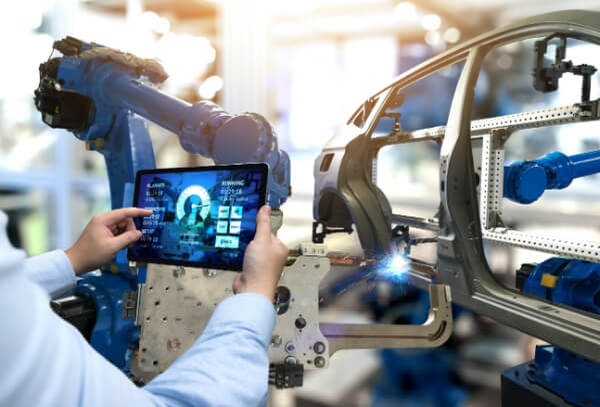
製造業におけるDX推進にあたり、BOP(Bill of Process)が注目されています。これは製造業における工程表に相当するもので、製造工程の管理方法をデジタル化していくことに、業界全体が重要性を認識してきていると考えられます。この記事ではBOPの意味や注目の背景、機能やケーススタディーについて紹介します。
BOPとは
BOPは、Bill of Processの略で、製品の組み立てや加工をするための部品ごとの手順を表したものです。製品を構成する部品を表にしたものをBOM(Bill of Materials)といいますが、BOPはこれに、工程名、工順、製造条件、作業時間、工程図などを統合した概念です。
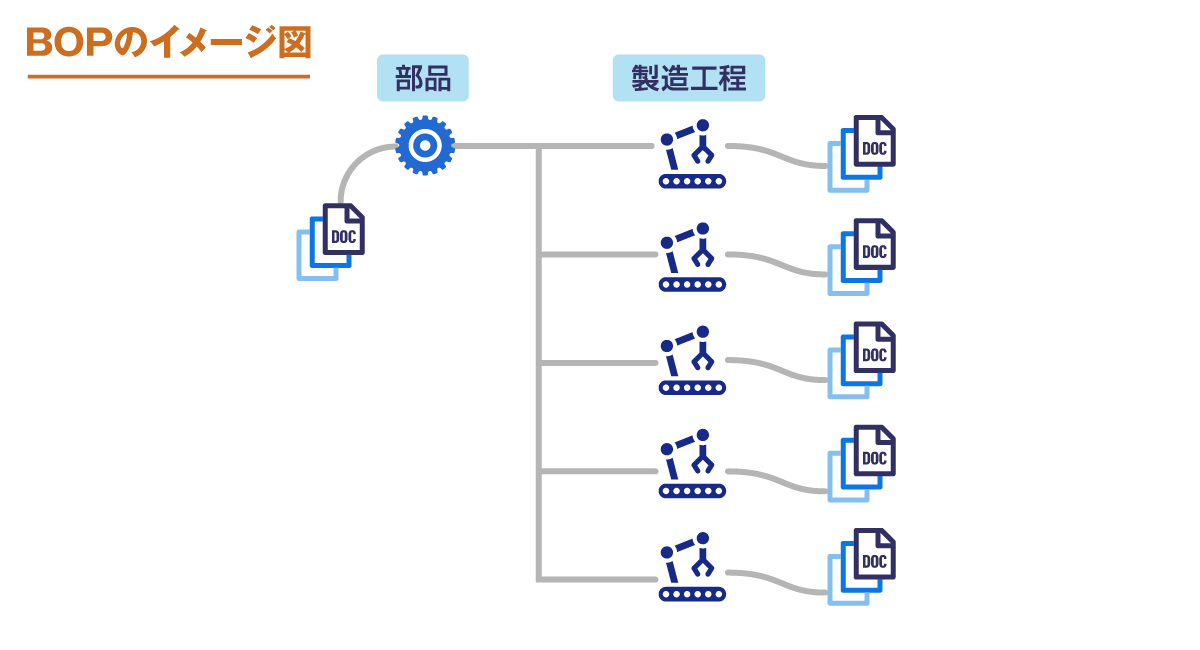
BOPは、製品を製造するための工程と、それを構成する情報を管理するための統合されたシステムです。製造のための管理システムには、図面などの技術情報を紐づけて管理するPLM (Product Lifecycle Management)がありますが、BOPはこれと連携して製品の生産にかかわる多くの情報を一元管理します。
その製品がどのような部品から構成されているかだけではなく、その製造方法や生産技術に関することまで統合管理できるため、設計から製造技術の開発工程が短縮されます。グローバル化した製造業では困難になりがちな生産技術情報の一元化を可能にするのです。
BOMには2種類があります。設計者の視点で記されたBOMと、中間品や在庫を踏まえ製造現場側で記されたBOMです。この2つのBOMにはそれぞれの立場の違いから連携がうまくいかないこともありました。
しかしBOPがあれば、設計と製造現場を仲介できるためスムーズな連携に寄与します。設計と製造をつなぐ役割もあるのです。
BOPの導入が進んでいる背景
自動車業界を筆頭とする製造業は1990年代以降、グローバルサプライチェーンを形成してきました。海外生産比率の高まりと同時に部品も海外から輸入が伸び続けています。これら海外の工場を管理するにはテクノロジーの力を借りる必要があります。
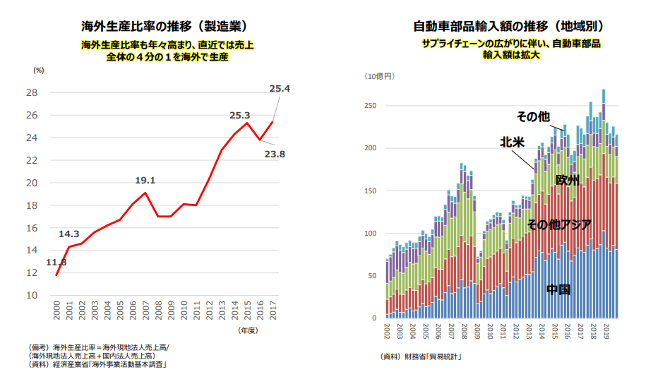
BOPの導入が進んでいる背景の1つにはこうしたテクノロジーの発達があります。製造業ではIoT機器の普及によって、設備の状況を示すデータを収集し、分析できるようになりました。これは、場所や規模に関係なく可能になることがポイントです。
つまり、世界各地に製造設備がたくさんあって長時間稼働していても、データは自動的に大量に集められ、それを分析できるようになったということです。ビッグデータの解析で設備のIoTセンサーから送信される信号を処理し、製品の品質を管理したり設備の故障を予知したりといったことが可能になったのです。
グローバルかつ大規模にデータが把握でき、データを検証できるようになったということは、計画通りに行っているのかどうかの基準が必要となります。その計画や基準を管理するのにBOPが整備されている状態が必要になってくるというわけです。

もう1つの背景は法規の改訂です。自動車のエアバッグに不具合が生じて安全に問題が生じたことは大きく報道されました。こうした事件に端を発して道路運送車両法が改正され、これまで自動車メーカーに対して出されていた改善勧告や報告の要求が、部品メーカーに対して直接出せるようになったのです。
最近の自動車は、製造や流通上の効率化を志向して部品の共通化を進めてきました。各自動車メーカーが横断的に同じ部品メーカーの製品を使っていた場合、ひとたび不具合が発生するとその規模はこれまでになく大きくなる可能性があります。
自動車部品メーカーは、このような「メガリコール」などとよばれる大規模な不具合があったときに説明責任を果たすため、管理体制を強化する必要が出てきました。その管理強化の方法が「トレーサビリティー(システム)」です。これは、不具合が起きた場合その部品が作られた時の状況を「追跡」してわかるようにするシステムのことです。
ある部品を構成する上位の部品のロット番号から構成部品のロット番号を調べられるようにして、その問題を発生させた工程や部材の調達先がわかるようになっています。同時にその時製造に携わった人、設備、部材、方法などが紐づけて記録されているので、より詳細に原因を探ることが可能です。
BOPのメリット
ここで、BOPのメリットについて考えられることを解説します。
製造業のスマート化に寄与する
DXによる生産性向上の1つに「スマートファクトリー」が挙げられます。経済産業省ではレベル3まであるロードマップを示していますが、そのレベル1に「データの収集・蓄積」があります。
▽スマートファクトリーロードマップ
このロードマップにBOPは出てきませんが、「データを利用することで生産ライン全体の設備の稼働・人の作業の進捗状況を収集把握できる」と定義されています。
これがまさにIoTによってデータを収集できるようになった工場の姿であり、この生産管理システムの最も基礎的なベースになるのがBOPです。BOPの構築は製造業のスマート化を代表するスマートファクトリー構築の第一歩となるものです。
コスト削減
従来、製造業における製造コストの削減は、設計段階に頼るところが大きいとされてきました。ところが自動車など多岐にわたる部品メーカーを見ると、1つ1つの部品を構成する点数は少なくなります。こうなってくると、全体の設計段階でコスト削減をするというよりは、それぞれの部品を「どこで」「どうやって作るか」ということになってきます。
BOPを用いて工程ごとの標準単価と標準時間を設定し、実際の結果と比較しながらPDCAを回していけば、各工程で改善が進み、コストがかかりすぎている場合は削減する試みを連続して行えます。
品質管理
生産拠点を海外へ移転するグローバル化が進むと、製品の品質を保証するのが難しくなるでしょう。そこで、部品や製品に個別番号をつけてトレーサビリティーを強化します。そしてIoT機器を用いて検査データや設備条件の情報を収集しておきます。
収集した情報はビッグデータとして分析をし、有意義な情報が発見できたら、製造部門や設計部門にフィードバックします。自動車業界のように共通の部品を多く使用する業界では、IoTで収集したデータを業界で共有することも考えられます。
情報共有
1つの製品を作るために多くの人が関わる場合、全員が情報を共有している必要があります。グローバル化した製造業では、図面などを翻訳する工程も必要です。さらに工程の中には業界の専門用語や言い回しがあり、これらをすべてExcelデータや紙に書き出して表現するのには限界がありました。
BOPのように部品表と設計から工程に必要な情報を紐づけたデータがあり、これを参照するようにすれば間違いはありませんし、業界の専門用語や言い回しをその国の言語で標準化しておけば効率的です。このようにBOPは、グローバル化した製造業の効率を上げるのに役立ちます。
ノウハウの活用基盤
モノづくりに携わる人は日々改善をおこないます。もっと安全な方法、もっと早い方法をもとめていつの間にか素晴らしいやり方が開発されているものです。このようなやり方は他の向上やほかの工程でも共有できたらすばらしいことです。BOPにその方法を記録しておけば、他の人たちにもこのことを伝えられます。
BOP構築の意義とポイント
BOPは「工程表」であり、製造上のあらゆる情報を統合管理するものです。BOPを構築することは、デジタルツインなどDX推進をするうえでも重要な取り組みです。
例えば、何を使って、どこで、どのように作業するのかあらかじめデータが保存してあれば、デジタルツインのような環境を作ったときにシミュレーションしやすくなります。BOPは、これまで現場ごとに散在していた生産にかかわる情報を一元化し、有効に活用できるようにするツールであるとも言えるでしょう。
BOPを構築する上でポイントとなるのは、設計部門から製造部門までを情報で接続させることです。
―設計の意図が正しく製造現場に伝わるようにする
―治具、設備、作業編成など製造現場のレイアウトや状況が次回に生かされる
―不具合の発生体験や記録が次の生産に生かされる
生産技術や製造が作業手順の検討を行う際に見る情報が紙などデータが書き出されている媒体だと、変更があったときに気が付かず、失敗や手戻りが発生するリスクがあります。設計部門からの情報をスムーズに流れに乗せて、一元化されたデータベースによって仕事ができるようにすることがポイントです。
BOPは全工程にかかる情報のデータベースですが、データベースを用いて得られる効果が成果物といえるでしょう。それは高度な情報共有による意思の統一であったり、不良率低下のためのPDCAが回り始めることであったりします。
こうした効果が、できるだけ多く生じるようにシステムを設計するのがBOP構築のポイントとなります。
BOPを使ったシステム導入の事例
ここからは、BOPの導入例を紹介します。
ブラザー工業
ブラザー工業は、アジアを中心にプリンターや複合機を生産しています。同社は設計データから連携された製造工程表を作成するシステムを導入し、効果を上げています。これは、BOPをBOMに紐づけて管理できるもので、生産活動が機動的になったといいます。
まず、システムは同社のベトナム工場に導入されました。工場の従業員に製造方法を伝えるにあたっては、製造用の帳票を翻訳することからはじめなくてはならず、うまく翻訳できたとしてもとらえ方が異なったり、誤解があったりでブレが生じることが多かったといいます。
書類によって製造情報を伝えようとすると、同じような情報を繰り返し伝えることがあったほか、書類と書類の間に必要な情報がないこともあり完全なものになりません。不明瞭な点が原因で失敗し、やり直しが発生すれば工程に遅れが生じます。これらに必要な事項を切れ目なく伝えるにはどうしたらいいかが課題でした。
そこで、BOPのシステムを導入します。課題となっていた翻訳と解釈のブレは、ねじを締める、グリスを塗るといった言い回しを標準化し、このシステムに取り込むことで解決していきました。製造に使う言葉を標準化し、BOPに乗せることで言葉の壁を越えたのです。これだけで、それまでの翻訳工程が従来の4分の1までに減少したといいます。
また、設計時には想定できない、製造上生じるリスクを数値化しBOPに乗せて、作業員がそれに対処できるようにしました。これによって故障の発生件数が10分の1にも減ったといいます。最も大きな効果には、本社と現地工場の意思疎通が活発になったことが挙げられるそうです。
マブチモーター
マブチモーターは、小型直流モーター市場では世界トップシェアを誇るメーカーです。現在は、すべての製品を海外で生産しており、その生産数は世界13拠点で年間12億個にも及びます。同社ではグローバル対応を強化するため基幹システムの刷新を計画しました。技術系ではPLMシステムの導入が計画されました。
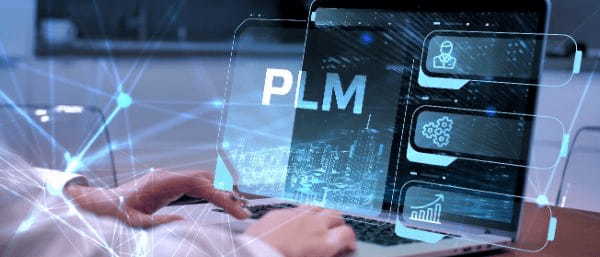
同社のモーターを構成する部品表・BOMやBOPは、複数のシステムに散らばって稼働していた状態で、それぞれの機能別に部分最適化されていました。この現象によって目的の情報はどのシステムのどこにあるのかすぐにわからず、探すのに時間がかかっていました。
ある部署で培った技術情報は、他部署でも同様に生かさなくてはなりません。こうした部分最適状態では技術情報の再利用は進まないばかりか、1つのメーカーとして技術的に「抜け」が生じることにもなりかねません。そこで、共通のシステムであるPLM上にすべてのBOP・BOMを集約しすべてを関連付けて管理することにしました。
この体制は、BOPを参照しやすくすることによって、自動車部品の調達基準である品質管理規格IATF16949の要求事項である「CP」(コントロールプラン)について推奨手法へ対応しやすくなるため、品質管理や顧客要求に対しても役立つこととなります。
BOPで製造業のDX実現へ
BOPは特段新しい技術ではなく、整理して考えれば一般的なデータベースです。工程とそれに付随するさまざまな情報が紐づいているので、構造的には小売業で使用する商品マスタと販売データの関係と同じです。
販売データトランザクションはありふれていてDXにはならないのかもしれませんが、製造業の工程をデータベースにするだけで、こんなにも革命的にものづくりが変わってしまうことには驚きがあります。
「ものづくり大国」といわれてきた日本ですが、DXに関しては遅れている部分も多いのが現状です。もともと現場力が高く、たいていのことを人の力で片づけられたがゆえに、DXが進まなかったとも言えます。
IoT機器の発達でこれまでできなかったいろいろなことができるようになりました。機械学習やAIが使われはじめ、データサイエンティストなど新しい役割を持つ人も現れました。BOPとはそのような最新の技術ではなく、「発想の転換」ともいえる“考え方をかえる”ことによって発生したシステムであるともいえるでしょう。
グローバル化した製造業にとって、情報を共有し不良を防ぎ、品質管理のPDCAを回して改善していくことのできるBOPは、必須のシステムになってくるでしょう。
【こんな記事も読まれています】
・国内製造業の再生を狙うINDUSTRIAL-Xが推進する[ESG×DX]時代の戦い方
・製造業における購買・調達業務とは?課題の解決方法も紹介
・サプライチェーン排出量はなぜ注目される?算定方法も含めて紹介