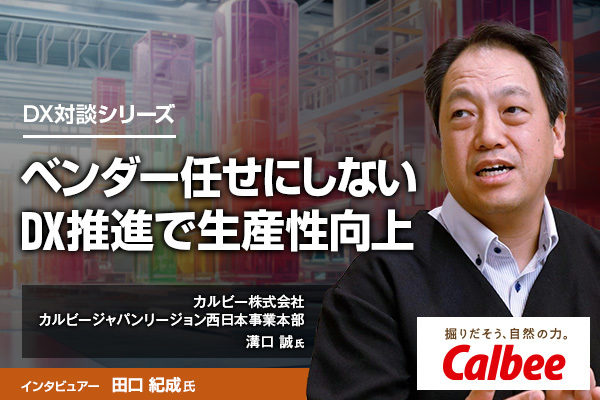
製造業のDXに対する取り組みについて、コアコンセプト・テクノロジー(CCT)CTOでKoto Online編集長の田口紀成氏が対談する本企画。第14回のお相手は、カルビー株式会社カルビージャパンリージョン西日本事業本部ゼネラルマネージャーの溝口誠氏です。
カルビーは「ポテトチップス」や「じゃがりこ」「フルグラ®」など、私たちの生活にお馴染みのスナック菓子やシリアル食品を製造・販売する大手メーカーです。
そんな同社では2019年からDXを本格的に推進し、2022年7月には滋賀県の湖南工場でIoT技術を活用した次世代工場モデルを実装しました。今回はこの取り組みについて掘り下げます。
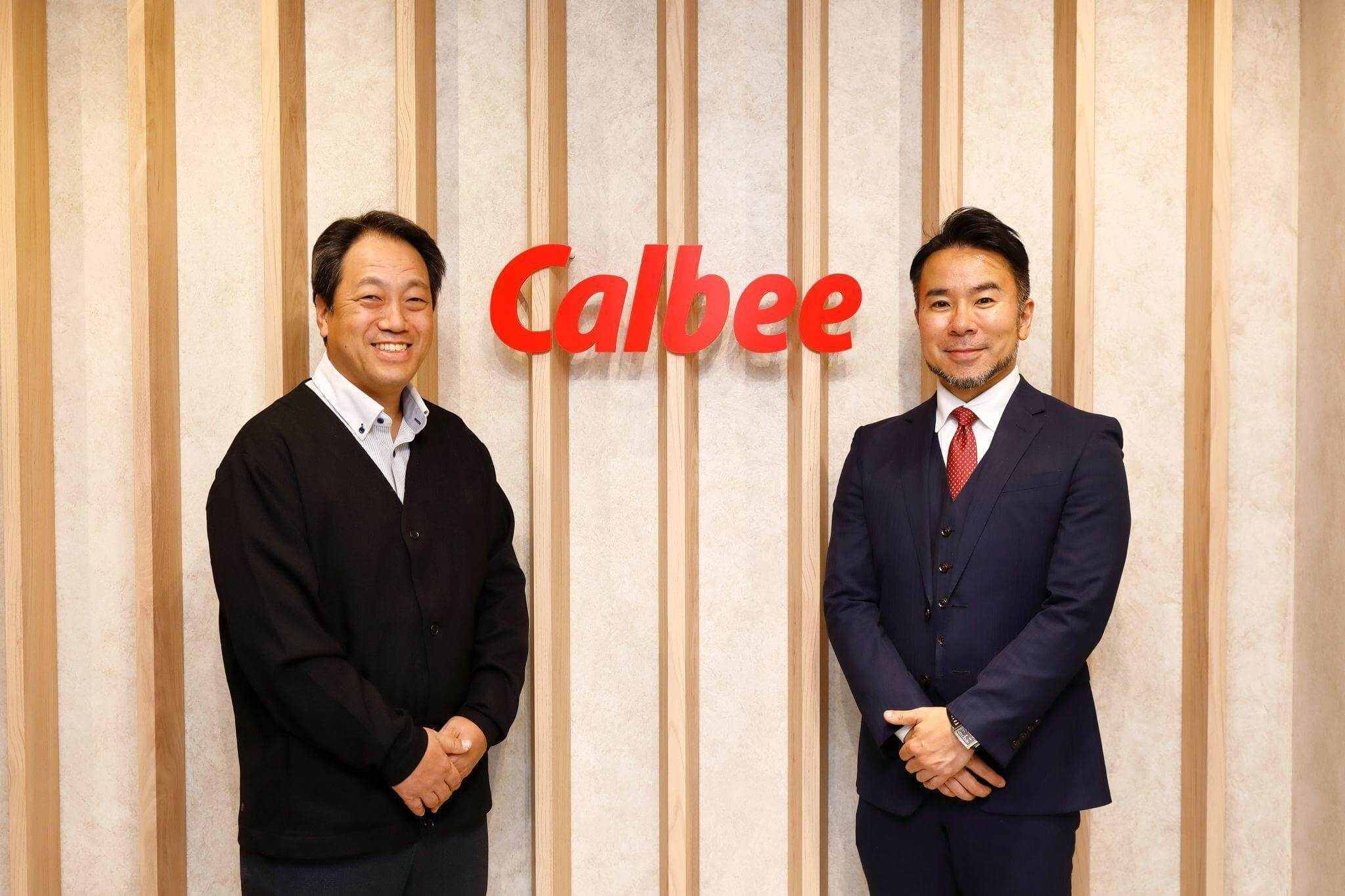
1992年、カルビー株式会社入社。一貫して生産畑を歩む。各務原工場長、西日本生産部長を経て、2023年から現職。2019年からは、新工場建設プロジェクト担当と工場DX担当を兼務。
2002年、明治大学大学院理工学研究科修了後、株式会社インクス入社。自動車部品製造、金属加工業向けの3D CAD/CAMシステム、自律型エージェントシステムの開発などに従事。2009年にコアコンセプト・テクノロジーの設立メンバーとして参画し、3D CAD/CAM/CAEシステム開発、IoT/AIプラットフォーム「Orizuru(オリヅル)」の企画・開発などDXに関する幅広い開発業務を牽引。2014年より理化学研究所客員研究員を兼務し、有機ELデバイスの製造システムの開発及び金属加工のIoTを研究。2015年に取締役CTOに就任後はモノづくり系ITエンジニアとして先端システムの企画・開発に従事しながら、データでマーケティング&営業活動する組織・環境構築を推進。
中期経営計画でDXによる生産性向上を公表
田口氏(以下、敬称略) 御社は国内において「ポテトチップス」や「じゃがりこ」などのスナック菓子で圧倒的な存在感を示し、シリアル商品でもトップシェアを誇っています。まさに日本を代表する食品メーカーといえますが、溝口様はどのようなキャリアを歩んでこられたのでしょうか。
溝口氏(以下、敬称略) 1992年に入社以降、オペレーターから始まり工場のプラント立ち上げやライン管理、工場長など生産畑に従事し続けてきました。現在は西日本における事業を管掌するとともに、2025年3月期に控える「せとうち広島工場」の設計に携わり、生産部門の代表としてDX推進委員会にも参加しています。
田口 御社がDXを意識するようになったのはいつからですか。
溝口 遡ること4年前、2019年5月に発表した中期経営計画の中で、今後の経営基盤強化策の1つとしてDX推進による生産性向上を掲げたのがきっかけです。
田口 当時は、DXの言葉自体は現在ほど世間に浸透していなかったと思います。はやめに注目した印象を受けます。
溝口 グローバルで事業を展開していることが大きかったと思います。GAFAの存在感が高まる中、日本国内の企業だけではなく外資系企業が競合になる可能性もあり、ポテトチップスが簡単に作れる電化製品が生まれるかもしれません。そういった危機感がカルビーの強みについて今一度振り返るきっかけとなり、DXの推進へつながっていきました。
田口 DXの推進体制はどのように作られたのでしょうか。
溝口 生産や営業、物流、マーケティング、開発、原材料調達など、各部門からなるDX推進委員会を組成し、私は生産部門の担当になりました。ただ、当時はDXの言葉自体よくわかっておらず、なんぞやを理解することから始める必要がありました。そこで、参加メンバーは外資系企業などに飛び込んで、世界のトレンドを学ぶことからスタートしました。
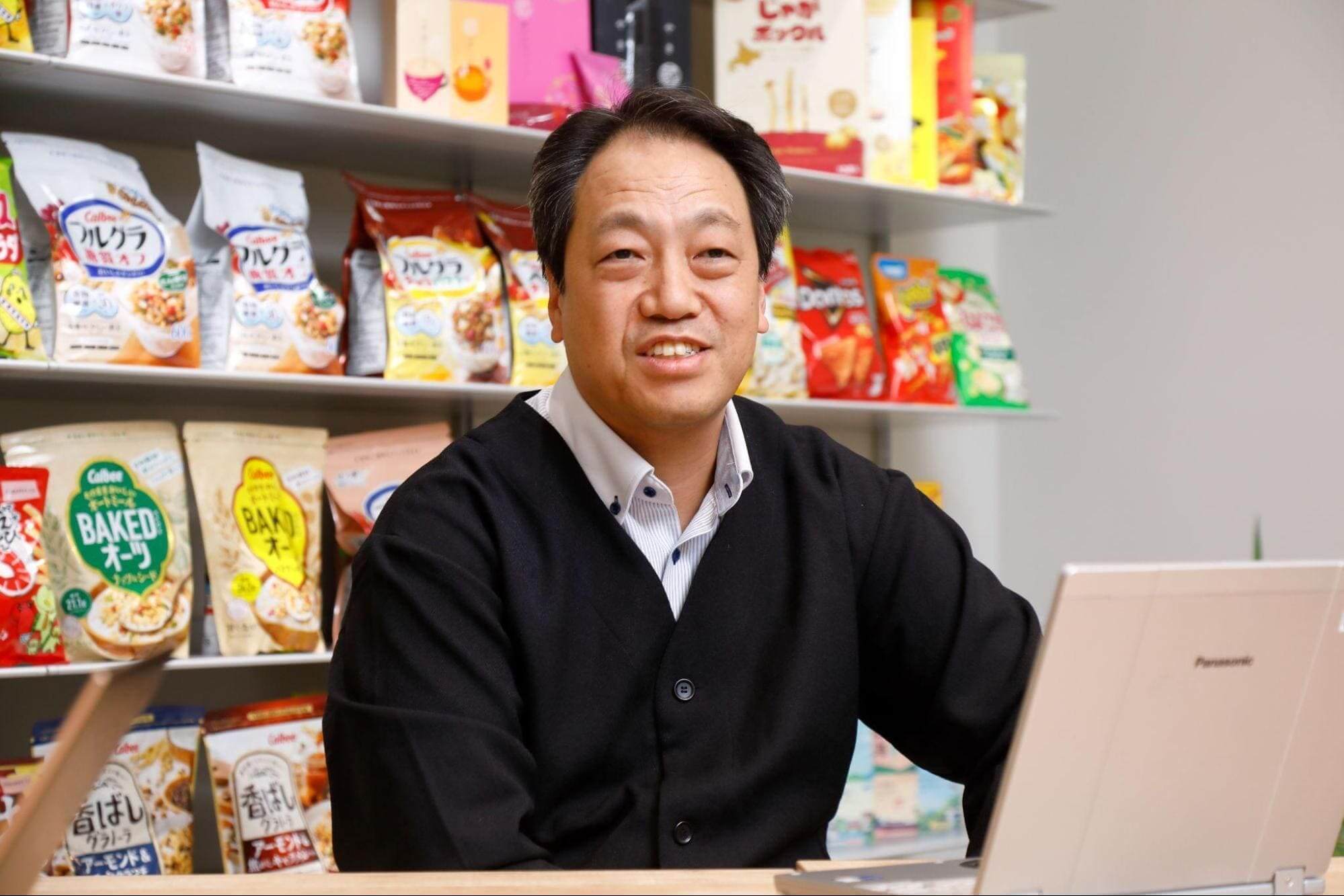
田口 記憶に残っているDXの事例はありますか。
溝口 佐賀市が自治体としてDXを推進しており、ドローンを使った農産物の薬剤散布、無人販売所の開設などの取り組みを見学しました。それまでDXは遠い世界でしたが、カルビーの中でも何かできるのではないかと身近に捉えることができたのは収穫です。まだ形にはなっていませんが、過去のデータを蓄積することで天候に左右されず育てやすい、収益性の高い品種がわかるかもしれません。
田口 ジャガイモの収穫量と御社の売上には相関関係があるでしょうし、すでに収穫量や農家の人手は足りていない状況だと思います。DXで解決できることはいくつもあるはずですが、例えば原料のジャガイモが足りないのであれば価値が高いところに寄せていくことになるでしょうし、何の価値が高いか判断するためにデジタル技術が活きてくるでしょう。
溝口 グループ会社のカルビーポテトでは、作物や収穫物の遠隔監視などのデジタル化を進めています。最終的には畑からお客様までをすべて追跡できる仕組みを構築したいと構想しており、当社が取り組むことで菓子業界にDXが広がる契機になってくれたらと願っています。
滋賀県・湖南工場では手作業をデジタル化
田口 2019年から始まったDX推進ですが、これまでの成果をお聞かせください。
溝口 滋賀県・湖南工場においてIoT技術を活用した事例をご紹介します。同工場は西日本最大級の生産力を持つ製造拠点であり「つながる工場」をテーマに、機器・設備をネットワークでつなぐなど、DXのモデル工場としても稼働させてきました。
私自身もプラント管理に携わるなど縁のある場所です。また、管掌エリアでもあることから同工場を舞台に2020年7月よりDX推進に着手し、2022年1月にトレーサビリティシステムを導入、2022年7月までに製造ラインの検査測定や生産計画なども自動化しました。
田口 トレーサビリティシステムを導入した経緯は、どのようなものだったのでしょうか。
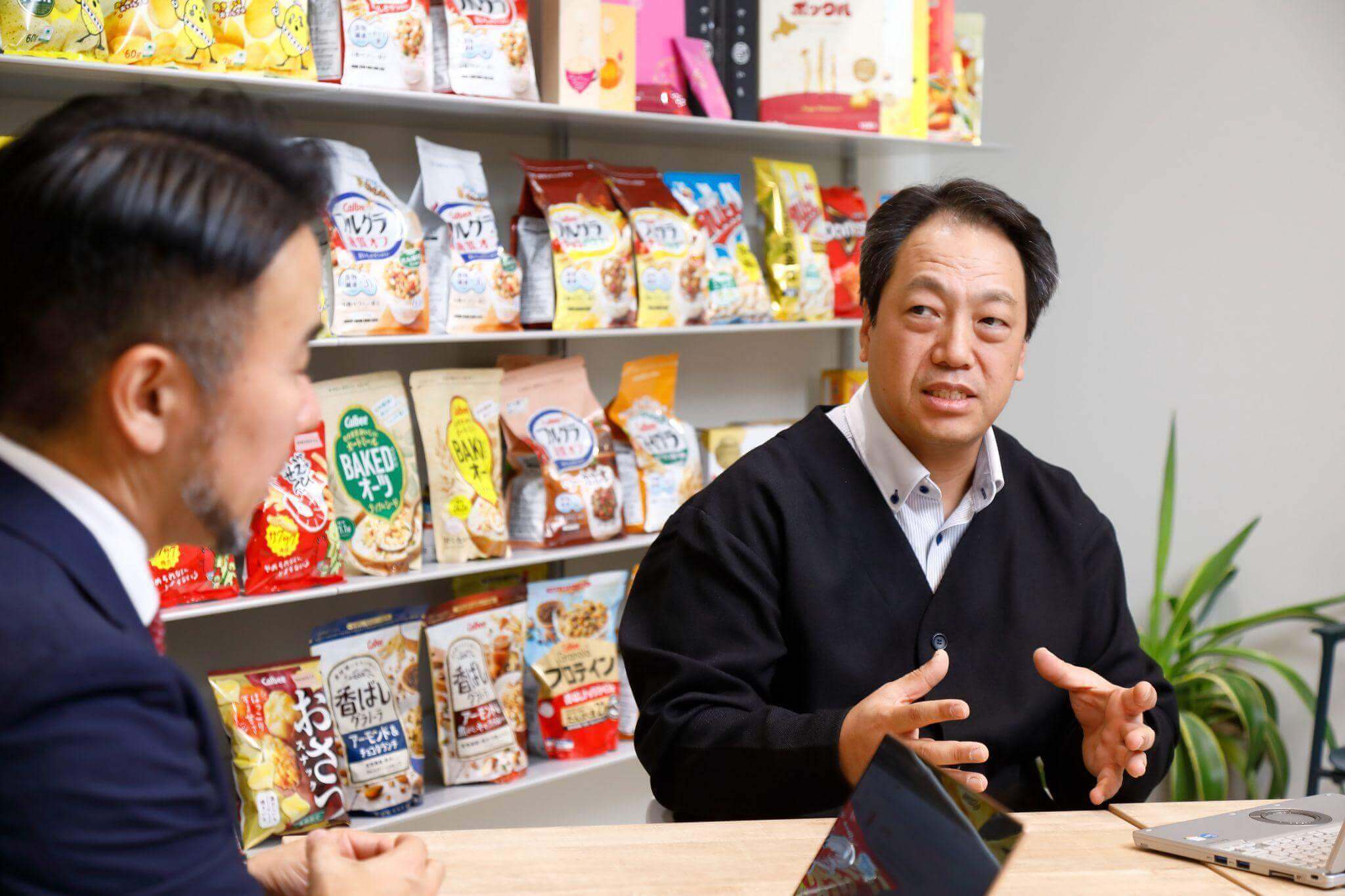
溝口 私はある程度電気の知識があり、比較的設備が新しい湖南工場ならシステムを導入しやすいと考えていました。ところが収集するデータ量があまりにも膨大で簡単にはいかないことがわかり、まずは製造ラインの一部である計量~箱詰工程部分を最新設備に更新しました。
品質管理においては、設備に何を監視・管理するか記録するQC工程表があり、デジタルに置き換えるとどこにどのデータがあると監視できるのかという観点で、DX向けに置き換える作業を中心にシステム化を進めました。
その結果、従来のシステムでは使用原料・製造工場・製造ライン・製造時間をもとにトレースしていたのを、製造工程内に複数の監視機器を入れ前後工程のデータと紐づけることで、1袋を単位として情報を一元管理できるようになりました。情報を蓄積することで各工程における作業状況を可視化でき、製品の状態把握や品質向上にもつながります。情報の照会スピードが上がることから、お客様の問い合わせにも迅速に対応できるようになります。
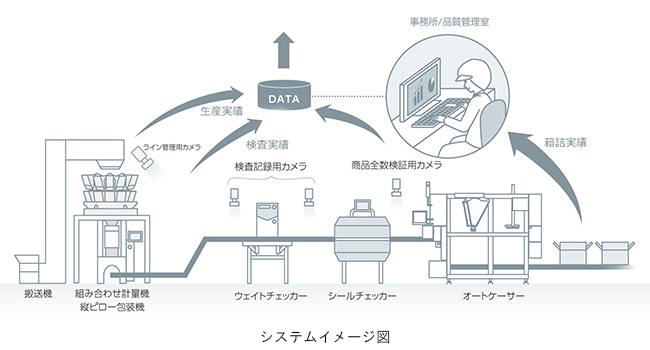
ライン上の製品流量調整も行いました。例えば1袋60グラムの製品を作るとしたら、従来であればオペレーターが製品量を目視し手作業で微調整していました。また、梱包後に規定の重さではないものや製品のシール部分に菓子が嚙み込んだ不良品などを排除していましたが、これらは従業員のヒアリングやカメラの映像チェックなどをもとにした対策です。
今回のDXでは、センサーを活用して機器にアラート機能を追加し、自動制御の可能性を検証しながら省力化につなげていきました。油分・水分・色味の検査測定も同様に、従来は定期的に製造ラインから商品サンプルを取得し手作業で実施していましたが、毎秒自動でデータを取得し規格外は自動排出することにより、省力化・検査精度の向上を実現しています。
田口 計量はともかく、その他においては画像が必要なのでデータ量が多くなり、設備にもコストがかかるということですね。これを当初は溝口さんご自身で取り組もうとしたのですか。
溝口 設備ベンダー側も今までは情報を囲い込んでいたのですが、我々もオープンにするので皆さんもいかがでしょうかと提案し、お互いに開示する流れで進めていきました。最初に入れ替えたラインにも4社ほど関わっていましたが、そのような方向性で開発を進めた形です。ベンダー側もそこまでしないと次のステージに進めないという危機感を持っていたこともあり、DX推進が始まった当初から協業関係はうまくいったと思います。
田口 設備メーカーが保有データを開示すること自体が特別です。どのように理解を得たのですか。
溝口 当社は、原料からお客様の手にお届けするまでを一貫させた垂直統合型の管理体制を敷いています。こうした考えがある中、当社にトレーサビリティが不可欠だということに共感いただきました。また、我々とのプロジェクトで成し遂げたことは、事前に一言いただければ他の企業に提供して構いませんとも持ちかけました。
田口 それは大きいと思います。通常であればクライアント企業が知財を含め権利として買い取るケースが多く、そうではない契約形態だったということですね。DXが広がる文化・素地はあっても、企業間の取り決めでできないことはたくさんあり、そういった慣習を超えた取り組みとしても興味深い点です。
自社が主導する形でDXを実現
田口 湖南工場のDX推進はスムーズに進んだのでしょうか。
溝口 紆余曲折がありました。2019年にDXに注力することが決まった時点で、ITベンダーがコンサルティングに入り、方向性や具体的な施策を模索しましたが、1年かけてもあまり前進しなかったのです。我々が困っていることや、何を成し遂げるとイノベーションが起きるのかということが、説明してもうまく伝わらなかったのが大きな原因です。しばらくするとコロナ禍に入り、密なコミュニケーションが取れなくなったことも原因の1つだと思います。結局、コンサルティング契約は終了しました。
当社側にも問題はありました。コンサルティングの世界では英語三文字の略語が多く、言葉の意味を理解するのが大変で、苦手意識を持つメンバーもいたと思います。その言葉を使いメンバー間で会話を始めたのはコンサルティングが入ってからおよそ1年経ってからのことで、もっと知りたい、自分たちで学習しようという考えにシフトできたのも、その頃からです。
湖南工場でDXを進める際も別のコンサルティング会社に1年ほど入っていただきましたが、うまくいきませんでした。コンサルティング会社のスタッフが常駐するほどの力の入れようでしたが、やはり当社の思いが伝わり切らなかったのが理由です。
田口 この時は何が問題だったのでしょうか。
溝口 我々は、ある情報を集めるためにそもそもの目的を提示することから始めるのですが、数日たつと見ている方向に違いが生じたり、本意ではない部分で高額なコストを提示されるなど、かなりのズレを感じました。
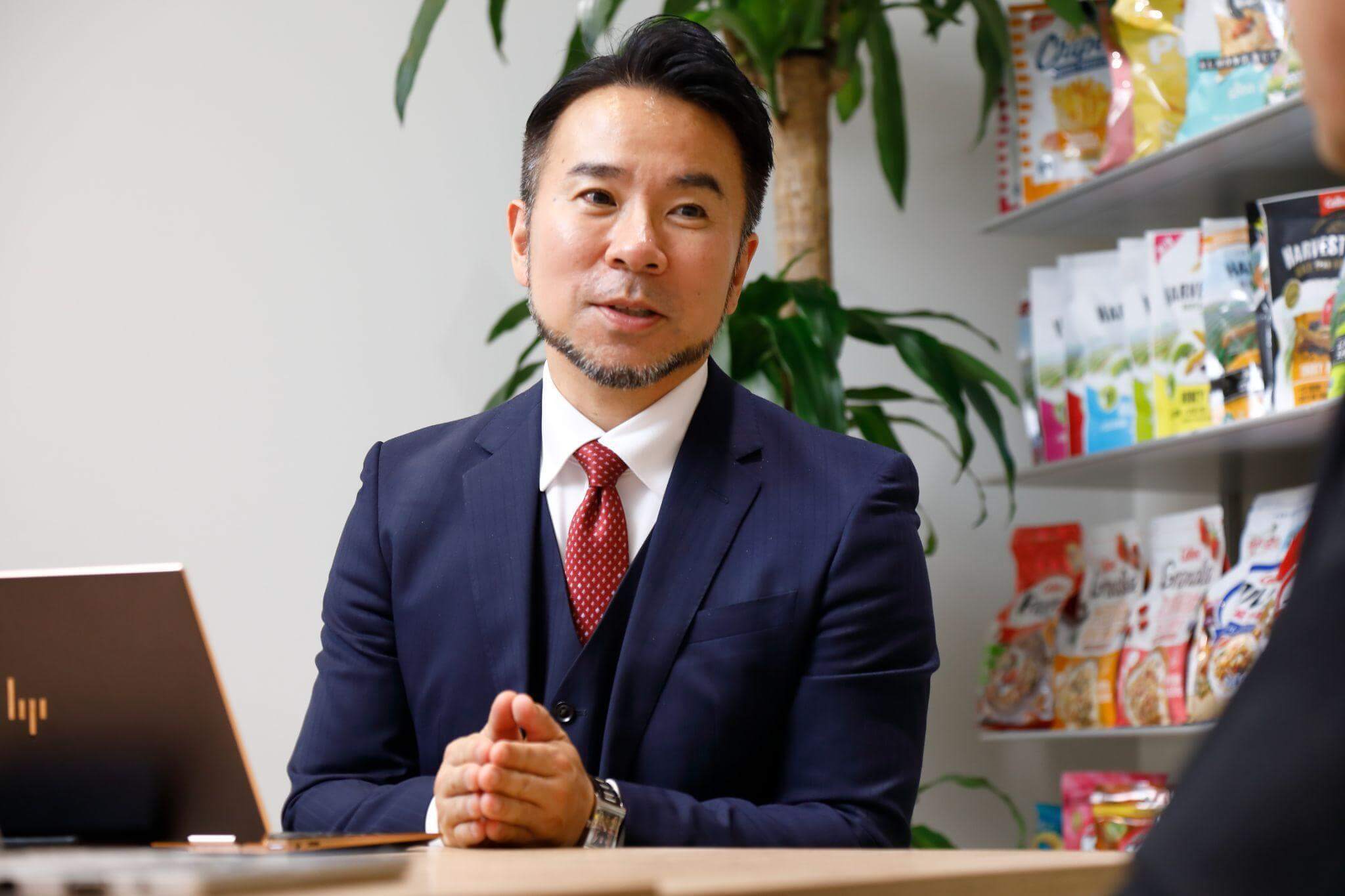
田口 DXが成功する要因の1つは、オーナーシップを持つことであり、その有無により成功に向かうスピード感は全く異なります。ベンダーに一部分を任せるのは構いませんが、オーナーシップまで失うと相手が何をしているのか判断できず、プロジェクトは頓挫しがちです。そうならなかったのは、御社に明確な目的意識があったからでしょう。
溝口 ただし、悪いことばかりではありません。コンサルティングを受けることで社内に知見がたまり、最終的にはベンチャー企業と手を組み、工場内のDXメンバーが主導する形でプロジェクトを進めることができました。
一方、時期が時期だったので設備機器の納品まで時間がかかり、シーケンサー1つにしても本来なら1ヵ月で届くところが1年かかるなど、時間を要したのは想定外のことでした。できることから先に進め、ようやく形になったのが2022年の7月ということです。ちなみに、プロジェクトの進め方はコンサルティング会社から教えていただいた手法を参考にしたので、ここまでの紆余曲折は決して無駄にはならなかったと思っています。
これまでは、高額な費用をかけて新しいプラントを立ち上げても数年たてば陳腐化し、アレンジするのに再び高額な投資が必要になることも課題でした。しかし今回は、ほぼ自分たちの力で作りあげたことで低コストに収まり、修正にもそれほど費用はかかりませんでした。ベンチャー企業に入ってもらったものの、システム自体はノーコードで開発できるので社内で対応ができます。
DXの推進に従業員の年齢は関係ない
田口 御社ではDX担当者が自ら学び、Slerが対応するような仕組みの部分も自ら構築されました。実際、我々も内製化の支援はよくしており、ITエンジニアが足りないと言われる中で効果的な進め方だと思います。一方、ここまでたどり着けた要因についてはどうお考えですか。
溝口 私が入社した頃は、毎月2時間ほどかけて製品の棚卸しをしていた時代でした。ITFコードを読み取ればすぐできると提案したところで、1台200万円もするバーコードリーダーの導入は却下され続けるわけです。これに限らず、IT系の取り組みがなかなか進まない中20年以上が過ぎ、ようやくDXの御旗のもとできるようになったことは、非常に大きいと思います。
田口 経営層の理解がDXの取り組みと無関係ではないのは言うまでもありません。
溝口 これまで温め続けていたことができるようになったのは、モチベーションになっています。
田口 一連の取り組みについてお聞きしましたが、その効果や今後の展開についてはどうお考えですか。
溝口 省力化になっていることは事実ですが、現在はあくまで製造ラインの一部にしかすぎません。今後1年ほどかけて包装の前後工程でもDXを進めていきます。最終的に人が介在しなくても済むようにするにはすべてをシステムでつなげる必要があり、せとうち広島工場ではこれを形にしたうえで、労働生産性(従業員一人あたり)の約6割向上を実現したい考えです。
さらにその後は、せとうち広島工場のように新設するものをグループ1、湖南工場のように今の状態から進化させるものをグループ2、手つかずの工場をグループ3に分類したうえで、グループ3を1もしくは2のどちらにするかグルーピングを行い、長期的に計画を進める方針です。
当社の工場は高温の油を使うので職場内が暑く、需要に応じて休日出勤や24時間操業もあります。こういった課題に対してDXを通じて遠隔で仕事ができる、夜間は無人で生産できるような工場を作るのが今後の目標であり、同時に従業員からもカルビーの工場で働いてよかったと思ってもらえるようにしたいと考えています。
田口 製造業では、電気をはじめ多くのエネルギーを消費します。DXでできることは多いと思いますが、何か取り組まれていますか。
溝口 エネルギーの消費に関しては、一部工場で太陽光発電を導入しています。DXの観点では、燃料を効率利用し、低コスト化と温室効果ガス排出量の削減に努めたいところです。まだ知見がなく実践できていませんが、データ収集を通じて環境改善に役立てたいと考えています。
田口 内製化も含め、DXをうまく進められたポイントについてはどうお考えですか。
溝口 大手のコンサルティング会社からベンチャー企業に切り替えるなど、スピーディーに決断を行ってきたことが今に活きていると思います。もし、あのままズルズルと続けていたら、今どうなっていたかわかりません。同じような課題意識を持つメンバーと協力し合うことも、うまく進めるポイントだと思います。
田口 最後に、Koto Onlineの読者にメッセージをお願いいたします。
溝口 入社から30年余り経ってDXの時代が到来し、過去に諦めていたことができるようになりました。こういった話を定年間近の方にすると非常に盛り上がるので、DXを進める上で年齢は関係ないと感じています。実際に工場では、50~60代のDX推進メンバーも活躍しています。年齢・性別に関係なく、皆さんと一緒にこれからもチャレンジを続けていきたいですね。幅広い人財が参加することで全社的な取り組みにも発展しやすいのではないかと思います。
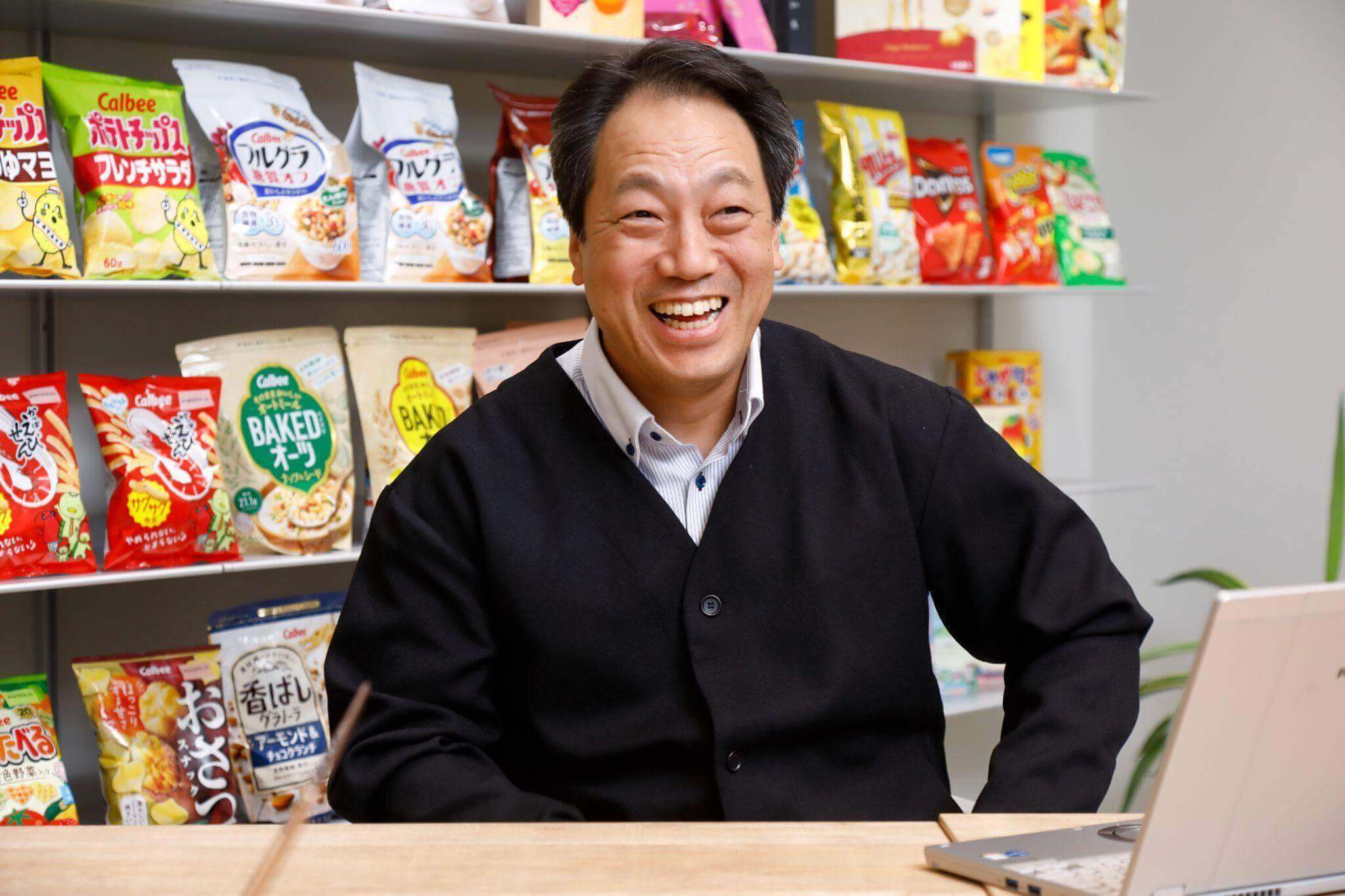
田口 DX推進は30代の方がメインと想像していましたが、実情はまったく異なるのですね。驚きました。労働力不足が加速する中、55歳が定年と言っているSlerもいますが、活躍できるフィールドがあるということは、非常に素晴らしいことだと思います。本日は貴重なお話をありがとうございました。
【関連リンク】
カルビー株式会社 https://www.calbee.co.jp/
株式会社コアコンセプト・テクノロジー https://www.cct-inc.co.jp/
【こんな記事も読まれています】
・【会員限定動画】サプライウェブで実現するマスカスタマイゼーション時代の企業戦略
・製造業における購買・調達業務とは?課題の解決方法も紹介
・ビジネスや技術のトレンドに反応しながら進化を続けるCRMの事例を紹介