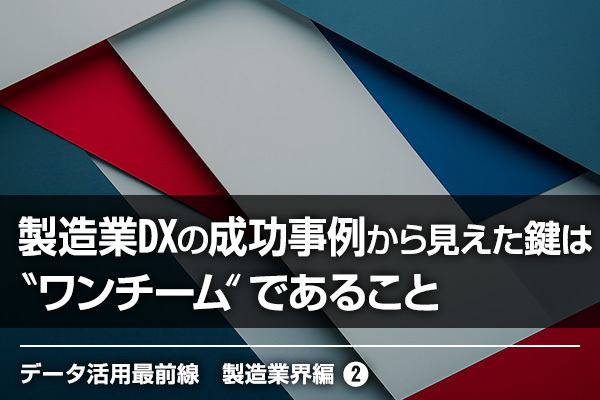
製造業全体でのDXが推進されない中、どのような企業が成功しているのか?数多くの製造業企業でDX推進を進めてきたウイングアーク1st株式会社の小林大悟 氏と株式会社コアコンセプト・テクノロジーの石原雅崇氏の2人による対談企画の後半では、DX推進を成功した企業事例にフォーカスをあて、そのポイントを探っていきます。
Data Empowerment事業部 ビジネスディベロップメント部
2018年、ウイングアーク1stに入社。現在 BIダッシュボード MotionBoardの製品企画・戦略立案に従事。また、2010年からIoTの推進に注力しており、ベンチャー企業でのIoTプラットフォームの事業企画や、大手ドイツ自動車部品メーカでのインダストリー4.0やコネクテッドカー向けシステムを手掛けた経験から、IoTデータの活用を中心としたエバンジェリスト活動も行っている。
DX事業本部 副本部長
東京大学工学部で原子炉材料研究のかたわら、Webシステム開発会社を起業。2015年、製造業関連で先進的なアプリケーション開発に取り組むCCTに入社。クラウド基盤構築、ビッグデータ基盤構築、機械学習アプリケーション開発、3Dレンダリング開発などを担当。2020年に、スマートファクトリーを中心とした製造業DX支援事業の責任者に就任。
目次
日報を紙からデータに変えた10年前。その一歩がスマートファクトリーにつながる
ーー製造業DXの現状の課題とその解決策についてお伺いしてきましたが、実際の事例についてもお聞き致します。まずはウイングアーク1stのお客様であるヤマハ株式会社様について、具体的にどのようにプロジェクトを進めたのでしょうか?
小林:ヤマハ様とのお付き合いは長く、当社のBIツールであるMotionBoardがリリースしたてのよちよち歩きだった10年以上前からご利用いただいております。
今日までに取り組まれたことは非常に多岐にわたりますが、初期段階ではレポーティングの効率化やリアルタイム化がポイントになったと思います。当時ヤマハ様の現場では、生産日報を紙で記録していました。その日報を現場リーダーが Excelへ 転記をして、月次レポートにしてマネジメントに報告するというサイクルでした。
このプロセスには問題点が大きく2つあります。ひとつ目は、データの転記や集計といったレポート化の工数が大きいこと。もうひとつは、工数がかかることなので短いサイクルで報告できないことです。
ーー作業のデータは取得できていたが、時間がかかり、改善も後手に回ってしまっていたということですね。
小林:一般的に月に一回の報告になりますと事後報告が多くなりますし、結果として改善や意思決定のスピードも遅くなります。
そこで取り組まれたことがタブレットを活用したPOP(Point Of Production=生産時点情報管理)です。生産時点でタブレットに実績を入力するシステムを導入したことで、入力されたデータがそのまま活用できるので転記の工数がなくなりました。そしてタブレットで入力されたデータはリアルタイムにMotionBoardで可視化できるようになりました。
入力した瞬間に可視化されるので、例えば出来高の目標と実績のギャップなどがタイムリーに把握でき、応援を呼ぶなどの改善施策が瞬時に判断できるようになりました。ヤマハ様の場合、日報の量も非常に多かったので工数削減のインパクトは非常に大きかったと聞いております。データの入力と出力の効率化がDX推進のスタート地点になっているかなと思います。
ーーデータ取得や可視化と聞くと、これまで定量化できない部分をイメージしますが、もっと現実的な作業の延長線上で実行されたことで成果を出されていたのですね。
小林:前半部分で世の中のDX事例は先進的なキーワードで溢れていると発言しました。投資対効果が出ないとDXの継続が難しくなりますが、極力、簡単かつ効果の出るテーマを初期フェーズで取り組まれると成果を実感しやすく、次のフェーズへ移行したり、他部署へ横展換しやすくなります。ヤマハ様も、当時から10年経った現在では、デジタルツインへとテーマが発展しています。ビジネス成果を着実に積み上げることで、 DXの継続的な推進に成功しています。
またデータ取得もさらに前に進んでいる印象です。ヤマハ様の工場は楽器製造という特性上、人による組み立て工程が多いです。例えば、サックスを組み立てるのに約2分半のタクトで、約30もの組立工程を経ています。
この際、各工程の作業時間を短縮したり、ラインバランスを改善するには、まず実際にかかった作業時間を測る必要がありますが、人からデータを取得するのには工夫が必要です。
ヤマハ様では作業者と製品の指示書にビーコンをつけて、作業者と製品の位置が重なっている時間をサイクルタイムとして測定しています。また、そのサイクルタイムが長くなったりバラついたときに、その作業の時刻で紐づけてすぐに表示できるようにしています。
そうすることで、作業が遅くなった理由、例えば治具の取り扱いに時間かかったのか、計器の読み取りに時間かかったのかがわかる。他には熟練の方と新人の方での作業の違いを分析して、エビデンスをもって改善に生かすようなことをされていらっしゃいます。
デジタルツインでは、ヤマハ様の中の標準の 製造モデルを定めることで、 RFIDやビーコンといった末端のセンサの違いによらず工場間の精算指標を比較したり、 仮想空間でのシミュレーションと現実空間の改善のループを回したり 、遠隔での生産管理を行ったり、そういった取り組みを進めていらっしゃいます 。
関連記事:スマートファクトリー化で生産性16%向上 デジタルツインで遠隔管理の実現を目指すヤマハ
ーーPOPによる成果があってこそ、データ取得からの改善を現場レベルでも実践されているんですね。MotionBoardの活用・実装部分ではウイングアーク様はどのように関われたのでしょうか?
小林:ヤマハ様のDX推進者の宮田さんは、私に言わせればスーパーマンに近いんです(笑)。ITに詳しいですし、IE(インダストリアルエンジニアリング=現場の改善科学)にも詳しくて、現場の落とし込みにも配慮をされている。
そのため弊社で手取り足取りの支援やサポートをしたことはなくて、ニーズを教えて いただいて、共同のPoCを通して製品改善をさせていただくようなやり取りが多いです 。
石原:ヤマハ様は現場の業務もITの理解も深い方が主体となっていて、ツールありきではなく業務ありきでしっかりと合うソリューションを選定されている。そのプロセスがあるからこそ効果が出る運用につながっていますよね。
当社のお客様では現場とITの双方の理解が深いご担当者がいらっしゃらないケースが多いので、コンサルティングから運用まで伴走支援させていただくことで価値を提供しております。その際にお客様側のご担当者を育成する視点を持ちながら、現場にも訪問して、業務に通用するツール、ソリューションを選ぶことを全員が意識しております。
ベストプラクティスとカスタマイズの併用が企業の強みを生み出す
ーー今後はどのような組織でもDXを進められることが重要になります。コアコンセプト・テクノロジー様ではどのようにツール、ソリューションの選定を進めているのでしょうか?
石原様:当社の考え方としては、まずお客様の業務の大部分は業界ベストプラクティスのツールに当てはめて標準機能を活用して構築します。例えば、ERPと呼ばれる基幹システムやデータ収集などの見える化の部分は、成功事例も多く手法はある程度確立されているので、ツール選定さえ適切であれば一定のDX推進が可能です。
その上で、各企業様の強み、差別化要素になる部分だけは、パッケージの実装では痒いところに手が届きません。最大限思い通りになるよう、カスタマイズないしはスクラッチ開発で実現するべきだと考えています。
当社のスクラッチ開発の例では、超高精度な外観検査自動化で無人の検査工程を実現したり、市販のスケジューラでは実現できない部分をスクラッチ開発して、リアルタイムかつ稼働率をほぼ100%に持っていけるように差立を最適化するなどがあります。
ーー汎用性の高い業務はベストプラクティスで実現し、企業の強みとなる部分はカスタムする二段階での実装は再現性が高そうです。では中小規模の製造業様の事例や、ヤマハ様とは異なるアプローチでの成功事例はありますか。
小林:中小規模の製造業様ではクラウドの活用がだいぶ普及してきたと感じています。一昔前までは製造業のお客様のほとんどがオンプレミスで、現在でもオンプレミスの導入が一定数あります。そんな中で クラウドの利便性が特に中小企業の皆様に関してはトレンドとしてあります。
コスト面でスモールスタートができますし、システムの保守運用もクラウドには必要ありません。IT部門が大きくなく、リソースも限られている企業規模のお客様からすると、クラウドはやはり楽です。さらに、工場とオフィスネットワークをつなぐネットワークが整備されておらず、オンプレでは工場から社内サーバへ つなげられないケースがあります。
そういった視点で、コスト面でも運用面でも以前と比較して中小企業のお客様も導入しやすくなっています。
当社のお客様では旭鉄工様や伊福精密様が、ITはもちろんIoTもうまく取り組んで、成果につなげています。
石原:旭鉄工様とか伊福精密様の規模感でDXがうまくいったのはどういう要因があったのでしょうか?
小林:旭鉄工様では、社長がIoT活用にかなり最初から取り組まれていらっしゃいました。ですので、トップの強い意思があり、そこに対する投資を惜しまなかった部分が大きいと感じています。同社には、もともと内製 で作られていたIoTの実績を収集するシステムがあるのですが、現在では子会社を設立して外販までされていますね。
ベンダーとクライアントの関係性を越えたワンチームの組成がDX成功の鍵
ーーやはり推進者の存在はDXの成否を分ける大きな要素となりそうです。一方、なかなか社内に人材がいないというのも現状かと思います。PM・IT人材の獲得についてはコアコンセプト・テクノロジー様は人材支援も行ってらっしゃいます。
石原:弊社ではIT人材調達支援を行っております。手を動かすITエンジニア人材もそうですし、場合によってはプロジェクトの推進役も含めて、弊社からご支援させていただいております。
小林:昔は自動化は人の仕事を奪う、という論調もありました が、最近は人が足りないから自動化しなくてはいけないと考える企業が多いですね。
石原:結局、ヒューマンリソースが足りなくなり、生産が追いつかなくなり、現場も経営も困っているのが実状です。人材不足は以前から指摘をされていた課題ですが、ようやく多くの方が危機感を持ってDXによる自動化、省人化を真剣に検討しているフェーズに移行したと感じています。
小林:現場のこともITも理解できる、業界のドメインナレッジを保有している人材は、本当に希少価値が高く、採用は現実的に難しい。コンサル、開発を含めて人材支援も可能なコアコンセプト・テクノロジー様の存在価値は大きいですよね。
石原:ありがとうございます。当社ではどちらもできる人材がおりますし、チームをうまく推進できるメンバーもおりますので、いろんなケースでお客様に足りてない部分をご提案できるかなと思います。例えば、スマートファクトリーに必要なシステム全体を構築するプロジェクトの顧客サイドのPMをお客様が確保できず、その役割を弊社から入れさせていただきました。組織上、お客様側にもプロジェクトのリーダーはいらっしゃって、その方に並走するPMO(プロジェクトマネジメントオフィス)という形でジョインさせていただきました。
今後、デジタル人材になるポテンシャルがある方をたてていただき、共同でチームを組む。一緒に開発・構築するなかで、当社がお客様側に入り込んでいく割合を段階的に減らしていく。弊社が構築して保守運用まで対応すると、お客様からしたら投資がいつまでも終わらないので、お客様側の体制構築、内製化をご支援させていただいております。
ーー支援を通じて社内人材の育成にもつながるのは、かなり理想的なモデルですよね。
小林:データ活用の成功には人や組織、文化などいろいろな壁を突破する必要があります。我々はIT企業ですが 、ツールを提供するだけではなく、それらの壁を一緒に乗り越えたいと考えているので、「ベンダーとクライアント」という立場ではなく、一緒に歩んでいきましょう、という形を実現したいですね。
石原:その通りですね。発注者と受注者みたいな関係だとうまくいかないケースが多いです。その関係性を越えて、同じ目標に向かっているワンチームが実現することが成功の鍵になると思います。
- DXではITと業務双方の理解が求められる
- 社内で適切な人材が不足している場合は、外部の支援をうまく活用しつつ自社の体制構築や内製化を実現する
- 発注者と受注者の関係を超えたワンチームの実現がDX成功の鍵
【注目コンテンツ】
・DX・ESGの具体的な取り組みを紹介!専門家インタビュー
・DX人材は社内にあり!リコーに学ぶ技術者リスキリングの重要性
・サービタイゼーションによる付加価値の創造と競争力の強化