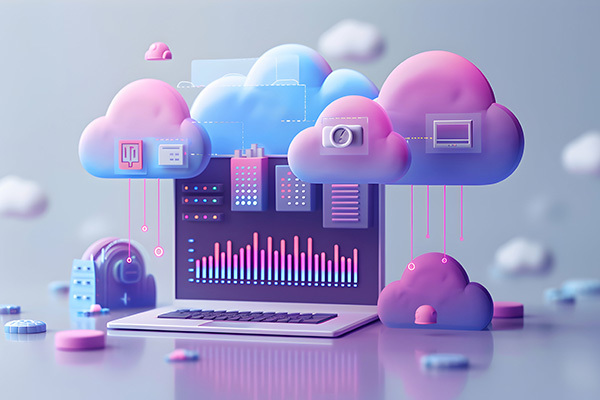
クラウドインテグレーションは、製造業のデジタル変革(DX)を推進する重要な基盤技術として注目を集めています。
従来のオンプレミス環境とは異なり、インターネットを通じて様々なリソースを連携させる技術であり、多くの企業で導入が進んでいるのが現状です。
製造業においてはコスト削減、データのリアルタイム活用による業務効率化など、多くのメリットがあるでしょう。
一方で、セキュリティリスクや既存システムとの連携の難しさなど、導入時には注意すべき点も存在します。
本記事では、製造業におけるクラウドインテグレーションの導入メリットや成功事例、導入手順、さらには今後の発展について詳しく解説していきます。
目次
クラウドインテグレーションとは?
クラウドインテグレーションとは、インターネットを通じて利用できるデータ保存、計算能力、アプリケーションサービスなどの一連のリソースを連携させる技術です。
従来は社内に設置したサーバーやネットワーク機器(オンプレミス環境)で管理していたシステムを、インターネット上のサービスとして統合する仕組みといえるでしょう。
主な特徴として、必要に応じて容量を増減できるスケーラビリティ、柔軟性、コスト効率の良さ、アクセスのしやすさなどが挙げられます。
クラウドインテグレーションは、製造業のデジタル変革(DX)を推進する重要な基盤技術として、多くの企業で導入が進んでいます。
製造業におけるクラウドインテグレーション導入の3つのメリット
製造業におけるクラウドインテグレーションを導入するメリットには、以下の3つがあげられます。
- コスト削減と柔軟なリソース管理
- データのリアルタイム管理と業務効率化
- 製造拠点間のデータ連携とイノベーションの促進
順番に見ていきましょう。
メリット1:コスト削減と柔軟なリソース管理
製造業でクラウドインテグレーションを導入する最大のメリットは、大幅なコスト削減と柔軟なリソース管理です。
従来のオンプレミス環境では、サーバーやネットワーク機器の購入に数百万円以上の初期投資が必要でした。
一方、クラウドでは物理的な設備が不要で、月額・年額のサブスクリプション契約で利用できるため、初期コストを大きく抑えられます。
また「必要な分だけリソースを利用できる」という特徴があり、繁忙期には処理能力を増強し、閑散期には縮小することで無駄なコストを削減できるのです。
さらに、システムのアップデートやセキュリティパッチの適用をクラウドベンダーが担当するため、IT担当者の負担が軽減され、人的リソースを他の重要な業務に回せるという利点もあります。
製造業の経営者として、限られた予算で最大の効果を得たいという願いに、クラウドインテグレーションは確かな答えを提供してくれるでしょう。
メリット2:データのリアルタイム管理と業務効率化
クラウドインテグレーションの導入により、製造現場のデータをリアルタイムで管理・可視化できることが大きな強みです。
各製造プロセスから得られるデータをクラウド上でリアルタイムに集約し、いつでもどこでもアクセス可能になります。生産ラインの稼働状況や在庫状況をリアルタイムで確認できるため、設備の稼働効率が向上し、予知保全も容易になります。
また、各業務システムがリアルタイムでデータを連携できるため、最新の情報を基に迅速な意思決定が可能になるのです。例えば、販売管理システムと会計システムをクラウドで統合すれば、売上データが自動的に会計システムへ反映され、手作業による入力ミスが減少します。
さらに、インターネット環境さえあれば、どこからでも業務システムにアクセス可能になるため、リモートワークやフレックス勤務がしやすくなり、社員の働きやすさも向上するでしょう。
メリット3:製造拠点間のデータ連携とイノベーションの促進
クラウドインテグレーションにより、異なる製造拠点やプロセス間でのデータ連携が容易になり、製造ラインの統一管理と全体最適化が実現します。
複数の工場や取引先とのデータ共有がスムーズになり、権限を持ったユーザーであればどこでも情報にアクセスできるようになります。
国際的な製造企業では、世界中の様々な拠点がリアルタイムでデータを共有し、統一された意思決定を行うことが可能になるのです。
また、クラウドの柔軟性を活かして、AIやIoTなどの新しい技術と組み合わせることで、さらなる業務改善やイノベーションを促進できます。例えば、AIや機械学習などの先進技術をクラウドを通じて利用することで、生産プロセスの最適化や品質管理の向上が図れるでしょう。
クラウドテクノロジーは製造業におけるイノベーションの加速器として機能し、新製品開発や業務改善の機会を広げ、市場での競争力強化につながります。
製造業におけるクラウドインテグレーション導入の成功事例3選
ここからは、クラウドインテグレーション導入の成功事例を3つ紹介していきます。
順番に解説していきます。
事例1:自動車メーカーによる次世代ものづくりプラットフォームの構築
ある大手自動車メーカーは、製造領域のデジタル変革を実現するため、「可用性・拡張性の確保」「製造現場データ活用」「運用効率化」を基本コンセプトとしたクラウドネイティブの技術を活用した次世代ものづくりプラットフォームを構築しました。
複数媒体で個別管理されていた製造現場のデータをクラウド上で集約管理することにより、データを効果的に活用できる環境を整備したのです。
サーバーレスアーキテクチャを採用したことで、自動的かつ柔軟なスケールアップに対応し、システムの拡張性を高めることに成功しました。
さらに、特定のアプリケーションやベンダーに依存しない運用体制を構築したことで、将来的な変更にも柔軟に対応できる汎用性の高い運用を実現しています。
製品軸でのデータ一元管理により、部門横断的な情報共有が可能となり、意思決定の迅速化にもつながっています。
このクラウド基盤の構築により、自動車業界の「100年に1度の大変革」と言われる電動化や新規参入企業との競争に柔軟に対応できる体制が整いました。
事例2:空調機器メーカーによる工場IoTプラットフォームの構築
ある大手空調機器メーカーは、グローバル展開の加速と製造コストの低価格化、製品差別化を図るため、製造現場データの一元化やリアルタイム分析を行う「工場IoTプラットフォーム」をクラウド上に構築しました。
大阪府内の新工場に導入されたこのプラットフォームでは、生産状態の見える化、生産計画の最適化、製造プロセスのロス低減などを実現しています。
特筆すべきは、デジタルツイン技術を活用し、部品の流れや組み立て、塗装、プレスなどの工程状況を仮想空間上に再現している点です。
このシステムにより、生産ラインの停止原因を事前に予測し、迅速に対応することが可能となりました。
製造設備や組立作業、ワークフローなどの状態を監視し、過去に発生した事象を詳細に分析することで、将来起こりうる問題を予測するシミュレーションも実現しています。
「工場IoTプロジェクトセンター」を設置したことで、メンバー間でのデータに基づいた迅速な意思決定が可能になり、生産管理の戦略性が向上しました。
事例3:電気機器メーカーによるバーチャル・ワンファクトリーの実現
ある電気機器メーカーは、複数の製造拠点を仮想的に1つの工場として統合する「バーチャル・ワンファクトリー」をクラウド技術を活用して実現しました。
具体的には、「部門間融合」「生産融合」「施策プロセス融合」「IT融合」の4つの面での融合を進め、各工場で異なっていた設計情報も共通化されました。
クラウド上で生産状況を見える化したことで、各工場の負荷状況や得意技能が明確になり、生産の繁閑に合わせた工場間での生産応援が可能となりました。
また、多品種少量生産に強い工場で試作を行うことで、試作の効率化とスピードアップ、量産工程へのフィードバックも容易になり、製品開発後の垂直立ち上げが実現しています。
その結果、生産量は維持しつつ生産効率を上げることに成功し、コスト削減だけでなく、工場間の人材や技術の交流も活発化しました。
さらに、工場間で負荷を分散することにより、人手不足や外部環境の変化にも柔軟に対応できる体制構築に成功しています。
製造業でクラウドインテグレーションを導入する手順9ステップ
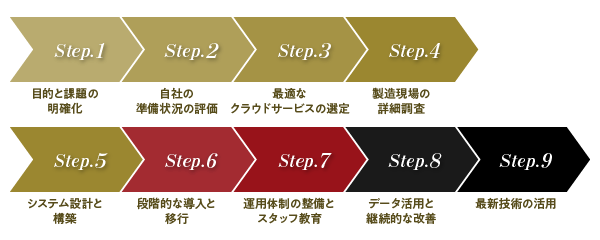
製造業でクラウドインテグレーションを導入する手順は、以下の9ステップです。
1.目的と課題の明確化
2.自社の準備状況の評価
3.最適なクラウドサービスの選定
4.製造現場の詳細調査
5.システム設計と構築
6.段階的な導入と移行
7.運用体制の整備とスタッフ教育
8.データ活用と継続的な改善
9.最新技術の活用
順番に見ていきましょう。
ステップ1:目的と課題の明確化
クラウドインテグレーション導入の第一歩は、自社の課題と導入目的を明確にすることから始まります。
漠然と「デジタル化したい」という思いだけでは、適切なシステム選択が難しく、導入後の成果も感じにくくなってしまいます。
まずは現在の工程管理や生産体制を詳細に分析し、「生産性向上」「コスト削減」「品質管理の強化」など、具体的な目標を設定しましょう。
製造現場の実態に即した目標設定が、後の工程をスムーズに進める鍵となります。目標は経営戦略と連動させ、数値化できるものにすると効果測定がしやすくなるでしょう。
最初は欲張らず、優先度の高い課題に焦点を当てることで、失敗リスクを低減できます。
ステップ2:自社の準備状況の評価
クラウドインテグレーションを成功させるには、自社のデジタル基盤や組織体制の準備状況を正確に評価することが重要です。
技術面では、現在の設備やシステムがクラウド環境と連携できるか、データ取得の仕組みは整っているかなどを確認します。
人材面では、システム導入を推進するチームの編成や、現場スタッフのITリテラシーレベルを把握しておく必要があります。
予算面では、初期投資だけでなく、運用コストや教育コストまで含めた総合的な計画を立てることが大切です。
準備不足のまま導入を進めると、予期せぬ技術的な問題に直面し、プロジェクト全体に悪影響を及ぼす可能性があります。自社だけでの評価が難しい場合は、専門家のアドバイスを求めることも検討しましょう。
ステップ3:最適なクラウドサービスの選定
自社の目的と準備状況を踏まえ、最適なクラウドサービスを選定します。
パブリッククラウド、プライベートクラウド、ハイブリッドクラウドなど、様々な形態があり、それぞれ特性が異なります。パブリッククラウドは初期コストが低く導入が容易である一方、プライベートクラウドはセキュリティ面で優れているといった特徴があります。
製造業向けに特化したクラウドサービスも増えているため、同業他社の導入事例も参考にすると良いでしょう。サービス選定時には、自社の既存システムとの連携のしやすさや、将来的な拡張性も重要な判断基準となります。
サプライヤーの製造業に対する理解度や、過去の導入実績も確認しておくと安心です。
ステップ4:製造現場の詳細調査
クラウドシステムを製造現場に適用するためには、現場の詳細な調査が欠かせません。
機械設備のデータ取得方法、作業者の動線、現在の管理手法など、現場の実態を細かく把握します。特に重要なのは、既存の機械設備からどのようにデータを収集し、クラウドシステムに転送するかという点です。
古い設備の場合、データ取得のためのセンサーや通信機器の追加が必要になることもあります。
また、手作業で行われている工程のデータ入力方法についても検討が必要です。現場調査の結果は、システム設計の基礎情報となるため、できるだけ詳細に記録しておきましょう。
ステップ5:システム設計と構築
調査結果をもとに、クラウドインテグレーションシステムの具体的な設計と構築を行います。
ネットワーク構成図を作成し、システム全体の構造と機能を明確にします。必要なリソース(サーバー、ストレージ、ネットワーク等)を特定し、適切な規模で準備します。セキュリティ設計も重要で、データの暗号化やアクセス制御の設定を慎重に行います。
製造業特有の要件に合わせたカスタマイズが必要な場合は、サプライヤーと綿密に協議しましょう。設計段階では将来の拡張性も考慮し、新たな機能や設備の追加にも対応できる柔軟な構造を目指します。
ステップ6:段階的な導入と移行
クラウドインテグレーションは、一度に全社導入するのではなく、段階的に進めることが成功の鍵です。
まずは特定の部署や工程から導入を始め、効果検証をしながら範囲を広げていく方法が推奨されています。
例えば、社内の工程管理から始めて、次に仕入先や外注先の発注管理、さらに顧客管理へと適用範囲を拡大していくといった方法があります。段階的導入により、システム導入による混乱を最小限に抑え、現場の抵抗感も軽減できます。
また、各段階での効果を測定することで、投資対効果を確認しながら進められるという利点もあります。万が一期待した効果が得られない場合は、計画の見直しも容易になります。
ステップ7:運用体制の整備とスタッフ教育
クラウドインテグレーションの効果を最大化するには、適切な運用体制の整備とスタッフ教育が不可欠です。
システム導入後、実際に使用するのは現場のスタッフです。彼らがシステムを正しく理解し、活用できるかどうかが成功の鍵を握ります。
まずは管理者層に対して徹底的なトレーニングを行い、次に彼らが現場スタッフを指導する体制を構築します。
教育内容は操作方法だけでなく、システム導入の目的や期待される効果についても説明し、スタッフの理解と協力を得ることが大切です。
定期的なフォローアップ研修や、質問・相談窓口の設置も効果的でしょう。現場からのフィードバックを収集し、必要に応じてシステムや運用方法を改善していく姿勢も重要です。
ステップ8:データ活用と継続的な改善
クラウドインテグレーションの真価は、収集したデータを分析し、業務改善に活かすことで発揮されます。
収集・蓄積したデータを分析して、生産効率を下げている要因や品質問題の原因を特定します。分析結果をもとに、設備の制御方法や作業手順、生産計画などを最適化していきます。
初期段階では人の手による分析と改善が中心ですが、徐々にAIなどを活用した自動最適化を目指します。データ分析のパターンが蓄積されれば、将来予測も可能になり、より戦略的な意思決定ができるようになります。
継続的な改善サイクルを回すことで、クラウドインテグレーションの投資効果を最大化できるでしょう。
ステップ9:最新技術の活用
クラウドインテグレーションの効果をさらに高めるには、IoTやAIなどの最新技術との連携が有効です。
IoT技術を活用すれば、製造設備にセンサーを設置して稼働状況をリアルタイムでモニタリングできます。異常の早期発見や予防保全が可能になり、設備の稼働率向上につながります。
AIによるデータ分析は、大量の生産データから不良品発生の原因を特定したり、最適な生産条件を導き出したりするのに役立ちます。
クラウドコンピューティングの特性を活かし、地理的に離れた拠点間でもデータを共有し、効果的な協力体制を構築できます。技術の進化は速いため、常に最新動向をキャッチアップし、自社のシステムに取り入れる姿勢が重要です。
クラウドインテグレーション導入時の3つのリスク
クラウドインテグレーションの導入時には、以下3つのようなリスクもあります。
- セキュリティリスク
- 既存システムとの連携の難しさ
- コスト増加のリスク
順番に解説していきます。
リスク1:セキュリティリスク
クラウドインテグレーション導入時に最も懸念されるのがセキュリティリスクです。
インターネットを介してデータをやり取りするため、情報漏洩や不正アクセスの危険性が高まります。
特に製造業では、技術や製品に関する機密情報、取引先・顧客のリスト、従業員の個人情報など、重要なデータを扱うことが多いでしょう。これらの情報が流出すると、知的財産の喪失、社会的信用の失墜、さらには莫大な損害賠償金の支払いなど、深刻な影響を及ぼす可能性があります。
また、サイバー攻撃によって工場設備が遠隔操作されたり、停止させられたりするリスクも存在します。
このような事態を防ぐには、強固なセキュリティ対策と従業員教育が不可欠です。
リスク2:既存システムとの連携の難しさ
クラウドインテグレーションを導入する際、既存のシステムとの連携が困難になるケースがあります。
長年使用してきた社内システムやソフトウェアが、新しいクラウド環境に対応していない場合があるのです。データ形式の不一致や、互換性の問題により、スムーズな業務遂行に支障をきたす可能性があります。
また、クラウドサービスは提供側の定めた仕様に準じているため、自社特有の要件や独自機能の追加が難しいことも多いでしょう。
このような問題を回避するには、導入前に十分な検証と準備が必要です。
場合によっては、既存システムの大幅な改修や、新システムへの完全移行を検討しなければならないかもしれません。
リスク3:コスト増加
クラウドインテグレーションの導入は、初期投資を抑えられるメリットがある一方で、予想外のコスト増加を招くリスクもあります。
例えば、既存システムとの連携のために大規模な改修が必要になったり、データ移行に想定以上の時間とコストがかかったりする可能性があります。
また、クラウドサービスの利用料は従量制のものが多く、使用量が増えるにつれて月々の支払いが膨らむこともあるでしょう。
さらに、セキュリティ対策の強化や従業員教育にも追加のコストがかかります。デジタル化に伴う出費を過小評価すると、経営を圧迫する恐れがあります。導入前に綿密な費用対効果の分析を行い、長期的な視点でコスト管理を行うことが重要です。
クラウドインテグレーションの今後の発展
製造業におけるクラウドインテグレーションは、2025年以降もさらなる進化を遂げる見込みです。
総務省の令和5年通信利用動向調査によると、製造業でのクラウド導入率は79.2%に達しており、この成長傾向が続けば2033年には90%近くの企業がクラウドを活用すると予測されています。
今後の発展方向として、IoTとの統合がより一層進み、製造機器やセンサーからリアルタイムデータを収集・分析することで生産効率の向上が期待できます。
AIと機械学習の活用も重要なトレンドとなり、生産プロセスの最適化や予知保全の実現によってコスト削減と品質向上が図られるでしょう。
さらに、クラウド上でのデジタルツイン技術の発展により、製造現場のリアルタイム監視や将来予測が可能になります。
製造業のCIOやITリーダーにとって、業界特化型クラウドプラットフォーム(ICP)の導入も戦略的な投資として重要性を増しています。
クラウド技術は製造業のデジタル変革の基盤として、複数工場間のデータ連携や意思決定の迅速化、サプライチェーン全体の可視化を実現し、製造業の未来を形作る重要な要素となるでしょう。
まとめ
クラウドインテグレーションは、製造業のデジタル変革を加速させる重要な技術基盤です。
本記事で解説したように、導入によって以下の3つの主要メリットが得られます。
メリット | 効果 |
---|---|
コスト削減 | 初期投資抑制、柔軟なリソース管理 |
データ活用 | リアルタイム管理、業務効率化 |
拠点間連携 | 工場間データ共有、イノベーション促進 |
導入を成功させるためには、目的明確化から始まる9ステップのプロセスを段階的に進めることが重要です。
特に「現場調査」「段階的導入」「スタッフ教育」の3点は成功の鍵となります。
一方で、セキュリティリスクや既存システムとの連携の難しさ、予想外のコスト増加といったリスクにも注意が必要です。これらのリスクは事前の綿密な計画と対策で軽減できます。
今後は、IoT・AI・デジタルツインなどの先端技術との融合がさらに進み、製造業の競争力強化に不可欠なインフラとなるでしょう。
製造業の経営者は、クラウドインテグレーションを単なるIT投資ではなく、未来の工場を実現するための戦略的投資として位置づけることが重要です。
【注目コンテンツ】
・DX・ESGの具体的な取り組みを紹介!専門家インタビュー
・DX人材は社内にあり!リコーに学ぶ技術者リスキリングの重要性
・サービタイゼーションによる付加価値の創造と競争力の強化