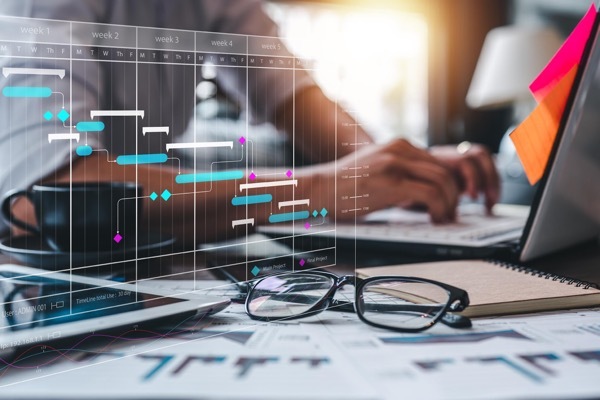
製造業において納期は、企業の競争力を左右する重要な要素です。納期が長ければ、顧客の満足度が低下し、競合他社にシェアを奪われる可能性も高まります。この納期を指すのが「リードタイム」です。リードタイムを短縮することは、顧客満足度の向上だけでなく、在庫削減や生産効率の向上など多くのメリットをもたらします。
しかしリードタイムを短縮するためには、生産工程の全体を見直し改善していくことが必要です。本記事では、製造業におけるリードタイムの意味や重要性、そしてリードタイムを短縮するための具体的な方法について、わかりやすく解説します。
リードタイムとは|意味と概要
はじめに、リードタイムの意味、計算方法など概要を解説します。
リードタイムとは
リードタイム(Lead time)とは、ある製品やサービスの発注から納品までの全期間、あるいは工程や作業の開始から終了までの所要時間を指す言葉です。製造業においては「手番(手配番数)」「先行日数」「基準日程」などとも呼ばれ、業務改善の重要な指標として活用されています。
リードタイムは、その対象となる範囲によってさまざまな種類に分類されます。例えば、製造業では製品の開発から納品までの全期間を「トータルリードタイム」、製造工程のみを対象とした期間を「生産(製造)リードタイム」などと呼び分けることがあります。
業界や業務内容によってその定義は異なりますが「リードタイムを短縮すること」は、顧客満足度の向上やコスト削減、生産性の向上など、企業全体の競争力強化につながることは共通しています。そのため、多くの企業がリードタイムの最適化を目標に、さまざまな改善活動を行っています。
リードタイムの計算方法
リードタイムの計算方法は、大きく分けて2つの方法があります。
(1)固定リードタイムの計算
各製品に対して、あらかじめ決まったリードタイムを設定し、納期から逆算して生産を開始するタイミングを算出する方法です。
<計算式>
予定開始日=納期-(リードタイム+安全リードタイム※)
メリットとしては、シンプルで計算が容易な点が挙げられます。一方デメリットとしては、製品ごとの生産状況や外部要因による遅延に対応しにくいことがあります。
※安全リードタイム:リードタイムに余裕をもたせるためのバッファとして設定される余分な時間のこと
(2)変動リードタイムの計算
製品の種類や数量によってリードタイムが変動することを考慮し、より詳細な計算を行う方法です。
<計算式>
予定開始日=納期-{(待ち時間+段取り時間+後処理時間+移動時間)+オーダーの所要量×1個あたりの実作業時間}
メリットとしては、実際の生産状況に合わせた柔軟な計画が可能になることが挙げられます。一方、計算が複雑になり、時間がかかることがデメリットです。
【関連記事】
タクトタイムとは?サイクルタイムやリードタイムとの関係性を解説
製造業におけるリードタイムの種類
製造業におけるリードタイムは、具体的にどのようなものがあるのか、その種類について解説します。
【図】リードタイムの種類
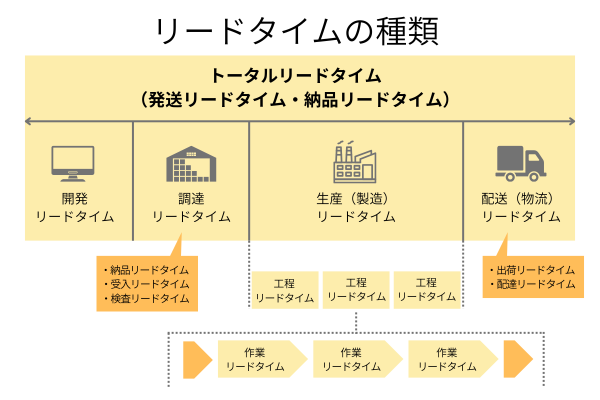
(1)開発リードタイム
開発リードタイムとは、製品の企画・設計から実際に開発に取り掛かるまでの期間を指します。新しい製品を世に出す際、アイデアを形にするまでにかかる時間と考えるとわかりやすいかもしれません。
この期間には、製品仕様の決定・試作による検証・設計図の制作・生産設備の準備・工程計画の策定などが含まれます。製品の種類や製造方法によって、この期間は大きく変わります。全く新しい商品を作る場合は長く、既存の商品をベースにマイナーチェンジ的に変える場合は短くなることが多い傾向です。
製造において、上流工程で計画遅延や長期化が発生すると製品ライフサイクル全体に影響を及ぼします。市場の変化に対応できなくなり、結果的に競争力を失うリスクが高まります。そのため、開発リードタイムの短縮は、企業にとって競争優位性を確保する重要な課題といえるでしょう。
(2)調達リードタイム
調達リードタイムとは、製品の製造に必要な原材料や部品が発注されたあと、製造現場に納品されるまでの期間を指します。具体的には、部品の選定や仕入れ先の決定から、納品、受入検査に至るプロセス全体にかかる期間を意味します。調達リードタイムは、さらに「納品リードタイム」「受入リードタイム」「検査リードタイム」に分けられます。
- 納品リードタイム:発注~納品まで
- 受入リードタイム:納品~受入検査まで
- 検査リードタイム:検査期間
調達リードタイムは、在庫管理においても重要な役割を果たします。仮に調達リードタイムが長かったり安定しなかったりする場合、製品の製造に必要な原材料を十分に確保するために多量の在庫を抱える必要が生じます。調達リードタイムが長い分、製造に取り掛かるまでの期間が長引くことは、機会損失につながるためです。
作りたいときに材料がなければ製造に取り掛かることはできません。そのため、あらかじめ原材料などの在庫をある程度抱えておくことが必要です。このように調達リードタイムは、結果的に在庫管理コストの上昇につながるだけでなく、製造時期が遅れた結果、製品の市場における需要や価値が低下して損失につながるおそれもあります(陳腐化リスク)。
なお、原材料ではなく「製造品(加工品)」を調達している場合は、さらにその製造品などの生産計画自体も把握し、計画に組み込んでおくことが必要です。仮にその製造品の製造リードタイムが長い場合は、その分発注したこちら側の調達リードタイムも長くなります。
このように調達リードタイムは、製造計画だけでなく在庫管理、さらにはサプライチェーン全体にも関わってくることを押さえておくことが必要です。
(3)生産(製造)リードタイム
生産リードタイム、または製造リードタイムとは、製品の製造を開始してから完成するまでの期間を指します。製品が製造ラインを通り、一つ一つの工程をクリアしてできあがるまでの工程と考えるとよいでしょう。
生産(製造)リードタイムは、製品の製造工程全体にかかる時間ですが、さらに各工程の「工程リードタイム」と、それを構成する作業ごとの「作業リードタイム」に分けることができます。生産リードタイムが長期化すると、次のような問題が生じるリスクがあります。
・仕掛かり品の在庫が増加する(仕掛品=製造途中の製品が増え、在庫管理の負担が増大する)
・納期遅延が起こる(顧客への納期が遅れ、顧客満足度が低下する可能性あり)
・コストの増加(在庫管理コストや人件費が増加し、製品のコストが高くなる可能性あり)
・市場の変化への柔軟な対応ができない(製品開発のスピードが遅くなり、市場の変化に対応できなくなる)
そこで、生産リードタイムを短縮するためには、以下のような対策が考えられます。
- 各工程の作業時間を均一化し、ボトルネックとなる工程を解消してバランス調整を行う
- 設備の故障を減らし、生産性を向上させる
- 人員不足を解消し、作業効率を上げるため配置を最適化させる
- 生産管理システムの導入を行い、生産計画の策定や進捗管理を効率化し、ムダを削減する
【関連記事】
MESとは?製造実行システムの機能をわかりやすく解説
製造業における生産管理とは?システム活用のメリットも紹介
(4)配送リードタイム(物流リードタイム)
配送リードタイム(物流リードタイム)とは、工場や倉庫から製品が出荷指示されてから顧客に向けて発送、配送されて納品されるまでの期間を指します。配送リードタイム(物流リードタイム)は、企業の物流システムや業務プロセスによってさらに細かく分解することが可能です。一般的には、以下の2つの要素に分けられます。
・出荷リードタイム
出荷指示が出されてから、製品が実際に倉庫から発送されるまでの期間です。この期間には、保管・運搬・仕分けやピッキング・検品・梱包などのマテハン作業が含まれます。
・配達リードタイム
製品が発送されてから顧客に届くまでの期間です。輸送手段や配送距離によって、この期間は大きく変動します。
配送リードタイム(物流リードタイム)は、顧客のもとに直接製品を届けることに直結しているため、その短縮は顧客満足度の向上に影響すると考えられます。
(5)トータルリードタイム(発注リードタイム・納品リードタイム)
トータルリードタイムとは、ある製品やサービスの発注から納品、あるいは顧客への提供が完了するまでの一連のプロセスにかかる全期間を指します。上記で説明した(1)~(4)のすべてを含むリードタイムです。
トータルリードタイムは、視点によって呼び名が異なることがあり、例えば顧客視点では顧客が商品を注文してから受け取るまでの期間を「納品リードタイム」や「顧客リードタイム」と呼ぶことがあります。企業視点では、同じ期間を「企業が商品を発注してから納品を受けるまでの期間」ととらえ「発注リードタイム」と呼ぶことがあります。
・製造業におけるリードタイム
製造業においては、トータルリードタイムと混同されやすい「製品リードタイム」「総合リードタイム」「累積リードタイム」といった用語も使用されます。これらの用語は、製品の受注から出荷までの期間を示し「(出荷後の)物流リードタイム」は含みません。そのため、厳密にはトータルリードタイムとは異なります。
【製造業】リードタイムを短縮するメリット
リードタイムを短縮することでどのようなメリットが得られるかについて解説します。
【メリット①】コスト削減が可能になる
リードタイムの短縮は、直接的・間接的にコスト削減につながります。
製品が早く出荷できるため、在庫を減らすことができ、保管費用や機会損失を減らすことが可能です。またボトルネックとなる工程の改善や、生産計画の最適化により、生産性が向上し、人件費やエネルギーコストを削減できます。さらに不良品発生率の低下にもつながります。
ただし、これらには各工程間の連携を密にし、情報を一元管理して品質管理を徹底するシステムづくりが必要です。
【メリット②】サービス向上による顧客満足度の向上がかなう
顧客への納期が短縮され、納期遅延による顧客からのクレームが減少します。また需要変動や顧客からの急な要求にも迅速かつ柔軟に対応でき、顧客満足度を高めることができます。
【メリット③】キャッシュフローの向上が期待できる
顧客への納期が短縮されることで売上を早期に計上でき、キャッシュフローが改善されます。在庫が早く回転するため、資金効率が向上します。
【メリット④】市場ニーズや緊急時への対応力の強化により企業競争力が上がる
市場ニーズの変化に迅速に対応でき、新製品を早期に市場に投入可能になるため、競合との差別化を図ることができます。その結果、競争力が高まることが期待できるでしょう。
またリードタイムの適切な管理は、緊急時の対応力も強化します。例えば、自然災害や部品供給の遅延など予期せぬ事態が発生した場合でも迅速に対応し、事業継続性を確保できます。
リードタイムの具体的な短縮方法
リードタイムを短縮することで多くのメリットが得られることは、前述のとおりです。ここでは
具体的にリードタイムを短縮するためにはどのような方法があるのかを解説します。
前提としてリードタイム短縮には、以下の4つの改善方針が必要です。
- 作業工程の棚卸し、ムダの洗い出しを行う
- 各工程の連携強化、情報の一元管理とシームレスな共有を可能にする環境整備とシステム化
- 各プロセスの最適化、それに必要な準備
- 従業員への継続的な教育と意識改革を行う
これらが実施されていることを前提に、各工程でのリードタイム短縮を目指すことになります。
開発リードタイムを短縮させる場合
開発リードタイムの短縮には「原材料や部品・製品仕様の共通化と標準化」「技術や知見の共有」「フロントローディング」といった多角的なアプローチが効果的です。部品や材料、仕様などを共通化することで設計や製造における無駄を削減し、効率を高める取り組みです。これにより、見積もりや手配といった作業の効率化だけでなく在庫管理の最適化にもつながります。
技術や知見の共有は、過去の成功事例や失敗事例を組織全体で共有し、新たな開発に活かす取り組みです。デジタルデータベースを活用することで、過去のトラブルを迅速に検索し、類似の問題発生時の対応をスムーズに行えます。
「フロントローディング」は、開発プロセスの初期段階から設計やシミュレーションなど、前倒し可能な作業を進める手法です。「コンカレントエンジニアリング」などが代表的な例となります。これにより設計段階での問題発見や修正が可能となり、後工程での手戻りを減らすことが可能です。
【関連記事】
フロントローディングとは? 基本概念とメリットを解説
製品開発を進化させるコンカレントエンジニアリングとは?
調達リードタイムを短縮させる場合
調達リードタイムを短縮し、サプライチェーン全体の効率化を図るためには「自社内の業務改善」と「サプライヤーとの連携強化」の両面からのアプローチが必要です。
自社内の業務改善
- BOM(部品表)のデジタル化(部品表を電子化することで手作業によるミスをなくし、情報共有を円滑にする。発注ミスや部品不足を防ぐ)
- 在庫管理システムの導入(実在庫とシステム上の在庫を一致させ、最適な発注タイミングを把握する。これにより過剰在庫や不足を防止)
- 調達業務の標準化(作業を標準化して手順書を作成し、作業のばらつきを減らすことで、効率化を図る)
- トータルな生産計画の作成と各部門、仕入先などとの連携強化(生産計画と調達計画を連携させることで、部品の不足や過剰発注を防ぐ)
サプライヤーとの連携強化
- 信頼できるサプライヤーの選定
- 複数サプライヤーの活用(単一サプライヤーへの依存度を下げることでリスクを分散し、供給の安定化を図る)
- 情報共有の強化(サプライヤーとの間で情報を共有し、連携強化で問題発生時の対応を迅速化)
- 安全在庫の確保(不測の事態に備えて一定量の安全在庫を保有しておく。ただし不良在庫になるリスクもあるため注意)
- 緊急時の対応マニュアルの作成(緊急事態が発生した場合の対応手順をあらかじめ定め、サプライヤーとも共有)
製造(生産)リードタイムを短縮させる場合
製造リードタイムを短縮するためには、各工程におけるムダの徹底的な排除が不可欠です。主なムダには、待ち時間の発生や不良品発生、不適切な作業レイアウトやライン構築による時間の発生などが挙げられます。これらのムダを特定し改善することで、生産効率を大幅に向上させることができます。
- 多能工化の推進(複数の工程をこなせる人材を育成することで人員配置の柔軟性を高められる。ただし人材教育や雇用の推進が必要になる)
- レイアウトの最適化(工程間の距離を短縮し無駄な移動を減らすことでリードタイムの短縮を図る)
- 最新機器の導入とDX推進(IoT、AI、RFIDなどの技術を活用することで生産データを可視化。問題点を迅速に特定し改善することが可能になる)
- 作業の標準化の徹底(作業の標準化とは、作業のばらつきを減らすこと。品質の安定化と生産性の向上を実現)
- 不良品発生原因の究明(不良品発生の原因を分析し、根本的な対策を講じることで品質向上と再加工による時間のロスを削減する)
配送リードタイム(物流リードタイム)を短縮させる場合
配送(物流)リードタイムに影響を与える要因としては、以下の点が挙げられます。これらを見直すことでリードタイムの短縮につながります。
- 物流システム(使用する物流システムやITシステムの効率性)
- 物流設備(フォークリフト、コンベヤシステムなどの設備の稼働率)
- 作業プロセス(ピッキング、梱包などの作業手順の効率性)
- 輸送手段(トラック、鉄道、航空など、使用する輸送手段)
- 配送距離(発送地と納品地の間の距離)
- 配送頻度(小口配送か大口配送か)
例えば、物流システムの自動化や配送ルートの最適化、在庫管理システムの導入などを行うことで、配送(物流)リードタイムの短縮につながる可能性が高まります。
ただし配送(物流)リードタイムの短縮は、必ずしもコスト低減につながるわけではないため、注意が必要です。仮に短納期を実現するために航空輸送を利用した場合、輸送コストが上昇する可能性は高いでしょう。配送(物流)リードタイムと物流にかかるコストは、トレードオフの関係にあることを理解しておく必要があります。
リードタイム短縮における注意点と対策
リードタイムを短縮することで、在庫削減によるコスト削減や顧客満足度向上など、多くのメリットが得られる一方、リードタイムを短縮することは品質の低下を招くリスクもはらんでいます。短納期化に伴う業務負荷の増加や新たな工程の導入によるトラブル発生などが考えられます。これらのリスクに対する対策について解説します。
1.在庫管理と需要予測の高度化をはかる
リードタイムが短縮されると、少ない在庫で生産を回せるようになり、資金効率が向上します。しかし需要が急激に増えたり、原材料の調達が困難になったりした場合、在庫不足で生産が滞り、顧客に迷惑をかける可能性があります。そのため、需要予測を正確に行い、最適な在庫量を維持することが重要です。AIを活用した高度な需要予測システムなども活用するとよいでしょう。
2.QCDバランスの維持を心がける
リードタイムを短縮するために無理な生産計画を立てたり、品質を犠牲にしたりすることは避けなければなりません。短納期化によって作業員の負荷が増加し、ミスが増えたり製品品質が低下したりする可能性があります。また、設備投資に見合うだけの効果が得られない場合もあります。
リードタイム短縮に取り組む際には「品質」「コスト」「納期(QCD)」のバランスを常に意識し、顧客のニーズをしっかりと把握することが重要です。
3.品質維持のための対策例
短納期化の達成は、あくまでも「手段」であり「目的」ではありません。品質を維持しながらリードタイムを短縮するためには、上記のような対策を継続的に実施し、企業に属する一人ひとりが意識をもって取り組むことが重要です。ほかにも以下が挙げられます。
- リアルタイムな品質モニタリング(製造データを継続的に収集・分析することで問題発生を早期に検知し、迅速な対策を講じる)
- フィードバックをルーチン化(品質データに基づいて工程改善につながるフィードバックを実施。特に新しい工程や技術導入時には、その影響を評価し必要な調整を行う)
- 従業員への継続的な教育(新しい生産方式への対応や品質意識の向上を目的とした教育・トレーニングを実施する)
- サプライヤーとの連携強化(品質基準を共有し、定期的なコミュニケーションを取ることで安定的な製品供給を実現できる可能性が高まる)
まとめ
この記事では、特に製造業におけるリードタイムについて、その意味と概要、短縮させることのメリットと注意点、各リードタイムの短縮方法を解説しました。リードタイムは、企業の競争力に直結する重要な要素です。リードタイムを短縮することで、顧客満足度の向上、在庫削減によるコスト削減、そして市場の変化への迅速な対応が可能になります。
リードタイムを短縮することは、あくまでも“手段”であり“目的”ではありません。品質を犠牲にしてリードタイムの短縮を進めることは、企業の信用失墜につながりかねません。競争力を高めるには、品質を維持しながらリードタイムを短縮することが重要です。
生産工程・在庫管理の改善やサプライチェーンの最適化、情報システムの活用、従業員の継続的なスキルアップなど、多角的な取り組みを行い、業務のデジタル化、DX化も活用していくことがこれからの製造業には求められるといえるでしょう。
【注目コンテンツ】
・DX・ESGの具体的な取り組みを紹介!専門家インタビュー
・DX人材は社内にあり!リコーに学ぶ技術者リスキリングの重要性
・サービタイゼーションによる付加価値の創造と競争力の強化