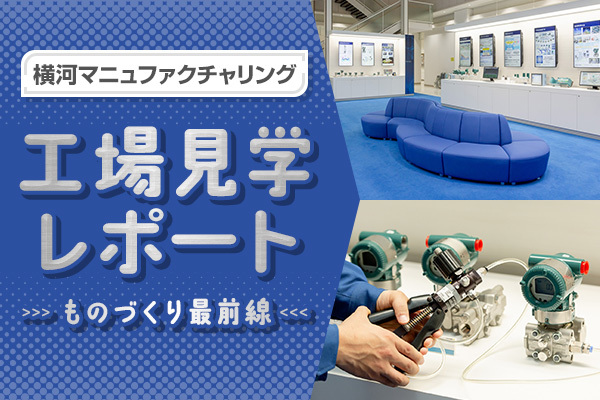
製造業の未来について発信するYouTubeチャンネル「AMANO SCOPE」とコラボレーションし、DXに取り組む製造業の姿を多角的にお伝えする本企画。今回ご紹介するのは、電気機器メーカーの横河マニュファクチャリング株式会社です。生産制御システムや差圧・圧力伝送器などを提供するYOKOGAWAグループにおいて、生産機能の中核を担う甲府事業所を訪ね、実際のものづくりの様子を見せていただきました。
電気や水道など、社会を支えるインフラの一部として求められる「高精度・高品質」な部品を、いかに低コストで素早く量産し、億単位に及ぶ製品ラインナップを、間違いなく正確に、不良品を出さずに組み立てるには、どのような仕組みがあるのでしょうか。
数多くの企業のDXや変革の歩みを知るAMANO SCOPEの天野眞也氏が、横河マニュファクチャリングの工場を訪れ、切り込みます。また、本記事ではAMANO SCOPEのYouTubeチャンネルの動画も紹介。映像カメラが入るのは初めてという横河マニュファクチャリングの工場内部の様子を映像でお届けします。
2015年 横河マニュファクチャリング株式会社 新卒入社
生産技術部へ配属
配属以来 主力製品である差圧・圧力伝送器のセンサに関わるコモンプロセスを担当
主に要素技術開発、生産設備の設計立上保守保全業務を担当
2009年 横河マニュファクチャリング株式会社 新卒入社
製造部へ配属 主力製品である差圧・圧力伝送器の組立に従事
2023年 NYPS推進部に異動
原価低減、経営に寄与するための改善活動に従事
株式会社FAプロダクツ 顧問
1992年、キーエンスに新卒入社。工場の自動化に関わるセンサやカメラの提案に従事し、グループ責任者、営業所長を経て社長直轄の海外営業・重点顧客プロジェクトの初代リーダーに抜擢。売上数百億円から二千億円の企業へと成長するまでの期間、営業として第一線でけん引する。キーエンスで築き上げた自動車・食品・半導体などのあらゆる業界の生産現場を見てきた経験と、顧客と共に海外を含む新工場プロジェクトを成功に導いてきた実績を基に、2010年に起業。
品質第一主義を具現化した「NYPS(ナイプス)」とは
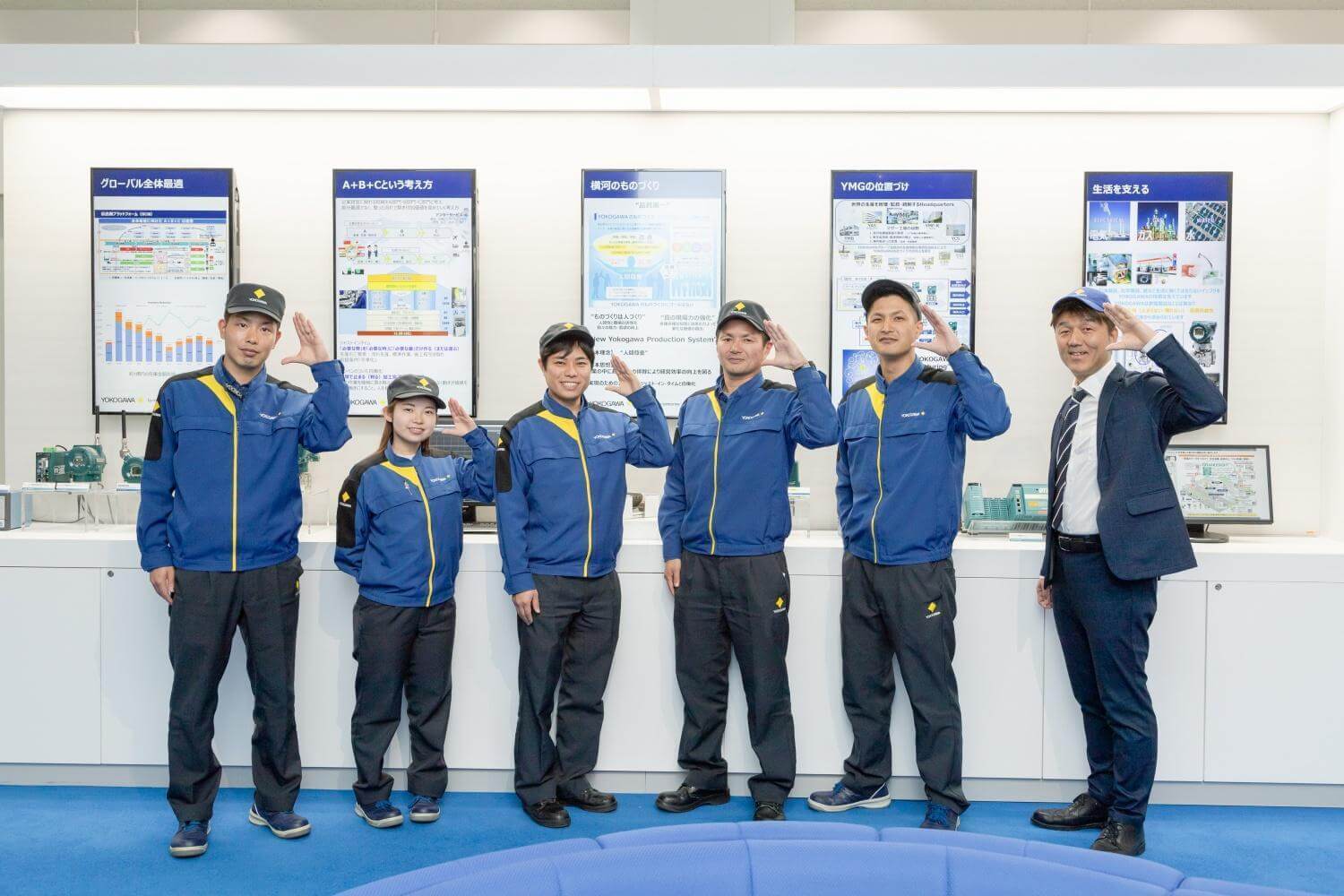
YOKOGAWAグループの国内主力工場の1つ、山梨県甲府市にある横河マニュファクチャリングの甲府事業所。工業用差圧・圧力伝送器や通信測定器などを製造し、ここから世界各地に供給しています。最初にYOKOGAWAグループ全体としてのものづくりに対する考え方、そして生産現場で無駄を排除する仕組みなどについて、現場を支える若手社員の皆さんに、ショールームでパネルに沿って説明していただきました。
天野氏(以下、敬称略) 本日はよろしくお願いします。さっそく、御社についてご説明をお願いできますか。
社員 よろしくお願いします。私たち横河マニュファクチャリングでは、皆さんが直接目にするような家電製品を生産しているのではなく、プラントや上下水道など、皆さんの日々の生活を支える社会インフラにて使用されている差圧・圧力伝送器や通信測定器などを生産しております。
これらの機器は工場やプラントの配管やタンクに取り付けられ、圧力や温度、流量を中枢システムに正しく伝達し、各種設備の安定稼働を実現するもので、もし何らかの理由により伝達が遮断されてしまうと、時として停電や断水、プラントのシャットダウンなど、社会活動に大きな影響を及ぼしてしまいます。そのため、私たちの製品は、過酷な環境下でも長期に渡って正常に稼働し続ける安定性と耐久性が求められています。
このように、生活に欠かせないものを生み出すプラントでは、生産設備、原材料、製品温度、圧力などが正常に動いているかなどの確認が必須条件となります。YOKOGAWAはプロセス制御の基本となる、温度、圧力、流量、レベルを測定する製品を製造・販売しています。
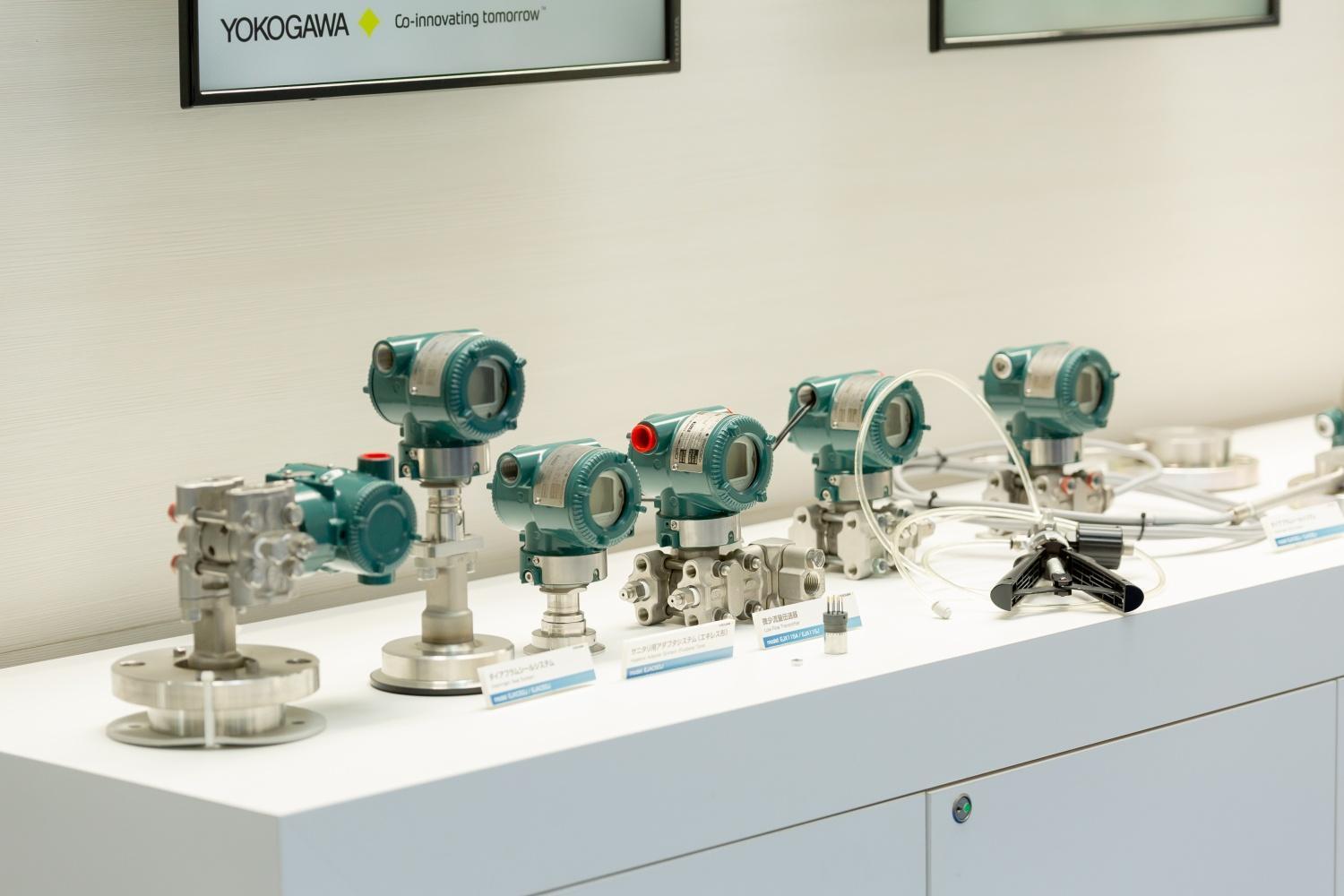
天野 YOKOGAWAグループさんといったらプラント、というイメージが非常に強いですよね。
社員 ありがとうございます。YOKOGAWAグループでは、「高品質な製品とソリューションを世界同一品質で提供する」というブランドイメージを掲げ、その根底には100年以上も守り続けてきた創業の精神の一つである「品質第一主義」があります。そして、横河マニュファクチャリングでは、この品質第一主義という精神を具現化するものづくりに取り組んでいます。
その1つが、「NYPS(ナイプス)」です。トヨタ生産方式(※)を源流とする、ものづくり企業による「NPS研究会」という組織があります。これは、トヨタ生産方式をいかなる業種にも応用できるものづくりの思想と捉え、1981年に新しい生産方式である「ニュー・プロダクション・システム」を確立することを目指して発足したものです。
YOKOGAWAグループもこの「NPS研究会」に会員として参加し、YOKOGAWAグループ特有の視点を加える意味で「Y」を入れた「NYPS」と呼ぶ新たな生産方式を確立しています。
「NYPS」の基本理念は人間尊重です。一人ひとりの限りある時間を1秒たりとも無駄にしない、付加価値を生まないものはさせない、しない。そして、作ったものが世のため人のためとなるように、人の価値を高めて生きた証が残るようにする。この人間尊重を基本理念として、品質、納期、価格を阻害する要因を全て無駄とみなし、組織・機能をつなげてあらゆる無駄を排除しながら付加価値を高めていく改善活動を「NYPS」の基本思想としています。
この思想にのっとり作り上げた、具体的な無駄を省いた製造工程を、後ほど実際の工場でご覧いただければと思います。
放電加工からドリル加工へ、圧倒的なコスト削減を実現
ショールームでの案内に続いて訪れたのが、液体や気体の圧力を測って出力する、圧力伝送器の加工をしている第5工場です。製造過程での工夫や自働化の取り組みについて、生産設備の設計を担当する、生産技術部の輿石大樹氏の案内のもと見学しました。
輿石氏(以下、敬称略) 最初に、弊社の主力製品である差圧・圧力伝送器の仕組みについてご説明したいと思います。差圧・圧力伝送器は、プラントの圧力を測定して電流信号やデジタル信号に変換し、その信号を上位の制御システムに伝送する機器です。
この差圧・圧力伝送器の測定の仕組みは、配管の途中に、オリフィスと呼ばれるドーナツ状の穴の開いた板を挟みます。左から流れてきた物質がオリフィスにせき止められ、真ん中の穴を通って右側に流れ出ていきます。物質がせき止められる影響でオリフィスの左右で配管内部の圧力に差が生まれます。この差を測ることで、配管内部の圧力を測る仕組みになっています。
配管は1種類だけではなく、多種多様な種類があります。あらゆる配管に接続できるように、弊社ではさまざまな仕様を用意して、お客様がよく使用する仕様は標準品として受注し、数の少ない仕様は特注品として製造しています。いろいろなねじの規格やフレキシブルなチューブを用意し、組み合わせは1億通り以上にもなっています。
天野 すごい数ですね。そして実際にこの差圧・圧力伝送器を手に持ってみると、やはり重たいですね。かなりしっかりした作りだなと感じます。
輿石 そうですね。この差圧・圧力伝送器の心臓部と言えるのが、圧力を測っているセンサです。このセンサは単結晶シリコンレゾナントセンサと言って、YOKOGAWAが世界で初めて自社開発に成功し、全て当社で製造しています。
シリコンウェハーの中に2つの振動子が入っており、この振動子を含むシリコンウェハーに圧力がかかると、振動子にひずみが生じます。そのひずみが生じることによって、2つの振動子が持つ固有の振動数が変化し、この振動数の変化を見ることで圧力を計測しています。
イメージとして、ギターのような弦楽器を想像してみてください。弦が強く張っている時は高音が響きますが、張りが弱い時は低音が響きますよね。これは、振動数の違いによって異なる音階になっているのですが、差圧・圧力伝送器のセンサも似たような仕組みで、個々の振動子の歪みの変化から圧力を測っています。
天野 僕はもともとセンサメーカー出身なので、なんだか懐かしい気持ちになりますね。今でも工場に行くと、まずセンサから見るのですが、やはりプラント用のものはがっちりしており、信頼感があるなと思って拝見していました。
輿石 ありがとうございます。第5工場のこちらのラインでは、差圧・圧力伝送器の中の受圧部に該当するカプセルBODYという部品を加工しています。この部品の特徴は、波になっている形状です。この波の部分には、ダイアフラムと呼ばれる金属の膜が溶接され、このダイアフラムも同じく波の形状になっています。
ダイアフラムは、配管などから伝わってくる圧力を早く・正確にセンサに伝えるための重要な部品です。この波の形状によって、非常に小さな変化も見逃さない、高い応答性を実現しています。
例えば、一本のまっすぐな銅線と波形状にした銅線、それぞれの先に同じ重さのおもりを引っかけると、波形状の銅線の方がよくしなって曲がります。同じ重さでより大きな変化量が得られるということは、それだけ重さの違いを正確に識別することができるといえます。
天野 なるほど、このようなばねの特性を持たせ、高精度な圧力検出を可能とするために、受圧部であるカプセルBODYもこうした波の形状をつけているのですね。
輿石 実際の加工ラインでは、高耐圧・高精度な計測を行うために高い加工精度が求められ、低コストで量産する必要があります。弊社では自働化を推進して経営効率向上を図っています。この加工ラインでは2つのポイントについて説明します。
その1つが「要素技術開発」です。カプセルBODYには細い穴が開いており、以前はこの穴を放電加工で開けていました。放電加工は、電極とワーク(被削材)の間で放電を繰り返してワークを加工する方法で、コストも時間もかかります。放電加工のまま自働化を進めても小さなメリットしか得られないため、短時間・低コストで加工できるドリル加工でこの穴が開けられるよう改善が必要でした。ドリル加工を実現するためには、細くて深いところまで加工しても折れないドリルが必要です。ドリルメーカーと協業して、ドリルメーカーの工程に入り込んで最適なドリルを開発し最適な加工ができるようになりました。その上で自働化を達成しました。
天野 放電加工をしていた時と比べ、どのぐらいのコスト削減、時間短縮が実現したのでしょうか。
輿石 ドリル加工にしたことで、放電加工をした時と比べて、1パーツあたりの加工コストを半分に、そして加工時間も27秒までに、大幅削減することができました。電力、工具費、放電加工液、洗浄排水、これらの大幅な削減につながり、この事例で平成26年度の省エネ大賞・審査委員会特別賞も受賞しています。
天野 そちらが1つ目のポイントである「要素技術開発」ですね。もう1つのポイントとはどのようなものですか。
輿石 2つ目のポイントが「自社開発設備」です。自働化設備についても自社で設計・組立・保守まで対応しています。オリジナルな工程での部品製造を必要としている為、自社で開発しています。設備開発は加工ラインに留まらず、製品の検査システムや組立装置なども自社で開発しています。
天野 大きな違いですね。精度の高い差圧・圧力伝送器を低コストかつ短時間で製造するための、細かな工夫がよくわかりました。
本記事では、工場見学の一部をご紹介しています。実際の横河マニュファクチャリングの工場見学の様子は、天野氏がナビゲートする以下の動画よりご覧ください。
YouTube動画を挿入
不良品を作ろうとしても作れない、「自工程完結」のライン
加工工程に続いて見学したのが、さまざまな部品から差圧・圧力伝送器を組み立てる第7工場です。NYPS推進部の須田和貴氏に、「NYPS」の考え方に沿って作り上げた不良品を出さない組み立てラインについて案内いただきました。
須田 こちらの第7工場では、差圧・圧力伝送器の組立から最終検査、梱包までの一連の流れを実施しています。第5工場などで加工された部品が、AGV(無人搬送車)で第7工場に入ってきます。そして長野県にある駒ヶ根工場から送られてきたセンサチップとともにクリーンルームでカプセルASSYとして組み立てていきます。その後カバーフランジを組み付け、各組立ラインに流していきます。
組立ラインはA、B、C、D、Eの5本あり、AやBは標準品のライン、Eに近づくにつれてより付加価値の高い複雑な製品のラインになっています。差圧・圧力伝送器は種類が多く、仕様の組み合わせは1億通り以上もあります。
天野 それだけの種類の製品を間違いなく組み立てるのは大変な作業ですよね。
須田 そうですね。人が確認するには限界があり、ヒューマンエラーを無くすため、間違ったものがラインに投入されないようにIDで照合し、製品情報を台車のIDに紐づけます。各ラインの工程には蓋の付いた部品置き場があり、台車のIDをトリガーに蓋が開き、その箱の中に取り付ける部品が入っているという仕組みです。
天野 正しいIDを読まないと蓋が開かないので、そもそも間違った部品を取り出すことができないようになっているんですね。
須田 そうなんです。他にも、例えば3回ネジを締めないといけない作業の場合、吊り下げてある電動ドライバーでトルクの管理を行っていて、3回トルクが掛からないと次の蓋が開かないようになっています。ライン内にある治具にもバーコードが付いていて、そのバーコードをヒットさせ、OKでないと次に進むことができません。不良を作ろうとしても作れない、そして誰にでもできるというコンセプトに基づき作り上げたラインです。弊社では「自工程完結」と呼んでおり、自分の工程で品質を保証し、後工程に不良を流さない仕組みになっています。
天野 まさに「組み立てDX」とも言える、素晴らしいラインですね。台車のIDと紐付けされ、トレーサビリティとしても使える組み立てた時のデータなども残っているのでしょうか。
須田 はい、データとして残っているので、何かお客様からの問い合わせがあったとしても、遡って確認することが可能です。現在のシステムができる以前は、お客様が求めている仕様と合っているかどうか、2者検査をしていたのですが、この仕組みを構築することで、仕組み上不良品が流れてくることがなくなったためそうした検査を廃止することもできました。
天野 検査というのは、不良品を見つけることはできたとしても、どこで間違えたのか、何が悪かったのか前工程に戻って確認することができないので、いわゆる改善活動にはなかなかつなげることができません。その観点で言うと、こちらのような自工程完結にした方が圧倒的に工数も減るし、データも残るし、良いこと尽くめではないでしょうか。この取り組みは横河マニュファクチャリングさんの技術とノウハウ、そして皆さんの血と汗と努力の結晶ですね。
本日は、世界に誇る高品質・高精度なものづくりの現場を、社員の皆さんにご案内いただきました。貴重なお話をありがとうございました。
【関連リンク】
横河マニュファクチャリング株式会社 https://www.yokogawa.com/jp-ymg/
AMANO SCOPE(YouTubeチャンネル) https://www.youtube.com/@AMANOSCOPE
【注目コンテンツ】
・DX・ESGの具体的な取り組みを紹介!専門家インタビュー
・DX人材は社内にあり!リコーに学ぶ技術者リスキリングの重要性
・サービタイゼーションによる付加価値の創造と競争力の強化