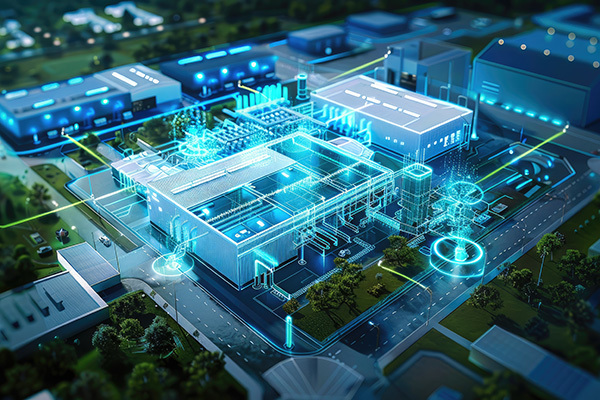
製造業の古いシステムは、変化の激しい市場環境で競争力を維持するための足かせとなっています。
モダナイゼーションは、こうした課題を解決し、企業全体のデジタル化を推進する重要な取り組みです。
製造業界では、デジタル技術を活用した新規参入企業が市場を変革している現状があります。
そこで本記事では、製造業におけるモダナイゼーションの手法や導入ステップ、成功事例などを詳しく解説していきます。
目次
モダナイゼーションとは?
モダナイゼーションは、製造業の古い情報システムを最新の技術で刷新し、業務プロセスを最適化する取り組みです。単なるシステム更新にとどまらず、企業全体のデジタル化を推進し、新たな価値を生み出すことを目指します。
製造業では、生産管理や販売管理など基幹業務を支えるシステムが対象となります。
この取り組みは、変化の激しい市場環境に柔軟に対応し、競争力を維持・向上させるために不可欠です。
モダナイゼーションによって、業務効率の向上、コスト削減、セキュリティ強化などの効果が期待できます。さらに、新たなビジネスモデルの創出や、顧客満足度の向上にもつながる可能性があります。
製造業の経営者にとって、モダナイゼーションは避けて通れない重要な経営課題となっているのです。
製造業にモダナイゼーションが必要な2つの理由
製造業にモダナイゼーションが必要な理由として、おもに以下の2つがあげられます。
- 競争力の維持と向上
- セキュリティリスクの軽減
順番に見ていきましょう。
理由1:競争力の維持と向上
製造業界では、デジタル技術を活用した新規参入企業が革新的なビジネスモデルで市場を変革しています。従来の古いシステムを使い続けると、機能面や処理速度の問題から業務効率が低下し、企業全体の生産性も下がります。
モダナイゼーションによって最新技術を導入すれば、生産性向上が見込め、リソース不足で取り組めなかった業務に時間を割いたり、新サービスの開発スピードを高められるでしょう。
データ活用を容易にする仕組みを構築することで、リアルタイムな情報分析が可能となり、ビジネス判断を素早く行えるため、変化の激しい市場環境でも競争力を維持できます。
経営資源のデジタル化により、組織を超えたデータ活用や企業間のデータ連携が可能になり、コスト削減にもつながります。
理由2:セキュリティリスクの軽減
老朽化したシステムを使い続けると、セキュリティの穴が増え、サイバー攻撃や情報漏えいの危険性が高まります。モダナイゼーションを通じて最新のセキュリティ対策を導入すれば、これらの脅威に効果的に対応できるようになるでしょう。
例えば、クラウドベースのシステムに移行することで、セキュリティ更新が自動的に行われ、最新の脅威にも迅速に対処できる環境が整います。ランサムウェアなどのサイバー攻撃に対する防御力を強化することで、システム障害やデータ損失といったリスクを減らすことが可能です。
モダナイゼーションによるセキュリティ強化は、業務の信頼性を高めるだけでなく、企業のIT基盤をより堅牢で安心できるものへと進化させる重要な取り組みといえるでしょう。
製造業のDX推進に効果的な5つのモダナイゼーション手法
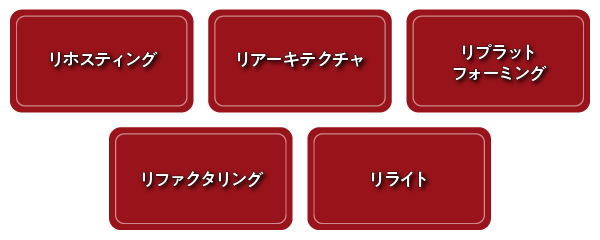
製造業のDX推進に効果的なモダナイゼーションの手法として、以下の5つがあげられます。
- リホスティング
- リアーキテクチャ
- リプラットフォーミング
- リファクタリング
- リライト
順番に解説していきます。
手法1:リホスティング
リホスティングとは、古くなった機材やオペレーティングシステムなどの基盤的な部分を新しいものに置き換え、アプリケーションソフトやデータにはほとんど手を加えずに移行する手法です。
サーバーやOSなどITインフラを刷新する方法で、既存システムを別環境へ移行します。大きな特徴は、既存システムをほぼそのまま移行できるため、コストを抑えて素早く実行できる点にあります。
製造業においては、古いシステムをクラウド環境に移行することで、運用コストの削減や外部の新しいシステムとの連携が可能になります。
ただし、レガシーシステム自体を根本的に変更するわけではないため、新しいデジタル技術を活用しづらく、業務効率化が限定的になるリスクも考慮する必要があるでしょう。
手法2:リアーキテクチャ
リアーキテクチャとは、既存のシステムを根本的に再設計し、新たな技術やアーキテクチャを採用することで課題を解決する取り組みです。
クラウドネイティブ化によるアジリティとスケーラビリティの向上を図り、ビジネスの変化に柔軟かつ迅速に対応できるシステムを実現します。
マイクロサービスアーキテクチャを導入することで、開発チームの自律性を高め、継続的なデリバリーを可能にする効果も期待できます。
製造業では特に、コンテナ技術(Dockerなど)やオーケストレーションツール(Kubernetesなど)を活用することで、リアーキテクチャの効率と信頼性を向上させることが可能です。
この手法は大規模な変革を伴いますが、長期的な視点で見ると製造プロセス全体の最適化につながり、DX推進の強固な基盤となるでしょう。
手法3:リプラットフォーミング
リプラットフォーミングは、既存システムのサーバーやOSなどを新プラットフォームに移行する手法で、一部のコンポーネントを修正してクラウド環境に適応させます。
クラウド環境に合わせた最適化により、システムのパフォーマンスを向上させる効果があります。
例えば、データベースをAmazon RDSに移行することで、自動バックアップや高可用性などのメリットを享受できるようになります。
製造業においては、リソースの効率的な利用によりクラウド利用料金を最適化でき、不要なインスタンスの削減や適切なインスタンスタイプの選択によってコスト削減が可能になります。
また、リファクタリングよりも移行期間を短縮できるため、迅速なクラウド移行が可能となり、ビジネスの変化に素早く対応できる点も大きな魅力です。
手法4:リファクタリング
リファクタリングとは、システムの内部構造を現在の状況に対応できるように最適化する手法です。コードがより整理され理解しやすくなることで、他の開発者や将来の自分がコードを読み解く際に迷うことが少なくなり、保守性が向上します。
関数やモジュールを分割し独立した部品として機能させることで、コードの再利用性が高まり、新しい機能を追加する際にも既存のコードを活用できるため、開発時間の短縮につながります。
製造業のシステムでは、最適化されたコードによってシステムのパフォーマンスが向上し、予期しないエラーの発生も防げるため、長期的に見てシステムの安定性と信頼性が向上する効果も期待できます。
ただし、リファクタリングはあくまで内部構造をシンプルにするだけなので、不具合の調整や機能追加などは行わない点に注意が必要です。
手法5:リライト
リライトとは、既存のソフトウェアと同じように動作するソフトウェアを、新しいプログラミング言語やライブラリを用いて、新しい動作環境向けに開発し直す手法です。
ITシステムの古い開発言語を新しいものに書き換えることで、レガシーシステムにおける既存機能はそのままで、より使いやすい開発言語に移行できます。
製造業では、COBOLなどの古い言語で書かれたシステムをJavaなどの現代的な言語に変換することで、将来的なモダンアプリケーションアーキテクチャの活用が可能になります。
リライトのメリットとして、リプレースにかかるコストを抑えられるほか、新しいデジタル技術への対応やセキュリティ性の向上が見込めます。
ただし、基本構造はそのままなので最適化されるとは限らず、専門スキルを持ったデジタル人材が必要になる点は課題となるでしょう。
製造業のモダナイゼーション成功事例3選
ここからは製造業におけるモダナイゼーションの成功事例を3つ紹介します。
順番に見ていきましょう。
事例1: 製鉄所の基幹システム刷新
ある大手製鉄会社では、約5,000万ステップという膨大な規模の基幹システムをオープン環境へ移行することに成功しました。
従来は富士通製のメインフレーム(大型コンピュータ)上で稼働していたCOBOLプログラムを、サポート終了前にJava言語へ完全移行したのです。
通常であれば膨大な時間と費用がかかる大規模システム刷新を、「ソースコードの自動変換」という手法を採用することで、4年半という短期間で完了させました。
この取り組みの特徴は、システムを一から作り直すのではなく、長年培ってきたノウハウを継承しながら新しい基盤で稼働させる点にあります。
製造業の基幹システムは競争優位性の源泉であるため、蓄積されたノウハウを保持しつつ最新技術との連携を可能にした点が高く評価されています。
事例2:複数工場の仮想統合によるデジタル改革
ある電機メーカーでは、地理的に離れた2つの工場を「バーチャル・ワンファクトリー」として仮想的に1つの工場に融合する取り組みを実施しました。
この取り組みでは「部門間融合」「生産融合」「試作プロセス融合」「IT融合」の4つの施策を推進し、外部環境変化への対応力を高めることに成功しています。
具体的には、各工場で異なっていた設計情報を共通化し、生産状況の可視化によって工場間の負荷分散や得意技能の活用を可能にしました。
また、大量生産に強い工場と多品種少量生産に強い工場の特性を活かし、試作と量産の効率化を実現しています。
この事例の成果として、コスト削減だけでなく、人材や技術の交流が活発化し、多様な生産ニーズへの対応や人手不足への対策が可能になりました。
事例3:業務プロセス可視化による中小製造業の変革
ある中小製造業では、「プロセス参照モデル」を活用して自社の業務プロセスを可視化し、デジタル技術活用の具体的な取り組みにつなげました。
事業の高付加価値化を目指す中で、多様な生産形態が混在し業務プロセスが複雑化していたため、業務の整流化が必要だと判断したのです。
外部の専門家や同業の中小企業との情報交換を積極的に行いながら、自社に合ったプロセス整理を行い、必要なシステムツールの小規模開発を進めました。
この取り組みにより、部署間でのデータ手動転記といった非効率なプロセスが明らかになり、データの自動流用による改善が実現しました。
また、製品設計・生産設計への注力シフトや、生産形態の特性に合わせた事業の位置づけ変更など、ビジネス面での成果も生み出しています。
成功率を高めるモダナイゼーションの導入プロセス5ステップ
成功率を高めるモダナイゼーションの導入手順は、以下の5ステップです。
1.現状分析と対象システムの明確化
2.目標設定と評価基準の確立
3.適切な手法の選択
4.移行計画の策定とリスク管理
5.従業員教育と継続的な改善体制づくり
順番に見ていきましょう。
ステップ1:現状分析と対象システムの明確化
まずは社内のIT資産を可視化し、システムの現状を正確に把握しましょう。
社内で使用している全てのシステムをリストアップし、各システムがどの業務で利用されているか、構築場所(オンプレミスかクラウドか)などの情報を整理します。
現行システムの運用状況やユーザー部門の利用実態を調査し、「変えられる部分」と「変えられない部分」を明確に区分けすることが重要です。
この分析により、どのシステムを優先的に刷新すべきか、業務への影響度はどの程度かを判断する基準が得られます。
例えば、セキュリティリスクが高いシステムや、維持費が高騰しているシステム、担当者しか理解できないブラックボックス化したシステムなどは、優先度の高い対象となるでしょう。
ステップ2:目標設定と評価基準の確立
具体的かつ定量的な目標を設定することで、モダナイゼーションの進捗を測定しやすくなります。
例えば、「生産効率を20%向上させる」「コストを10%削減する」「納期回答時間を4分の1に短縮する」など、数値化された目標を掲げると良いでしょう。
目標設定の際には、業務プロセスの最適化、効率化、柔軟性の向上、セキュリティの強化など、モダナイゼーションの主要な目的を踏まえることが大切です。
明確な評価基準を持つことで、プロジェクト完了後に成功したかどうかを客観的に判断できるようになり、関係者間での認識のずれを防ぐことができます。
ステップ3:適切な手法の選択
モダナイゼーションには、リプレイス、リライト、リホスト、リファクターなど様々な手法があります。自社の状況や目標に合わせて最適な手法を選択することが、プロジェクト成功の鍵となります。
特に重要なのは、一度にすべてのシステムを刷新するのではなく、段階的なアプローチを取ることです。
初めは基幹システムではなく、一部の業務システムから段階的に移行を進めることで、リスクを分散させることができます。
例えば、パイロットプロジェクトとして小規模なDXプロジェクトを実施し、その効果を検証してから他の部門やプロセスに拡大していく方法が効果的です。
ステップ4:移行計画の策定とリスク管理
システムの移行計画を具体的に立て、どのタイミングで何をすべきかを明確にすることが重要です。
移行期間中の業務への影響を最小限に抑えるための対策も考慮しなければなりません。
例えば、一括でシステム移行を行う場合は、システムを一時的に停止する期間が必要になりますが、停止できない場合は旧システムと新システムを並行運用する方法も検討できます。
リスク管理の観点から、移行中のトラブルに備えたバックアッププランや、万が一の際の元のシステムへの復旧手順も準備しておくと安心です。
また、スケジュール作成の際には余裕を持った計画を立てることで、予期せぬトラブルにも対応できるようにしておきましょう。
ステップ5:従業員教育と継続的な改善体制づくり
モダナイゼーションの成功には、新しいシステムを使いこなす従業員の教育が不可欠です。
定期的な研修や教育プログラムを実施し、従業員のスキルアップを図ることで、新技術への適応力を高めることができます。
具体的には、オンラインコースや専門家によるワークショップなどを通じて、従業員が新しいシステムに慣れる機会を提供しましょう。
また、モダナイゼーション後も継続的に改善を行う体制を構築することが重要です。
データを有効に活用し、リアルタイムデータの収集と分析による迅速な意思決定ができる環境を整えることで、変化の激しいビジネス環境にも柔軟に対応できるようになります。
モダナイゼーション推進における3つの確認ポイント
モダナイゼーション推進時のポイントとして、以下の3点があげられます。
- 明確な目的設定と社内共有の徹底
- 既存システムの徹底分析
- 業務プロセスの見直し
順番に見ていきましょう。
ポイント1:明確な目的設定と社内共有の徹底
モダナイゼーションを始める前に、なぜ実施するのか、どのような成果を目指すのかという目的を明確にすることが不可欠です。
「業務プロセスの最適化」「生産性向上」「データ活用の推進」「セキュリティ強化」など、自社の課題解決につながる具体的な目標を設定しましょう。
明確な目的があれば、予算規模や人員配置の決定、計画実行の過程で適切な意思決定がしやすくなります。
また、目的を社内全体で共有することで、現場からの理解と協力を得やすくなり、モダナイゼーション推進がスムーズになります。
製造業では特に、現場と経営層の認識のずれが生じやすいため、定期的な意見聴取や情報共有の場を設け、プロセス全体を通して円滑なコミュニケーションを確保することが大切です。
ポイント2:既存システムの徹底分析
モダナイゼーションを進める前に、現行システムを深く理解し、「変えなければならない部分」「変えられる部分」「変えられない部分」を明確に区分けする必要があります。
製造業のシステムは長年にわたって構築されてきた複雑なものが多く、システムのアーキテクチャ、使用技術、依存関係、データフロー、業務プロセス全体を把握することが重要です。
システムの強みと弱みを分析し、改善が必要な領域を特定することで、新システムの設計指針が得られます。
また、モダナイゼーションはシステム全体に影響を与えるため、レガシーシステムを前提として動いていたアプリケーションの操作に支障が出たり、移行過程でデータが破損したりするリスクも考慮しなければなりません。
システム全体にどのような影響があるか、リスク評価を必ず行い、適切な対策を講じることで、予期せぬトラブルを防止できます。
ポイント3:業務プロセスの見直し
モダナイゼーションの実施に先立ち、業務プロセスの見直しを行うことが重要です。
現行システムのすべての機能を新システムに移行しようとすると、膨大な手間とコストがかかるだけでなく、時代の変化に即さない業務がそのまま残ってしまう可能性もあります。
製造業では特に、長年の慣習で非効率な業務が残っていることが多いため、今の時代・これからの時代に対応していけるよう、業務改革をした上でモダナイゼーションを実施することが効果的です。
また、一度にすべてのシステムを刷新するのではなく、段階的なアプローチを取ることも重要なポイントです。
移行計画を策定し、リスクの特定と軽減策を講じた上で、段階的な実装へと進むことで、効率的かつ効果的なシステム刷新を実現できます。
製造業の基幹システムは業務の根幹を支えるものだけに、慎重かつ計画的に移行しましょう。
モダナイゼーションの今後の発展
製造現場では、見積AI、生産計画AI、画像検査AIなど様々なAI技術が実用化され、業務効率化に貢献しています。特に注目すべきは、AIとスマート製造技術の融合により、工場の自動化と効率化が飛躍的に進んでいる点です。
モダナイゼーションの主流は、リライトやリホストといった手法から、複数技術を組み合わせた段階的アプローチへと移行しています。
ビジネスの要求に応じて段階的にシステムを改善しながら、基幹システムの一部をクラウドベースに移行する手法が主流となっています。
今後は、DX人材の育成・確保がさらに重要となり、組織内でDX人材を育成する体制づくりが競争力の鍵となるでしょう。
まとめ
モダナイゼーションは製造業の古いシステムを最新技術で刷新し、業務プロセスを最適化する取り組みです。レガシーシステムによる競争力低下やセキュリティリスクといった課題を解決する手段として不可欠となっています。
成功のポイントは、明確な目的設定と社内共有、既存システムの徹底分析、業務プロセスの見直しにあります。導入プロセスは、現状分析→目標設定→手法選択→移行計画策定→従業員教育の5ステップで進めるのが効果的です。
今後はAIとスマート製造技術の融合による工場の自動化・効率化が進み、複数技術を組み合わせた段階的アプローチが主流になるでしょう。
モダナイゼーションは単なるシステム更新ではなく、製造業のビジネスモデル変革を実現する戦略的取り組みなのです。
【注目コンテンツ】
・DX・ESGの具体的な取り組みを紹介!専門家インタビュー
・DX人材は社内にあり!リコーに学ぶ技術者リスキリングの重要性
・サービタイゼーションによる付加価値の創造と競争力の強化