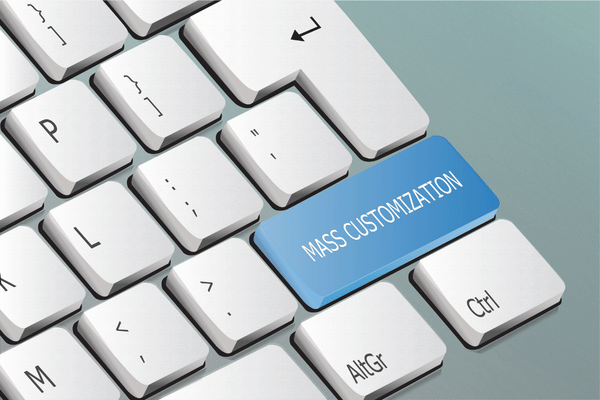
「大量生産並みのコストで、オーダーメード製品を作る」というマスカスタマイゼーションの考え方は、日本の製造業の未来を明るくするものといえます。この考え方はどこから生まれ、それを実現するにはどんなことが必要なのでしょうか。実際のビジネスでこのコンセプトを仕組みとして実装している企業などについても紹介します。
マスカスタマイゼーションとは
マスカスタマイゼーション(英語でmass customization)は、一般消費財を扱っている製造業ではすでになじみのある言葉となっているかもしれません。マスカスタマイゼーションは、大量生産の生産性を維持しながら顧客のニーズに合わせた製品を生産する仕組みです。つまり「大量多品種生産」ということになります。
この説明を聞くと「多品種少量生産」とどう違うのだろうと思われる人もいるでしょう。多品種ということは細かな顧客の好みに合わせた「受注生産品」ということになります。そのことと「大量生産のメリットを維持する」ということは二律背反になるのではないか、という考えもあるのです。
もちろん特定の好みに合わせた商品は売れる数も少ない、ということになりますが、そうした自分の好みに合わせた「特注品」を一般の既製品と同じ価格で購入できる、となったら消費者はどういう反応を示すでしょうか。おそらくあまりその商品を買わなかった人も、買ってみたいと思うはずです。これによって市場の拡大が期待されます。つまり大量生産のメリットというのは、低コストで生産できる、ということなのです。
マスカスタマイゼーションでは、顧客側はオーダーメードの製品を低価格、短納期で入手でき、メーカー側は付加価値の高い製品を提供することで収益性の高いビジネスを展開できます。そのため、マスカスタマイゼーションを実現する仕組みには常に低コスト、高効率の維持が欠かせません。
またマスカスタマイゼーションの手法は、従来注文生産を行ってきた企業にとっても有効です。一般消費財メーカーだけでなく、工作機械などの工業製品は受注生産が中心というケースが多いので、マスカスタマイゼーションによって、大量生産と同じレベルのコスト低下が見込めるならば、それは新たな競争力の源泉となります。
マスカスタマイゼーションが注目される理由
マスカスタマイゼーションは製造業のビジネスモデルを変える概念だと言われています。マスカスタマイゼーションが注目される背景の1つに「製品ライフサイクルの短期化」が挙げられるでしょう。
経済産業省は、2016年版ものづくり白書「概要」~第四次産業革命への対応~のなかで「過去10年で全業種において、製品ライフサイクルは短縮傾向にある」と明記しています。実際に同省の調べでもほとんどの業界で、10年前との比較で自社の主要製品のライフサイクルについて、「短くなっている」と回答した企業が「長くなっている」と回答した企業よりも多い結果が出ています。
原材料や労働力のコストを限りなく低減させて大量生産しても、製品がコモディティ化してしまえば、販売量は振るわなくなり、在庫の山ができて儲け度外視で安売りするしかありません。コモディティ化するまでの時間が短期化してくると、さらに企業の体力を奪うことになります。
一般消費者に近い商品を売る製造業では、こうした現状を打開するために、顧客のニーズに合わせた注文生産品を拡大させようとしました。しかし、これは一般の商品と比較してコスト高になってしまい、大きなビジネスにはなりにくいという現状があります。
また1つの商品のバリエーションを増やし、さまざまなニーズを拾っていこうという取り組みも続いています。しかしこの取り組みもその商品自体がコモディティ化してしまえば、バリエーションを維持して販売し続けることはできなくなります。
このようなジレンマに悩む企業にとって、マスカスタマイゼーションが実現できるなら本望です。「カスタマイズ」という付加価値を提供し、多様化、個別化する消費者のニーズにも応えることができ、価格競争力を維持しながら在庫リスクも大幅に軽減できます。
マスカスタマイゼーションの課題
「モノが売れない」「事業の成長性が鈍い」と悩む製造業にとって、マスカスタマイゼーションは、まさしくブレイクスルーとなる概念です。しかしこれを実際の製造現場で実現しようとすると、さまざまな課題を乗り越える必要があります。
まずマスカスタマイゼーションには、生産にまつわるあらゆるプロセスでのデジタル化が必要になります。マーケティングに始まり、製品の企画・開発・設計、そして実際の生産の現場はもちろんのこと、物流、販売、カスタマーサービスに至るまで、一気通貫で情報共有できるシステム環境が欠かせないと言われています。
さまざまなプロセスをデジタル化することにより、人件費などのコストが低減され、生産・販売のスピード化を図ることで、一般の商品と同じ価格で「カスタマイズされた商品」を売ることが可能になり、また短納期で消費者に商品を届けることができるようになるのです。
マスカスタマイゼーションを実現するには、ほとんどの企業にとって多くのIT関連投資が必要であり、それに合わせて生産現場などの新設、改良などのコストも欠かせなくなるでしょう。
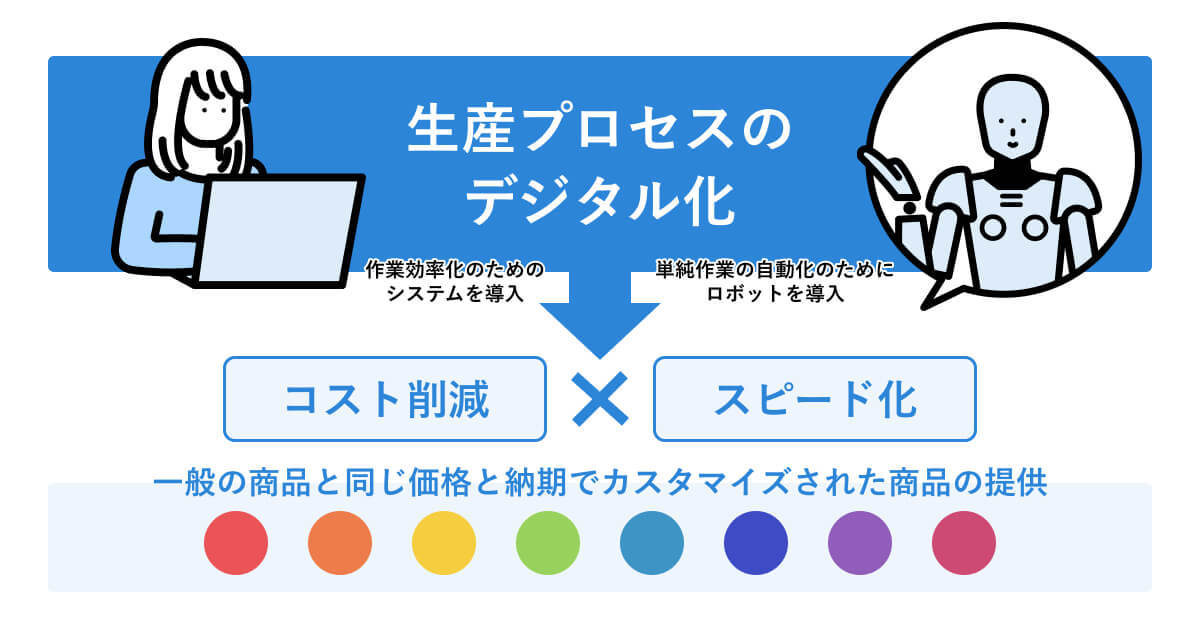
具体的には生産現場ではIoT機器などを用いたソリューションとそれに伴う生産の自動化を実現するシステムが必要です。また複数の生産現場と経営管理部門の情報連携を司るMES(Manufacturing Execution System)、受発注ではCRM(Customer Relationship Management)、企画開発ではCAD(Computer-aided Design)、PLM(Product Lifecycle Management)なども必須となるでしょう。そしてサプライチェーン全体を管理するSCM(Supply Chain Management)の導入も重要となります。
また、大量生産と個別受注生産は完全には両立させにくい点も懸念されます。ここまで説明したデジタル化は大量生産には大きく貢献できることがはっきりしていますが、個別のニーズに対応するプロセスが不十分だと、生産スビードが鈍る可能性があります。スピーディな生産体制のなかに個別ニーズを素早く反映できる仕組みづくりが必要です。
逆に個別ニーズの取り込み、商品化だけに集中してしまうことで、生産プロセス全体が複雑化してしまう懸念もあります。こうした問題を解決するには、デジタル技術をうまく生かしてバランスを取ることが欠かせません。デジタル投資を抑えるために人手による改善を繰り返していては、おそらくマスカスタマイゼーションは困難なものになるでしょう。
マスカスタマイゼーションの取り組み事例
ここからは、マスカスタマイゼーションへの理解を深めるため、実際にマスカスタマイゼーションを取り組んでいる企業についてみていきましょう。
今回は2つの企業を取り上げましたが、これ以外にもコンピューター販売大手のデル・テクノロジーズ、ドイツのBMW、ナイキ、日本ではユニクロやZOZOなどが現実のビジネスの中で、マスカスタマイゼーションのコンセプトを実践しています。
また消費財メーカーだけでなく産業用機械など工業製品を製造している企業が、生産現場の効率化を高めて、短納期受注や納期・仕様変更に迅速に対応し、コストを抑えてニーズに応えているケースはいくつもあります。
事例① ハーレーダビッドソン
1903年創業のハーレーダビッドソン(Harley Davidson)は、オートバイ専業メーカーで大型バイクのみを提供しています。同社のオートバイユーザーのほとんどは、購入した製品をカスタマイズすることが多く、最初に提供される市販品はいわば「素材」といえるでしょう。
こうしたカスタマイズのニーズがあることから、同社は車輪、マフラー、ハンドルなどあらゆるパーツをユーザーなりに組み合わせて、初めから購入できるオーダーメイドサービスをWebサイトで展開しはじめました。
これに合わせて同社はペンシルバニア州にある工場を刷新します。この工場はIoT(モノのインターネット)システムにより、稼働状態をセンサーからの情報で把握できるようになりました。また生産プロセスの大部分がデジタル化され、作業者は自動的に必要な情報を正確に得ながら、作業ができるようになりました。
Webサイトからカスタム発注を受けると、必要なすべての部品のリストが取り入れられ、生産計画に反映します。部品の在庫確認と手配、生産の進捗管理も生産管理システムが行います。
この工場では、1台ごとに異なる製品を生産しても作業手順が標準化されているため、それほど多くの熟練工は必要なく、作業者も従来の半分で済むようになりました。また新工場では納品リードタイムを2~3週間も短縮し、部品在庫も大幅に減らすことができたといいます。
事例② フクル
フクルは、衣類製造販売企業で群馬県桐生市に拠点を構えています。同社は自動化された生産システムを構築し、価格を抑えた女性用のオーダースーツとワンピースを生産、販売しています。同社は経済産業省・独立行政法人情報処理推進機構(IPA)が主催する「IoT Lab Selection ファイナリスト」のファイナリストにも選ばれています。
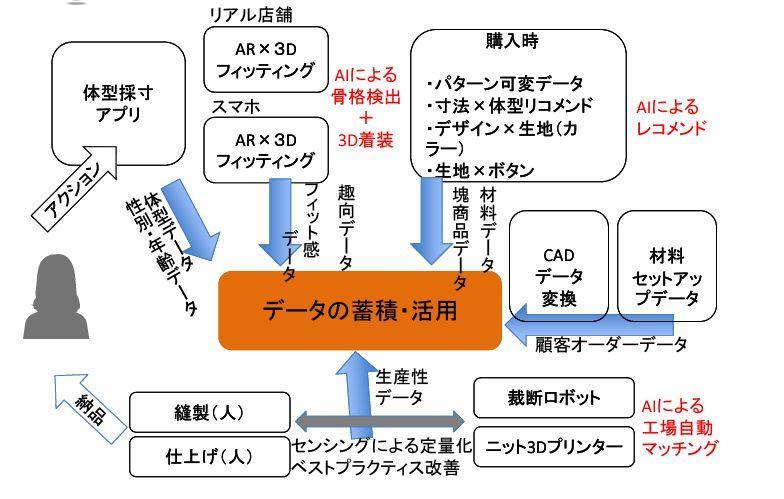
※フクルのSCMスキーム(経済産業省資料より)
同社のSCMシステムは生地、ボタン、デザイン、サイズの各データベースをクラウド上で稼働させており、これらの資材情報から、顧客から注文がはいると各商社、織物工場、オーダー工場、縫製工場などに発注し、完成品を顧客に届ける仕組みを構築しています。
同社の木島代表は「スマホで簡単に、自分仕様の服が買えるような仕組みができないか」という投資家の声をきっかけに、このビジネスを構築していきました。同氏は洋服のパターンやデザインをしていた経験から、原価を概算し、稼働していない工場や人を使って、一点物を生産できると踏んだのです。
各工場のシステムをクラウドコンピューティングでつなぎ、データの受け渡しを行うことで、時間とコストの節約を進め、ノウハウを共有して質の高い一点物を作り上げています。採寸も来店不要で、顧客の持っている服や顧客の画像から、プロのパタンナーが寸法の補正を行いデータ化していきます。このように同社では単にデジタルの力を利用するのではなく、プロフェッショナルの技術をデジタル技術と合わせて活用しています。
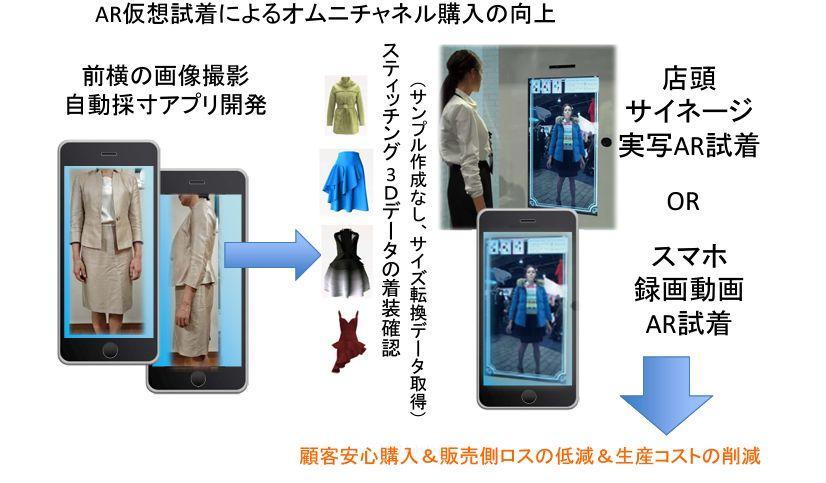
※AR仮想試着によるオムニチャネル購入の向上(経済産業省資料より)
さらに前面と側面の画像を撮影して使う自動採寸アプリを開発し、店頭のサイネージかスマホでAR(拡張現実:Augmented Reality)による試着を行えるように仕組みを作ります。これによって何度も採寸する手間がなくなり、コスト削減につながりました。
またビーコンとICタグで職人と製造した製品をIoTでつなぐことで、作業効率を改善させたり、ビーコンに反応したカメラで作業風景を顧客が閲覧確認できたりといったサービスも開発しています。
フクルの場合、オーダー製品をいかに低コストで早く仕上げるかが勝負であって、大量生産の必要はありません。しかし、一品生産である以上、できあがったもののクオリティは高いものでなければリピート利用につながりません。同社は、生産の効率化とクオリティの向上の両方にデジタル化を大いに活用しています。
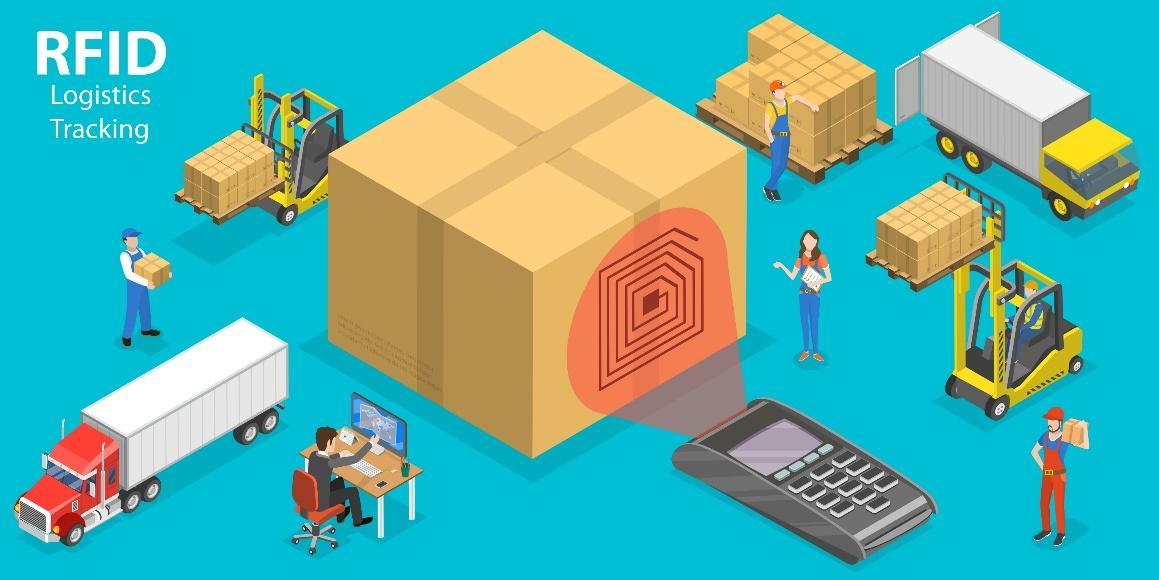
スマートファクトリーへの道
マスカスタマイゼーションを成功させるには、形式の違いはあるものの、IoTやビッグデータ、AI、ロボットなどの技術、そして高度なデータ活用ツールが必要です。さらにそれを支えるエンジニアリングチェーンやサプライチェーンがネットワーク化された各種システムや自動化の仕組みも必要となるでしょう。
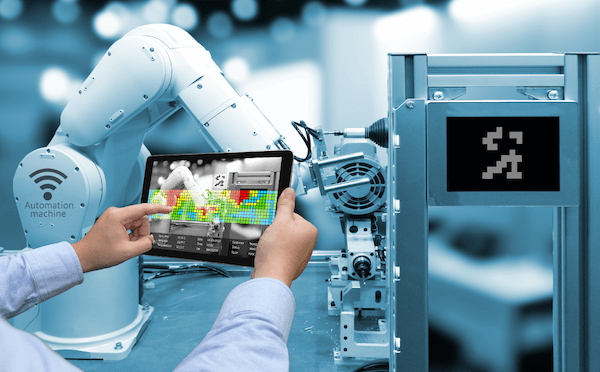
こうした仕組みを持つ工場を「スマートファクトリー」といいます。スマートファクトリーは 経営判断の迅速化や製造工程の可視化、レジリエンス(変動対応力)の強化、技術継承、 設備の予知保全などに大きな効果をもたらしますが、国内企業ではそれほど普及しているとはいえません。
経済産業省による「ものづくり白書」(2019年度版)では、製造過程のデータ化や自動化の実施状況に関する調査結果が掲載されています。それによると、データの利活用はまだまだといったところでしょう。
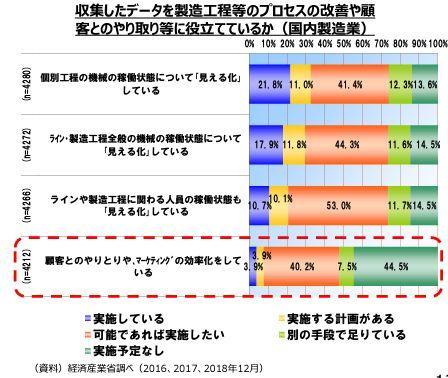
※収集したデータを製造工程等のプロセスの改善や顧客とのやり取り等に役立てているか(経済産業省による「ものづくり白書」(2019年度版)より)
収集したデータを活用して、顧客とのやり取りやマーケティングに利用しているかという問いに「実施している」と答えたのはわずか3.9%でした。また個別工程の機械の稼働状態について、見える化しているかという問いにも2割程度の企業しか「実施している」と答えていない状況で、データ活用そのものが進んでいないことがわかります。
まとめ:インダストリー4.0とマスカスタマイゼーション
スマートファクトリーが注目されたのは、「インダストリー4.0」というコンセプトの中で紹介されていたのがきっかけとされています。
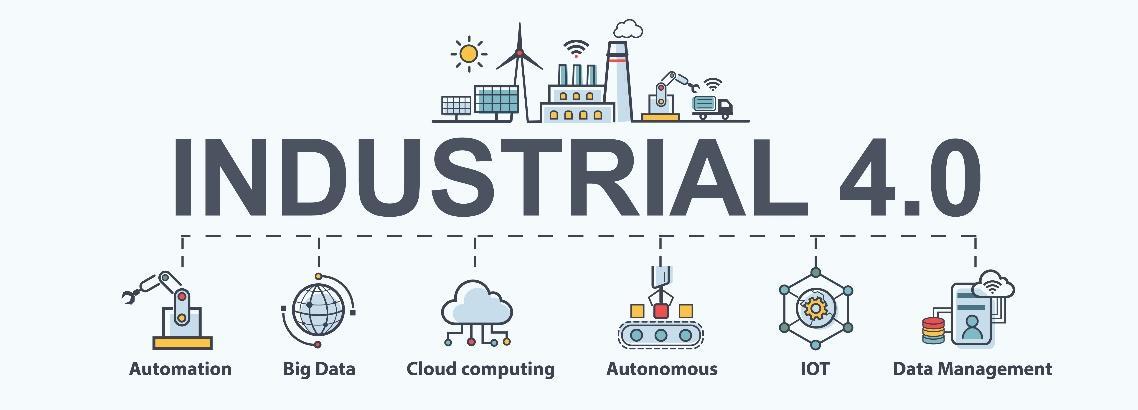
インダストリー4.0はで、ドイツ政府が2011年に発表した産業政策です。相互運用性、情報の透明性、技術的アシスト、分散型意思決定という4つの設計原則をもっています。マイスター制度が根付き、モノづくりの分野では日本とも競合することの多いドイツから発せられたコンセプトとして日本でも大いに注目されています。
総務省は情報通信白書の中で、「インダストリー4.0の主眼は、スマート工場を中心としたエコシステムの構築である」とし、これらの仕組みの整備が進むことで「例えば大量生産の仕組みを活用しながらオーダーメードの製品作りを行う『マスカスタマイゼーション』が実現する。」としています。
現在、日本企業ではDXが一種のブームとなり、さまざまなデジタル化の施策に取り組んでいます。一方で、生産現場でのデータ活用やデジタル化は進んでいないという現状も見逃せません。
こうした現状の中で「大量生産と同等のコストでオーダーメード製品を作り販売する」というマスカスタマイゼーションの考え方は、非常にわかりやすく、導入するメリットが明確です。この生産体制を実現することで市場のパイを拡大させることが大いに期待できるでしょう。
これを実現するには、相応の投資が必要となり、また運用ノウハウの積み上げも必要です。しかし、それ以上に、市場が成熟し経済力もある消費者がそろっている日本では、マスカスタマイゼーションは大きな可能性を秘めた生産手法だといえるでしょう。さまざまな業界で、少しずつスマートファクトリーへの取り組みが実践されていくのではないでしょうか。
【こんな記事も読まれています】
・国内製造業の再生を狙うINDUSTRIAL-Xが推進する[ESG×DX]時代の戦い方
・製造業における購買・調達業務とは?課題の解決方法も紹介
・サプライチェーン排出量はなぜ注目される?算定方法も含めて紹介