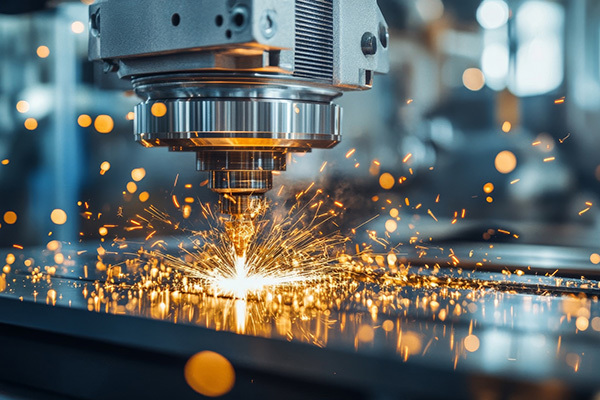
製造業において治工具管理は、治具や工具、金型などを一元的に管理する仕組みであり、製造現場の生産性向上に直結しています。
適切な管理が行われないと、欠品による生産停止や不良品発生といった問題が生じるため、購入から廃棄までの全ライフサイクルを通じた管理が必須となっています。
従来は紙台帳による管理が主流でしたが、作業の煩雑さやヒューマンエラーのリスクが課題でした。
近年はRFIDやバーコードを活用したデジタル管理システムの導入が進み、治工具の所在や状態をリアルタイムで把握できるようになっています。
本記事では、治工具管理の基本から実践法、導入事例まで詳しく解説し、製造業の競争力強化につながる知識を提供します。
治工具管理とは?
治工具管理とは治具や工具、金型などを一元的に管理することです。
治具は部品の固定や作業のガイドをする役割があり、工具にはドライバーのような作業工具のほか、切削加工や変形に用いられるものも含まれます。
製造業において、治工具は生産効率化と作業精度を向上するための極めて重要なツールとなっています。
治工具が欠品すると生産ができず、不良があると製品の品質に直接影響するため、購入から廃棄までのライフサイクル全般にわたる管理が必要です。
従来、治工具の保証や破棄は現場の担当者の感覚で行われることが多く、紙の台帳で管理すると作業が煩雑になるだけでなく、ヒューマンエラーも発生しやすくなります。
適切な治工具管理により、生産性向上、品質安定化、コスト削減などの経営メリットが得られるでしょう。
治工具管理の最大の目的は、必要な治工具を必要なときに使用できる状態を維持し、生産性と品質の向上を安定して実現することにあるのです。
治工具管理システムとは?
治工具管理システムとは、製造現場で使用する治具や工具を効率的に管理するためのデジタルシステムです。
治具や工具の所在、使用状況、メンテナンス履歴などを一元管理し、必要なときに必要な治工具をすぐに使える状態に保つ仕組みを提供します。
従来の紙台帳による管理と比較して、人的ミスの削減や管理工数の大幅な削減が可能になります。
基本的な機能としては、治工具の受入・貸出・返却管理、在庫管理、寿命管理、メンテナンス管理などがあります。最新のシステムではRFIDタグやバーコードを活用した個体識別機能や、クラウド連携によるリアルタイム情報共有機能も搭載されています。
導入企業の事例では、治工具の紛失率や探索時間が減少し、メンテナンスコストも削減されるなどの効果が報告されています。
製造業の生産性向上と品質安定化を実現するための重要なインフラとして、多くの企業で導入が進んでいるのです。
治工具管理の具体的な方法と実践法10ステップ
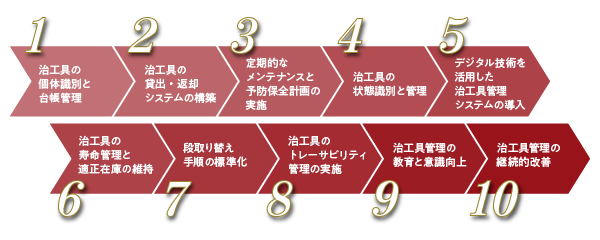
治工具管理を実際に行っていく際の手順は、以下の10ステップです。
1.治工具の個体識別と台帳管理
2.治工具の貸出・返却システムの構築
3.定期的なメンテナンスと予防保全計画の実施
4.治工具の状態識別と管理
5.デジタル技術を活用した治工具管理システムの導入
6.治工具の寿命管理と適正在庫の維持
7.段取り替え手順の標準化
8.治工具のトレーサビリティ管理の実施
9.治工具管理の教育と意識向上
10.治工具管理の継続的改善
順番に解説していきます。
ステップ1:治工具の個体識別と台帳管理
まずは治工具に固有の識別番号を付与し、管理台帳に登録しておくとよいでしょう。識別番号はシールの貼付や直接刻印など、剥がれない方法で表示します。
台帳には工具の種類、型番、数量、メーカー、購入価格などの基本情報を記録し、常に最新の状態を維持します。この管理方法により、類似した治工具や複数所有している同一治工具の混同を防止できます。
特に顧客から提供された治工具には、恒久的なマークで識別し、見やすい位置に表示することが重要です。
ステップ2:治工具の貸出・返却システムの構築
つぎは治工具の貸出時には、使用者名、所属部署、貸出日、返却予定日、使用目的などを記録するシステムの導入です。
返却時には貸出記録と照合し、破損や異常がないかを確認する手順を設けます。このシステムにより、誰がどの工具をいつ使用しているかを明確にし、紛失リスクを大幅に削減できるのです。
貸出予約機能を設けることで、計画的な治工具の使用が可能になり、作業の効率化につながります。
ステップ3:定期的なメンテナンスと予防保全計画の実施
治工具の性能を維持するため、定期的なメンテナンスと予防保全計画を策定しましょう。
計画には治工具の定期点検スケジュール、消耗部品の交換タイミング、交換部品の在庫管理などを含めます。使用後は清掃して所定の場所に戻すことを徹底し、次回使用時の問題発生を防止します。
メンテナンス履歴を記録することで、治工具の状態を把握し、適切なタイミングでの交換や修理が可能になるのです。
ステップ4:治工具の状態識別と管理
治工具の現在の状態(使用中、修理中、校正中など)を明確に識別できる仕組みを構築します。
状態識別には色分けシールやタグなどを活用し、一目で状態がわかるようにしましょう。不良品や使用禁止の治工具は明確に区別し、誤使用を防止する対策を講じます。
治工具の状態を視覚的に管理することで、作業者が適切な治工具を選択でき、品質問題の発生を未然に防ぎます。
ステップ5:デジタル技術を活用した治工具管理システムの導入
RFIDタグやバーコードを治工具に取り付け、デジタル管理システムによる一元管理を検討しましょう。治工具管理システムでは治工具の所在、使用状況、メンテナンス履歴などをリアルタイムで把握できます。
生産実績とのリンクにより、治工具の使用頻度や寿命を正確に把握し、適切な時期の交換や廃棄判断が可能になります。デジタル管理により、属人化を防ぎ、誰でも必要な治工具の情報にアクセスできる環境を整えられるでしょう。
ステップ6:治工具の寿命管理と適正在庫の維持
治工具の使用回数や時間を記録し、寿命を管理するシステムを構築します。寿命に近づいた治工具は事前に交換計画を立てることで、生産への影響を最小限に抑えられるでしょう。
使用頻度や重要度に応じた適正在庫を維持し、過剰在庫や在庫切れを防止します。定期的な棚卸しを実施し、実際の在庫と記録の整合性を確認することで、正確な在庫管理を実現します。
ステップ7:段取り替え手順の標準化
治工具の交換や設定変更など、段取り替えの手順を標準化し、マニュアル化します。標準作業手順書には、使用する治工具、設定条件、確認ポイントなどを明記しましょう。
段取り替え作業の効率化により、生産ラインの停止時間を最小限に抑え、生産性向上につながります。作業者による手順のばらつきを防ぎ、品質の安定化と作業時間の短縮を実現できます。
ステップ8:治工具のトレーサビリティ管理の実施
治工具の使用履歴を記録し、どの製品にどの治工具が使用されたかを追跡できるシステムを構築します。
製品に不具合が発生した場合、使用した治工具を特定し、同じ治工具で製造された他の製品への影響範囲を把握できます。また治工具の履歴データを分析することで、品質問題の早期発見や予防対策に活用可能です。
トレーサビリティ管理により、品質問題の原因究明と対策が迅速に行え、顧客への信頼性向上につながります。
ステップ9:治工具管理の教育と意識向上
作業者に治工具管理の重要性を理解させるための教育プログラムを実施します。正しい使用方法、保管方法、異常時の報告手順などを定期的に指導しましょう。
管理ルールの遵守状況を定期的に確認し、必要に応じて改善指導を行います。治工具管理への意識向上により、作業者自らが治工具の状態に注意を払い、問題の早期発見につながります。
ステップ10:治工具管理の継続的改善
定期的に治工具管理の状況を評価し、問題点や改善点を洗い出します。
現場の作業者からのフィードバックを積極的に収集し、管理方法の改善に活かしましょう。新しい管理技術や方法を常に研究し、より効率的な管理システムへと進化させます。
継続的な改善活動により、治工具管理の精度向上とコスト削減を両立させることが可能になります。
治工具管理の成功事例3選
ここからは、治工具管理を行って成果を上げた事例を3つ紹介していきます。
順番に見ていきましょう。
事例1:在庫削減と品質向上
ある製造業企業では、工具のデジタル管理と使用量分析、自動発注機能を持つ治工具管理システムを導入しました。
在庫の適正化だけでなく、工具の取り出し間違いによる加工不良もなくなり、製品品質も向上しました。治工具管理システムは、必要な工具を必要な時に取り出せるよう、キャビネットの引き出しに工具ごとの所定位置を設定しています。
出庫の際はタッチパネルで品目や数量を入力するか、バーコードを読み取ると該当する引き出しが光って施錠が解除される仕組みです。
このシステムにより、工具を探し回る時間のロスがなくなり、欠品もゼロになるという成果が得られました。
事例2:工具データベース統合による業務効率化
ある設備機器メーカーでは、社内に9つも存在していた工具データベースを1つに統合することに成功しました。統合により、工具情報の検索が容易になり、正確な工具リストの作成が可能になりました。
段取り作業のスピードアップとミスの減少につながり、業務効率が大幅に向上しています。
工具情報の見える化により、より正確な機械加工作業のスケジュール計画が立てられるようになりました。各担当者が自分の席から離れることなく工具の利用可否や所在を把握できるようになり、作業の流れがスムーズになりました。
予期しない切削問題が発生した場合でも、素早く代替工具や最適な切削条件を検索できるため、トラブル対応時間も短縮されています。
事例3:工具改善プロジェクトによる交換時間短縮
ある製造業企業では、生産性向上を目的として製造部と生産技術部が合同で「工具改善プロジェクトチーム」を発足させました。
NC機械における工具交換時間、工具寿命、工具費低減、切粉処理などの課題に取り組み、具体的な改善案を作成。プロジェクトの成果として、ヘッド交換式の工具を導入し、刃先のみを交換する方式に切り替えました。
高さ調節の必要がないため機上での工具交換が可能となり、工具交換時間を削減することに成功しています。
消費工具の少ないオペレーターから作業のコツを他のメンバーに伝授することで、工具費が削減されただけでなく、人材育成にもつながったという副次的効果も得られています。
治工具管理システム導入する際の3つの注意点
治工具管理システムの導入を検討している場合は、以下の3点を確認しておきましょう。
- 自社の製造工程に合ったシステムを選定する
- 従業員の教育とリーダーシップの確保
- 既存システムとの互換性とカスタマイズ性の確認
順番に解説していきます。
注意点1:自社の製造工程に合ったシステムを選定する
治工具管理システムを導入する前に、「自社にとって本当にメリットがあるのか」をしっかり検討しましょう。
効率化や省力化などの具体的な改善につながるか、導入によって逆に現場が混乱しないか、作業手順や人員配置で解決できる問題ではないかなどを考慮する必要があります。
特に治具の場合は数十万円単位のコストがかかることも珍しくないため、対費用効果も確認しながら導入を検討してください。
自社製品ならびに製造工程の特徴・問題点に合わせた治工具管理システムを選ぶことが重要です。
現段階での作業の問題点を抽出し、導入担当者と現場作業者との意見をすり合わせることで、より効果的なシステム選定が可能になるでしょう。
テスト運用での調整を妥協せずに行うことも、システムの有効性を確保するために欠かせません。
注意点2:従業員の教育とリーダーシップの確保
システム導入の成功には、従業員への適切な教育と経営層のサポートが不可欠です。
新しいシステムの導入は、使い方の教育が不十分だと従業員が効果的に活用できず、導入効果が大幅に低下してしまいます。忙しい従業員が新しいシステムを学ぶ時間を確保するのは難しいため、分かりやすい教育リソースを用意することが重要です。
また、経営層のサポートがなければ、新システム導入は困難な戦いになります。リーダーシップのサポートがない場合、管理者やチームは新システム導入を単なる提案と捉え、真剣に取り組まない可能性があります。
トレーニングへの参加率低下や導入率の低さ、ワークフロー変更への関心の低さにつながることもあるため、経営層の積極的な関与が成功の秘訣です。
注意点3:既存システムとの互換性とカスタマイズ性の確認
導入するシステムが社内の既存ITインフラと互換性があるか確認することが重要です。
WindowsやiOS、Androidなど、どのOSで動作するかを事前に確認し、社内で使用しているITインフラとの互換性を考慮して選択しましょう。
また、組織のニーズに合わせてカスタマイズできるシステムを選ぶことも大切です。
自社である程度カスタマイズできる製品のほうが使い勝手が良い場合も多く、発注システムなどと統合できれば、データの一元化や自動化によって効率向上に貢献します。
さらに、システムのインターフェースを確認し、システム担当者以外の使用者が迅速に情報を入力し、必要なデータを取得できるか確認することも重要です。
発行会社のサポート体制が十分かも確認し、導入後も効果的にシステムを活用できる環境を整えましょう。
治工具管理の今後の発展
製造業では、治工具管理のデジタル化が急速に進展しています。特に注目すべきは、IoT技術を活用したスマート治具の普及です。
センサーを組み込んだ治具により、使用状況やメンテナンス状態をリアルタイムでモニタリングし、作業のダウンタイムを最小限に抑える仕組みが実現しています。
さらに、AI技術を活用した自動調整フィクスチャや3Dプリンタによる迅速な治具製造も広がってきているのです。製造現場のオペレーター不足や賃金上昇に対応するため、工程集約・自動化・DXのニーズは今後さらに高まると予想されています。
治工具のデジタル化は、設計効率化、製造コスト削減、品質向上など多くのメリットをもたらし、スマートファクトリー実現の重要な要素となっているのです。
治工具管理システムを活用した資産追跡や予防保守の最適化がさらに進み、製造プロセス全体の透明性向上に貢献するでしょう。
まとめ
治工具管理は製造業の生産性と品質を左右する重要な要素です。
適切な治工具管理により、生産効率の向上、品質の安定化、コスト削減、人的ミスの減少、安全性の向上といった多くのメリットが得られます。
システム導入時は自社の製造工程に合ったものを選び、従業員教育とリーダーシップの確保、既存システムとの互換性確認が重要です。
今後はIoT、AI、3Dプリンティングなどの技術を活用したスマート治工具管理がさらに発展し、製造業のDXを加速させるでしょう。
【注目コンテンツ】
・DX・ESGの具体的な取り組みを紹介!専門家インタビュー
・DX人材は社内にあり!リコーに学ぶ技術者リスキリングの重要性
・サービタイゼーションによる付加価値の創造と競争力の強化