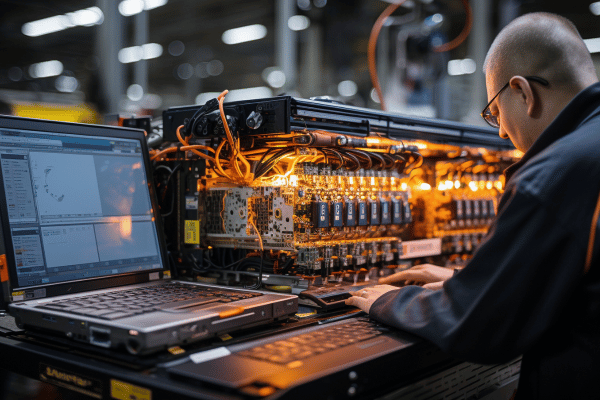
多くの工場や製造業の設備、電気製品には、動作を制御するPLCという装置が搭載されています。PLCは複雑な制御を効率的かつ正確に行える装置として、製造業や設備管理の現場に欠かせない存在です。また、PLCは工場の大規模な設備だけでなく、エレベーターや自動ドアなど、日常生活の身近な設備にも利用されています。
この記事では、PLCの仕組みや特徴、導入時に押さえておきたい基礎知識について解説します。
目次
PLCとは?基礎からやさしく解説
PLCとは「Programmable Logic Controller(プログラマブル・ロジック・コントローラ)」という言葉の略称で、製造業の設備や機器をコントロールする制御装置のことです。
PLCの定義と特徴
PLCは入力機器からの信号を取り込み、組み込まれているプログラムに従ってさまざまな処理を行い、接続された出力機器を制御しています。たとえば、ベルトコンベアのスタート・ストップ、ロボットアームの動作制御、温度調整や圧力制御など、多様な場面で使われています。
また、遊園地のアトラクションやエレベーター、エスカレーターなどの身近にある設備から、電子レンジや冷蔵庫などの家庭用の製品にもPLCが使われています。
PLCは、従来の制御手法である「リレーシーケンス制御」の代替として開発されました。リレーシーケンス制御は「物理的な電気信号」で制御していますが、PLCは「プログラム」によって制御を行うという大きな違いがあります。
このPLCの「シーケンス制御」によって機械・装置をコントロールできるようになったことで、専用のデバイスなどのハードウェアだけでなく、アプリなどのソフトウェアからも制御が可能になりました。
さらに、手動で1つ1つ動作を管理しなくても、PLCが全ての機械・装置の動作を制御してくれるので、操作が複雑な機械の制御も自動化できるようになっています。
PLCを構成している装置の内容
PLCは、主に下記の5つの装置によって構成されており、どれもPLCを動作させるために重要なものです。
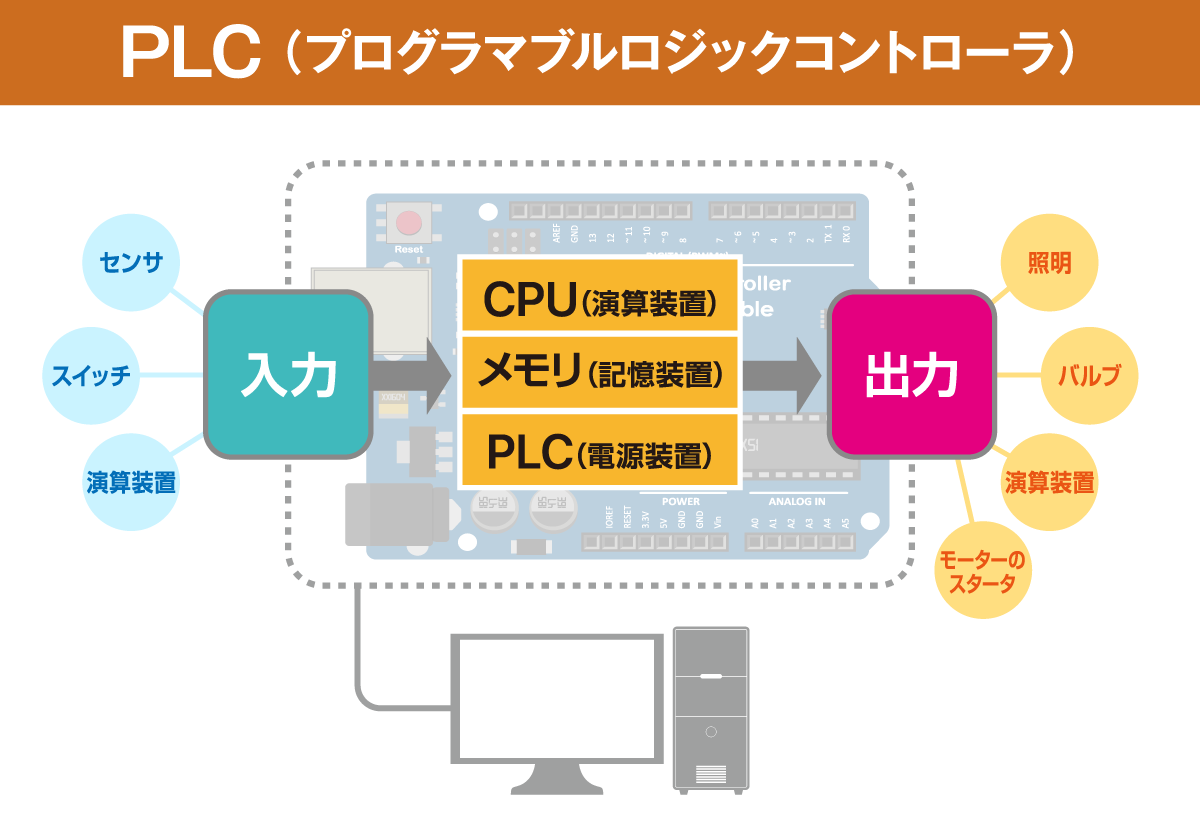
- 入力装置:スイッチやリレー回路などを入力する装置
- 出力装置:ランプやコンダクタ、センサーなど外部に情報を出力する装置
- 演算装置:CPUなど制御や演算を行う装置
- 記憶装置:メモリなど制御する機器の動作手順の情報を記憶する装置
- 電源装置:PLCの電源を扱う装置
PLCは、上記の5つがそれぞれの役割を行うことで、さまざまな機械の制御を可能にします。5つの装置のどれか1つでも欠けると機能しません。
PLCの歴史と発展
PLCは1960年代後半、アメリカの自動車産業において、制御装置の柔軟性を高める目的で開発されました。従来は制御回路を構成するために大量のリレーや配線が必要でしたが、変更や保守に時間とコストがかかるという課題がありました。これを解決するために登場したのが、ソフトウェアで制御を行うPLCです。
当初は簡易的な論理制御のみ対応していましたが、技術の進歩とともに機能は大きく進化。現在ではアナログ制御、ネットワーク通信、データロギングなど、複雑な制御も可能となっています。加えて、プログラミング環境も使いやすくなっており、ラダー図、SFC(シーケンシャル・ファンクション・チャート)、ST(構造化テキスト)など多様な記述方式に対応しています。
年代 | 出来事・発展内容 |
---|---|
1960年代後半 | 1968年、アメリカの自動車産業において制御装置の柔軟性向上を目的にPLCが開発。最初に商品化されたのは1969年で、Modicon(現シュナイダーエレクトリック)だと言われている。従来のリレー制御の課題(複雑な配線・高い保守コスト)を解決した。 |
1980年代 | ラダーロジックプログラミングが導入されてPLC の使用が簡単になったことで用途が拡大。 |
1990年代 | ネットワーク通信機能が実装され、他の制御機器との連携が容易に。PLCの分散配置や集中管理が可能になった。 |
2000年代〜 | スマートファクトリー・IoTとの連携が進み、産業用ネットワークやクラウドと接続。リアルタイムデータ処理やリモート制御など、次世代の制御システムの中核になった。 |
現在、PLCは日本国内では「シーケンサ」とも呼ばれ、オムロン、三菱電機、キーエンスなどの国産メーカーが世界中の産業現場で採用しています。その柔軟性と拡張性の高さから、スマートファクトリーやIoTと連携した次世代の製造ラインにも欠かせない存在となっています。
シーケンサとは?PLCとの違いも解説
「シーケンサ」と「PLC」は、ほとんど同じものを指す言葉ですが、使われる地域や場面によって表現が異なります。それぞれの用語の違いや背景を詳しく解説します。
シーケンサとPLCの用語の違い(国内外の使い方)
PLCは、海外で一般的に使われる正式な英語表記で、世界中の工場や製造現場で通じる用語です。一方、「シーケンサ」は、日本で独自に発展した呼び方で、特に三菱電機が製品名として「シーケンサ」を商標登録したことから広まりました。
国内では、技術者同士の会話や業務マニュアルでも「シーケンサ」という言葉がよく使われますが、国際規格や技術文書では「PLC」が主流です。つまり、呼び方は違っても、制御機器としての本質的な役割には違いがありません。
シーケンサとリレーシーケンスの違い
「リレーシーケンス」とは、かつて工場の自動制御に使われていた物理的なリレー(電磁スイッチ)を組み合わせた制御回路のことを指します。この方式では、制御の変更には回路や配線の組み替えが必要で、作業も複雑でした。
それに対して、シーケンサ(PLC)は、リレーシーケンスの機能をソフトウェアで置き換えた進化形です。制御内容はプログラムとしてメモリに記録され、配線を変えずにロジックだけを変更できます。そのため、変更作業が簡単になり、保守性や拡張性にも優れています。
主な違いを整理すると以下の通りです
リレーシーケンス | シーケンサ | |
---|---|---|
制御方法 | ハード制御 | ソフト制御 |
保守性 | 物理的交換が必要 | プログラム変更のみ |
拡張性 | 制御の変更には回路や配線の組み替えが必要 | 通信やネットワーク制御にも対応 |
このように、シーケンサはリレー制御の課題を克服した次世代の制御機器と言えます。
PLC=シーケンサ?日本国内での呼び方の違い
日本では、国内トップシェアのPLCメーカーである三菱電機が自社製品を「シーケンサ」として長く販売してきた歴史的背景があります。そのため、国際規格や技術文書では「PLC」という言葉が標準的な用語になりますが、日本国内では「シーケンサ」のほうが定着しており、制御機器の取扱説明書やカタログにも多く使われています。
技術者の間では、「シーケンサは三菱製のPLC」という認識が根強くあります。そのため、特定の機種やブランドを指定せずに汎用的に話す場合は「PLC」を使うのが一般的です。グローバル化の影響もあり、国内の現場レベルでも「PLC」という呼称を使う場面が増えてきていますが、依然として「シーケンサ」という呼び方も根強く残っています。
PLC制御の仕組みとプログラミングの基本
PLCは、入力された信号に応じて出力を制御する仕組みで動作します。その制御の流れやプログラミングの基本をわかりやすく紹介します。
PLC制御の流れ
PLCによる制御は、大きく「1.入力 → 2.処理 → 3.出力」という流れで行われます。具体的なステップは以下の通りです。
入力(センサ類)
温度、圧力、光、位置などの情報をセンサが検出し、その信号をPLCに送信します。たとえば、製品がラインに到達したかどうかを確認するフォトセンサなどが該当します。処理(PLC本体)
PLCはあらかじめ設定されたプログラムに基づき、入力信号を判定し、必要な制御ロジックを実行します。この処理の中心が、PLCのCPUユニットです。出力(アクチュエータ)
処理結果に応じて、出力信号が発信されます。これによって、モーターが回転したり、ソレノイドバルブが開閉したりといったアクションが実行されます。
このように、PLCは「信号を受け取り、判断し、動かす」という一連の流れを高速かつ正確に実行することで、機械の自動化を実現しています。
PLCは少し特殊なプログラミング言語を採用
PLCで採用されているプログラミング言語は、通常のPCで使われるプログラミング言語(PythonやC言語など)とは異なる、専用の言語を用いて制御内容を設定します。「IEC61131-3」という世界共有の標準規格で、主に以下の5種類があります。
- IL(インストラクション・リスト)
- LD(ラダー・ダイアグラム、ラダー言語)
- FBD(ファンクション・ブロック・ダイアグラム)
- ST(ストラクチャ―ド・テキスト、構造化テキスト)
- SFC(シーケンシャル・ファンクション・チャート、順序機能チャート)
IL(インストラクション・リスト)は、PLC向けの低水準なテキストベースのプログラミング言語で、アセンブリ言語に似た構文を持ち、命令を1行ずつ記述します。可読性が低いため、現在では非推奨とされています。
LD(ラダー・ダイアグラム)は、電気回路のリレー制御に似た図で構成され、初心者でも理解しやすい。日本国内では最も普及している形式です。
FBD(ファンクション・ブロック・ダイアグラム)は、機能ブロックを線でつないで制御を表す形式で、視覚的にわかりやすいのが特徴です。
ST(ストラクチャ―ド・テキスト)は、C言語やPascalに似た構文のテキストベース言語で、複雑な演算や分岐処理に適しています。
SFC(シーケンシャル・ファンクション・チャート)は、工程を段階的に制御するのに適した言語で、工程管理によく使われます。
特にLDは、日本の現場で長年使われてきたリレー制御に近いため、ベテラン技術者にも親しみやすく、教育現場でも多く採用されています。
PLCが採用されている機器・設備
PLCは産業界の様々な場面で利用されており、私たちの生活を支える多くの機器や設備に組み込まれています。
工場の生産ラインでは、組立工程の自動化や品質検査システムにPLCが使われています。コンベアベルトの制御やロボットアームの動作管理、各種センサーからの情報処理など、製造プロセスの中核を担っています。
また、食品加工プラントでは温度や圧力の精密制御、材料の自動計量・混合などにPLCが採用されています。衛生面や品質管理が特に重要な食品業界では、PLCによる安定した制御が欠かせません。
その他、以下のような日常生活で目にするさまざまな設備にもPLCが採用されています。
- エアコン
- 電子レンジ、洗濯機などの家電
- 自動ドア
- 遊園地のアトラクション
- エレベーター
- エスカレーター
- 信号機 など
このように、PLCは単なる産業用機器ではなく、私たちの身近なところで幅広く活用されている存在です。今後ますますPLCの活躍の場が広がっていくことが予想されます。
PLCの代表的な活用事例
PLCは製造業だけでなく、さまざまな産業や生活の場面で利用されています。ここでは代表的な活用シーンを紹介しながら、その役割と効果を具体的に解説します。
工場の自動化(FA)での活用〜株式会社JRCの事例〜
PLCが最も広く使われているのが、工場の自動化(FA=Factory Automation)です。例えば、組立工程や検査工程、包装工程などにおいて、センサと連携してモーターやアクチュエータを正確に制御します。
これにより、人手を減らしつつ生産性と品質を安定させることができます。ライン変更時もソフトウェアで制御プログラムを書き換えるだけで済むため、柔軟な対応が可能です。また、故障診断機能などによりダウンタイムを最小限に抑えることも、FAにおけるPLCの大きなメリットのひとつです。
具体的な事例を上げると、株式会社JRCでは自社工場の自動化として、ロボットで部品を持ち上げ、両面をエアブローで清掃するといったことが行われています。
ビル設備管理・空調制御〜三菱電機株式会社の事例〜
ビル管理にも広く応用されているPLC。空調・照明・エレベーターなどの制御に活用されています。例えば、センサからの情報を元にエアコンのON/OFFや風量を自動調整したり、時間帯や利用状況に応じて照明を制御したりすることが可能です。
こうした自動制御により、省エネ効果や快適な空間づくりに貢献します。また、ネットワークと連携することで、遠隔からの監視や操作も可能となり、ビル全体の統合管理にも有効です。
具体的には、三菱電機名古屋製作所では空調や照明をシーケンサ(PLC)で制御し、エネルギーの見える化を推進しています。これにより、以前よりも10%ほど消費電力を削減できたとしています。
自動販売機やエレベーター、信号機での応用
PLCは私たちの日常にも密接に関わっています。たとえば、自動販売機では商品の選択から払い出し、在庫管理まで一連の動作をPLCが担っています。また、エレベーターのフロア移動、ドア開閉、安全制御などのタイミング制御にもPLCが使われています。これらの装置では、正確で迅速な処理が求められるため、リアルタイム性に優れたPLC制御が適しているのです。
また、わたしたちが普段目にする「信号機」にもPLCが活用されています。交通量に応じた制御やタイミング調整を自動で行っているのです。プログラムの変更で運用の最適化や緊急車両優先の制御も可能です。
このように、製品の小型化・高性能化が進む中、PLCもコンパクトかつ多機能なモデルが増えており、今後も応用範囲は広がると考えられます。
PLCを導入するメリット・デメリット
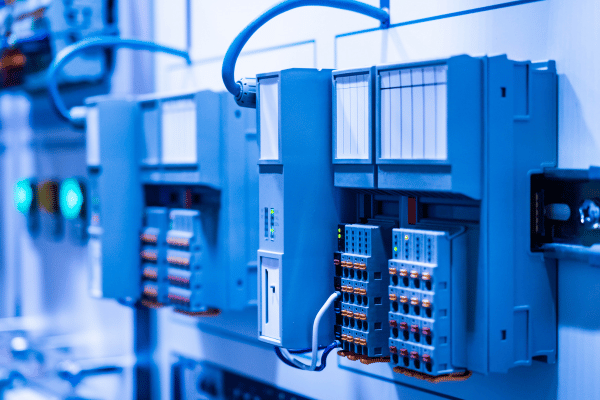
PLCの導入には多くの利点がありますが、同時に注意すべき課題も存在します。ここでは、メリットとデメリットを解説します。
PLC導入によるメリット
PLCの導入には多くの利点がありますが、一方で導入・運用に際して注意すべきデメリットも存在します。ここでは実務視点でメリット・デメリットを整理して解説します。
・製作コストの削減ができる
PLCは、回路設計をソフトウェアで行うので、従来のリレーシーケンス制御のように電子タイマーや電磁リレーなどの電気制御機器を大量に用意する必要がなく、最小限の電子機器のみで動作変更ができます。
部品の購入費用や修理・メンテナンス費用、人件費なども削減できるので、通常の制御機器よりも大幅にコストを削減できます。
さらに、通常の制御機器ではリレー回路が複雑になり、スペースを必要とするなど動作変更による機械故障の確率が高くなってしまいますが、そのリスクを抑えられます。
・制御部分の小型化ができる
PLCは、制御部分を小型化して省スペース化が可能です。ソフトウェアによってプログラムするだけで機械制御を行うことができ、施設や工場においてPLC本体の設置スペースを確保するだけで済みます。
しかし、リレー回路の制御装置では、リレー回路同士を電線でつないだり、電磁リレーや電子タイマーなども設置する必要があるので、そのためのスペースが必要になってしまいます。
限られたスペースしか確保できない場合、リレー回路の制御装置を設置することは業務効率低下のリスクがあります。しかし、PLCではこれらの追加のコンポーネントを必要とせず、狭いスペースでも効率的な制御が可能です。
・プログラミング変更だけで動作制御が可能
PLCは、動作制御や回路の変更、設計が簡単に行えることも大きなメリットの1つです。
リレー回路では、動作制御を変更するためには一度機械を停止させて回路を繋ぎ直す必要があるので、その分の作業時間がかかってしまいます。
PLCであればソフトウェアの組んであるプログラムを変更するだけで動作制御が可能です。
さらに、機械を止める必要がないので、生産性を維持したまま変更ができ、機械故障の確率も減少します。
・保守や整備が簡単に行える
PLCは、保守や整備を簡単に行うこともできます。
PLCには、電子タイマーや電磁リレーなどの電気制御機器が必要なく、電源回路同士を繋ぐ必要もありません。
さらに、機械を動かしている状態でも問題なくプログラムを変更・設計できるので、保守や整備にかかるコストが抑えられます。
リレー回路であれば、整備士に依頼したり工場の機械を停止させたりする場合があるので、PLCのように簡単にはいきません。
その点、PLCは低コストで長期的な運用も容易にできます。
PLC導入によるデメリットと注意点
次に、PLCを導入する5つのデメリットや注意点をそれぞれ解説します。
・初期コストが高い
PLC本体や入出力装置、電源装置などのハードウェアに加え、設計・開発費用、プログラミングソフトのライセンス料などが発生します。加えて、導入時には技術者の人件費やトレーニング費用もかかるため、設備投資としてのハードルは高めです。
・プログラミングスキルが必要
PLC制御をするためには、ラダー図やST(構造化テキスト)など専用の言語でのプログラミングが不可欠です。簡単な制御でも、基礎知識がないと設定や変更が難しく、現場のスタッフが扱うには一定の教育や経験が必要になります。
・導入・保守に時間がかかる
機器の選定から設計、配線、ソフト開発、試運転まで複数の工程を踏むため、導入にはある程度のリードタイムが必要です。また、稼働後の修正や機能追加を行う場合も、事前の検証や工程管理が必要となり、柔軟な運用には工夫が求められます。
・故障時の対応が複雑
PLCのトラブルは、ハードの故障だけでなく、プログラム上のミスや外部機器との通信エラーなど、複合的な原因で発生します。原因の特定には専用ソフトや知識が求められるため、一般作業員では対応が難しく、技術者の常駐や連携が不可欠です。
・メーカー間の互換性が低い
PLCは各メーカーに仕様やソフトウェアが異なるため、異なるメーカーの機器間での互換性が低いのが現状です。一度導入したメーカーに依存しやすく、将来的なシステム変更や拡張に制約が出る可能性があります。
バーチャルPLCとは?
バーチャルPLCは、物理的なPLC装置を持たずに、ソフトウェア上で制御ロジックを実行する新しい技術です。以下では、その特徴やメリット・課題について解説します。
バーチャルPLCの概要と定義
バーチャルPLCは、仮想環境上で動作するソフトウェアベースのPLCで、物理ハードウェアの代わりにクラウドや産業用PC上で制御処理を行います。これにより、従来のように個別のPLC機器を設置する必要がなくなり、柔軟性と拡張性が大きく向上します。近年のIIoT(産業用IoT)やスマートファクトリー化の流れの中で、注目が高まっています。
従来型PLCとの違い
従来のPLCは専用ハードウェアを使用して制御を行いますが、バーチャルPLCはその処理をソフトウェアとして仮想マシンやコンテナ上で実行します。そのため、物理的制約が少なく、リソースの最適化やシミュレーションとの親和性が高い点が異なります。
バーチャルPLCのメリット・デメリット
メリットには、ハード不要によるコスト削減、リモートでの管理や迅速な構成変更が挙げられます。一方で、リアルタイム性や通信遅延の課題、セキュリティ面での対策も必要です。用途や現場環境によって適性が分かれるでしょう。
今後の展望と技術動向
バーチャルPLCは今後、クラウドベースの製造制御やAIとの連携など、よりスマートな製造プロセスの中核としての活用が期待されています。リアルタイムOSの発展やエッジコンピューティングとの融合も注目されています。
PLCを選ぶ上での3つのポイント
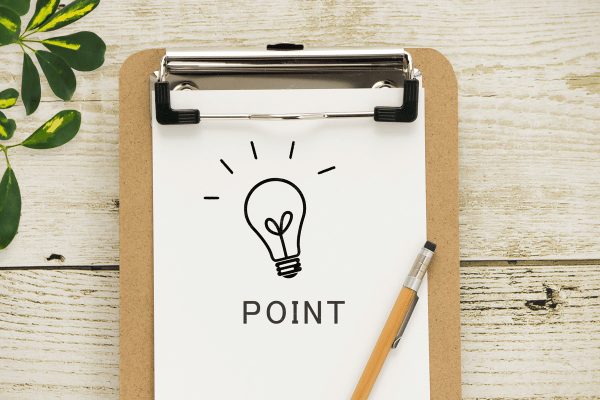
PLCはさまざまなメーカーから多種多様な製品が提供されており、用途や現場の要件に応じて最適なモデルを選ぶことが重要です。ここでは、PLCを選定する際に押さえておきたい基本の3つのポイントをご紹介します。
既設製品のメーカーをベースに検討
PLCを選ぶときには、現場ですでに使われているメーカーの製品をベースに検討することが基本となります。メーカー間でプログラミングソフトや通信仕様が異なるため、異なるメーカー製品を混在させると、互換性や保守対応の面で手間が増える可能性があるからです。
自社でプログラム開発が行いやすい製品を選ぶ
PLCの運用にはプログラミングが不可欠です。そのため、社内にあるスキルや人材に合った開発環境が整っているかを事前に確認しておくことが重要です。
たとえば、電気制御出身の技術者が多い場合はラダー言語対応が豊富なメーカーを、IT系出身のエンジニアが関わる現場では構造化テキスト(ST)に強い製品を選ぶことで、開発や運用がスムーズになります。
また、教育コンテンツや技術サポートが充実しているメーカーを選ぶことで、社内でのスキル定着や運用支援にもつながります。
メモリーや処理速度の要件を満たしているか確認する
メモリーや処理速度の要件を満たしているかを確認することも大切なポイントの1つです。
PLCは、製品ごとにメモリーや処理能力が異なっているため、導入した製品によっては処理能力が不十分である場合があります。
導入してから製品の問題点に気づいてしまうと、再導入やパーツの追加のコストが必要になるほか、生産性を向上させられないといったトラブルに繋がります。
そのため、しっかりと自社の機械や設備に必要な処理能力を持っているPLC製品かどうか確認した上で導入するようにしましょう。
PLC販売を行う主なメーカー4選
さまざまなメーカーがPLCを販売・提供しており、メーカーごとに機能や処理能力、特徴などは大きく異なります。
ここでは、PLC販売を行うメーカーの中から、主なメーカー4社を紹介します。
三菱電機株式会社
三菱電機株式会社は、PLC販売の国内シェア1位というだけでなく、世界でもトップクラスのシェアを誇るPLCを代表するメーカーです。
三菱電機株式会社のPLCの商標「シーケンサ」の知名度が高く、PLC=シーケンサというイメージを持つ方も多くいます。
世界トップクラスの豊富な実績と、高い技術力・信頼性により、多くの企業で使用されています。
PLCの仕様は三菱電機の独自規格となっていますが、すでに多くの企業で導入されていることもあり、シーケンサのプログラミングに慣れているエンジニアも多く、導入しやすいというメリットがあります。
その需要の高さから品揃えも豊富で、他機器との連携性もよいため「迷ったら三菱電機のPLCを選ぶ」というケースも少なくありません。
オムロン株式会社
医療機器や電気機器メーカーとして有名なオムロン株式会社は、日本国内でトップクラスのPLC販売シェアを誇ります。
オムロン株式会社は、PLCに加えて、関連するセンサーやモーターのシェアが高いことでも知られています。 特にセンサー類のIoT化をすすめており、PLCを活用したIoTプラットフォームの構築に力をいれています。
またオムロン株式会社では、コントローラを動作させるためのプログラミング言語に、C言語が採用されているという特徴があります。
C言語はシステム開発などで多くのエンジニアが使用している言語です。そのため、PLC独自のプログラミング言語の知識がなくとも、多くのエンジニアが取り扱えるという点が大きな強みです。
オムロン株式会社のPLCは、製造業のFAシステムや自動車工場、IoT開発など、さまざまな現場に導入されています。
株式会社キーエンス
株式会社キーエンスは、情報機器や電子・光子顕微鏡などの精密機器の開発及び製造・販売を行う企業です。
基本的にBtoBが主体の企業であり、企業や工場に対して営業活動を行うことで自社製品の販売を促進しています。
キーエンスのPLCは機能性が高く、日本国内でのシェア率も高いため、運用やメンテナンスを行えるエンジニアが多いというメリットがあります。
また、三菱電機株式会社のPLCとリンクさせて互換モードが使用できるという強みもあるため、違うメーカー同士でもデータのやり取りや連携が容易に行えます。
さらに精密機器を扱う企業の製造するPLCのため、処理速度の速さにも定評があります。
富士電機株式会社
大手電気機器メーカーである富士電機株式会社は、PLCの国内シェアでは三菱電機、オムロン、キーエンスに劣るものの、提供しているPLCが、国土交通省が定めた電気設備の標準仕様に対応しているという大きな特徴があります。
特に富士電機の「MICREX-SXシリーズ」は、小規模から大規模なシステムまで対応可能です。国土交通省が定めた電気設備の標準仕様(IEC61131)だけでなく、IECやJIS、CEマーキング、UL、RoHSに標準で対応しています。
そのため、国内だけでなく、海外市場からの要望にも対応できるという強みを持っています。
PLCの基礎知識を知って自社に最適な製品を導入しよう
PLC(プログラマブル・ロジック・コントローラ)は、製造業をはじめとする多くの分野で、設備の自動制御や省人化、トラブル対応力の向上に貢献する重要な存在です。従来のリレー回路に代わり、柔軟かつ高効率な制御を可能にしたことで、現代の産業インフラを支える基盤技術のひとつとなりました。
また、近年では「バーチャルPLC」といった新たな技術も登場しており、制御のあり方も大きく進化しています。
本記事でご紹介した内容を参考に、基本知識をしっかりと身につけた上で、自社に最適なPLCを選び、安定した制御環境を構築していきましょう。
【注目コンテンツ】
・エンジニアの精鋭部隊が集結した合弁会社「DTダイナミクス」設立で生産性が3倍に。内製化支援と技術移転、成功の秘訣とは
・新たな建築プロセスを目指す「設計BIMツール」開発、400年の歴史を誇る竹中工務店が描く理想の建築業界とは
・事業の進化、組織の改革、THKの変革を支える「二項動態」の考え方