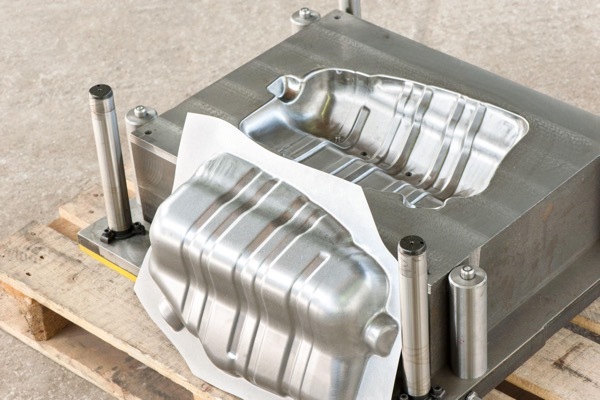
慢性的な技術者不足に悩む金型業界ではAIの活用に注目が集まっています。
この記事では、金型業界の抱える課題やAIを導入するメリット、成功のポイントについて解説します。
金型業界が抱える課題
金型業界では、下記のような課題を抱えています。
・金型業界の国内生産額の減少
・金型製作の量産化のハードルが高い
それぞれの課題はどのようなものなのか、詳しく確認していきましょう。
金型業界の国内生産額の減少
かつて日本の金型産業は世界一の生産額を誇り、日本は「金型大国」と呼ばれるほどでした。2006年は、年間で1.8兆円の生産額がありました。
現在は、組み立てメーカー(アセンブリー・メーカー)が海外移転したことから国内需要が減少し、海外企業の台頭したことなどが原因となって、金型の生産額はピーク時の8割ほどの1.4兆円まで減少しています。
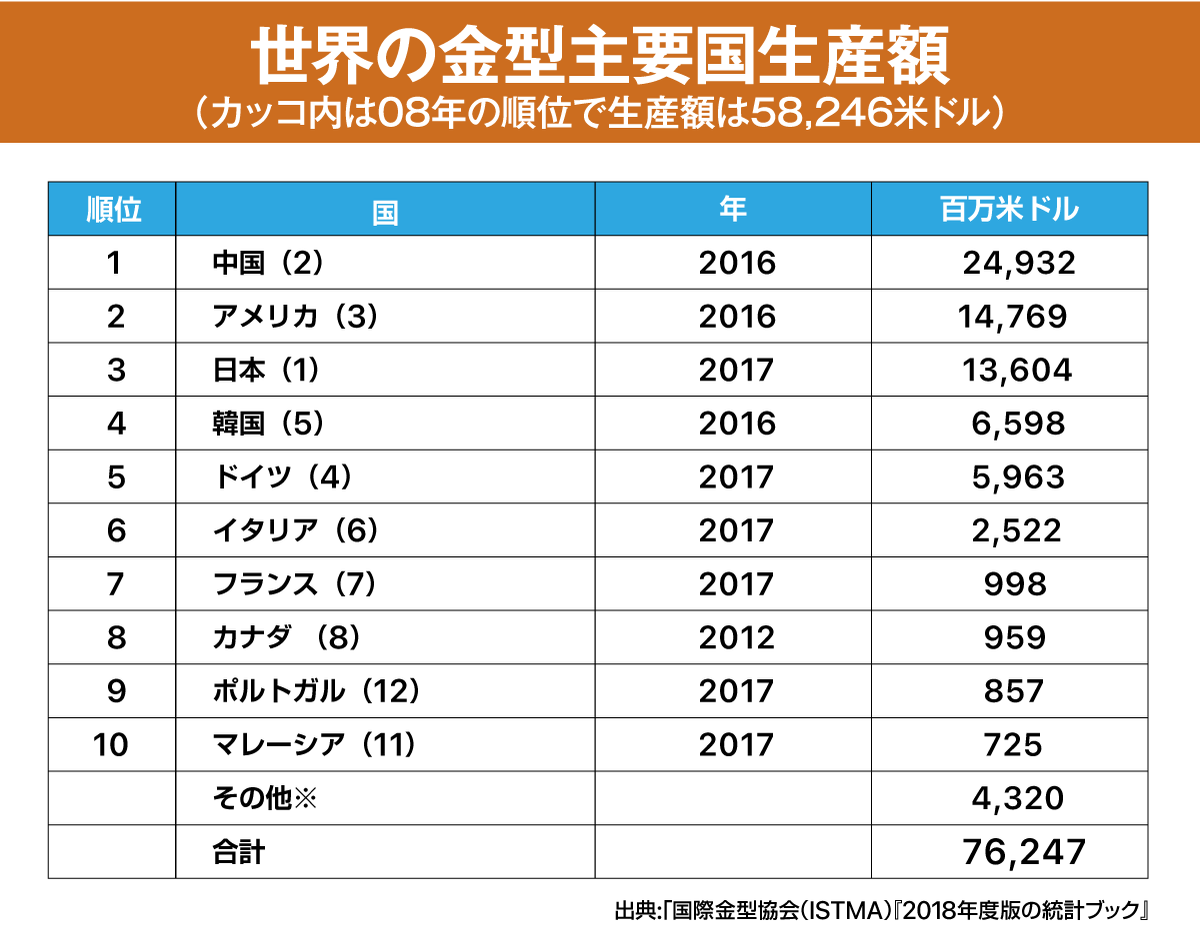
国際金型協会(ISTMA)発表の「2018年度版の統計ブック」によると、2016年頃の世界の金型生産額は760億ドルで、1位は中国の249億ドル、2位はアメリカの147億ドルでした。日本は136億ドルで、生産額3位まで順位を落としています。
世界一の座を失っただけでなく、事業所数や従業員数なども大幅に減少しているという現状もあります。
金型製作の量産化のハードルが高い
金型は、製品の大量生産のために必要不可欠です。そして、金型の品質は製品の良否を決定づけます。ドイツでは、金型を「生産工学の王」と呼ぶほどです。
金型は個別設計・個別製作であり、製作には専門知識や熟練度が必要です。したがって、量産品の製作とは異なり、製作の自動化や効率化が難しいとされています。
金型業界ですすむIoT化
金型の製造は自動化や効率化が難しいとされてきましたが、現在、金型業界では深刻な人材不足などの課題を解決する手段として、IoT化が進められています。
一例を挙げると、マシニングセンタ(切削加工を1台でできる工作機械)や放電加工機といった生産設備のIoT化があります。生産設備の機械情報を自動で取得し、クラウドサーバーを通じて運転状況や稼働率などを遠隔で分析・監視できるようなシステムやサービスが登場しています。
生産設備のIoT化は、機械情報を数値化して把握することを可能にし、機械の効率性や品質の向上につながると期待されています。効率良く品質の良いモノを製作するには、こうしたIoTに関連した技術を活用していくことが急務になるでしょう。
IoTとAIを組み合わせて効率化も可能
IoTとAIを組み合わせることは、生産機械の機械情報の取得により、機械の効率性や品質の向上が望めるほか、メンテナンスの効率化にも活用が期待されています。
金型産業に限らず、どの業種の工場でも生産性向上のポイントになるのが「いかに生産ラインを止めることなく稼働させ続けるか」ということです。生産ラインのチョコ停(ちょっとした停止)は、装置の動作不良や装置間連携不良などの複合的な要因で起こるため、事前の対処は難しいものでした。
しかし、金型がIoT化されていれば、センサーなどから損傷状態などのメンテナンスに必要な情報を自動で収集できます。AIでその情報を分析して、過去の発生事例を参照しながら「どの部品が、いつ故障する可能性が高いか」という予測をもとにしたメンテナンス計画が立てられます。
このように、IoTとAIを組み合わせて活用することは、予知保全に役立つのです。
金型業界にAIを導入する5つのメリット
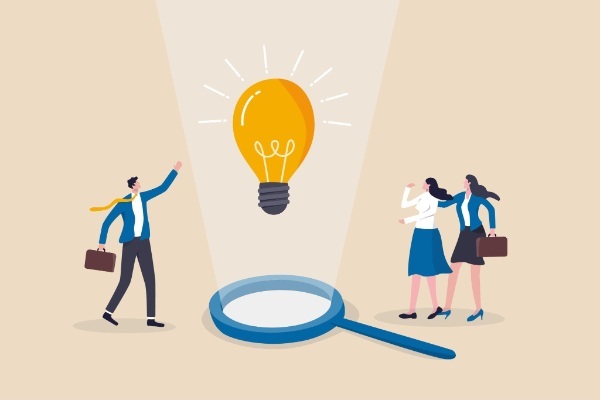
金型業界にAIを導入することで、現在の金型業界が抱える課題の解決につながるさまざまなメリットがあります。
1. 人手不足の解消
AIを導入すれば、今までヒューマンパワーに頼っていた業務を自動化・効率化することが可能です。AIによって業務に余裕ができれば、人的資源を付加価値の高い業務や企業競争力を生み出す施策に投じることが可能になり、企業の生産性向上が期待できます。
2. 機械設備の故障予知や異常検知が可能
機械の故障や異常は、劣化や摩耗だけでなく複合的な要因で起こるため、事前の対処が難しいものです。しかし、先ほど紹介したIoTとAIを組み合わせた予知保全システムなどを活用すれば、予知保全ができるでしょう。
AIは、高速計算と膨大なデータ処理を得意としています。おびただしいデータを短い時間で処理し、精度の高い分析を行うことが可能です。また、人の脳と同じく、学習を重ねることでより分析の精度が高まります。
AIを用いることで、機械情報から目視でわかりにくい劣化状態や内部の動作状況なども把握でき、未然に設備トラブルを防ぐことができるでしょう。メンテナンス業務の負担軽減が期待できます。
3. 目視せず不良品検出が可能
AIにより画像解析技術などで不良品を検出できれば、検出を担当する従業員にかかるコストを圧縮し、さらにヒューマンエラーを防ぐことができます。
不良品の検出は、ベルトコンベアに流れている製品を従業員が目視で確認するのが一般的です。しかしながら、目視作業には従業員の採用や育成が不可欠であるため、相応の手間とコストがかかります。また、疲れや不注意などによってヒューマンエラーが起こり、不良品の確認漏れや見逃しが発生する可能性はゼロではありません。
そのため不良品の検出には、画像解析技術が用いられることが多く、近年のAIは、良品の画像データから学習機能により外観から不良品を検知するアルゴリズムを構築できるようになりました。その利便性と人件費の抑制効果、ヒューマンエラーの防止などのメリットから、多くの製造業で不良品検出にAIの導入が進んでいます。
AI分析でも誤差が生じる可能性はありますが、人よりも高い精度での不良品検出が期待できます。
4. 効率の良い最適な業務プロセスを実現
専門知識や熟練度を要する作業においてもAIを活用すれば、蓄積されたデータから最適な業務プロセスを導き出し、効率的に業務を遂行してくれるでしょう。
AIには、機械学習とディープラーニングの技術が用いられています。機械学習により、AIは膨大なデータの中から特定のルール・法則性を学習して出力の精度を上げます。そして、ディープラーニングにより人の手を借りずとも、自動で特徴や法則性を学習していくのです。
AIを活用すれば、特定の従業員の技能に依存していた業務を最適な方法で実行できるようになるでしょう。
5. 品質の向上と安定化が可能
ここまで解説したメリットにより、AIを導入をすれば、企業の業務は自動化・効率化し、企業の生産性や品質の向上が期待できます。
金型は製品の生産のために不可欠なものであるため、AIの導入により製品の品質が安定して高まることが企業の優位性となり、新たな販路開拓につながる可能性もあるでしょう。
金型業界でAIを導入するための3つのポイント
金型業界でAIの導入を検討する場合には、AIの導入そのものを目的としてしまわないように留意しましょう。AIの導入は、あくまで「課題解決のための手段」だと考えることが大切です。
1. 現状の課題を整理する
AIを導入する場合は、自社のどの業務にどのような課題があるのかを整理して、明確にすることが大切です。
そして、その課題を解決できるAIを導入しましょう。課題を整理するには、業務プロセスの見える化や現場へのヒアリングが有効です。
「周りがAIを導入しているから」「AIを導入しさえすれば、生産性が上がるだろう」など、課題を明確にしないままAIを導入してしまうと、AIを十分に活用できないまま持ち腐れになってしまったり、AIの導入が頓挫したりする可能性があります。
人手不足を補うためにAIを導入したいのか、生産性を向上させたいのか、抱えている課題は企業ごとに異なるでしょう。課題が異なれば、そのソリューションとして、どのようなAIが適切かどうかは違ってきます。
AIは優れた技術ですが、万能ではありません。そのため、課題を整理し、AIの導入によりその課題が解決できるかどうかを精査しておく必要があるのです。
2. 一度に広範囲で導入せず優先順位をつける
AIの導入は、優先順位をつけて小範囲から導入してみることをおすすめします。
AIの導入には、手間やコストがかかります。また、同業他社でAIが活用されているからといって、自社でも有効とは限りません。企業によって、業務プロセスはさまざまであるからです。
最初からすべての業務にAIを導入しようとすると、初期費用が嵩むだけでなく、急激な変化に現場が混乱して適切に運用できなかったり、自社の業務に合わなかった場合にAI導入費用が無駄になる可能性もあります。
そのため、課題の解決に優先順位をつけてAIを導入していきましょう。AIの導入効果を検証したのちに、ほかの業務にもAIを導入していくとよいでしょう。
3. PoCにより導入効果を検証する
AIは、PoCにより導入効果を検証できてから、導入を決めるようにしましょう。
PoC(Proof of Concept)とは、アイデアやコンセプトの実現可能性や得られる効果などを検証することです。
「本当にAIの導入により課題解決が実現できるのか」「AIの導入により効果が得られるのか」ということを、机上の議論で判断せず、試作のAIモデルをつくって実際に稼働させ、結果を評価します。
PoCにより、自動化・効率化したい業務に必要なデータが揃うかどうかや、十分な精度が得られるかどうかを検証したのちにAIを導入すれば、AIの導入に失敗する可能性は下がるでしょう。
金型業界でAIを導入した事例
金型業界で実際にAIを導入している企業は、どのようにAIを活用しているのでしょうか。
ここでは、金型業界でAIを導入した2社の事例をご紹介します。
オムロン株式会社
オムロン株式会社では、草津工場の金型加工工程と綾部工場の組み立て工程にIoT基盤「i-BELT」を導入しました。
草津工場ではAIで金型加工を自動制御し、技術者のノウハウをそれに活かして加工時間を40%削減し、工具の摩耗量を20%削減しました。また、綾部工場ではチョコ停の予兆把握と計画保全により、チョコ停による停止時間を月に45時間削減することに成功しました。
また、制御機器やセンサーなどの入力機器からデータをAIコントローラーで収集し、熟練工が感覚として設定していた加工条件の見える化を行い、AI分析で得た知見から制御アルゴリズムを生成し、それをAIコントローラーにフィードバックしました。
一方、綾部工場では、不定期にチョコ停が散発して生産効率が落ちていたため、ロボットにセンサーを設置して常時監視を行い、不具合が発生する予兆を把握することで、不定期のチョコ停が起きないよう計画保全をすることが可能になりました。
株式会社IBUKI
株式会社IBUKIでは、技術者の知見や技術といった暗黙知をAI化し、過去情報が探索できるAIソリューション「ORGENIUS」を開発しました。そして、ORGENIUSにより技能継承の問題を解消しました。
具体的には、技術者の知見や技術などに関する情報をヒアリングや各種センサーから集めて分析し、ネットワーク図を作成して見える化します。そして、それをORGENIUSというAIソリューションにより、誰でも活用できるようにしたのです。
ORGENIUSの導入により、半日がかりだった業務が30分程度にまで短縮されるなど、大幅な業務効率化を実現しました。加えて、AIの学習機能によりさらにORGENIUSの精度を上げています。
金型業界でのAI導入事例は増えている
金型は個別設計・個別製作であり、製作には専門知識や熟練度を必要とするため、製作の自動化・効率化が難しいことが人手不足に拍車をかけています。
そのような金型業界の人手不足の課題解決として注目を集めているのが、AIの導入です。
AIは機械設備の故障予知や異常検知が可能です。また、機械学習やディープラーニングにより最適な業務プロセスを実現するほか、不良品検出などの業務を人よりも高い精度で実施できます。
企業の課題や業務プロセスに適したAIを導入することで、人的資源を付加価値の高い業務や企業競争力を生み出す施策に投じたり、企業の生産性向上や製品の品質向上・安定化につなげたりすることができるでしょう。
ただし、自社でAIを導入する場合はいきなり広範囲で導入せず、まずは現状の課題を整理し、特に課題の大きい業務に絞って導入するなど、慎重に検討していくことをおすすめします。
【こんな記事も読まれています】
・【会員限定動画】サプライウェブで実現するマスカスタマイゼーション時代の企業戦略
・製造業における購買・調達業務とは?課題の解決方法も紹介
・ビジネスや技術のトレンドに反応しながら進化を続けるCRMの事例を紹介