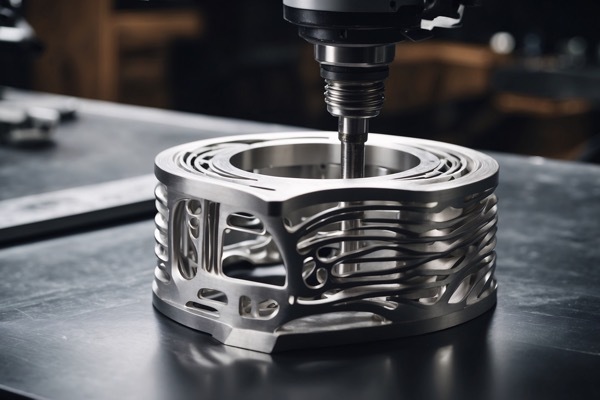
金属3Dプリンターは、革命的な製造技術として近年注目が高まっています。金属加工の技術は多岐に渡りますが、金属3Dプリンターを利用することで高い精度で複雑な形状に加工することができるため、製造現場の人手不足解消や生産性向上の手段としても導入が検討されるケースが増えているのです。
本記事では、金属3Dプリンターの概要や代表的な造形方法、導入のメリットとデメリット、活用事例などについて紹介します。
目次
金属3Dプリンターとは?
金属3Dプリンターとは文字通り、金属加工に特化した3Dプリンターを意味します。3Dプリンターは、CADなどの3次元データをベースとして、平面の2次元データを蓄積していくことによって立体的な造形を行う技術です。金属3Dプリンターで扱える材料としては、アルミニウム、ステンレス、チタンなどが挙げられます。
従来の金属加工は金属を削る、圧力を使って鍛造するといった手法が一般的でした。一方で、金属3Dプリンターでは設計ソフトで作成された平面データを積み重ねて造形していくことから、メッシュ構造などのより複雑な造形が可能です。
また、従来の手法よりも加工に時間がかからないことも特徴として挙げられます。金属3Dプリンターを活用することで、より細かなニーズに迅速に対応できるでしょう。
金属3Dプリンターの代表的な4つの造形方法
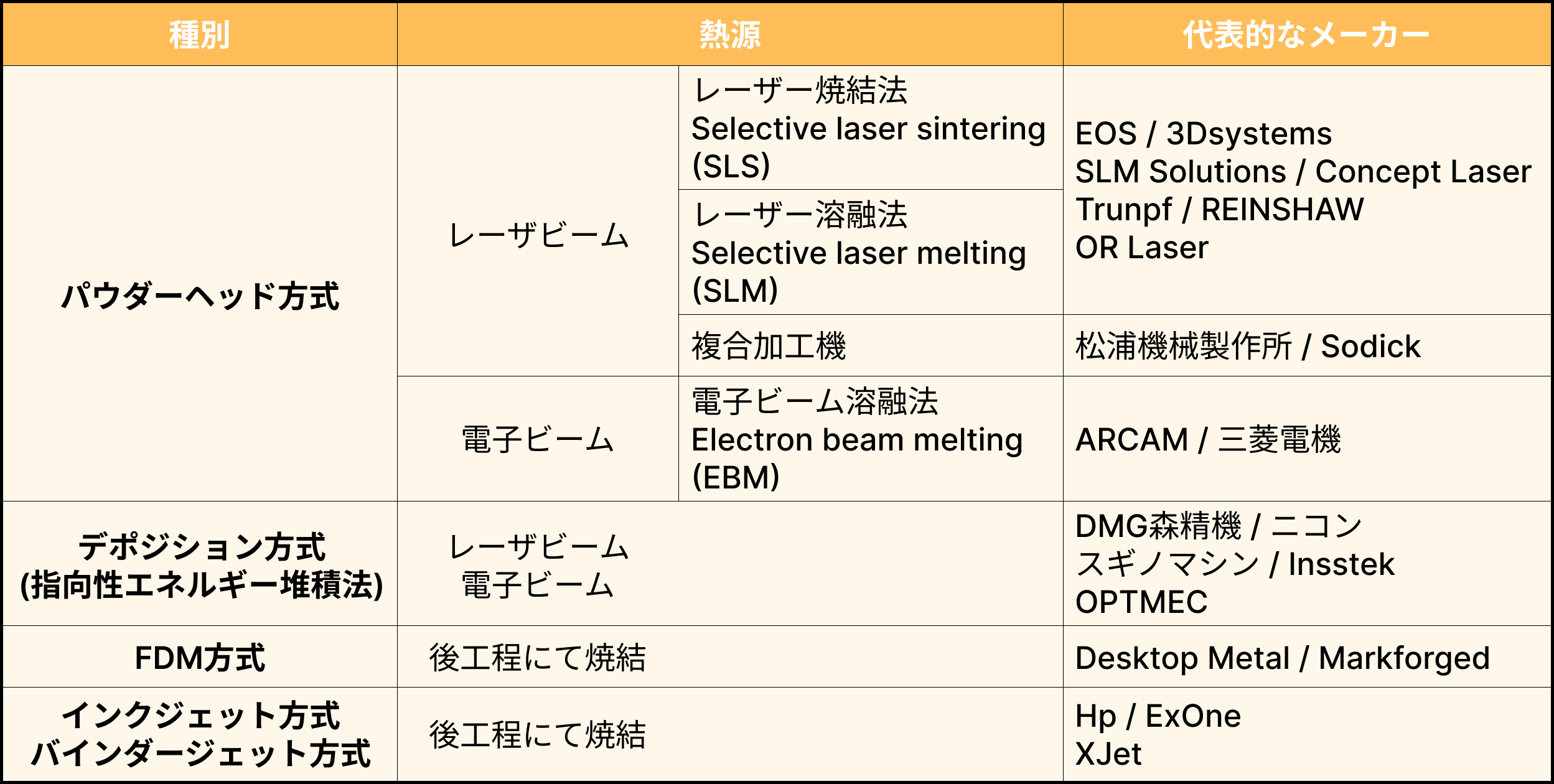
金属3Dプリンターには、いくつかの造形方法があり、それぞれの手法によって実現できる造形や導入コストなどに違いがあります。そのため、金属3Dプリンターの導入を考える際には、実現したい品質のレベルやかけられる予算を考慮して検討することが重要です。
ここでは、代表的な4つの造形方法について紹介しましょう。
1. パウダーベッド方式
金属3Dプリンターの中で主流とされているのが、パウダーヘッド方式です。パウダーヘッド方式は微細な金属の粉末を敷き詰め、レーザーや電子ビームの高熱で溶かして造形する方式を指します。
金属の粉末は溶解と凝固を繰り返すことで次第に造形されますが、完成時には凝固していない粉末を除去しなければならないことに注意が必要です。また、パウダーヘッド方式にはレーザー方式と電子ビーム方式の2種類があります。
レーザー方式
パウダーヘッド方式のうち、レーザーを使用してパウダーを溶かして所定の形状に凝固させるのがレーザー方式です。レーザーはレンズで一定方向に光を集めて電磁波を発生させるものであり、このレーザーの焦点が小さいほど造形の精度は高まります。
一方で、レーザーの焦点が小さいと完成までにかかる時間が長くなることに注意が必要です。またレーザーは光のため、材料によっては吸収や反射をしてしまいます。全ての材料に使えるわけではないことにも留意する必要があります。
電子ビーム方式
パウダーヘッド方式のうち、電子ビームを使うものが電子ビーム方式です。電子ビームとは電子を一定方向に集約したものであり、エネルギーの熱変換効率が高いことが特徴として挙げられます。
また、レーザー方式がレンズで方向を制御するのに対し、電子ビーム方式では電磁コイルで方向を制御します。そのため、より高速で造形することが可能です。ただし、レーザー方式と比べて造形の精度が若干劣る点には注意が必要です。
2. 指向性エネルギー堆積(デポジション)方式
指向性エネルギー堆積(デポジション)方式は、エネルギーを特定方向に集中させて、金属を造形させる方式です。具体的には、レーザーによる高熱で溶かした金属をノズルから噴射して造形していきます。この方式では、縦と横、奥行きを調整することで、より精密な造形が可能になることが大きな特徴です。
指向性エネルギー堆積方式には、金属を溶かすための方法によっていくつかの種類があります。レーザーを熱源とする方式がレーザー直接堆積法、圧縮加熱空気によって金属を噴射するのがMPA(Metal Powder Application)と呼ばれる方式です。MPAは特定の熱源を用いないことから、レーザー直接堆積法に比べて早い造形が可能になります。
3. 熱溶解積層(FDM)方式
熱溶解積層(FDM)方式は、熱で溶かしたフィラメントを層状に積み重ねて立体物を造形する方法です。FDM方式では、CADモデルから取得したデータをもとにして、加熱されたノズルからフィラメントを圧出し、指定された形状に積層することで造形します。ノズルから圧出されたフィラメントは、冷却されることで固まり、立体物として形成されます。造形の最終段階では、金属を結合するための樹脂を除去する脱脂という作業を行い、焼結炉の中で焼結させることが必要です。
FDM方式は、素材の種類や色を簡単に変更できることから、低コストかつ短い時間で試作品を作成するのに適していますが、一方で造形物の表面の粗さや部品の強度にはやや難があるといえるでしょう。
4. バインダージェット方式
バインダージェット方式は、粉末金属を使用して造形する方式です。この方式では、金属粉末を均一に敷き詰めたベッド上にバインダーと呼ばれる結合剤を噴射します。バインダージェット方式では、造形に使われなかった材料が造形物を支えるため、他の方式では必須となるサポート材が不要です。サポート材が不要になることで造形に対する制約が減り、複雑な形状に造形することも可能になります。
また、造形時に高温の熱源を必要としないこともバインダージェット方式の大きなメリットといえるでしょう。金属は高温に晒されることで劣化の原因となるため、金属劣化を避けたい場合にはバインダージェット方式が有力な選択肢になります。
一方で、最終工程では造形物の強度を確保するために焼結の作業が必要で、焼結時の収縮も考慮して設計しなければならないことに注意が必要です。
金属3Dプリンターのメリット
近年はさまざまな業界や分野で金属3Dプリンターが活用されています。ここでは、金属3Dプリンターを利用することで得られるメリットについて、代表的なものをいくつか紹介します。
広範囲の材料で金属部品を印刷できる
金属3Dプリンターの大きな特徴として、多様な素材で金属部品を造形できることが挙げられます。金属は種類によって、耐久性、耐熱性、熱同伝導性などさまざまな特性を備えています。
金属3Dプリンターの材料に広い選択肢があるということは、それだけ多様なニーズに沿った造形が可能だということです。実際に、金属3Dプリンターは製造業のほか医療など、幅広い分野で活用されています。
試作品や小ロット品を短納期で製造可能
金属3Dプリンターは方式による差はあるものの、基本的には短い時間での造形が可能であり、試作品やプロトタイプの作成に適した技術といえます。試作品が速いサイクルで提供できることにより、製品化に向けた検証や実験の段階において試行錯誤のスピードを上げ、商品開発のサイクルを速めることができるでしょう。
また、開発のスピードが高まることで競合他社に対する優位性の確保や顧客ニーズへの迅速な対応など、マーケティングの面でも効果が期待できます。
材料コストを削減できる
金属3Dプリンターは、従来の造形技術に比べて既存の設計データに基づいて造形されることから、必要とされる部品が少なくなります。さらに溶接などの工程も不要となるため、造形全体にかかる材料コストの低減が可能です。
また、間接的な効果ではありますが必要な材料が少なくなることで、材料の調達にかかる取引先との調整や納期確保といった業務の削減にもつながるでしょう。
金属3Dプリンターのデメリット
金属3Dプリンターには、造形のスピードアップやコスト削減といったメリットがある一方、注意すべき点もあります。ここでは、金属3Dプリンターの導入にあたって考慮すべきデメリットについて解説します。
造形に関する一定の知識が必要
金属3Dプリンターは既存の設計データに沿って金属を造形する技術であり、ゼロから造形物を設計することはできません。そのため、最終形となる造形のイメージや知識については利用者側で備えていることが前提となります。
数ある金属3Dプリンターの方式によって特徴は異なるほか、3Dデータを扱うCADや専用ソフトウェアの利用方法など、金属3Dプリンターの利用に求められる知識は多岐に渡ります。金属3Dプリンターの初心者がいきなり活用できるわけではないということを、理解しておきましょう。
初期費用やランニングコストが発生する
金属3Dプリンターの導入にあたっては、初期費用と導入後も継続的に発生するランニングコストの両面で費用対効果を検討することが重要です。初期費用についてはイメージしやすいものの、ランニングコストについては金属3Dプリンターの保守費用、サポート費用、材料費など中長期的には不透明な要素も含まれます。また、広義には金属3Dプリンターを使える人材の採用や育成コストも考慮する必要があるでしょう。
金属3Dプリンターの導入には、材料費の削減といった効果が期待できますが、ランニングコストについても把握した上での導入判断が必要です。
造形後に加工が必要になることも
金属3Dプリンターは方式によるものの、造形後の精度によっては別途加工が必要になるケースがあります。造形後の加工については、金属3Dプリンターが自動的に行うことができず、造形の知識を持った人の手で行わなければなりません。
造形後の加工について事前に考慮できていない場合、加工のための追加費用が発生するなど、金属3Dプリンターの導入効果が大きく損なわれる恐れがあります。
金属3Dプリンターが向いている製品
金属3Dプリンターには多彩な特徴がありますが、具体的にはどのような製品で金属3Dプリンターの技術が活用されているのでしょうか。ここでは、金属3Dプリンターの活用が適した製品について代表的な例を紹介します。
複雑な形状の製品
複雑な形状を持った製品は、金属3Dプリンターによる造形に向いているでしょう。従来の切削加工を前提とした方式で複雑な形状を実現するためには、加工技術によって精度が左右される上に切削できる範囲にも限界があります。
一方で、金属3Dプリンターでは材質を堆積させていくことから、複雑な形状にも柔軟に対応できます。また、チタン合金のような物理的な加工が難しい材料であっても造形が可能です。
少量多品種の製品
従来の方式では少しでも造形が変わると切削加工に使う機器の変更や調整が必要になりましたが、金属3Dプリンターは複雑な造形にも対応できることから、個別の顧客ニーズに対応することが可能です。
金属3Dプリンターを導入することで、従来は難しかった少量多品種の生産体制を大幅な設備投資を伴わずに実現できます。
熱溶解積層(FDM)方式で代用できる場合も
造形の目的や用途次第では金属3Dプリンターではなく、比較的広く普及しているFDM方式の3Dプリンターで代用できる場合があります。
具体例として挙げられるのが、熱溶解積層方式3Dプリンター「Creator4S」です。「Creator4S」の大きな特徴は水溶性のサポート材に対応していることです。水溶性のサポート材は時間の経過に伴い、水に溶けてなくなることから後工程で除去する手間を省略できます。
また、「Creator4S」は温度管理が可能であることから、湿度や温度に左右されずに安定的な造形を行うことが可能です。
金属3Dプリンターの活用事例
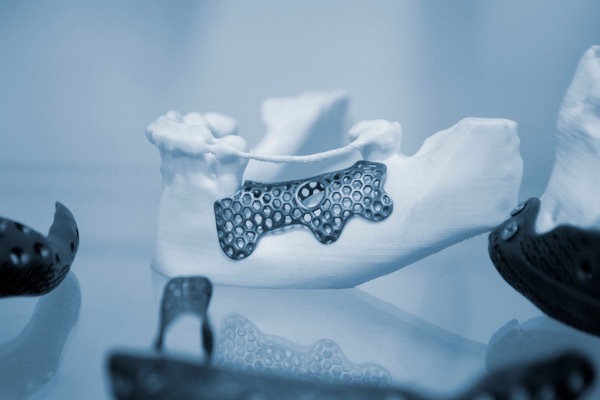
さまざまな特性を持つ金属3Dプリンターですが、実際にはどのような活用事例があるのでしょうか。ここでは、分野別に代表的な活用事例を紹介します。
医療分野での事例
金属3Dプリンターは、医療分野でも数々の活用事例があります。その代表的なものとして、歯科分野におけるカスタムメイドのインプラントや整形外科分野における人工関節が挙げられるでしょう。インプラントや人工関節は患者によって形状が異なる上に、肉体にフィットさせるために精緻な造形が求められることから金属3Dプリンターが積極的に活用されているのです。
医療分野における金属3Dプリンターの技術は飛躍的に向上しており、米国の3Dプリンターメーカーは歯科治療に必要な部品を大量生産する技術を確立しています。
航空宇宙分野での事例
旅客機やロケットを構成する部品の軽量化と耐久性向上が求められる航空宇宙分野でも、金属3Dプリンターの活用が進んでいます。米国の航空機エンジンメーカーは、燃料ノズルの造形に金属3Dプリンターを活用し、800個以上の構成部品を12個に減らし、大幅な軽量化と耐久性向上につなげています。
自動車分野での事例
自動車分野においても、金属3Dプリンターを活用した取り組みの事例があります。自動車メーカーのトヨタ自動車は国内のスタートアップ企業であるSUN METALONが開発した金属3Dプリンターをアルミニウム合金リサイクルのプロセスに導入しました。従来は金属の造形を目的に導入される金属3Dプリンターですが、金属リサイクルを目的に利用されるのは珍しい事例といえるでしょう。トヨタ自動車はこの取り組みによって、CO2削減を目指しています。
金属3Dプリンターを選ぶときのポイント
金属3Dプリンターを選定する際には、まず導入目的や用途を明確にすることが重要です。先述したように、金属3Dプリンターにはいくつかの造形方式があり、それぞれに特徴があります。使用する材質やサイズ、強度、形状といった仕様も、造形方式を選択する際の判断材料になるでしょう。
造形の方式や仕様が明確になった後は、金属3Dプリンターの機種選定に入ります。近年はさまざまなメーカーから製品が発表されているため、かけられる予算や費用対効果を加味して選定することが重要です。
金属3Dプリンターの活用の場は広いものの、導入には注意も必要
金属3Dプリンターは切削加工をはじめとした従来の造形方法に比べて、造形スピードの向上や材料コストの低減が期待できます。医療や航空宇宙、自動車といった幅広い分野で活用されており、今後も発展が予想されるでしょう。
一方で、金属3Dプリンターの活用には造形の知識やランニングコストの負担が求められることから、導入にあたっては費用対効果の分析をはじめ、さまざまな準備が必要となります。また、造形方式によっても一長一短があるため、目的に応じて必要な金属3Dプリンターを選定することが重要です。
本記事で紹介した金属3Dプリンターの選定ポイントなどを参考に、導入を検討してみてはいかがでしょうか。
【注目コンテンツ】
・DX・ESGの具体的な取り組みを紹介!専門家インタビュー
・DX人材は社内にあり!リコーに学ぶ技術者リスキリングの重要性
・サービタイゼーションによる付加価値の創造と競争力の強化