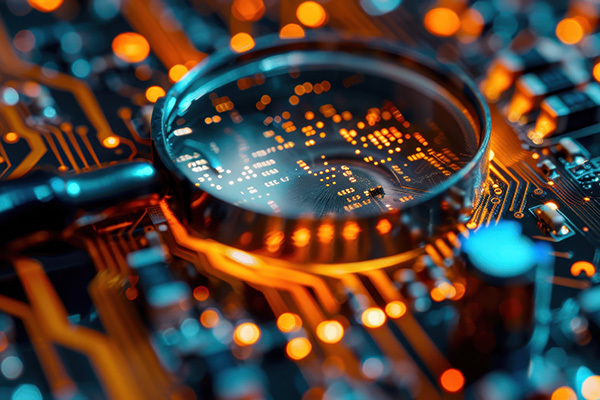
製造業において異常検知技術は、生産現場の安定稼働と品質向上に欠かせない技術です。
機械や設備の故障を未然に防ぎ、トラブルを早期に検知するこの技術は、従来の熟練作業員による目視や経験に頼る方法から、AIや機械学習を活用した高度なシステムへと進化しました。
異常検知の導入により、生産ラインの停止防止によるコスト削減、品質管理の精度向上、そして深刻化する人材不足問題への対応が可能です。
外れ値検出や変化点検出、異常部位検出といった基本的な手法から、統計的手法、機械学習、ディープラーニングまで、様々なアプローチが製造現場で活用されています。
本記事では、異常検知の基本概念から具体的な導入事例、そして実装時の注意点まで、製造業のDX推進に役立つ情報を体系的に解説していきます。
目次
異常検知とは?
異常検知とは、製造・生産現場において機械や設備が故障する前に何らかの異常を捉え、トラブルを未然に防いだり、故障した際にそれを検知したりする技術です。
従来は熟練作業員の目視や勘、あるいは温度・圧力・流量などのセンサーに閾値を設定して異常を知らせる仕組みが一般的でした。
製造業では異常検知が特に重要な理由として、機器を正常稼働させ生産を安定的に継続することが挙げられます。工場が停止すると、供給できないことによる売上機会の損失と停止による原価が同時に発生し、事業に大きな損失をもたらすからです。
近年では人手不足や品質向上の要求から、AIや機械学習を活用した異常検知システムが注目されています。
このシステムは、正常稼働時のデータをAIに学習させることで、従来の方法では発見できなかった異常状態や未知の異常を捉える可能性を持っています。
製造業で異常検知が必要な3つの理由
製造業で異常検知が必要な理由としては、大きく以下3点があげられます。
- 生産ラインの停止防止によるコスト削減
- 品質管理の精度向上と不良品削減
- 人材不足解消と技術継承の効率化
順番に見ていきましょう。
理由1:生産ラインの停止防止によるコスト削減
製造業において、機械や設備の突然の故障による生産ラインの停止は、大きな経済的損失を招きます。
異常検知技術を導入することで、設備の異常や故障が発生する前に予兆を捉え、計画的な点検やメンテナンスを行うことが可能になります。
これにより、予期せぬ機器の停止を未然に防ぎ、生産ラインの稼働率を向上させられるのです。例えば、センサーデータをリアルタイムで分析し、通常のパターンから外れるデータを早期に検知することで、重大な故障に発展する前に対処できます。
製造現場では24時間365日、安定した検知精度で監視を続けることができるため、人為的なミスによる見逃しも防止できるという大きな利点があります。
結果として、生産性の向上だけでなく、修理コストの削減や製品供給の安定化にもつながるのです。
理由2:品質管理の精度向上と不良品削減
製造業における品質管理は、企業の信頼性と直結する重要な課題です。
従来の目視検査では見逃してしまうような微細な異常も、AIを活用した異常検知システムなら高精度で検出できます。
製造ラインに設置したセンサーから得られるデータを多角的に分析することで、熟練作業員でも気づかなかった異常を客観的に検知し、不良品の発生を早期に発見することが可能になりました。特に、製品の外観検査においては、画像データを分析して不良品を特定する技術が活用されています。
こうした取り組みにより、不良品の流出を抑制し、品質向上とコスト削減を同時に実現できるのです。
さらに、データ分析に基づいて異常発生の根本原因を特定できるため、同様の問題の再発防止にも効果的に対応できます。
理由3:人材不足解消と技術継承の効率化
深刻化する労働力不足は製造業全体の課題となっています。
AIによる異常検知システムを導入することで、単純作業の自動化が進み、限られた人材を最適に配置することが可能になります。24時間体制での監視や繰り返し作業をAIに任せることで、作業員の負担を大幅に軽減できるのです。
また熟練作業員の「勘」や「コツ」といった暗黙知を数値化・データ化できることも大きな利点です。これにより、技術継承の時間を削減し、効率的な知識移転が実現します。
製造現場における様々な課題をAIによって解決することで、人員の省人化を図りながらも、品質と生産性を向上させることができるのです。
さらに、熟練者の経験に頼らない客観的な異常検知が可能になるため、人材育成の負担も軽減されます。
初心者でも分かる!異常検知の3つの基本タイプ
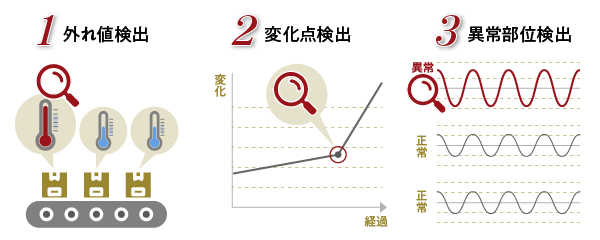
製造業では機械の故障予測や品質管理に活用され、大きく以下の3つのタイプに分類できます。
- 外れ値検出
- 変化点検出
- 異常部位検出
順番に見ていきましょう。
タイプ1:外れ値検出
外れ値検出は、全体のデータから著しく離れた値を見つける手法です。
例えば、通常の温度範囲が20~30℃の製造工程で突然40℃を記録した場合、外れ値として検知します。
この手法では、異常度を計算し、設定した閾値を超えると異常と判断するのが一般的です。
k近傍法という手法では、あるデータ点から近い順にk個のデータまでの距離を測り、その距離が大きいほど異常と判定します。
この方法は多次元データにも適用できる利点がありますが、全てのデータ間の距離を計算するため処理量が多くなる欠点もあります。
製造ラインでの不良品検出や、センサーデータの誤測定の発見に役立ちます。
タイプ2:変化点検出
変化点検出は、時間とともに変化するデータの中で、傾向が急に変わる時点を特定する手法です。
製造設備の状態が徐々に悪化し始めた瞬間や、製品品質が低下し始めたタイミングを捉えることができます。
例えば、Webサイトへのアクセスが急増した場合、その変化点を検出して原因を調査できます。
製造業では、生産ラインの稼働率改善や品質管理に活用され、工程のボトルネックを特定したり、製品仕様変更の影響を評価したりするのに役立ちます。
CUSUM法やベイズ法などの手法があり、データの特性や分析目的に応じて適切な方法を選ぶことが大切です。
タイプ3:異常部位検出
異常部位検出は、通常とは明らかに異なる動きや挙動のパターンを見つける手法です。
製造機器の振動パターンが変化した場合や、生産ラインの動作が不規則になった場合などを検知できます。
例えば、正常時は一定のリズムで動作する機械が、故障の前兆として不規則な動きを示し始めた場合に異常として検出します。この方法は、不正行為や不審な動作の検知にも応用され、製造現場では作業者の安全確保や品質維持に貢献します。
通常の状態を学習したAIが、新たに入力されたデータが正常パターンから逸脱しているかを判断するため、データが蓄積されるほど精度が向上するという特長も。
製造業で活用できる4つの異常検知の手法
製造業で活用できる異常検知の手法は、以下の4種類です。
- 統計的手法
- 機械学習アルゴリズム
- ディープラーニング
- リアルタイム異常検知
順番に解説していきます。
手法1:統計的手法
統計的手法は、データの分布や平均値、分散などを基に異常を発見する方法で、比較的少ないデータでも実施可能な手法です。
例えば、シグマ法では平均値から標準偏差の何倍かを超えた場合に異常と判断したり、移動範囲法では一定期間のデータ変動を監視したりします。
製造ラインの温度や圧力などの基本的なセンサーデータに対して閾値を設定し、通常範囲を逸脱した場合に警告を発する仕組みが代表的です。専門的な知識がなくても導入しやすく、コストパフォーマンスに優れているため、異常検知の第一歩として多くの製造現場で採用されています。
手法2:機械学習アルゴリズム
機械学習を用いた異常検知は、ある程度のデータ量がある場合に効果を発揮します。
教師あり学習では正常と異常のデータを用いて学習し、新たなデータが正常か異常かを判断します。
一方、教師なし学習では正常データのみで学習し、通常とは異なるデータを異常と判断するため、異常事例が少ない製造現場でも活用できます。
k近傍法やクラスタリングなどの手法があり、多次元データの分析も可能なため、複数のセンサー情報を組み合わせた総合的な判断ができます。
製造設備の予知保全や品質管理において、単純な閾値設定では捉えられない複雑な異常パターンの検出に役立ちます。
手法3:ディープラーニング
ディープラーニングは、画像や音声などの複雑なデータから異常を検出するのに適しています。製造業では特に、製品の外観検査や設備の異常音検知などに活用されています。
CNN(畳み込みニューラルネットワーク)やVAE(変分オートエンコーダ)、GAN(敵対的生成ネットワーク)などの手法が用いられ、人間の目では見逃しがちな微細な異常も高精度で検出可能です。
例えば、カメラで撮影した製品画像から不良品を自動判別するシステムは、検査工程の自動化や精度向上に貢献しています。ただし、導入には大量のデータと専門知識が必要であり、運用コストも考慮する必要があります。
手法4:リアルタイム異常検知
製造現場では、異常を即座に検知して対応することが重要です。
リアルタイム異常検知システムは、センサーやカメラからのデータをリアルタイムで分析し、通常とは異なる動作やパターンを迅速に検出します。
例えば、ベルトコンベアの速度異常や機械の異常振動を検知した際に即座にアラートを発することで、機械の停止や人為的なチェックを促し、大きな故障や不良品の発生を未然に防ぎます。
5Gやエッジコンピューティングの普及により処理速度が向上し、より迅速な対応が可能になっています。
このシステムにより、生産ラインの停止時間を最小限に抑え、生産効率の向上とコスト削減を同時に実現できます。
製造業における異常検知の活用事例3選
ここからは、製造業における異常検知の活用事例を3つ紹介していきます。
順番に見ていきましょう。
事例1:食品製造ラインでの不良品検出
食品業界では、製品の品質管理が消費者の安全に直結するため、AIによる異常検知技術が大きな効果を発揮しています。
ある食品会社では、ポテトの選別作業にAIを導入し、不良品の検知精度を飛躍的に向上させました。
従来の目視検査では見逃してしまうような微細な異常も、画像分析技術によって高精度で発見できるようになっています。具体的には、製造ラインに流れる食品を撮影した動画をオープンソースの深層学習フレームワーク「TensorFlow」でディープラーニングすることで、不良品を自動的に検出するシステムを構築しています。
この技術導入により、不良品の発生リスクを抑えつつ、検品作業の効率化と異常検知のコスト削減を同時に実現しました。
人間の目では確認できなかった小さな不具合も漏らさず検出できるため、製品の品質向上と消費者の信頼獲得につながっています。
事例2:飲料缶充填ラインでの故障予兆検知
飲料製造業界では、生産ラインの停止が大きな損失につながるため、故障の予兆を事前に検知する技術が注目されています。
あるビール製造会社では、缶充填ラインにAIによる異常検知システムを導入し、トラブルの抑制に成功しました。
このシステムでは、生産ライン上の膨大なセンサー情報を収集・分析し、センサー間の関係性から変化を察知する仕組みを採用しています。従来はセンサーのしきい値による単純な異常監視が一般的でしたが、詳細なデータ変化の検知には熟練作業員の経験やノウハウが必要でした。
最先端AI技術である「インバリアント分析」を活用することで、センサー同士の不変的な関係性をモデル化し、予測データと実測データの比較から「いつもと違う状態」を早期に検知できるようになりました。
この技術により、属人的な保全業務からの脱却と作業負担の軽減を実現し、熟練技術者のノウハウを継承することも可能になっています。
事例3:製造現場での作業安全監視
製造現場における労働安全は最重要課題の一つであり、AIによる異常検知技術が安全管理の強化に貢献しています。
ある製造業では、ネットワークカメラとマーカーを活用して作業員の位置をリアルタイムでトラッキングするシステムを導入しました。このシステムでは、立ち入り禁止エリアへの侵入や異常な滞留をAIが即座に検知し、管理者にアラートを送信します。
従来の安全管理では見落としがちだった危険な状況も、AIが24時間体制で監視することで事故リスクを大幅に低減しています。さらに、作業員の動線を可視化することで、最適な人員配置の検討も可能になりました。
製造現場では、機械と人間が共存する環境で安全を確保することが課題でしたが、AIによる異常検知技術の導入により、危険を未然に防ぎ、より安全で効率的な作業環境を実現しています。
異常検知導入時の3つの注意点
異常検知導入時の注意点として、以下の3つがあげられます。
- 質の高い大量のデータ収集が必要
- 現場の理解と協力体制
- 誤検知リスクへの対策と改善
順番に見ていきましょう。
注意点1:質の高い大量のデータ収集が必要
異常検知システムはAIによる機械学習を必要としているため、学習用のデータを大量に準備しなければなりません。機械学習は大量のデータの中から一定のパターンを見つけ出し、それを元に判定していくことを得意としているためです。
少量のデータでは入念に工夫しない限り偏った学習になり、現実で起こりうるさまざまなパターンに対応できなくなってしまいます。
異常検知をAIが行う際、その判断の基になるのは学習用データセットです。データセットの精度が悪ければ、異常検知ができません。
さらにAIでは現場で計測したデータを用いるため高い精度が必要になります。センサーでデータを収集する際にノイズを排除することも重要です。ノイズが異常検知の反応よりも大きかったならば、効果が得られません。
あるメーカーでは商品の需要予測を行おうとしましたが、CMのプロモーションやセールといったイベントが反映されておらず、高い精度を出せなかった事例もあります。
注意点2:現場の理解と協力体制
AIの導入を決定するのは経営陣ですが、実際に活用するのは現場の従業員です。
あるプロジェクトでAIを導入するためにデータ収集を現場に要請したところ、「今は忙しいから」といって想定したデータが収集できなかった事例も。さらに集まったデータも画像の質が悪いものばかりで、AIモデルの構築までに予定以上の時間を費やしてしまいました。時間がかかると費用がどんどん膨らみ、AI導入の担当者は頭を抱えてしまったようです。
なぜAIを導入するのか、その後現場ではどのような変化が期待できるのか、という説明をして、現場の協力体制を整えておくことが重要です。
現場を巻き込めずに、現場が望まないシステムになってしまうと、せっかく導入したAIも活用されない結果となります。
現場の声を反映していない使いにくいシステムを開発してしまったケースでは、担当者があまり効果的に活用しない結果となりました。
注意点3:誤検知リスクへの対策と改善
異常検知システムが持つ誤検出(正常を異常と判断)や未検出(異常を見逃す)のリスクには注意が必要です。
誤検出が多いと、無駄な対応が増え、作業効率が低下し、現場の信頼も損なわれる可能性があります。一方、未検出は設備故障や製品不良の見逃しに繋がり、コストや品質に直接的なダメージを与えます。
人力と比べるとかなり精度の高い異常検知システムでも、100%完璧に判定することは難しいといえます。システムの学習が足りない場合、データが少し変動するだけでも誤判定のリスクがあります。誤検知を最小限にするためには、データのノイズ除去や欠損値補完による機械学習モデルの精度向上が不可欠です。
さらに、リスク許容度を設定し、業務影響を見極めたうえで、適切な検知基準を設けることが求められます。
また、人によるモニタリングでAIの判断を検証し、システム改善に役立てる体制を整えることも大切です。
異常検知の今後の発展
異常検知技術の市場は今後も拡大していく見通しです。
製造業では予防保全の観点から、故障や不具合の予兆を早期に発見するニーズが高まっており、特に注目すべき点は、AIと機械学習の進化による技術革新です。
IoTや5Gの普及により、より多くのデバイスが接続され、2030年までに接続デバイス数は250億台を超えると予測されています。
膨大なデータからリアルタイムで異常を検知する需要が高まる中、クラウドとエッジコンピューティングを組み合わせたハイブリッド型のアーキテクチャも主流になりつつあります。
さらに、テキストだけでなく画像や音声などのマルチモーダルデータに対応したLLMの開発も進んでおり、より包括的な異常検知が可能になると期待されています。
この技術の発展により、製造業の品質改善やコスト削減だけでなく、サプライチェーン全体の効率向上にも大きく貢献するでしょう。
まとめ
本記事では、製造業における異常検知技術について詳しく解説しました。
異常検知は機械や設備の故障前に異常を捉え、トラブルを未然に防ぐ技術で、AIや機械学習の活用により精度が飛躍的に向上しています。
異常検知のおもなメリットは以下のとおり。
- 生産ライン停止防止によるコスト削減
- 品質管理の精度向上と不良品削減
- 人材不足解消と技術継承の効率化
また異常検知の基本タイプと、おもな手法は以下のとおりです。
基本タイプ | おもな手法 | 特徴 |
---|---|---|
外れ値検出 | 統計的手法、k近傍法 | 全体から著しく離れた値を検出 |
変化点検出 | CUSUM法、ベイズ法 | データの傾向が変わる時点を特定 |
異常部位検出 | 機械学習、ディープラーニング | 通常と異なる動きやパターンを検出 |
異常検知システムの導入時は質の高いデータ収集、現場の協力体制構築、誤検知対策に注意が必要ですが、適切に実装すれば製造現場の生産性と品質を大幅に向上させられます。
食品製造ラインや飲料缶充填ラインなど、さまざまな業種での導入事例も増加中です。
【注目コンテンツ】
・DX・ESGの具体的な取り組みを紹介!専門家インタビュー
・DX人材は社内にあり!リコーに学ぶ技術者リスキリングの重要性
・サービタイゼーションによる付加価値の創造と競争力の強化