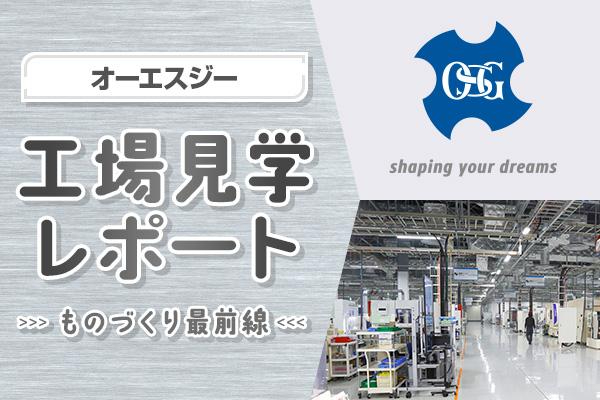
コアコンセプト・テクノロジー(CCT)CTOでKoto Online編集長の田口紀成氏が、工場見学を通じて製造業DXの最前線に迫る本シリーズ。オーエスジー株式会社のNEO新城工場(愛知県新城市)に伺い、同所の開設・運営に携わる第2製造部 部長の桝田典宏氏にご案内いただきました。
オーエスジーは、世界32ヵ国に製造・販売拠点を展開する、総合切削工具メーカーです。金属加工において、穴の内側にねじを刻むタップを柱に、エンドミル、ドリル、転造工具などを手掛け、創業製品のタップは世界トップシェアを誇ります。
NEO新城工場は、2020年5月に誕生した新たな生産拠点で、現場のノウハウとデジタル技術を融合し、さらなる効率化を実現しているのが特徴です。ここでは、桝田氏に工場のコンセプトやDX推進における取り組みなどについて、お聞きしています。
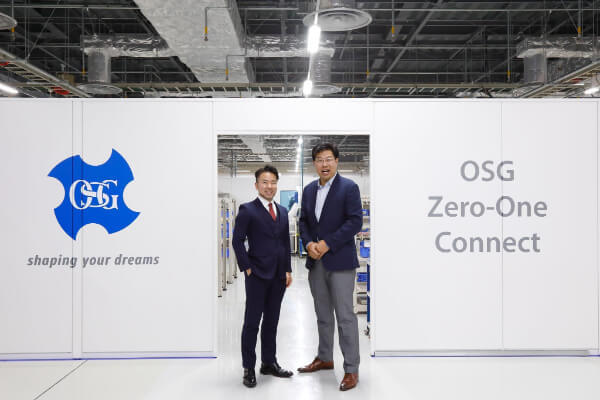
1997年 静大工学部 精密機械工学科卒業 日本電信電話株式会社入社
オーエスジー株式会社中途入社 第四製造部設計課へ配属 【ドリル設計/新製品開発業務に従事】
2004年 デザインセンター穴加工グループ穴あけ開発チームへ異動【ドリル新製品開発に従事】
2005年 トヨタ自動車エンジン生技部へ出向 【エンジン生産の原価低減活動に従事】
2007年 デザインセンター開発グループ穴あけ開発チーム 係長就任 【ドリル/タップ新製品開発に従事】
2009年 海外現地法人 OSGUSA 出向 Engineering Manager就任 【セールスエンジニアとして営業の技術サポート】
2013年 OSGUSA Vice President 就任 【エンジニアリング/マーケティング担当】
2019年 日本へ本帰国 第二製造部 新城工場スマートファクトリー実証室 室長就任【NEO新城工場立上げプロジェクト牽引】
2020年 NEO新城工場 部長就任 【達成感を原動力とし、0から1を産み出すNEO新城Zero-One Factoryにて現場力を後押しするDX化推進】
2002年、明治大学大学院理工学研究科修了後、株式会社インクス入社。自動車部品製造、金属加工業向けの3D CAD/CAMシステム、自律型エージェントシステムの開発などに従事。2009年にコアコンセプト・テクノロジーの設立メンバーとして参画し、3D CAD/CAM/CAEシステム開発、IoT/AIプラットフォーム「Orizuru(オリヅル)」の企画・開発などDXに関する幅広い開発業務を牽引。2014年より理化学研究所客員研究員を兼務し、有機ELデバイスの製造システムの開発及び金属加工のIoTを研究。2015年に取締役CTOに就任後はモノづくり系ITエンジニアとして先端システムの企画・開発に従事しながら、データでマーケティング&営業活動する組織・環境構築を推進。
目次
多品種少量生産を担う国内マザー工場
田口氏(以下、敬称略) この度は、NEO新城工場にお招きいただきありがとうございます。こちらは、どういった役割を担う工場なのでしょうか。
桝田氏(以下、敬称略) NEO新城工場は東三河地区にある4工場の内の1つで、超硬ドリル、超硬タップ、ハイスドリル、ハイスエンドミルの製造に特化しています。11万2,000平方メートルの敷地面積に700人の従業員が勤め、月産70万本の生産能力、月当たりでは6,000種類、8,000ロットの生産能力を有しています。
田口 桝田さんは、どういった経緯でNEO新城工場の立ち上げに携わったのですか。
桝田 自己紹介も兼ねてお話しします。私は静岡大学工学部を卒業後、大手通信メーカー勤務を経て、メーカーでのものづくりに携わりたかった想いを叶える為に、1997年にオーエスジーに中途入社しました。そして、穴あけ加工工具のドリルの設計・開発業務に8年間従事した後、トヨタ自動車エンジン生技部へ2年間出向し、エンジン生産にかかわる工具の原価低減に取り組み、帰任後は開発グループ係長として差別化新製品開発に注力しました。
2009年から約10年間は米シカゴにある海外現地法人OSUGAへ出向し、セールスエンジニアとして現地営業マンの技術サポートを担当した後、Vice Presidentに就任しエンジニアリングとマーケティングを統括。2018年12月に日本へ帰任すると同時に、新城工場スマートファクトリー実証室(SFJ)室長に就任してNEO新城工場立ち上げプロジェクトをけん引し、2020年12月からはNEO新城工場の部長として、生産現場のDX施策を進めています。
田口 SFJ室長になったのは、こうした経験を買われてのことですか。
桝田 インダストリー4.0や将来を見据えた生産体制の増強、超多品種少量生産と生産体制のデジタル化を目的に、新工場建設の話が始まったのは、2018年2月のことです。12月にプロジェクトを主導するSFJが発足するとともに、室長に着任しました。私は工場の叩き上げ人財ではなく、工場のことはずぶの素人ですが、素人だからこそ産まれる「発想の転換」に期待をしていただいたのかもしれません。
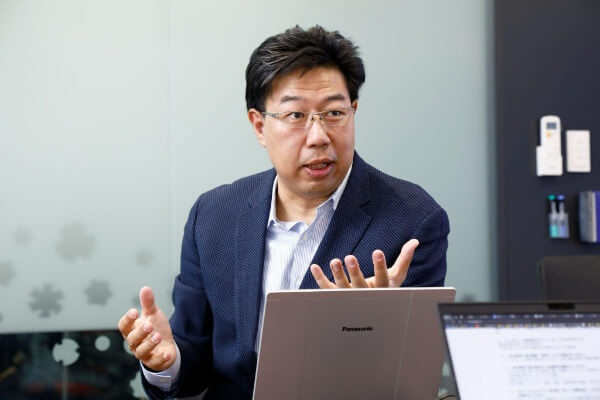
また、私自身「一生懸命に取り組む限り乗り越えられない試練はない」というのが持論であり、新製品の開発や駐在期間中は「達成感を原動力に」をモットーとし市場開拓に奮闘してきました。そういったポジティブ思考を踏まえて新たなチャレンジの場をいただけたのかもしれません。
新工場のコンセプトは「Zero-One」
田口 NEO新城工場のコンセプトを、どのように具体化していきましたか。
桝田 私がシカゴから帰任した時点で、工場の広さやレイアウト、旧工場とつなぐといった構想はできていましたが、生産体制刷新のコンセプトはまだ未確定の状況でした。ただし、私自身も工場の経営・運営や生産体制の刷新に関してまったくの素人ですから、まずは関係者に積極的に声をかけ協力を仰ぎ、生産企画・製造技術・生産管理の各部署から集まったSFJチームメンバーとも意見を出し合いながら物事を進めました。
スマートファクトリーの具現化に向けて動き出したのは、工場が完成し機械を近隣の大池工場から移設し終わった2020年6月からです。経営層からは「ただ機械を並べるだけではなく、逆転の発想で新しいことに是非挑戦をして欲しい」と言われていました。また、生産体制刷新の根幹となるデジタル化は【0】と【1】のコンビネーションで成り立っていることも加味し、【0】から【1】を産みだすゲームチェンジャーであり続けたいとの想いから「Zero-One」を工場全体のコンセプトとして決めました。
これを受け、新しい発想が生まれることを期待し、NEO新城工場以外の呼び名として「Zero-One Factory」、フリーアドレスを採用するオフィスは「Zero-One Office」、社員が日々利用するカフェテリアは「Zero-One Cafeteria」というように、主要エリアの名称に「Zero-One」を冠しています。
田口 スマートファクトリーに対しては、どのように捉えていますか。
桝田 我々が最終的に描いた構想は、ボタンを押せば全自動で製品が完成する「お金をかけた見た目のかっこいい自動化」ではありません。週末無人稼働に必要なロボットなどはもちろん導入するとともに、スキルを持った製造現場の方々の無駄を省き効率的な生産を可能にする「現場力を後押しするデジタル化」をDXとともに推進・深化することだと考えています。
田口 自動化だけではなく、デジタル技術の導入による人と生産の効率化がテーマになっているわけですね。
桝田 スマートファクトリーに関しては新聞などでよく取り上げられていますが、100社あるとそのコンセプトも100通りあります。アセンブリの会社や毎月同じ製品を指定された数作るものづくりと、我々のような毎月の受注の状況で生産するものが目まぐるしく変わる超多品種少量生産の会社とでは、段取りの数が根本的に大きく異なってきます。これから労働人口が減少するなか、アウトプットを最大化するにはどうすればよいか。その答えの1つがデジタル技術の活用でした。
また、当社は工具メーカーとして、お客様から選ばれる存在であり続けなくてはなりません。そのためにはお客様に寄り添ったフレキシブルな対応や、約束した納期を確実に守ることが求められます。例えば、ある日の朝からお客様がテストを予定されている場合、前日までに確実に製品をお届けしないといけません。簡単にできることのように考えがちですが、さまざまな阻害要因から常に100点を取り続けるのは難しいことも事実です。
製造業にとってQCD(品質、コスト、納期)は永遠の課題であり、NEO新城工場では、お約束した納期で確実にお届けするものづくりを提唱しています。
納期を守る手段としてのデジタル化
田口 もっとも重要な納期を守る手段として、デジタル技術の導入があるわけですね。
桝田 その通りです。具体的にはMicrosoftのBIツール「Power BI」を導入し、自社でものづくりを見える化するアプリを作り、QCDを管理。中期経営計画で掲げたROAの拡大を実現するため、初回回答納期遵守率などを遵守する仕組みを構築しました。
田口 初回回答納期率95%は、かなりの高水準ですね。
桝田 他にも原価率や欠品率なども可視化し、最終的に会社の利益拡大に貢献しましょうということで、工場側でKPIを定めています。
田口 経営上で重要な数値となりますが、誰が決めているのですか。
桝田 工場サイドです。毎月押さえないといけない指標があり、それらを管理するページを作っていった結果全てがつながっていきました。そして、これらの数字は経営層を交えた月次開催の会議の場などで報告しますし、権限を付与された社員であればいつでも閲覧することが可能です。問題点は何でいつまでに解決するのか、予定通り正しく解決されたかのか、について答え合わせもできます。
田口 バランスト・スコアカードのように見えますが、アメリカでも事業を指標ベースで管理されていたのでしょうか。
桝田 はい。もちろん会社としてのスコアカードの管理はされていました。例えば営業系の方々は個人別の四半期の売上目標・新製品売上目標・顧客アカウント数の管理をしており、製造系はNEO新城工場と同様に製造原価・稼働率・欠品率などさまざまな製造指標について管理を行っていましたが、私が駐在していた当時はまだエクセルベースがほとんどでした。
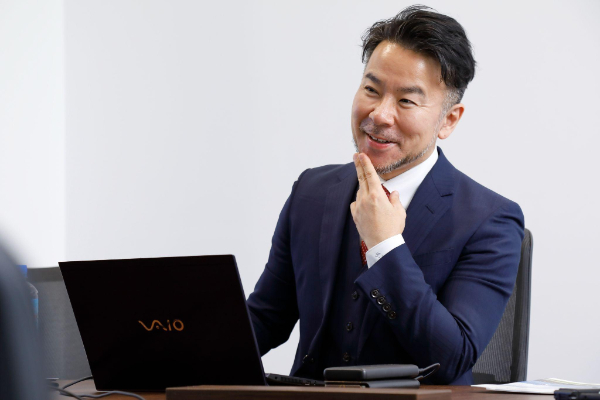
現場力を支えるデジタル化がキーワード
田口 ここからは、NEO新城工場について、さらに掘り下げてご解説ください。
桝田 NEO新城工場は多品種少量生産の工場です。当社はカタログ品と、お客様のニーズに合わせた特殊品の両方を手掛けています。特殊品はお客様のアプリケーションに最適化した仕様になっており、形状も複雑でなかなか作り難いものが多いですが、痒いところに手が届く総合工具メーカーになることで、お客様に継続して選んでいただける存在になりたいと思っています。
例えば海外にも製造拠点を持つお客様の場合ですと、新しいラインを作るためのテストを日本で実施され、初回の手配は5本納品と少量であったとしても、うまくいくと国内の量産ラインで使われるようになり、次は海外の工場に横展開され、結果的に膨大な数になります。スペックインするので、他のメーカーに目移りされることもほぼありません。当社の工具がないと生産が成り立たないというのが、目指すべきところです。
田口 そこまで行くと、10年以上は使い続けられるわけですね。
桝田 ですから、オーエスジーは特殊品も喜んで引き受けるスタイルを貫いています。規格品だけ作っていると楽ですが、他社ではなかなか作れない600ミリメートルの長いドリルなど、難しい製品にも愚直に取り組むのがOSGの文化でもあり、そこから学んだことが将来の新製品の作り込みや製作可能範囲拡大につながる効果もあります。
NEO新城工場は生産体制の刷新などが課題で、ロボットなどの技術を使いながらも、現場力を支えるデジタル化がキーワードでした。実際に行っているのは、徹底した加工の見える化です。加工機ごとの稼働率、生産スケジュール、生産状況などの情報を共有し、収集したデータを分析。生産の無駄を徹底的に省き、状況に応じた最適な組み入れを行うことで、標準品・特殊品ともにリードタイムの短縮を目指しました。
他にも、複合加工機においては能力を最大限に活かす多品種少量生産の実現、スマートエリアでは稼働率を最大化するためエリア内のセッティングルームでスケジュールに従い外段取りを行っています。事前に段取りをすることで、加工する機械にオペレーターが関わる時間を最小限にすることができ、ここでは外段取部隊と機械段取部隊とでグループを2つにわけ、72時間連続稼働で様々な製品を昼夜問わず作っています。
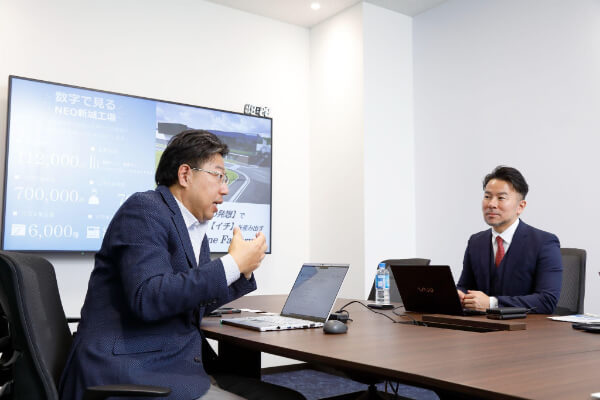
田口 標準品に少し手を入れた、言うなれば標準品と特注品の間の製品は、どちらに分類されますか。
桝田 特注品として取り扱っています。標準品は材料のストックがありますのでそれを流用すれば短納期で作ることが可能です。ですから営業には、特注品を受注する際にできればお客様と話し合って標準品の材料を使えるものにしてくださいとお願いすることで、製造リードタイムの短縮だけでなく価格も安く提供することが可能となり、他社から切替の受注につながる可能性を広げられます。
田口 確かにそうですね。
桝田 仮にお客様が全長95ミリメートルの形状を希望された場合、材料在庫がある100ミリメートルで製作させていただけないかという交渉ができるかどうかです。
生産管理と製造状況を見える化
田口 製造工程の見える化を通じて、NEO新城工場は納期を厳守した多品種少量生産を実現したと理解できました。
桝田 以前はエクセルで管理していましたが、6,000種類、8,000ロットを作るのにエクセルの対応でよいのかというのは、大きな疑問でした。そこで、ペーパーレス化や脱エクセル管理に舵を切る必要性が出てきて、デジタル技術を活用した生産体制の刷新につながりました。
現場力を後押しするデジタル化ツールは大きく分けて2つあり、1つは生産管理のツールです。ボトルネック工程からのアウトプットを最大化する為に、生産スケジューラーなどを活用しています。類似アイテム同士をできる限り集約して連続で組み入れることで段取替えを極限まで削減したり、加工機の混雑具合により稼働率に余裕のある他機種へ負荷分散するなど最適化組入れを実現することで最終的な生産アウトプットも最大化できました。
また、製造現場では納期を確実に守るものづくり】と同時に納期リクエストにフレキシブルに対応すべく、加工優先順の管理方法を刷新いたしました。常に今最優先で作るべきものに注力するものづくりを実践するためにRFIDを活用しており、製品の進捗データはすべてERPと連動し最新の加工優先順位をステイタスモニターで確認できます。さらに、家電量販店やスーパーマーケットで価格を表示する電子ペーパーを活用し、工程完了納期も同時に表示することで、今何を作るべきかがわかるように徹底しています。
一昔前は工程ごとに設置したホワイトボードに「進行表」と呼ばれる紙を貼り、加工機別の仕掛状況や加工優先順位管理、納期確認などを行っていましたが、お客様から納期変更依頼がある度に生産管理担当者が現品の所在工程を調べ、その現場に出向いて、赤ペン先生のごとく納期を修正することに疑問を感じていました。だからこそ、ステータスモニターや電子ペーパーに置き換えて今までの無駄な時間を大幅削減したのです。
田口 こういった現状は、どのように確認できるのでしょうか。
桝田 各工程に設置されたモニターです。ステイタスモニターに工程完了納期に対する各オーダーの残り時間が色分けで区分されて表示されるので、どれから取り掛かればよいか、遅れが多いかなど、現状を瞬時に判断することができます。システムを使うことで現場の方々が迷うことなく、リアルタイムの優先順位で加工に取り組める「シンプルスマート」な環境を整備しました。
そしてもう1つの現場力を後押しするデジタル化ツールは、製造の状況を管理するPowerBIです。製造の状況がさまざまな切り口で見える化されるPowerBIが存在しますが、そのなかでも稼働率の見える化はとても重要で、「前日と当日の比較」だけでなく、「週次・月次での比較」や「加工機別の比較」なども可能となっています。
稼働率と言ってもそれぞれの会社によって定義は異なり土日を含めない場合もありますが、弊社の稼働率の定義は365日24時間をベースとしています。繁忙期には製造現場の方々に土曜日も臨時出勤していただきますが、基本的に日曜日は出勤しません。しかし自動測定・自動補正機能を有した機械を取り揃えることで、日曜日でも平日と同様の稼働率が得られていますし、週末にロット内の数量が多いアイテムを流すような工夫もしており、これも高稼働率につながる要因と言えます。
田口 自動で作れるものを週末に寄せているということですか。
桝田 そうです。平日は段取工の人数も多いので本数の少ない小口オーダーの対応に注力し、週末稼働時に300本ロットを3種類連続で作るといった具合です。ですから、日曜日でも90%以上の稼働率ということもあります。また、同じ機種でも号機によっても稼働率に差が生まれますので、実際に稼働が低かった加工機については、製造現場のラインストップミーティングにて原因の分析を行い稼働率の改善につなげています。
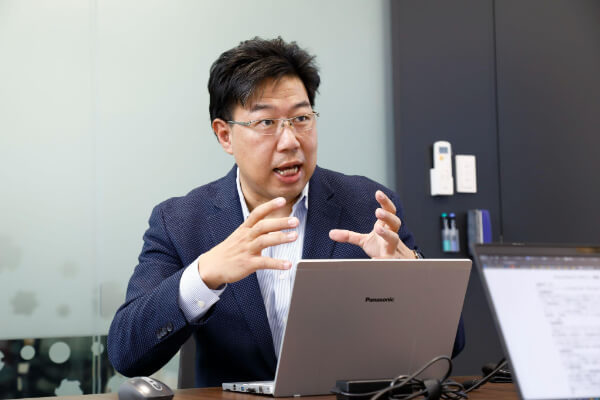
田口 BIを主とした見える化のシステムは、どなたが作ったのですか。
桝田 NEO新城工場のデジタル推進チーム(現DX推進課)が担当しました。OSG社内のIT部門は基幹システムや営業系のシステム対応などでとても忙しいので、製造の状況を管理する見える化システムに時間を割いてもらうのは申し訳なかったので、製造技術、生産管理のメンバーや、製造現場でエクセルを上手に使いこなすメンバーを集め、工場直下にデジタル推進チームを設けたのです。これまで紹介したBIベースの見える化システムはすべて彼らが作ったもので、何ひとつ外注していません。日々の製造の中で起きる問題にスピード感を持って対処するために、データを見たい切り口で自由に料理しすぐに自社内で可視化できるのは、我々の強みです。
納期に関するBIもあります。ものづくりでは初工程からの遅れが蓄積して最終工程に近づくにつれて遅れの数が増え非常に遅れているように見えます。ところが、最終工程の職制からすると、抱えている遅れが前工程からの累積の遅れなのか、それとも自分たちの工程で遅れを発生させたのか、また遅れを軽減・解消できたのかなど、責任の所在がわかりません。そこで明確化したいという声が挙がり、要望に応じて作りました。ここでは赤系統の色で遅れの発生や増加を、青系統の色で遅れの解消や低減を確かめられます。
例えば、ある工程で赤色の遅れが多発しても、適切な対策を講じることで遅れが減少したことがわかるなど、班のパフォーマンスを表す成績表としても機能しています。今は、毎週の週次ミーティングで現場の係長が自分の係の製造進捗状況や問題点を分析し対策をいつまでに実施するかなど、BIのデータとパワーポイントを駆使しプレゼンするのが、我々の工場のスタイルとなっており、同時に職制の方の分析力・プレゼン力・伝える力を磨くことにもつながっています。
田口 状況の可視化や確認に関して、BIは非常に優秀ですよね。
桝田 ある工程に到着した時点で70%遅れがあり、その工程の完了時点では23%まで減っていたら、その班が遅れのリカバリーに奮闘した頑張りが浮き彫りになります。かつ、70%遅れで入ってくるということは、その前工程のどこかが足を引っ張っているわけです。そこまでを見える化できるのがBIの良さであり、これがないと工場は回せません。
ちなみにこういったBIの情報はリアルタイムでどこからでもチェックできるのが利便性の1つで、例えば私が海外出張に出かけていても携帯電話さえあれば製造の状況をどこからでも把握することが可能です。逆に工場の方々からすると常に状況を見られているという意識が働きますが、暗黙の信頼関係の醸成にも役立っています。
田口 これだけDXを進めたとなると、設備投資にかなり費用がかかったと思います。
桝田 もっとも費用を投じたのは生産スケジューラーですかね。毎年の保守料金なども加味するとかなりの額になるかと思いますが、PowerBIにはほぼお金はかかっていませんし電子ペーパーも皆さんが想像されるよりは決して高価ではありません。
現場の意見をくみ取ったツールを作ること
田口 大胆な取り組みでしたが、周囲の理解はいかがでしたか。
桝田 一般的には既設の工場にDXを展開する流れかと思いますが、NEO新城工場の場合は、新しい建屋を作るプロジェクトと並行してDXを展開していきましたので、今までの概念から脱却して新しいことを始める、つまり職場環境を大きく変えるチャンスがありました。その施策として「Zero-One Office」や「Zero-One Cafeteria」を作り、社員の皆さんの意識改革につなげて行く流れができたのはとてもラッキーでした。
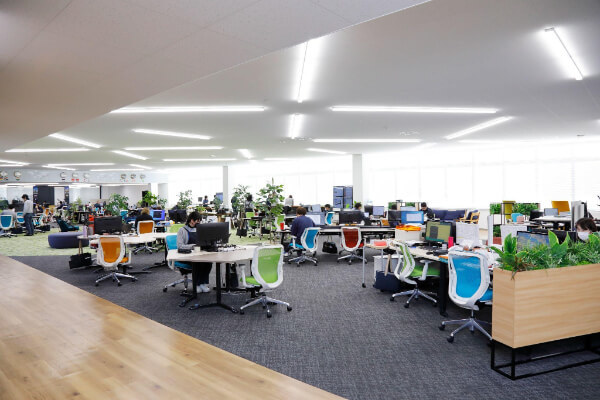
「Zero-One Office」は社員が個々の席を持つことなく、働く場所を自由に選べるフリーアドレスのオフィスで、1人で集中できる席など、さまざまなスペースを設けています。シャッフルされることで今まで関りがなかったもの同士で交流が生まれ、所属部署の壁を越えた横のつながりを生んでいます。
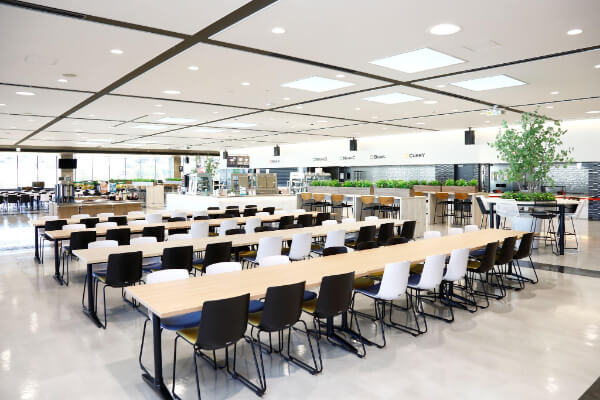
「Zero-One Cafeteria」に関しては、昔ながらの工場の食堂を象徴する長テーブルに丸椅子が並ぶスタイルから大きく変え、メニューも12月なら唐揚げ食べ放題など、毎月さまざまな御褒美ランチイベントを開催しています。リーズナブルな価格にしているので反響が良く、楽しみにしていただいているようです。フリードリンクやサラダバー、焼き立てのパン、スイーツなどメニューも豊富で、従業員の満足度向上に一役買っていると思います。
田口 働く環境を大きく改善することで、皆さんの意識を前向きにするのが狙いでしょうか。
桝田 そういった考えもありますし、NEO新城工場はDXだけでなく複合化・省人化・無人化などさまざまな取組みをスピード感を持って実践する工場を目指しておりますので、そこで働く皆さんにも新しいことにポジティブにチャレンジする意識が育って欲しいと思っています。私も部長になり4年目を迎えましたが、多くの方のご協力のお陰で以前と比べるとかなり雰囲気が変わってきたと実感できていますし、今後も更に進化させていくのが私の役割だと思っています。 毎年新しいチャレンジを継続していますが、その取組みのアイデアやヒントは製造現場で働く社員の皆さんとの会話の中から生まれたものも多くありますので、いただいたアイデアを忘れないように携帯にメモして形に残しています。単にDXを推進するだけではなく、社員の皆さんからいただいた意見を具現化して実践すること、そして「あったら良いな!が形になった」を積み重ねることで信頼関係が構築され、結果的にDXが加速し大きな成功要因になっているように感じます。
PowerBIの各ツールも一方的に作って使ってもらうのではなく、実際に使ってお仕事をされる現場の方々の意見をくみ取ってシンプルスマートにしないと結局は陳腐化してしまう危険性があります。時間はかかりますが、綿密に打ち合わせを重ねてより良いものを作ることに挑戦し続け、最終的には他の工場への横展開も行うという意味で、NEO新城工場はDXのマザー工場としての役割も担っています。
田口 非常に大きな取り組みだったからこそ、周囲からの反響も大きかったと思います。
桝田 愛知県の大村知事にも工場へお越しいただいたり、ものづくり日本会議中部地区研究会 特別シンポジウムにて「現場力を後押しするDX化」と題して、NEO新城工場での活動や弊社グループ会社でのDX事例も踏まえ、企業規模に関わらずDX成功の鍵についてお話しする機会もいただきました。
田口 DXを定着させるポイントについてもお聞かせください。
桝田 1つは、現場の意見をくみ取ってシンプルかつスマートなツールを開発することです。難しいものは必ず敬遠されるので、使いやすくモニターを見てすぐさま状況判断ができるようなものが理想的です。また、DXなどの新しい取組みをする際はよく言われる20:60:20の法則が付いて回ります。チャレンジ精神旺盛な20%の方は色々と自発的に進んでいただけますが、中間の60%の方々に先「ずはやってみようじゃないか!」と前向きに取り組んでいただける仕掛けを講じることが大切だと思います。
また、デジタル機器は導入するだけでなく、それをしっかりと理解して使いこなしていただくことがとても重要です。ただ見えているだけではダメで、関係者が使いこなせるよう教育しなければなりません。さらに、この教育も大人数を集めた研修ではなく、時間はかかりますが5人グループで8回実施するなど、少人数で行う方が理解度も高く効果的だと思います。
使いこなせるようになると同時にデータを分析して結果につなげるスキルも大切となってきます。しっかりと理解して日々の業務を積み重ねていくと、「こんなのあったら良いな!」と新しい切り口でデータを分析などの新たなアイディアが生まれ、それをまた見える化することで深化が加速する流れになります。 DXを進めていくと、予期せぬ問題が勃発するなど梯子を外されるような事態が起きることがあります。そのような状況下でも、関係者が問題を他人事とせず自分事として腹を括り向き合って取組む姿勢を持つこと。更に最後まで諦めずに挑戦し続けた後に、達成感を共有することで、一体感が生まれ次なる挑戦につながるプラスの循環が生まれてきます。そこに必要不可欠なのはコミュニケーションであり、NEO新城工場では各部署の皆さんから絶大な協力をいただけたことは本当に大きかったと思いますし、更にはデジタル推進チームを工場直下に設置し、寄り添い型でスピード感のある対応ができたことも大きな効果につながったと思います。
現場への周知という点では、毎月月初に30分程度の月次朝礼の時間を使って、我々製造業を取り巻く環境の変化の例として2025年の製造業の壁や、DXを進めないとどんな未来が待っているか生の声で伝え、取組みの意義や効果について理解を深めていただいています。
納期と言う切り口で言えば、10年前と今とではお客様の納期に対する考え方が大きく変化しており、例えばAmazonは指定した納期に必ずすぐ届くから便利で利用するのであって、製造業も絶対に約束した納期でお届けするものづくりをしないとお客様から選んでいただけなくなるなど、納期遅れの引き起こす悪影響などを身近な話からつなげていくと、皆さんに重要性を理解してもらいやすいです。初回回答納期遵守率の改善など取り組みが確実に効果を示したときには、効果をしっかりと説明するとともに、感謝の言葉を伝えることで達成感を共有し次なる挑戦の原動力になると思います。
田口 Koto Onlineではいろいろな企業にインタビューをしてきましたが、DXに成功している方たちに共通しているのは、経営や現場、マーケットとの距離が近いということ。御社の場合、とりわけ経営層と現場との関係性が良好であると感じました。
桝田 実際に構想を始めたのが2020年6月からで、2022年半ばに今の形になりました。DXは終わりなき挑戦ですし、現在はデジタライゼーションに取り組んでいるところです。DXの最終形はデジタルトランスフォーメーションであり競争優位性を見出し、新たな価値を生み出すことで、この先まだまだやるべきことやりたいことはたくさんあります。「できると信じるかできないと信じるか、結果は全てその通りになる」という名言もありますが、私はOSGの企業文化であれば必ずできると信じて、この先も達成感を原動力としてポジティブ思考で進んでいきたいと思っています。
田口 さらなる進化を期待しています。本日はありがとうございました。
【関連リンク】
オーエスジー株式会社 https://www.osg.co.jp/index.html
株式会社コアコンセプト・テクノロジー https://www.cct-inc.co.jp/
【注目コンテンツ】
・DX・ESGの具体的な取り組みを紹介!専門家インタビュー
・DX人材は社内にあり!リコーに学ぶ技術者リスキリングの重要性
・サービタイゼーションによる付加価値の創造と競争力の強化