応し、必要な品質管理を維持するための方法論が含まれています。
サプライヤーは、納品先メーカーなどに対し、その部品の品質や要求事項に対する適合性について実証することが必要です。そのための具体的な証拠書類や保証書(PSW)の書式なども内容に含まれます。
・FMEA(Failure Mode and Effects Analysis:故障モード影響解析)
製品や製造プロセスにおける潜在的な故障モードを洗い出し、その影響度を評価し、対策を講じる手法です。設計段階であらかじめリスクを予測し、事前に取り除くことを目的としています。リスクの解析・評価が「故障モード」をもとに行われることから、この名称となっています。
【関連記事】
FMEA(故障モード影響解析)とは?実施手順や導入メリットを解説
・MSA(Measurement System Analysis:測定システム解析)
測定システムの精度や再現性を評価し、測定データの信頼性を確保するための手法です。正確な測定データに基づいた品質管理を行うために必要となります。具体的には、測定を行う機器や測定する担当者によって起こる誤差・偏りなどが起きていないか、評価する手法を規定しています。
測定データの誤差は、自動車の大事故を引き起こしかねないため、統計的調査の実施が必須事項としてIATF16949で定められています。
・SPC(Statistical Process Control:統計的工程管理)
製造工程で起こる品質の変動を、統計的手法を用いて管理し異常を早期に検出して対策を講じる手法です。安定した品質を維持するために欠かせません。
製造業では、製造の過程において同じ製品を同じラインで同じ人員が監視し、同じサプライヤーから部品提供などを受けていたとしても品質にぶれ(不均等や不良)が生じることは常にあり得ます。
品質にぶれがあると顧客からの信頼を失うことにつながりかねません。製品品質を常に一定の範囲の仕上がりにおさめる必要があり、これを管理統制するための手法としてSPCがあります。
【関連記事】
DRBFMとは?正しい進め方やFMEAとの違いを解説
APQPを導入する目的と実現すべき目標
APQPの根本的な目的は、概念的にいえば顧客のニーズを満たす「品質の高い製品」を開発初期段階から計画に落とし込んで作り、リスクを最小限に抑えること。そして、それらを量産して市場にスムーズに投入し顧客満足度を高めることです。
- 製品の品質向上と顧客満足度の向上
- リスクの低減
- コスト削減
- 開発期間の短縮
- 法規制への対応
APQPをもとに実現しなければならない目標としては「規格に合った適合品を・期日に間に合うように・発注どおりの数量で納入する」ことができる「品質保証体制」を作って製造を行い、「期日までに所定の書類などを完備させ提出」し、「ミッションを完了する」こととなります。
そのために自動車メーカー自身が規格を守った製品を作るだけでなく、部品提供を行うサプライヤーにもそれらを遵守してもらうのです。
近年、市場のニーズの入れ替わりはますます速度を上げていますが、品質に対する顧客の要求も非常に高まっています。その要求に応えるには、より効率的な生産プロセスを作り上げると同時に、製造段階の最初から品質の確保を意識した開発を行わなければなりません。
上記のうち「開発期間の短縮」のためには、それに対応する生産のための手法(コンカレントエンジニアリング)と体制(CFT:クロスファンクショナルチーム)の準備が必要です(後述)。
APQPの5つのフェーズ
APQPでは、目標達成のためにプロジェクトの各段階(=フェーズ)と設計・審査の時期や期間、活動内容を盛り込んだ計画を企画段階で作成します。この目標と計画を達成するために、5つのフェーズがあります。
【図】APQPの5つのフェーズ
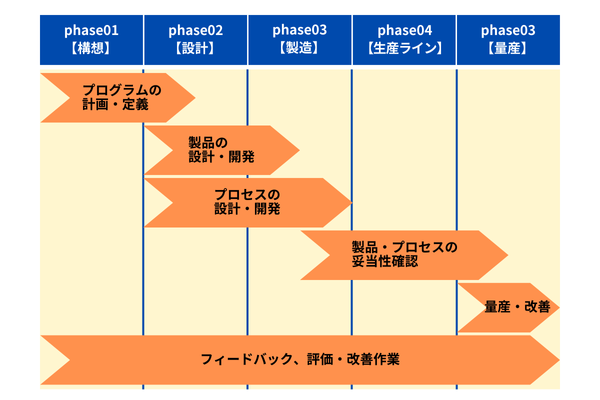
フェーズ1:プログラムの計画と定義(Plan and Define Program)
顧客の要求をもとに、製品の仕様や品質目標を定めるフェーズです。顧客の声や市場調査、事業計画などの情報を集め、プロジェクト(製品開発の全体計画)を策定します。
・フェーズ1で必要なアウトプット
「(APQPにもとづく)計画書」「特殊特性の計画」「部材表」ほか
フェーズ2:製品の設計と開発(Product Design and Development)
製品設計の詳細を決定し、試作による検証を行うフェーズです。設計FMEAなどのツールを用いて設計リスクを事前に評価し、対策を講じます。
・フェーズ2で必要なアウトプット
「設計図面」「設計FMEA(故障モード影響解析)」「試作CP(コントロールプラン)」ほか
フェーズ3:プロセスの設計と開発(Process Design and Development)
製品仕様に基づき、最も効率的で高品質な製造方法を検討するフェーズです。具体的な製造工程を設計し、工程フロー図やCPを作成します。同時にPFMEAを実施し、製造工程で起こりうる不具合を事前に予測し、リスク対策を検討します。
・フェーズ3で必要なアウトプット
「プロセス(工程)FMEA」「MSA計画書」「工程能力調査計画書」「量産試作CP」ほか
フェーズ4:製品と製造プロセスの検証(Product and Process Validation)
製品や工程の計画が実際に機能するか、妥当性を検証するフェーズです。量産試作を行って品質や生産性、量産が可能かどうかを評価します。PPAP、MSA、SPCなどの手法を用い、量産体制の準備を進めます。
・フェーズ4で必要なアウトプット
「MSAの結果」「工程能力調査の結果」「量産CP」「PPAP」ほか
フェーズ5:フィードバック、評価そして是正(Feedback, Assessment and Corrective Action)
新製品の量産を開始後、顧客の声や製造現場のデータからフィードバックを行い、製品の品質向上を図るフェーズです。製造プロセスを継続的に改善し、より良い製品を提供していきます。
・フェーズ5で必要なアウトプット
「製造工程の改善提案」「顧客の声をもとにした改善提案」ほか
APQPを進めるために必要なコンカレントエンジニアリングとCFTの導入
ここでは、APQPを進めるための体制に必要な、「コンカレントエンジニアリング」と「CFT(クロスファンクショナルチーム)」の導入について解説します。
APQPとコンカレントエンジニアリングの関係
前述したAPQPの5つのフェーズを表した図を見ると、それぞれのフェーズは切れ目なく連続しており、一つのフェーズが完了してから次のフェーズに移るのではないことにお気づきではないでしょうか。この手法は「コンカレントエンジニアリング」と呼ばれます。
【図】コンカレントエンジニアリング
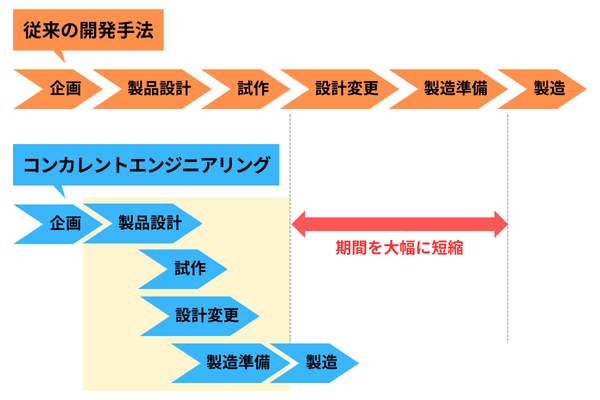
「APQPを導入する目的」の項目で紹介したとおり、APQPの目的には「製品の品質レベルを高く維持する」ことのほか、「製品の開発、製造、納品のサイクルを早くする」ことも含まれています。高い品質を維持しながら生産ペースも上げることで、顧客のニーズに合った製品を、タイミングを逃さずに提供するためです。
これは、前のフェーズが完了してから次のフェーズに移っていたのでは実現できません。そのため、ある程度同時並行的に進行することが求められます。現在は、システム開発などで広く使われる手法となっていますが、製造業を行う中小企業などではあまりなじみがないかもしれません。
APQPとCFTの関係
APQPを進めるための手法であるコンカレントエンジニアリングでは、各工程を担うチームやグループがそれぞれの情報を正確に共有、あるいはフィードバックしながら進めなければ同時並行的なフェーズ移行は難しい傾向です。そのため、これらの情報共有を行う担当者が間に入り、各工程の進捗の管理とその情報共有を担うことになります。
これを行う担当者だけを集めたチームをCFT(クロスファンクショナルチーム)と呼びます。CFTは、1980年代の日本企業の製造業が国際的にも高い技術と競争力をもっていた時代、アメリカがその理由を研究する中で理論化されたものです。
従来の日本企業では、コミュニケーションを密にとることで仕事上の情報共有を行い、チームや企業の士気を高め、生産力を上げていたという経緯があります。しかし現在の日本では、このやり方は失われていることも多くCFTを逆輸入する例も少なくありません。
例えば日産自動車では、ゴーン元CEOがCFTを導入して事業成績を上げたことでも知られています。CFTは、縦割りの部署構成では難しい「部門や部署ごとの横の連携」を可能にするものです。CFTチームに所属する担当者には、各工程の責任者であると同時に他の工程についても理解が深く、コミュニケーションを緊密にしてプロジェクトを進められる人材が必要になります。
このチームを結成することでコンカレントエンジニアリングが、ひいてはAPQPの手法がよりスムーズに実現します。
APQPを成功させるためのポイント
APQPは、自動車生産における品質管理のためのエッセンスですが、これは他分野にも活用できるものです。ここでは、APQPの主旨を理解して導入したとき、成功させるためのポイントをまとめました。
継続的かつ段階的に改善を行う
APQPの目的は、高品質な製品を不良品などの発生を極力抑えてリスクを減らし顧客へ迅速に届けることです。そのために、まずは製品やプロセスの改善を「段階的に」「繰り返し」行うことで上記の目的を実現することが可能になります。
例えば、顧客からのフィードバックをもとに製品仕様を改善したり、従業員の意見をくみ上げて製造工程の無駄を省いて効率化を図ったりといった具体的な取り組みが挙げられます。顧客だけでなく従業員からの意見も随時募集し、改善を進めることが大切です。これを実施しているものの一つが、トヨタ自動車の「創意くふう提案制度」といえます。
(参考)トヨタイムズ:仕事を楽しく、面白く! トヨタの創意くふう提案制度とは?
製品への要求を検証し顧客のニーズを把握する
品質の高い製品を生み出すには、顧客ニーズを正確に把握することが必要です。顧客の直接の声を集めることも大切になります。
例えばインタビューやアンケート調査を定期的かつ継続して実施する方法があります。近年は、オンラインの個別インタビューや複数の顧客を集めて意見交換会を開催することも可能です。具体的な要望や期待を抽出して製品設計に反映させることで、顧客満足度を高めることができるでしょう。
ITツールを活用する
人手不足や時間制限の中でAPQPを成功させるには、ITツールによる業務の効率化が有効です。さまざまなAPQP支援のためのITツールを活用することで、人的ミスを減らし、データ分析の精度向上や意思決定のスピードアップを実現できます。その結果、顧客満足度の向上やリソース(時間・コスト)の削減にもつながるでしょう。
ただし自社に合ったITツールを選び、導入するにも人材やコストなどのリソースが必要になります。導入してみたものの使いこなせなかったり、そもそも社内システムでは使えなかったりということもあり得ます。
ITツール導入については、アウトソーシングを活用することも一つの方法です。その際は、導入前だけでなく導入後のサービス範囲などについても確認しておくとよいでしょう。
まとめ
APQPは、製品の企画から量産までの全工程を品質確保の視点から体系的に管理するための手法です。顧客の要求を満たす高品質な製品を開発して市場に送り出すために不可欠なツールであり、国際規格ではAPQPがコアツールとして位置づけられ、自動車産業をはじめとする多くの業界で活用されています。
APQPを理解し導入、実施することで品質向上とその維持だけでなく、製品開発の効率化や不良品の削減、顧客満足度の向上などを実現できるでしょう。
【注目コンテンツ】
・DX・ESGの具体的な取り組みを紹介!専門家インタビュー
・DX人材は社内にあり!リコーに学ぶ技術者リスキリングの重要性
・サービタイゼーションによる付加価値の創造と競争力の強化