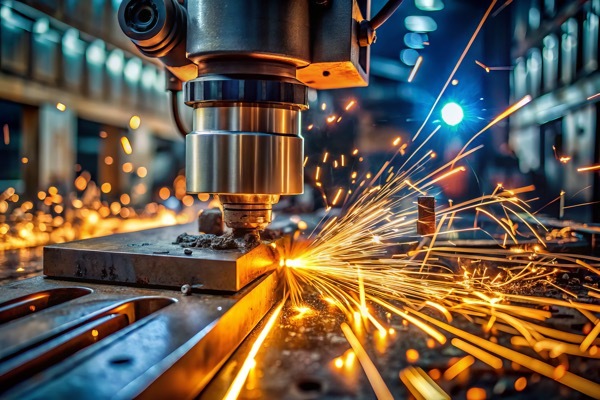
放電加工(EDM)は、高硬度材料や複雑形状の加工を可能にする精密加工技術です。DXの進展により、AIによる最適化やIoTを活用した自動化が進み、生産性や精度が飛躍的に向上しています。本記事では、放電加工とは何か、その基本原理から最新のDX技術との融合、今後の展望までを詳しく解説します。
目次
放電加工の仕組みと原理
放電加工(Electrical Discharge Machining)は、電気エネルギーを利用して金属を除去する加工技術です。特に硬い材料や複雑な形状の加工に適しており、精密加工に欠かせない技術の一つです。この項では、放電加工の定義や仕組み、メカニズム、加工液の役割、そして歴史について詳しく解説します。
放電加工の仕組みと電気放電のメカニズム
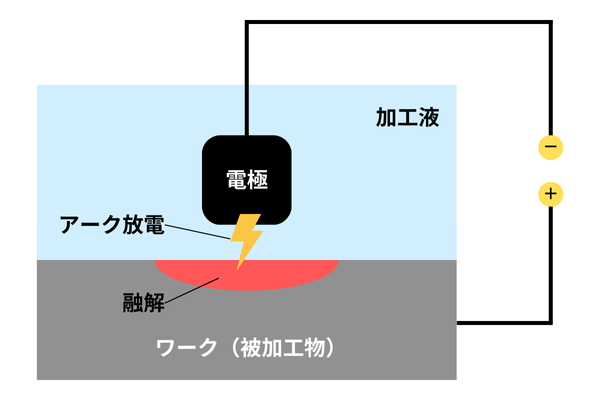
放電加工とは、電極とワーク(被加工物)の間に高電圧をかけることで発生するアーク放電(弧状に見える気体放電)を利用し、金属を融解させて除去する加工技術(除去加工法)です。切削加工のように工具が直接ワークに接触しないため、極めて硬い材料や複雑な形状の加工が可能です。
・電気放電のメカニズム
放電加工は、電気放電の特性を活用して加工を行います。そのメカニズムを詳しく見ていきましょう。
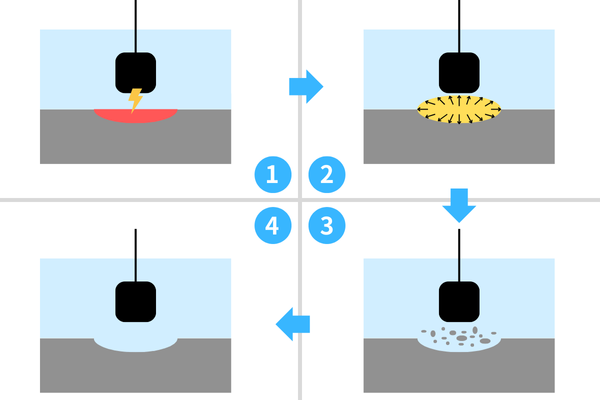
①ワークと電極の間に加工液を満たし、数十ミクロン(μm)の一定距離まで近づくと、加工液の絶縁が破壊され、放電が発生します。
②放電が発生すると、局所的な高温(約3,000℃以上)によってワーク表面が融解し、小さな金属粒子が飛散します。
③加工液がこの融解金属を洗い流します。
④次の放電が発生する準備を整えます。
これを繰り返すことで、徐々に材料が除去され、目的の形状が形成されます。
放電加工に使用する加工液の役割
放電加工において、加工液(誘電体)は重要な役割を果たします。主な機能は以下です。
・放電の安定化
電極とワークの間の絶縁を維持し、一定の条件下で放電を発生させます。
・冷却効果
放電により発生する高温を抑え、加工部位や電極の熱変形を防ぎます。
・スラッジの除去
融解した金属粒子(スラッジ)を流し去ることで、加工の安定性を向上させます。
・電極とワークの摩耗軽減
適切な加工液を使用することで、電極の消耗を抑え、精度を向上させます。
放電加工の歴史
放電加工は、比較的新しい加工技術として実用化が進んできました。、1940年代に研究が始まり、その後、実用化や技術革新を経て、現在では精密加工の分野で広く活用されています。放電加工の歴史は1940年代に始まり、その後は技術革新によって急速に発展してきました。以下にその主な進化の流れを示します。
年代 | 概要 |
1943年 | ソ連の研究者ラザレンコ夫妻が放電加工技術を開発し、加工に利用できることを発見 |
1950年代 | 商業用の放電加工機が登場し、金型製造などの分野で広く使用される |
1980年代 | CNC(コンピュータ数値制御)技術が導入され、自動化と高精度加工が可能になる |
2000年代以降 | AIやIoT技術の発展により、さらなる精密加工と省エネ化が進む |
現在では、航空宇宙、自動車、医療機器などの分野で幅広く活用され、従来の切削加工では難しい微細加工にも対応できる技術として進化を続けています。
放電加工の種類と特徴|ワイヤー・形彫り・細穴
硬い金属や複雑な形状の加工が可能な放電加工はさまざまな業界で活用されています。ここでは、放電加工の種類とその特徴について詳しく解説します。
ワイヤー放電加工
ワイヤー放電加工は、細い金属ワイヤーを電極として使用し、加工対象となる金属を融解・蒸発させながら切断する方法です。高精度な加工が可能であり、特に精密部品の製造に適しています。
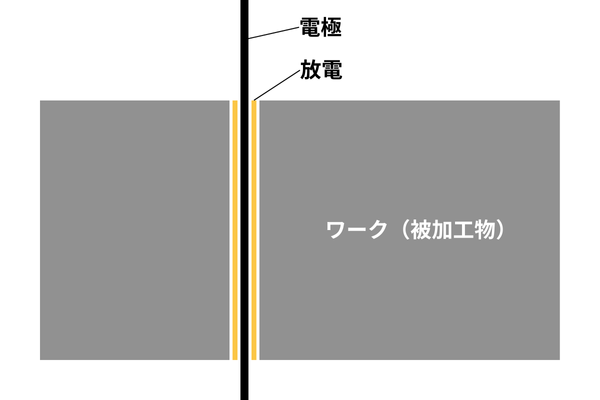
・ワイヤー放電加工の原理
ワイヤー放電加工では、直径0.05mm〜0.3mm程度の金属ワイヤー(通常は真鍮や銅)を電極として使用し、加工対象となる金属との間に放電を発生させます。放電によって発生する熱エネルギーにより、金属が局所的に融解し、加工が進行します。ワイヤーは加工中に消耗するため、加自動的に供給される仕組みが採用されています。
・ワイヤー放電加工の用途
ワイヤー放電加工は、主に次のような用途に用いられます。
精密金型の製作
航空機部品や医療機器の加工
微細部品の製造
高硬度材料の加工(タングステンや超硬合金など)
形彫り放電加工
形彫り放電加工は、電極の形状をそのままワークに転写するように加工する方法です。複雑な形状の金型や部品を高精度に加工できるため、製造業で広く利用されています。
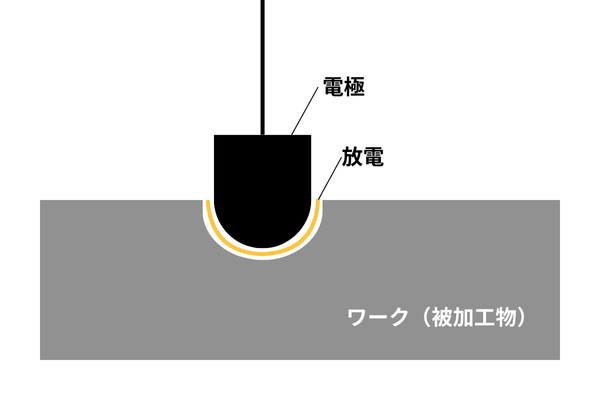
・形彫り放電加工の原理
形彫り放電加工では、導電性のある電極を工具として使用し、加工対象との間で放電を発生させます。電極は放電の熱によってワークの表面を局所的に除去しながら加工を進めます。加工液(誘電体)を使用することで、放電の制御や加工くずの排除が行われます。
・形彫り放電加工の用途
形彫り放電加工は、以下のような用途で活用されます。
金型の製作(プラスチック成形金型やダイカスト金型など)
精密部品の加工(電子機器や自動車部品)
難削材(チタン合金やニッケル合金)の加工
その他の放電加工
放電加工には、ワイヤー放電加工や形彫り放電加工以外にも、特定の用途に応じた加工法が存在します。ここでは、代表的なものを紹介します。
・細穴放電加工
細穴放電加工は、電極を回転させながら放電を行い、小径の貫通穴を加工する方法です。通常のドリル加工では困難な高硬度材料にも適用できます。
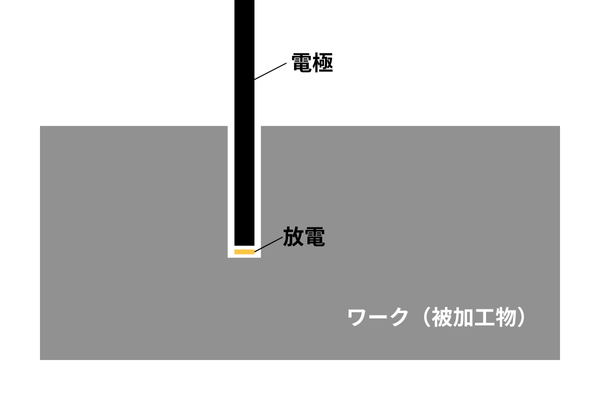
主な用途は、ジェットエンジンの燃料噴射ノズルの穴あけ、精密フィルターの製造、微細電極の製作などがあります。
・放電加工の複合加工
放電加工と他の加工方法を組み合わせることで、より高精度な加工が可能になります。例えば、放電加工と研削加工を組み合わせた方法などがあります。主な用途は、超高精度な部品加工、極小部品の製造、高効率な微細加工などです。
放電加工は、金属加工の分野で非常に重要な技術の一つです。それぞれの加工方法の特徴を理解し、適切な用途で活用することで、精密加工の可能性を広げることができます。
放電加工のメリット・デメリット
放電加工は、電気エネルギーを利用して金属を除去する加工方法であり、他の切削加工では難しい高硬度材料や複雑な形状の加工が可能です。しかし、一方でデメリットも存在します。ここでは、放電加工のメリットとデメリットについて詳しく解説します。
放電加工の5つのメリット
放電加工には、以下のような5つのメリットがあります。
1.高硬度材料の加工が可能
放電加工は、超硬合金やタングステン、チタン合金などの高硬度材料にも適用できます。通常の切削工具では加工が困難な材料でも、放電の熱エネルギーによって精密な加工が可能です。
2.複雑形状の加工が可能
放電加工では、細かい形状や複雑な内部構造を持つ部品の加工が可能です。特に、ワイヤー放電加工や形彫り放電加工を活用することで、自由度の高いデザインを実現できます。
3.精密な加工が可能
放電加工は、高い寸法精度と表面仕上げが求められる加工に適しています。精密金型や電子部品の製造において、微細な加工が可能なため、多くの業界で活用されています。
4.非接触で対象物への負荷が少ない
放電加工は、電極とワークが直接接触しないため、加工対象物に機械的な負荷がかかりません。そのため、薄肉部品や脆い材料の加工にも適用できます。
5.冷却状態で加工が可能
放電加工では、加工液を使用するため、熱影響が抑えられます。これにより、熱による歪みや変形を最小限に抑えながら加工を進めることができます。
放電加工の5つのデメリット
放電加工にはメリットが多い一方で、以下のような5つのデメリットもあります。
1.加工速度が遅い
放電加工は、一般的な切削加工と比較して加工速度が遅いのが欠点です。放電による金属除去は局所的かつ断続的に行われるため、短期間での大量生産には不向きな場合があります。
2.熱影響層が発生する
放電加工では、高温の放電エネルギーによって金属が融解するため、加工面には熱影響層(加工変質層)が形成されることがあります。この層が強度や精度に影響を与える可能性があるため、必要に応じて追加の研磨や処理が求められます。
3.電極の消耗がある
放電加工では、工具電極も放電によって消耗します。特に形彫り放電加工では、電極の消耗が加工精度に影響を及ぼすため、電極の材質や形状を工夫する必要があります。
4.電極の作成が必要(形彫り放電)
形彫り放電加工を行う場合、加工する形状に合わせた電極を事前に作成する必要があります。電極の設計・製作に時間とコストがかかるため、極端な少量生産ではコストに見合わない可能性もあります。
5.加工の向きが限定される(ワイヤー放電)
ワイヤー放電加工では、ワイヤーが垂直に設置されているため、加工形状に制約が生じる場合があります。特に、立体的な形状を加工する際には、他の加工方法と組み合わせる必要が出てきます。
放電加工は、高硬度材料や精密加工に適した加工方法ですが、加工速度やコストの面で注意が必要です。用途に応じて適切な加工方法を選択するようにしましょう。
4分野での放電加工の用途事例
放電加工は、さまざまな業界で活用されている精密加工技術です。特に、高硬度材料や複雑形状の加工が求められる分野でその威力を発揮します。ここでは、放電加工がどのように活用されているのか、具体的な事例を紹介します。
【金型製造】金型の精度向上・長寿命化
放電加工は、金型製造において欠かせない技術の一つです。特に、プラスチック成形やダイカスト用の金型は、高い精度と耐久性が求められるため、放電加工が適しています。例えば、形彫り放電加工では、複雑な金型のキャビティ(金型の凹側部分)を高精度に加工可能です。ワイヤー放電加工では、微細なエッジや薄肉部の加工が実現できます。
焼入れ鋼、超硬合金の加工が可能で、耐摩耗性の高い金型を製作可能です。放電加工を活用することで、金型の精度向上や長寿命化が図られ、製品品質の向上にもつながります。
【航空宇宙産業】安全性につながる精度や耐久性
航空宇宙産業では、耐熱性や高強度が求められる特殊材料を使用することが多く、放電加工が有効な手段となります。特に、チタン合金やニッケル基合金といった難削材の加工に適しています。また、タービンブレードやエンジン部品の精密加工に活用されます。
航空機部品の精度や耐久性は安全性に直結するため、高精度な加工が可能な放電加工が多く採用されています。
【医療機器製造】安全性と機能性を実現
医療機器の製造では、微細加工やバリのない滑らかな仕上げが求められます。放電加工は、その精密性から医療分野でも活用されています。
例えば、微細電極を用いたカテーテル部品や手術器具の加工に適しています。インプラント用のチタンやコバルトクロム合金の加工も可能です。バリの発生が少ないため、仕上げ工程の負担が軽減できます。
医療機器は人体に直接関わるため、精密で高品質な加工が必須です。放電加工を活用することで、安全性と機能性を兼ね備えた製品が製造されています。
【自動車産業】性能向上や燃費改善
自動車産業では、エンジン部品やトランスミッション部品など、耐摩耗性や高精度が求められる部品の製造に放電加工が活用されています。
具体的には、インジェクターの噴射ノズルなど、微細な穴加工に使用されます。またギアやベアリングの高精度加工もできます。軽量化と高強度化を両立する難削材(超硬合金など)の加工に適しています。
自動車の性能向上や燃費改善には、精密な部品加工が不可欠です。放電加工の活用により、より高性能な車両の開発が進められています。
このように、精密加工が求められるさまざまな業界で放電加工は重要な役割を果たしています。
放電加工の未来展望と最新技術
放電加工技術は進化を続けており、AIの活用やレーザーとの融合、自動化・省力化などの分野で大きな進展が見られます。ここでは、放電加工の未来展望と最新技術について解説します。
・AIを活用した放電加工で技術者不足の解消へ
AI技術の発展により、放電加工の効率や精度が飛躍的に向上しています。加工条件の最適化をAIが自動で判断し、最適な電圧や放電間隔を設定することで、AIが放電条件を最適化することで、不良品発生率が減少し、加工精度のばらつきも抑制されるとされています。
加工履歴をデータベース化し、より高度な加工ノウハウを蓄積できるため、AIによるプロセス最適化によって熟練技術者の経験に頼らずとも、高品質な加工を実現できる可能性を秘めています。
・レーザー複合放電加工で高速加工が可能
放電加工とレーザー加工を組み合わせた「レーザー複合放電加工」は、より高精度かつ高効率な加工を可能にします。例えば、レーザーの熱エネルギーを活用することで、放電加工単独では難しい微細加工が可能です。放電加工の電極摩耗を低減し、より長寿命な加工も実現できます。
さらに、高速加工が可能となることで、生産性の向上につながるでしょう。この技術は、半導体や精密機器の分野で特に期待されています。
・微細放電加工の進展でナノレベルの加工ができる
ナノレベルの加工が求められる分野では、微細放電加工の技術革新が進んでいます。具体的には、マイクロメートル単位の精度で微細穴や溝を形成可能です。生体適合材料や特殊合金への適用が進み、医療分野や精密部品の製造に寄与します。高精度センサーや電子部品の製造にも応用が広がるでしょう。
微細放電加工は、次世代の電子機器や医療機器の製造に不可欠な技術として注目されています。
・放電加工の自動化・省力化
製造業の自動化ニーズの高まりに伴い、放電加工の自動化・省力化が加速しています。
例えば、ロボットや自動搬送システムと組み合わせた完全無人加工ラインの導入が可能です。IoT技術を活用することによりリアルタイムで加工状態を監視・制御できます。省エネルギー型の放電加工機の開発により、コスト削減と環境負荷低減が実現されるでしょう。
今後、放電加工の自動化技術が進展することで、より効率的で持続可能な製造が期待されています。
放電加工の未来は、AIやレーザーとの融合、微細加工技術の進化、自動化・省力化の推進によってさらに発展していくでしょう。
放電加工に関するQ&A
放電加工についてよくある質問に回答します。加工可能な材料、費用、オペレーターとしてのキャリアパスについて詳しく解説しましょう。
Q.放電加工で加工できない材料はありますか?
放電加工は、電気を通す材料であれば加工可能ですが、絶縁体の材料は加工ができません。具体的には、樹脂やセラミックス(通常のプラスチック、ゴム、ビニール)などの非導電性材料です。
ただし、一部の特殊材料(高抵抗のセラミック系金属など)は、導電処理を施すことで加工可能になる場合もあります。導電性のある金属でも、極端に低融点のものは加工中に形状が崩れやすいため注意が必要です。
Q.放電加工の費用はどのくらいかかりますか?
放電加工の費用は、加工の種類や精度、加工時間によって異なります。例えば、一般的なワイヤー放電加工は数千円〜数万円程度と言われています。
微細加工や高精度加工が求められる場合は、加工費用が高くなる傾向にあります。加工材料や電極の消耗コスト、設備の維持費も費用に影響を与えるでしょう。
具体的な見積もりを取る際には、加工業者と詳細な仕様を相談することが重要です。
Q.放電加工のオペレーターになるにはどうすればいいですか?
放電加工のオペレーターになるためには、基本的な専門技術の習得、金属加工の知識と経験が求められます。
具体的には、工業高校や専門学校で機械加工・電気加工の基礎を学ぶことです。その後、企業での実務経験を積みながら、放電加工機の操作技術を習得します。国家資格として「放電加工技能士」の取得を目指すとキャリアアップにつながるでしょう。
経験を積むことで、より高度な加工技術やプログラミングスキルを身につけることができます。
次世代のものづくりを支える重要な技術「放電加工」
放電加工とは、電気を利用して金属を精密に加工する技術です。DXの進化により、AIによる加工条件の最適化やIoTを活用したリアルタイム監視が可能になり、より効率的で高精度な加工が実現されています。従来の課題であった加工速度やコストの問題も、新技術の導入で改善が進んでいます。放電加工とDXの融合は、製造業の競争力を高め、次世代のものづくりを支える重要な鍵となるでしょう。
【注目コンテンツ】
・DX・ESGの具体的な取り組みを紹介!専門家インタビュー
・DX人材は社内にあり!リコーに学ぶ技術者リスキリングの重要性
・サービタイゼーションによる付加価値の創造と競争力の強化