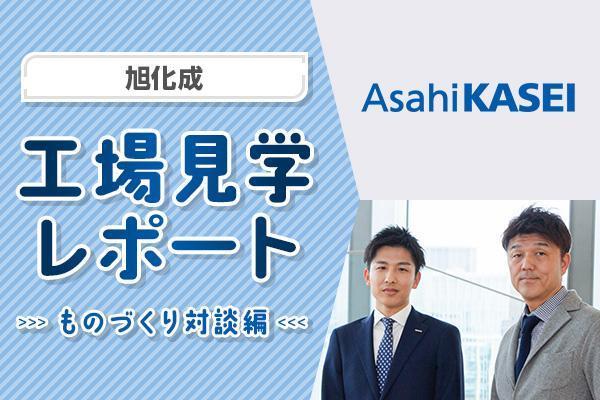
製造業の未来について発信していくYouTubeチャンネル「AMANO SCOPE」とコラボレーションし、DXに取り組む製造業の姿をより多角的にお伝えする本企画。今回は、多岐にわたるものづくりを展開する旭化成のデジタルツインについて紹介します。
今回対談を行った同社生産技術センター 産機システム技術部 エキスパートの松下雄史さんのお話からは、現場の若手が生産機能強化を図るうえで、デジタルと共に伝統的な手法も活用しながら、現場が感じていた課題を丁寧に洗い出していく過程が伺えます。最先端の技術をフル活用するうえで、どのような工夫があるのでしょうか。
本記事では、対談の様子をYouTubeチャンネルの動画でもお届けします。
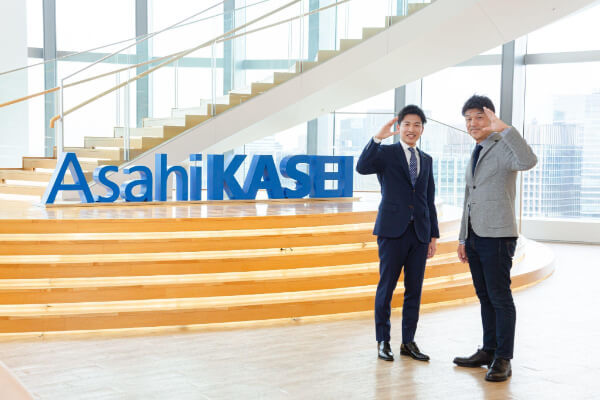
2013年、旭化成株式会社に入社。メディカル事業にて医療機器製造の設備開発に従事。検査工程の自動化、生産工程のシステム開発を担当。2018年から生産技術本部に異動し、旭化成グループにおける工場の自動化業務を推進。最新自動化技術開発と並行してデジタル活用を推進し社内のDXを牽引。2023年より計測・制御、機械システム技術領域のエキスパートに就任。
株式会社カクシン CRO
株式会社FAプロダクツ/株式会社さくらFuture Vision 顧問
1992年、キーエンスに新卒入社。工場の自動化に関わるセンサやカメラの提案に従事し、グループ責任者、営業所長を経て社長直轄の海外営業・重点顧客プロジェクトの初代リーダーに抜擢。売上数百億円から二千億円の企業へと成長するまでの期間、営業として第一線でけん引する。キーエンスで築き上げた自動車・食品・半導体などのあらゆる業界の生産現場を見てきた経験と、顧客と共に海外を含む新工場プロジェクトを成功に導いてきた実績を基に、2010年に起業。
目次
多種多様な事業に合わせた「最適な自動化」を追求する
天野氏(以下、敬称略) 御社については大半の読者の方がご存知だと思うのですが、まずは会社の概要を松下さんの自己紹介も兼ねてお願いします。
松下氏(以下、敬称略) 当社の創業は1922年で、現在4万8千人を超える従業員がグローバルで働いています。主に3つの領域があり、マテリアル、住宅、ヘルスケアの各領域で事業展開をしています。私が所属する生産技術本部では、新事業創出と既存事業を生産技術力で強化、推進していくというビジョンのもと業務を進めています。
天野 とても大事なところですね。
松下 そうですね。当社の生産技術本部の特徴的なところは、開発機能を持つ生産技術センターに加えて、建設、設備管理や企画、外販の機能すべてを持っている点です。
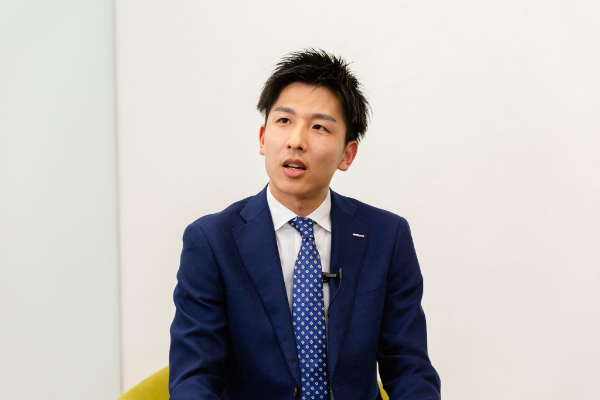
天野 なるほど。では、旭化成さんの生産技術領域の核は松下さんが担っていると言っても過言ではないですね
松下 私一人ではありませんが、そうしなければいけないと思っています。
天野 今回はデジタルが開く未来についてお話を伺いたいと思っています。松下さんの部署としては、DXをどのように位置付けているのでしょうか。
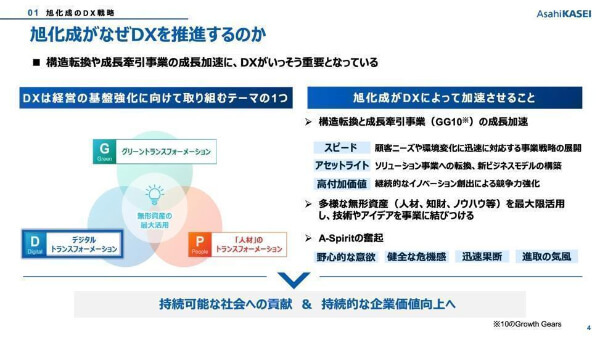
松下 DXの推進は、中期経営計画で目指す構造転換や成長事業を加速させる点において、経営基盤強化を図るうえで非常に重要なポイントの1つです。デジタルを活用して工場自動化へのソリューション力を強化し事業に貢献していくことが、会社全体の方針を我々の部署の中に落とし込んだ目標です。
当社の中で自動化対応している事業でも人工腎臓や半導体、それから、別会社なのではないかというくらいさまざまな事業が同じ会社の中にあります。天野さんはお気づきだと思うのですが、この場合の自動化の設備はそれぞれ全く違う形態になります。
天野 確かに。生産工程は全く違いますからね。
松下 そうですね。自動車製造業のように新しいモデルに新しい設備を用意するというふうにはいかず、本当にその事業にあった最適な自動化を提要する必要があるのですが、その中でも価値を上げるためにもっと効率的にデジタルを使っていくことが、弊部署(生技本)におけるデジタルの活用となります。
天野 御社が全社的にDXを強力に進めていくという方針を掲げているのは、さまざまな要素技術をたくさん持っていることが大きいのでしょうか。
松下 そうですね。そこに横串を指して、違う軸へ展開していこうとしています。
天野 なるほど。今回はたくさん事例をご用意いただいているとのことですので、DXの取り組みについてご教示いただければと思います。
人の動きをデジタルツインで可視化 肉体的、精神的負荷の定量的評価につなげる
天野 最初のDX推進のきっかけは、どういった点にあったのでしょうか。
松下 我々の仕事をもっと効率よくできないかという問題意識が、スタート地点にありました。特に今回の取り組みの特徴は、デジタル専門の者ではなくて普段は図面を描いていたり、現場で設備の立ち上げなどを頑張っているメンバーたちが、デジタルを使ってもっと自分たちの仕事を効率良くして発展させていく方法として、つまり普段の仕事をきっかけに進めていることです。
天野 なるほど。では事例をご紹介いただけますか。
松下 まず、オペレーター作業の負担の可視化の例を紹介します。工場の相談で多いのは、人の作業に関する部分です。例えば作業者への負荷については、どのような設備を構想すべきか把握するために、人の動きをデジタル空間上で再現する取り組みがあります。
作業する人の体の何ヵ所かにモーションキャプチャーを付け、デジタルツールと連動させます。こうすることで、今の動きのどの部分で腰や膝に負担がかかっているかといったことが分かります。これを指標にして、その際の姿勢などを定量的に評価することが可能です。また、作業者がどんな目線で見ているかも確認しながら、設備の高さや位置などを検討しています。
天野 今までももちろん、経験や勘である程度はやられていたと思いますが、定量的に見ることができると全然違いますね。
松下 具体的にどこが負担になっているのかが分かり、負担が軽減される前後の比較もできるなど、説得力があります。
天野 これは素晴らしいですね。では、今まで人にかかっていた負荷をデジタル化によってかなり軽減できているのでしょうか。
松下 そうですね。軽減をしている最中です。
天野 とても先駆的な取り組みですね。特に人間にかかる負荷は労災のリスクも含め、低ければ低いほどいいですからね。また、精神的な負荷も減りますよね。
松下 おっしゃる通りです。肉体的な負荷のほかにも、周りの環境、例えば匂いやマスクを着けるか否かなども影響します。また、作業の流れの中でもし失敗してしまった場合に全てを設備の上流からやり直す必要があるような、大きな緊張感を感じる作業であるのかどうかなどの精神的な負荷も含めて、全て点数化しています。当社独自の方法で数値化して、社内のいろいろな作業に適用しています。
天野 「この作業はすごくやりたくない、自分に回ってきたらどうしよう」というような精神的な負荷が原因で従業員が辞めがちなのは、多くの工場でみられることです。
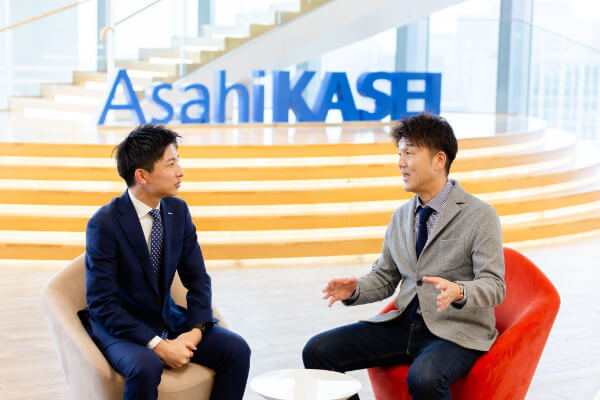
天野 では、人に負荷がかかる工程はどんどん減っていくということですね。
松下 そうですね。そして、人が本当にしたい、するべき仕事に集中することになります。
天野 すごいですね。他の事例はいかがでしょうか。
シミュレーションで加速する
松下 どのような自動化をすべきか構想する際にも、さまざまなやり方があります。こうしたらいいのではないかと考える際は、設備の構想段階から3DCADを使って、さらに動きを付けて確認することで、例えば素材の並べ方などについて、自分のアイデアがいいかどうかを検証できます。動かし方の順番やシーケンス、干渉などについて事前に分かるのです。
天野 図面の状態ではなかなか、干渉や動きの部分は分かりにくいのですよね。
松下 そうですね。熟練の方なら分かるかもしれませんが。
天野 熟練となるとだいたい15~20年くらいの経験がある人の世界ですから、相当なレベルです。でも、今ご紹介いただいた方法で設備の構想段階から検証することで、中堅や若手の方でもある程度「手戻り」が少なくなるような、構想・設計が可能だということですよね。
「シーケンス」については、読者の皆さんのために少し解説します。制御プログラムは基本的に、メカの設計が終わらないと作業に入れません。そうなると、構想があってメカ設計があって、制御設計に入るという順番になりますが、このシミュレーションがあることで、フロントローディング(※1)が可能になるということです。
制御担当の人がこのシミュレーションを見ると、メカがどのようになるのかが把握できるので、ある程度のフロントローディングができますね。全体構想設計の段階でメカ設計、制御設計がフロントローディングをバンとできると、非常に効率がいいということになります。すごい取り組みですね。
企画や製品設計など開発の初期段階で負荷をかけ、作業を前倒しで進めること。
松下 そうですね。現在最も活用しています。
天野 これによって、ミスなどはかなり減りましたか。
松下 はい。意外と凡ミスが多いということも分かり、シミュレーションの段階でどんどん減らしていくので、その後の工程が非常にスムーズに流れます。それから、イメージが伝わりやすいですね。自動化のイメージについて工場の方に絵で見せるとイメージしやすいらしく、「こうしたらもっといいのではないか」という、次の改善のアイデアが出てくるようなこともあります。この点は意外と、最も大きな効果かもしれません。
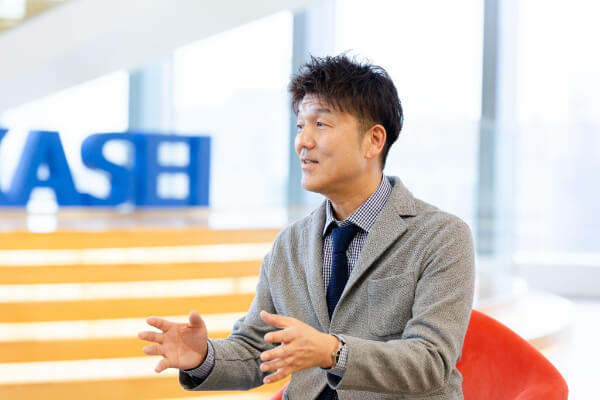
天野 でも、ある程度未来予想図を見せると「いや、ここはこうすべきだ」「ここの干渉を考えているのか」とか、「あの場所に柱があるがきちんと考慮しているのか」など、周りからいろんなアイデアがどんどん出てくるでしょうね。中には、設計者の方が気づいてない部分も含まれるでしょう。
「自分たちの目で見ること」が全ての基本
松下 このほかに、プログラムと機械の動きをソフト上で連携し確認していくいわば「仮想試運転」のような方法があります。実際にソフトを使って試運転をしながら連動してCADを動かし、ソフトのデバッグがないか機械が干渉していないかなど、機械を作る前に確認してしまいます。
天野 まさにバーチャルコミッショニング(仮想試運転 ※2)ですね。これをやることで、リスクを限りなく減らせますね。設計や制御の部分でミスが起きたとして、実際に機械が出来上がってから気づくととても大変です。場合によっては全部部品を外して設計し直して、部品加工業者さんに出して、また取り付けて動かす……といった事態になりかねません。この日数と費用でだいたい、2週間×何十万円ぐらいのコストがすぐ発生してしまいますからね。
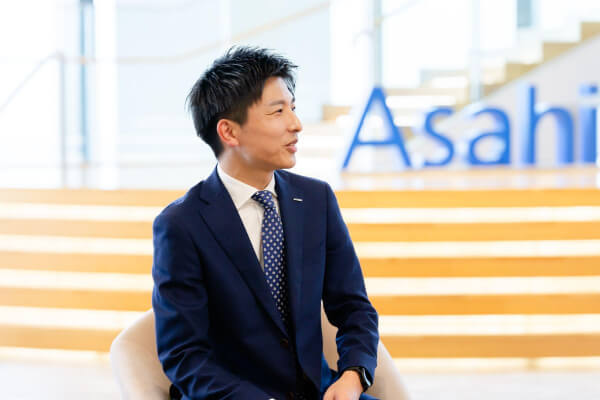
天野 御社では、リアルの装置ができる前に、CAD上で仕上げることのほうが多くなってきているのでしょうか。
松下 そうですね。とはいえ、まだこれからの課題でもあり、先行して進めながら横展開をしていかなければならないと考えています。
天野 皆さんが「これからやっていかなければいけない」という意思統一が、もうできているということですね。
松下 ベテランの方が、「これをやりたい」と言ってくれています。今までトラブルなどを経験してきた分、こういう思いが強いのではないかと思います。
天野 ライン全体のシミュレーションも、おそらく既にやっているのでは。
松下 はい。先ほどの例は設備単体でしたが、工場全体のシミュレーションも進めています。次の事例はフィルムの製造工程で梱包するところで、自動化とはいえ完全無人化は難しく、例えば設備に資材を供給する人が必要になりますので、その場合の人数をシミュレーションで確認しました。
シミュレーション前はExcelで頑張って計算しており、その段階では一人で大丈夫かなと思っていたのですが、実際にシミュレーションすると、人が移動する距離や時間、段取りなどが積み重なって、一人だと作業できないことが分かりました。そのうえで、レイアウトを見直して一人で十分回せるような工程に装置を作る前に調整することができました。
天野 つまり、Excelで弾き出したのは一人で、シミュレーションしたら二人必要だとなって、さらにシミュレーション上で改善してもう一度、一人に戻せたということですね。「超未来予測」をフル活用されています。設備の検証から工場レイアウトを含めた全体の検証になっているので、かなり手戻りは減らせますね。
松下 複数の設備が絡んできますので、特に重要だと思っています。
天野 複数の要素が絡むと、二次曲線的にパラメーターが増えてくるので、Excelではもう計算できない。アルゴリズムが必要になってきますね。
松下 はい。まず最初に各工場の作業現場を我々がきちんと見て、シミュレーションを作成することがとても大事だと思っています。きちんと現場を知って、その後も自動化のイメージを持っているメンバーが取り組むことで、デジタルと現実の間にあるギャップも分かりつつ作っていくことができます。
天野 どのようにして作業を実測していますか。
松下 ここは古典的で、カメラを設置してそこの時間をストップウオッチで測るなどのやり方です。
天野 シミュレーションの中のパラメーターの数値もできる限り正しく取ることで、未来予測をより正確にできますね。
松下 先ほどお伝えしたモーションキャプチャーを使えばより正確に把握できるのですが、自分たちがしっかり見にいくことが最も大事なところだと考えています。
製造現場から全社へ広がるDXの未来図を描いて
天野 さまざまなソフトを活用して、爆速で進んでいますね。ツールを選ぶうえで苦労した点や基準などはありますか。
松下 ここまで来るのにも実際、いろいろなソフトを試しまして、その中で我々に合ったソフトを選びました。自動化ではロボットをたくさん使いますので、ロボットに適用したロボットシミュレーターを使っているところです。当初は、どの業務の領域でも使える良いソフトウェアがないかなと思っていたのですが、まだありません。
むしろ、例えば文章を書くのにもWordやExcel、PowerPointと使い分けるように、我々の業務の中でもこの業務に適しているのはどのソフトかと分けた形で考えると、評価基準がクリアになっていきました。
天野 ツール選定そのものが、ノウハウですよね。差し支えなければ、よく使っているものをいくつか教えていただけますか。
松下 ほとんどがシーメンスやロボットメーカーのものですね。NVIDIAのOmniverse Isaac simなどそういったものを活用しています。
天野 これは参考になります。選定するうえでは、どの領域も数社比較されたのでしょうか。
松下 はい。どのソフトも2~3社は見て評価しました。
天野 このレベルに達しているのは、日本でもまだ稀有なのではないですか。チームで手分けしてソフトや領域ごとに検証を進めることで、社内のノウハウがどんどん溜まってきているのでしょう。
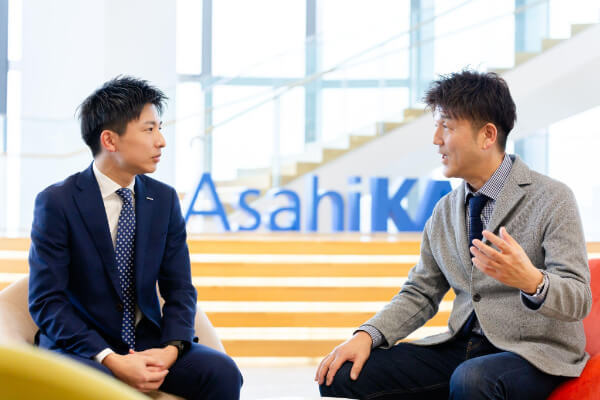
松下 そうですね。実際に使いながら分かってくることがありますね。
天野 松下さんの中で、デジタルが作る未来のものづくりは、どんなイメージでしょうか。
松下 今まで関わった業務がデジタルになると、いろいろなデータがつながっていくのではないかと考えています。現在の我々の取り組みは自動化の業務だけなのですが、まずは工場全体に広がり、それから営業やマーケティングにもつながっていき、仕事の全体が変わっていくのではないかと考えていますし、そうしたいなと。
天野 では、製造領域から販売領域へ、最終的には経営、基幹システムまで統合していくようなものをデジタル世界の中で実現していくということですね。御社はさまざまなデジタルの取り組みにチャレンジされていると思うのですが、松下さんご自身が、会社の取り組みを理解して、これからデジタルだぞ、となっていった経緯についてお聞かせいただけますか。
松下 次に何が来るのかとか、そのためには何を勉強したらいいのかなどについて、自分で考える時期がありました。自分でAIやIoTなどについて調べることから始めました。ほぼ同じ時期に、実際にそのような流れが起きて、自分がやりたいと考えていた提案が通りやすくなってきたのです。
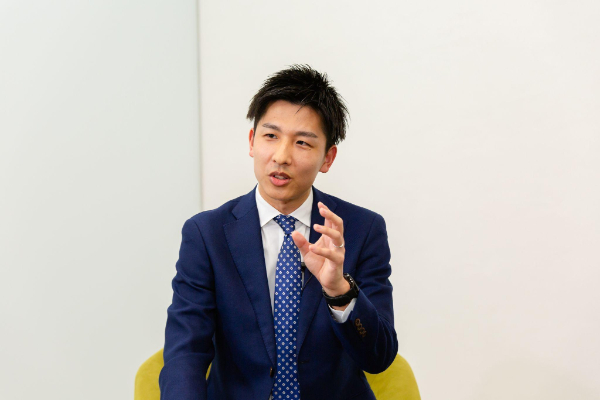
天野 会社側からは、デジタル化へ向かう働きかけのようなものはあったのでしょうか。
松下 たくさんありました。例えば「オープンバッジ制度」もその1つです。当社が掲げる「全従業員向けDX教育」として推進しているもので、スキルを見える化する制度です。
また、最近は、自分たちの取り組みを外部に発信して、皆で作っていこうという機運があります。それを受けて、内部の事情を外から知る機会も増えてきて、逆に会社がどういう方向に進みたいと考えているかが、今までよりも分かってきた面もありますね。
天野 なるほど。たいへん貴重なお話をありがとうございました。今後もご活躍ください。
旭化成の対談動画
https://www.youtube.com/c/AMANOSCOPE
【関連リンク】
旭化成株式会社 https://www.asahi-kasei.com/jp/
AMANO SCOPE(YouTubeチャンネル) https://www.youtube.com/@AMANOSCOPE
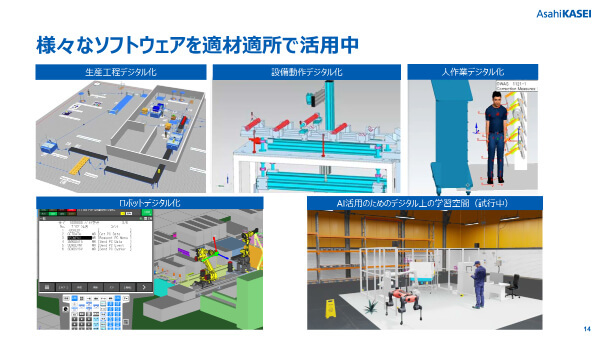
【注目コンテンツ】
・DX・ESGの具体的な取り組みを紹介!専門家インタビュー
・DX人材は社内にあり!リコーに学ぶ技術者リスキリングの重要性
・サービタイゼーションによる付加価値の創造と競争力の強化