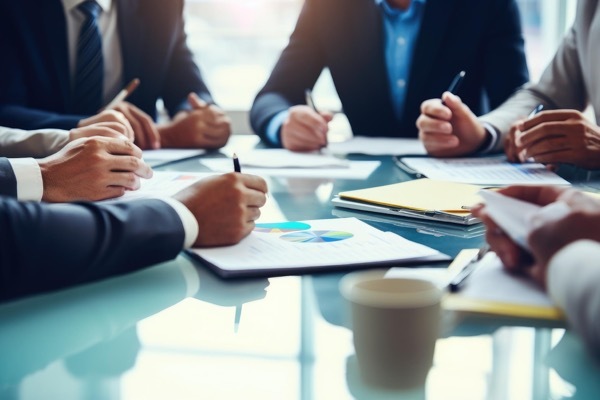
企業にとって成果を最大化することは、市場競争の激しい近年、ますます重要になっています。しかし従来のマネジメント手法では、組織全体の最適化が難しく課題解決に時間がかかってしまうケースも少なくありません。そこで注目されているのがTOC(Theory of Constraints)、「制約理論」と呼ばれるマネジメント理論です。
TOCは、システム全体の「制約条件」つまり最も弱い部分にフォーカスし、改善することで成果向上を実現する手法です。本記事では、TOCの概要や導入のメリット、具体的な導入ステップについて詳しく解説します。
TOCとは|組織における制約理論
はじめにTOCとは何か、その定義と考え方について解説します。
TOCの定義|組織における制約とは
TOC(Theory of Constraints)とは、日本語では「制約条件の理論」と訳されます。「制約」とは、ある組織やシステムにおけるボトルネック(業務プロセスやシステムのなかで全体の効率を最も制限している部分、つまり最も弱い部分、生産性や業務効率に深刻な影響を与える箇所)を指しています。
組織における制約とは、生産性や目標達成を妨げるあらゆる要因を指します。例えば人材不足や設備の老朽化、工程の複雑さ、顧客の難しい要求、属人化による生産性の低下、セキュリティシステムの脆弱性など多岐にわたります。
TOCでは、制約を単なる問題ではなく組織やシステム全体の性能を決定づける重要な要素として捉えることが特徴です。そのためSCM(サプライチェーンマネジメント)の理論基盤としても親和性が高いとされています。
TOC(制約理論)の基本的な考え方
TOCの核となる考え方は「全体の性能は、最も弱い部分(制約)によって決定される」ということです。これは「鎖全体の強さが最も弱い輪によって決まる」という考え方に似ています。この「鎖のアナロジー」は、TOCを用いる目的の例としてしばしば用いられます。
ここでいう個々の鎖の「輪」とは、例えば企業活動における個々の業務活動を表しています。つまり受注して原材料を調達し、開発、生産、販売、搬送、販売……など利益を生むまでの一連の流れと考えられるでしょう。また組織を構成する人や部門とも考えられますし、一つの成果を出すまでに関わるすべてのものと仕組みとも考えられます。ただしここで注意しなければならないことがあります。
一本の鎖をその仕組みやシステム、組織などと考えたとき鎖の強度の合計は何で決まるでしょうか。全体の強さが個々の鎖の強さを「加算」するものと考えるならば、鎖をつくる輪一つ一つを強くしたうえで「加算」すればよいことになります。しかし現実には、それぞれの部分を個別に強化しても、必ずしも全体として見たときにうまくいくわけではありません。
例えば、ある生産ラインにABCDの4つの工程があるとします。ABCDは、それぞれ1時間に100個、150個、50個、80個の作業を完了させられる場合、この生産ラインの能力をどのように判断するでしょうか。
TOCの考え方では、最も数の少ないCのラインがこのラインの能力および強度になります。なぜならCのラインが50個しか作れないなら、その前後で50個以上作れるとしても結局Cのライン段階でほかのラインは手待ちが発生してしまうことになるからです。つまりCがこの生産ラインのボトルネックということになります。
この例でわかるようにTOCでは、全体を「相互に依存し連携するもの」と考え、そのつながりがスムーズに動く仕組みが構築されていることを組織の強さと考えます。鎖の例でいえば、個々の鎖がそれぞれに強く、また重ければ加算すればその値は増えるのが一般的です。しかしそれをつなぐなかに弱い鎖があれば、そこで鎖は千切れてしまいます。
つまりその弱い鎖のある箇所が「ボトルネック」ということになるのです。TOCでは、一番弱い輪の強度を鎖「全体」の強度とみなし、ボトルネックの抱える問題を解決するため注力します。
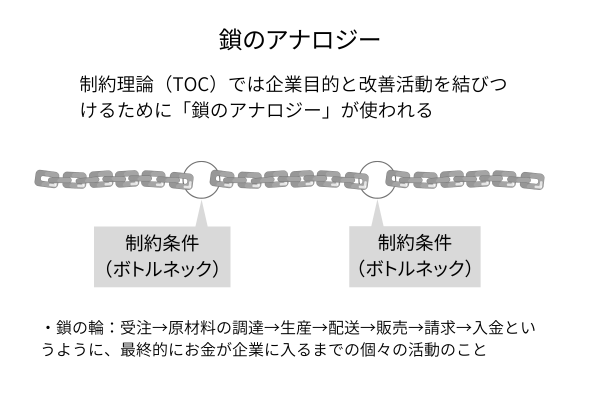
しかし、これを今度は現実の人間社会における組織とそれを構成する要素に当てはめて考えるとどのようになるでしょうか。ここでいう「要素」とは、人や設備、製造される成果物であり、サプライヤーやステークホルダーなどでもあります。単純にどれか一つが弱いからと鎖の輪のように簡単かつすぐに強くすることはできません。
またそこだけが強くても、ほかの鎖とのバランスが取れていなければ、結局そこが千切れてしまう=ボトルネックとなるでしょう。組織や社会におけるさまざまな要素は、それぞれに意味と価値があり、目的をもって構成され活動し、何かを為しています。目的を達成するために自分の役割を果たして機能するだけでなく、ほかの組織や組織の活動、成果に助けられているのです。
そうやってつながっていく大きな仕組みのなかで、企業の成果一つとっても達成されていることになります。TOCにおける制約を考えるとき、「全体を最適化し最大化するために制約を特定する必要があること」「全体とのバランスを見ながらボトルネックを強化しなければならないこと」を念頭に置かなければなりません。
TOCの歴史
TOCは、1970年代後半にイスラエルの物理学者エリヤフ・ゴールドラットがその著書『The Goal』のなかで提唱した考え方です。OPT(Optimized Production Technology)と呼ばれる生産管理ソフトウェア導入によって生産性が大幅改善した工場があり、ゴールドラットはそのソフトウェア普及のために著書(小説)を書いたとされます。小説はベストセラーとなりました。
当初、ゴールドラットは「単純にソフトウェアOPTを導入すれば生産性改善の源になる」と考えていたようです。しかし、ある読者が小説を読み「自分の工場で小説と同じように改善を行ってみると高い効果があった」と手紙で知らせてきたそうです。
このときゴールドラットは、ソフトウェアの導入が成果を出したのではなく「そのソフトウェアを導入した組織の背景や現状を理解したうえで導入しなければ効果は見込めない」ということに気づきます。そしてゴールドラットは、この理論をTOCと名づけました。
現在は生産管理や管理会計だけでなく、プロジェクト管理なども含むオペレーション・マネジメント(※)として注目を集めています。
日本においては、1990年代後半から理論の紹介が始まり、2000年代初頭から小説の邦訳が出版されて普及しました。
※オペレーション・マネジメント:企業全体の視点から、機能や部門を超えた業務のつながりや連携、流れを考慮して企業の業務プロセスを管理するマネジメント手法。戦略に基づいて経営資源を最大限活用し、目標達成を図ることを目的とするもの
「思考プロセス(TP:Thinking Process)」とTOCの発展
実際にTOCを導入して改善活動を進めていると企業や組織の方針が「制約」として問題になるほか、せっかくTOC導入で生産性が上がっても売り上げが逆に伸びないなどの問題が起こりました。組織などの複雑な対立に起因していることが多く、それを妥協せずに解決するために「思考プロセス(TP:Thinking Process)」と呼ばれる手法が開発されました。
思考プロセスの開発を機に、TOCはそれまでの製造業、生産に関する問題以外にも活用されるようになりました。
(参考資料)
「制約条件の理論(TOC)に基づく改善に対する一考察」八木英一郎,『東海大学紀要』政治経済学部 第44号(2012)
“The Thinking Processes (TP) and uncertainty” Eli Schragenheim
TOCと他の経営手法の違い
ここでは、他のマネジメント理論や生産方式とTOCを比較して見てみます。
TOC理論とトヨタ生産方式(TPS)の違い
TOC理論とトヨタ生産方式(TPS:Toyota Production System)、特にジャスト・イン・タイムのコンセプトは似ています。どちらも製造現場の効率化を目指す生産方式として導入されますが、そのアプローチや着眼点には違いがあります。
項目 | TOC理論 | トヨタ生産方式(TPS) |
---|---|---|
フォーカスするもの | ボトルネック | すべての工程の「ムダ」 |
目的 | ・システム全体の最適化 | ・高品質、低コスト、短納期 |
解決のための アプローチ方法 | ・制約の特定と解消、そのためのスループット会計や思考プロセスの実施 | ・「ニンベンのついた自働化」(生産性の向上) ・「ジャスト・イン・タイム」(生産工程の同期化、ムダの排除) |
考え方 | ボトルネックを特定して解消し、システムや組織全体のバランスをとったうえで強化する | 各工程の最適化を目指すことで全体を流れるようにつなげ、生産性を高める |
課題 | 全体最適およびボトルネックの強化を図るため、ボトルネックではない部分的な課題改善、部分最適化には向いていない | 「サプライヤーの犠牲の上に成り立つアプローチ」という指摘もある |
TOC理論は、システム全体のボトルネックとなる制約を特定し、その制約を解消することで全体の性能の最大化を目指すマネジメント理論です。前述のとおり組織やシステムは、最も弱い部分(制約)によってその能力が制限されると考えます。
そのためボトルネックとなる工程に集中し、その能力を向上させることで全体の生産性を向上させます(もちろん、全体とのバランスは考慮します)。根幹にあるのは、「システムは全体の『バランス』で成り立っており、その全体強度を上げることが重要」ということです。
一方、トヨタ生産方式(TPS)は、ムダを徹底的に排除し、ジャスト・イン・タイムの理念のもと不良品を作らずムダをなくし「必要なものを、必要な時に、必要なだけ」作ったり運んだりすることを実現するための手法で、高品質な製品を効率的に生産することを目指すものです。生産現場におけるすべてのムダ(ムリ、ムラ、ムダ)を徹底的に排除し、流れるような生産ラインを実現します。
最もフォーカスされるのは、すべての工程におけるムダの排除と人材育成です。また高品質、低コスト、短納期を実現し、顧客満足度を高めることが目標となります。「両方の手法のどちらがその組織に適しているか」は、状況によって異なります。
考え方の一例としてTOC理論は、複雑なシステムや問題(組織における対立なども含む)の継続的な改善に最適です。TPSは「長期的な視点ですべての工程を改善したい」「高品質な製品を安定的に供給したい」といった場合に適しています。
どちらも「弱点を見つけてそれを改善する」「全体の流れや連携を重視する」といったことは同じです。一方で、サプライチェーンマネジメントの観点からは「TPSは下請け業者などの犠牲の上に成り立っている」という意見もあります。TOCは、全体最適を目指すもののため、一時的な部分最適化には向いていません。
TOC理論とTPSは、どちらも製造現場の改善に役立つ考え方ですが、現在は製造業に限らずさまざまな業界や分野で応用、活用されています。アプローチや着眼点が異なるため、どちらを導入すべきか迷う場合は専門家へ相談してみるとよいでしょう。自社の状況に合わせて、どちらの考え方を取り入れるか、あるいは両方を組み合わせるかを検討することが大切です。
【関連記事】
7つのムダとは?トヨタの生産方式が指摘する「ムダ」と具体的な排除方法
TOCとその他の経営手法との違い|全体最適化と部分最適化
上記では、TPSをピックアップしました。しかし一般的には、TOCと他の経営手法やマネジメント理論を比較したときの大きな違いは、部分最適ではなくシステム全体の最適化を目指すことといえるでしょう。企業でいえば、各部門の目標達成ではなく組織全体の目標達成を優先します。またTOCは、一度の改善で終わるのではなく常に変化する状況に合わせて継続的に改善していくことを重視します。
TOCのメリット
TOCを企業や組織に導入する主なメリットは、以下の3つです。
短期間で大きな成果を上げられる
ボトルネックに集中することで、短期間で大きな改善効果が期待できます。
資源の効率的な活用
制約に合わせた資源配分を行うことで、資源の無駄遣いを防ぎます。
組織全体の活性化
全員が共通の目標に向かって取り組むことで、組織全体の活性化につながります。
TOCの5段階集中プロセス
TOCでは、以下の5つのステップを繰り返すことで、制約を特定し、改善していくプロセスを回します。
【ステップ1】制約を特定する
【ステップ2】制約を最大限に活用できる方針を決める
【ステップ3】制約以外を方針に従属させる
【ステップ4】制約を強化し全体機能を向上させる
【ステップ5】制約の解消を確認しここまでのプロセスを繰り返す
【ステップ1】制約を特定する
システムのなかで、全体の性能を最も制限している制約を特定します。
【ステップ2】制約を最大限に活用できる方針を決める
特定された制約を最大限に活用する方法を検討します。
【ステップ3】制約以外を方針に従属させる
制約以外の部分を制約が最大限に機能するように調整します。
【ステップ4】制約を強化し全体機能を向上させる
制約自体を強化するか、新しい制約を作り出すことで、システム全体の性能を向上させます。
【ステップ5】制約の解消を確認しここまでのプロセスを繰り返す
上記のステップを繰り返し、新たな制約が生まれるまで、改善を続けていきます。
TOCを活用した問題解決の具体的な実践に役立つ手法
TOCは、組織のボトルネックとなる制約を特定し、それを解消することで「全体的な性能を最大化する経営手法」と紹介しました。前述した5つのステップは、TOCの核心を捉えていますが、より詳細なステップと実践的な手法を加えることで、さらに効果的な問題解決が可能になります。
①問題の本質を見極め、制約条件を見つける
UDE(Undesirable Effect:望ましくない状況)の洗い出し
問題となっている状況を具体的な「望ましくない状況」に落とし込みます。例えば「納期遅延」や「売上減少」などです。
・因果関係の分析
UDEの原因を深掘りし、根本的な問題(制約)を特定します。因果関係を図示することで、複雑な問題も視覚的に捉えやすくなります。
・制約の特定
分析結果からシステム全体の性能を最も制限している制約を特定します。この制約が、問題解決の焦点となります。
②制約条件の解決策を検討する
・創造的な解決策の検討
制約を解消するためにさまざまなアイデアを出し合います。従来の考え方にとらわれず、大胆な発想も歓迎します。
・ボトルネックの強化・向上
制約となっている部分の能力を向上させる方法を検討します。例えば「人員を増やす」「設備を更新する」「プロセスを改善する」などです。
・他の要素の調整
制約以外の要素を制約が最大限に機能するように調整します。例えば生産スケジュールを調整したり、在庫レベルを最適化したりといった具合です。
③解決のための実行計画を立てる
・具体的な行動計画
検討した解決策に基づき具体的な行動計画を立てます。「誰が・いつ・何を・どのように行うのか」を明確にします。
・資源の配分
行動計画の実行に必要な資源(人材、資金、時間など)を配分します。
・目標の設定
目標を数値化し、進捗状況を測定できるようにします。
TOCを導入する際の注意点
TOCを導入する場合、問題となっているのは全体の最適化なのか、部分の最適かなのかを見極める必要があります。前述したように一部分だけもしくは一時的な改善にTOCは向いていません。TOCは、一度の改善で終わるものではなく常に変化する状況に合わせて改善を続けていくことが重要です。また全員が共通の目標に向かって取り組むことが大切です。
まとめ
本記事では、TOCについて理論の成り立ちや概要、実際に導入する場合のステップ、注意点について解説しました。TOCは、全体最適化を目指す企業や組織にとってボトルネックを見つけ問題を解決するための優れたフレームワークです。導入にあたっては、理論とその特性をよく理解し、自社の課題に合っているかを見極めて検討してください。
【注目コンテンツ】
・DX・ESGの具体的な取り組みを紹介!専門家インタビュー
・DX人材は社内にあり!リコーに学ぶ技術者リスキリングの重要性
・サービタイゼーションによる付加価値の創造と競争力の強化