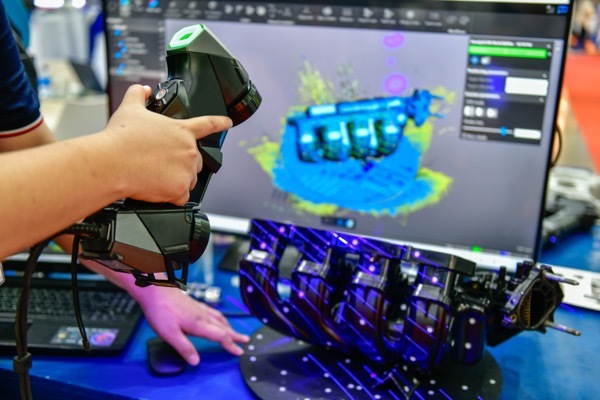
三次元測定機(CMM:Coordinate Measuring Machine)は、高精度な寸法測定が可能で、幾何公差の管理や品質保証の分野において不可欠な存在として、製造業の現場に根付いています。従来は接触式の大型の測定機でしたが、現場のニーズはさらに進化しています。
人手不足、作業の属人化、測定業務の効率化、さらには品質データのDX(デジタルトランスフォーメーション)対応など、多くの課題を背景に、非接触式かつ3Dスキャン機能を備えた三次元測定機が新たな選択肢として注目を集めています。
本記事では、三次元測定機の基礎から接触・非接触式それぞれの特徴、導入メリット、そして製造現場の課題をどう解決できるのかまで、実践的な視点でわかりやすく解説します。
三次元測定機とは?
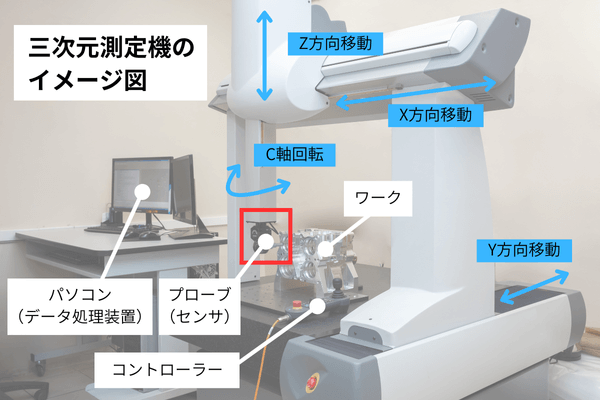
製造業の現場では、製品の精度や安全性を確保するために、寸法測定は欠かせない工程の一つです。中でもミクロン単位の寸法誤差が品質に直結する業界では、手作業によるノギスやマイクロメーターだけでは対応が難しくなっています。そこで導入されてきたのが「三次元測定機」です。
三次元測定機は、対象物の形状や寸法をXYZ軸に基づいて高精度に測定する機器で、幾何公差の管理や設計図との照合、品質保証などに広く活用されています。
三次元測定機の種類:接触式と非接触式
従来の接触式三次元測定機は、プローブと呼ばれる測定針をワークに直接触れさせて測定点の座標を取得する方式です。一点一点を正確に測定できるため、幾何公差の評価に強く、特に金属部品や精密機械など、極めて高精度が求められる現場では現在も中心的な存在です。
一方で、非接触式の三次元測定機は、レーザーや光学センサーを用いて、ワークに触れずにスキャンしながら形状全体のデータを取得します。スキャンによって数十万〜数百万点の測定点を一度に記録できるため、測定時間を大幅に短縮しながら、形状の全体把握や3Dモデル化が可能となります。
この非接触式の進化は、単なる測定方式の違いにとどまりません。人手不足や技術継承の難しさ、紙ベースの記録作業の非効率さといった、現場が抱える構造的な課題の解決につながる手段として、DX文脈での導入が進んでいます。後ほど詳しく解説します。
三次元測定機の定義
三次元測定機は、XYZ軸を基準にワークの寸法や形状を高精度に測定する装置です。接触式ではプローブを用いて特定の点を測定し、座標データを解析することで寸法を算出します。一方、非接触式ではレーザーや光学センサーを用いて、ワーク全体をスキャンしながら形状データを取得します。測定データはデジタル化され、CADデータとの比較や品質管理のために活用されます。
ノギスやマイクロメーターとの違い
ノギスやマイクロメーターは、製造現場で一般的に使われる測定工具ですが、測定範囲や精度に限界があります。
たとえば、測定できるのは長さ・直径・厚みなど限られた部位にとどまり、複雑形状の全体測定には対応できません。また、作業者の技量によって誤差が生じやすく、測定値のばらつきも課題です。さらに、測定結果の記録や管理は手作業が主流で、デジタル化やDXへの対応も難しいという実情があります。
一方、三次元測定機はこれらの課題を大きく解決します。複雑な形状のワークでも全体の座標データを取得でき、データはデジタル化された状態でCADや品質管理システムと連携可能です。また、測定者によるばらつきが少なく、誰が測っても同じ結果が得られるという信頼性も特長です。
特に、非接触式は測定時間を短縮しながら精密な3Dデータを取得できるため、DX推進にも適しているという点で注目されています。
製造業での活用シーン
三次元測定機は、以下のような業界で幅広く活用されています。
- 自動車業界:エンジン部品や車体パネルの精密測定
- 航空宇宙業界:複雑な曲面を持つ部品の品質管理
- 医療機器業界:人工関節やインプラントの寸法管理
- 金型・鋳造業界:リバースエンジニアリングや摩耗チェック
特に、非接触式の三次元測定機は、従来測定が難しかった柔らかい素材や、大型ワークの迅速な測定に適しているため、導入が進んでいます。
このように、三次元測定機には接触式・非接触式の2種類があり、それぞれの特徴やメリットを理解した上で、自社のニーズに適した測定機を選ぶことが重要です。
次の章では、三次元測定機の種類ごとの特徴を詳しく解説していきます。
三次元測定機の測定原理
三次元測定機は、XYZ軸を基準に対象物の座標情報を取得し、寸法や幾何公差を高精度に評価する装置です。測定方法にはいくつかの種類があり、用途や求める精度、作業効率に応じて適切な方式を選択する必要があります。ここでは、代表的な測定原理について解説します。
・接触式(タッチプローブ方式)
まず、最も伝統的で広く普及しているのが、接触式(タッチプローブ方式)です。これは、測定針(プローブ)をワークの表面に直接接触させ、接触点のXYZ座標を取得する方式で、非常に高い精度が得られるのが特長です。
特に、幾何公差の評価や加工精度の確認には欠かせない手法として、現在も多くの現場で使われ続けています。ただし、1点ずつの測定となるため、広範囲の測定には時間を要するほか、柔らかい素材や微細な構造物には不向きです。
・非接触式(レーザー・光学センサー方式)
これに対して、近年急速に導入が進んでいるのが、非接触式の測定方式です。レーザーや光学センサーを用いてワークをスキャンすることで、接触することなく形状情報を取得できます。
測定スピードが格段に速く、一度の操作で数十万点以上の座標を取得することが可能なため、測定時間の短縮や作業負荷の軽減に大きく貢献します。また、複雑形状や柔らかい素材、大型ワークなど、接触式では扱いにくい対象にも柔軟に対応できます。
・スキャニング測定(連続測定方式)
さらに、近年では“スキャニング測定”と呼ばれる連続的な測定方式も広がりを見せています。これは、接触式プローブやレーザースキャナを用いながら、連続的にワーク表面をなぞるように測定する方式で、点単位ではなく曲面や形状全体の変化をデータとして取得できるのが特長です。
点の集合だけでなく、面の連続性や形状の傾向を把握したい場合に有効です。
・測定データの可視化とCAD連携
これらの測定原理によって取得されたデータは、測定ソフトウェア上でリアルタイムに可視化・解析され、CADデータとの比較も可能です。設計値との差異を自動的にハイライト表示したり、測定レポートを自動出力したりといった機能も整っており、測定工程のデジタル化・自動化が加速しています。
このように、三次元測定機の測定原理は進化を遂げており、従来の「高精度な点の測定」から、「面や形状全体の高速デジタルスキャン」へと広がりを見せています。
次に、こうした測定原理を支える三次元測定機の構造タイプや特徴について、より具体的に見ていきましょう。
三次元測定機の主な分類
三次元測定機は、測定方式(接触・非接触)だけでなく、装置の構造や設置形態にもいくつかのタイプがあります。それぞれ、測定精度・作業スペース・可搬性・対応ワークサイズなどに違いがあり、導入現場の条件に応じた選択が求められます。
ここでは、代表的な構造タイプを4つ取り上げ、それぞれの特長と活用シーンについて解説します。
・ブリッジ型
最も広く普及しているのがブリッジ型の三次元測定機です。固定されたベース上に測定テーブルがあり、その上を橋のような構造(ブリッジ)で測定ヘッドが移動する構造を持ちます。剛性が高く、安定性に優れるため、接触式の高精度測定に最適とされています。
汎用性が高く、ワークサイズも中型程度までであれば対応可能。自動車部品や金型、精密機械加工品の検査工程など、幅広い分野で使用されています。ただし、据え置き型であるため、設置スペースの確保や振動対策が必要になる点には留意が必要です。
・アーム型
アーム型は、可動式の多関節アームを用いた構造で、自由度の高い測定動作が可能なタイプです。アームの先端に接触式プローブや非接触スキャナを装着し、複雑形状や大型ワークの細部まで柔軟にアクセスできるのが大きな特長です。
また、設置が簡単で可搬性が高く、ラインサイドや組立工程でのスポット測定にも対応できます。操作性にも優れ、作業者が実際にアームを動かして測定するスタイルが一般的で、CADと連携した測定フローの構築もスムーズです。
・ガントリー型
ガントリー型は、非常に大きなワークを高精度に測定するための構造で、測定テーブルの上を門型の大型フレーム(ガントリー)が移動しながら測定を行います。航空機の構造部品や産業用設備など、サイズも重量もある製品の検査に用いられます。
このタイプは、広い測定範囲と高い剛性を両立しており、大型でも細部まで安定した精度を確保できるのが特長です。ただし、導入には設置スペースや設備投資の面で相応の準備が必要であり、大手製造業の本格的な検査室などで採用されるケースが多く見られます。
・ポータブル型
ポータブル型は、軽量で可搬性に優れた三次元測定機で、測定対象のある現場へ持ち込んで、その場で計測が可能なタイプです。近年は、非接触型の3Dスキャナや小型アーム型CMMがこのカテゴリに多く含まれます。
設備の設置が不要で、立ち上げや操作も比較的簡単なため、初めて三次元測定機を導入する企業でも扱いやすい点が魅力です。製品検査だけでなく、リバースエンジニアリングや修理前の形状確認など、幅広い現場用途に対応できます。
それぞれの構造タイプには明確な特性があり、どの方式が最適かは、測定対象・精度要求・作業環境・リソース状況によって異なります。
次章では、これらの機器を導入することで製造現場にどのようなメリットが生まれるのか、実務の課題と結びつけて考察していきます。
三次元測定機の導入メリット
製造業の現場では、「測定は最後の砦」とも言われるくらい、品質管理において重要な役割を果たします。加工精度がいくら高くても、測定がずさんでは「本当にこの部品は基準を満たしているのか?」と誰も確信を持てません。
従来の現場では、「測定値が作業員によってバラつく」「複雑な形状は測れない」「記録が手書きでミスが発生する」といった悩みを抱えていることが多いです。そこで三次元測定機を導入することで、測定精度の向上、作業の効率化、コスト削減といった大きなメリットが得られます。
品質管理の向上 「測定ミスをゼロに近づける」
製造現場では、たった数ミクロンのズレが「不良品」と「合格品」を分ける決定的な差になることもあります。測定が不正確だと、設計通りに作られたはずの部品が規格外と判断されてしまったり、逆に基準を満たしていない部品が出荷されるリスクも生まれます。
・ミクロン単位の精密測定が可能
たとえば、自動車のエンジン部品や航空機の構造部品など、わずかな寸法の狂いが大きな影響を与える業界では、ミクロン単位の測定精度が求められます。三次元測定機を使えば、XYZ軸に基づいた正確な寸法測定ができ、「測定する人によって数値が変わる」ことが低減できます。
・測定誤差の低減による製品精度向上
手作業の測定では、どうしても「測り方のクセ」や「測定環境」による誤差が出てしまいます。三次元測定機を導入すれば、どの作業員が測定しても同じ結果が得られるため、品質が安定します。
・リバースエンジニアリングへの活用
こうした現場の悩みを解決できるのが、非接触型三次元測定機による3Dスキャンです。ワークをスキャンすれば、現物の形状をそのままデータ化し、新たにCADデータとして活用できます。金型修正や古い部品の復元にも役立つため、ものづくりの可能性が広がります。
関連記事:リバースエンジニアリングとは?実践方法や適法性を解説
測定の効率化 「測る時間を減らして、生産性を上げる」
三次元測定機を導入すれば、測定スピードが向上し、作業の流れをスムーズにできます。
・測定時間の短縮と人的ミスの削減
従来、ノギスやマイクロメーターで測っていた作業を三次元測定機に置き換えることで、測定時間を大幅に短縮できます。特に非接触型のレーザースキャナなら、一瞬で広範囲の測定が完了するため、「1点ずつ測る手間」がなくなります。また、手書きで記録していた測定データも自動で保存されるため、入力ミスや記録漏れといった人的エラーもゼロに近づきます。
・測定データの自動保存・分析
測定結果をデジタルデータとして記録し、自動で蓄積・分析できます。トレーサビリティも確保されるため、「いつ」「誰が」「どの測定をしたのか」もすぐに確認できます。
・CAD/CAMとのデータ連携で工程全体の最適化
測定結果をCADデータと照合することで、「設計通りに加工されているか」をリアルタイムで確認可能。これにより、加工精度の向上だけでなく、製造工程全体の最適化が進みます。
関連記事:CAM/CADとは?CAEとの違いや製造業での活用方法を解説
コスト削減 「無駄をなくし、利益につなげる」
測定ミスによる不良品が増えれば、それだけコストも膨らみますが、材料の無駄や作業コストを削減し、結果的に利益の最大化につながります。
・不良品の削減による材料ロス低減
こうした事態を減らすためには、測定の精度を上げて、早い段階で異常を検知することが重要です。加工の初期段階で寸法不良を検出し、不良品の発生を未然に防ぐことができます。
・再加工・修正コストの最小化
測定精度が向上することで、加工ミスを最小限に抑え、再加工や修正の手間を削減できます。特に、高価な材料を使う製造業では、このコスト削減効果が大きいです。
・検査工程の自動化による人件費削減
測定作業の自動化が進めば、測定のために熟練技術者を何人も割く必要がなくなり、人手不足の解消にも貢献します。また、作業負担の軽減により、現場の働きやすさも向上します。
三次元測定機の導入事例
三次元測定機は、製造業のさまざまな分野で活用が進んでいます。特に、高精度な測定を求められる業界では、製品の品質向上や工程の効率化において大きな役割を果たしています。
ここでは、業界全体での導入事例を紹介し、三次元測定機がどのように活用されているのかを見ていきます。
自動車部品メーカーにおける品質管理の向上
自動車業界では、部品の寸法精度が車両の安全性や燃費に直接影響を与えるため、厳密な品質管理が求められます。
近年、多くの自動車部品メーカーが三次元測定機を導入し、試作段階から測定データを取得することで、設計と製造のズレを早期に発見し、製品精度の向上に役立てています。また、従来の測定方法では手間がかかっていた複雑な形状の部品も、非接触型の三次元測定機を用いることで短時間で測定が可能になり、製造工程全体の効率化が進んでいます。
航空機メーカーによるリバースエンジニアリングへの活用
航空機産業では、老朽化した部品の再生や、メンテナンス時の精度管理が課題となっています。従来は、手作業による測定が主流でしたが、三次元測定機を活用することで、部品の形状データをデジタル化し、リバースエンジニアリングに活用する事例が増えています。
特に、非接触型の三次元測定機を用いることで、短時間で高精度な3Dデータを取得し、既存の設計データと照合。これにより、古い部品の復元や、金型の補修が効率的に行えるようになりました。航空機の部品は高価なものが多いため、この技術によるコスト削減効果も期待されています。
医療機器業界でのナノレベル精度の測定
医療機器分野では、ナノメートル単位の精密な測定が必要とされる製品が多く存在します。たとえば、人工関節や歯科インプラントなどは、患者ごとに異なる形状に適合させる必要があり、寸法誤差が製品の性能に直接影響を及ぼします。
三次元測定機を活用することで、製品の表面形状を高精度に測定し、設計通りの形状を維持できるかを厳密にチェック。特に、ナノレベルの測定が求められる業界では、三次元測定機の導入が標準化しつつあります。
三次元測定機を活用したDX推進
三次元測定機は、単なる寸法測定機器としての役割を超え、DXを推進するための重要なツールとしても活用が進んでいます。近年は、IoTやAI、5Gといった最新技術との連携によって、測定結果をリアルタイムで活用したり、工程全体を最適化したりといった新たな取り組みが広がりを見せています。
ここでは、三次元測定機がDXとどのように結びつき、現場にどのような変化をもたらしているのか、3つの観点から紹介します。
IoT連携によるリアルタイム測定
測定データを即時に共有・活用するために、三次元測定機とIoTを連携させる動きが広がっています。測定機に取り込まれたデータはクラウド上に保存され、製造現場だけでなく、品質管理部門や本社からもリアルタイムに確認することが可能になります。
これにより、測定作業の進捗を常時モニタリングでき、異常値の即時発見・対応が可能となりました。多拠点展開している企業においては、各拠点の測定情報を一元的に管理できる仕組みとして活用されています。
AI・ビッグデータ解析との組み合わせ
三次元測定機によって蓄積された膨大な測定データをAIやビッグデータ解析に活用する動きも進んでいます。製品の微小な形状変化や、加工誤差の傾向など、人の目では見逃しがちなパターンをAIが検出することで、プロセス改善や不良率の低減が期待されています。
測定結果の傾向から、特定の条件下で不良が発生しやすいといった予兆をつかみ、製造現場にフィードバックをかけることができるため、品質の安定化にも大きく貢献しています。
5G通信を活用した遠隔測定技術
高速・大容量・低遅延という5Gの特性を活かし、遠隔地から三次元測定機を操作・監視する技術も実用化が進んでいます。特に人手不足が課題となる地方拠点や海外工場においては、専門技術者が本社からリアルタイムで測定状況を把握し、指示を出すことで、現場の即応性と効率性が大きく向上します。
これまでのように、測定のために技術者が現場に常駐する必要がなくなるため、リソースの最適配置にも寄与しています。
このように、三次元測定機はIoTやAI、5Gといった技術と組み合わさることで、単なる検査工程の装置ではなく、製造業におけるDXの中核を担う存在へと進化しつつあります。
三次元測定機の選び方
三次元測定機は、高精度な測定が可能な反面、導入コストや運用環境のハードルも高いため、選定時には慎重な検討が必要です。導入後に「想定していたワークに合わなかった」「操作が難しくて使いこなせない」といった事態を避けるためにも、測定精度・対象物・操作性・ソフトウェア対応などを総合的に判断することが重要です。ここでは、三次元測定機を選定する際に重視すべき3つの視点を紹介します。
測定精度と用途のマッチング
まず確認すべきは、自社製品に求められる測定精度と、測定対象物の特性に適した機種かどうかです。
・測定精度
測定機のスペック表に記載される「測定誤差(MPE:Maximum Permissible Error)」を確認することが第一歩です。たとえば、精密部品や金型など、数ミクロン単位での測定が求められる場合は、±0.001mm程度の精度を持つ接触式の高精度機種が適しています。
一方、外形寸法の把握や形状全体の把握が目的であれば、非接触式のスキャナでも十分対応可能です。
・測定対象物のサイズ
測定物が大型である場合、機種によっては測定エリアに収まらない可能性があります。あくまで一般的なマッチングですが、参考にしてみてください。
測定対象 | 適したタイプ |
小型~中型部品(100mm~500mm) | ブリッジ型、ポータブル型 |
中型~大型部品(500mm~2,000mm) | アーム型、ガントリー型 |
不定形・現場設置品 | ポータブルスキャナ、アーム型 |
・ワーク材質
ワークが柔らかい樹脂やゴムなどの場合、接触測定では変形や傷のリスクがあるため、非接触式を選ぶほうが安全です。逆に、金属や硬質材料の寸法精度を厳密に確認したい場合は、接触式の安定した精度が信頼性を高めます。
操作性とソフトウェアの対応
どれだけ高性能な機種でも、現場で使いこなせなければ意味がありません。操作性の高さとソフトウェアの柔軟性は、導入後の活用度を左右する重要なポイントです。
・初心者でも扱いやすいUI
タッチパネル操作やガイド付き測定フローなど、初心者でも迷わず操作できるUIを備えた機種は、人材育成や現場定着のハードルを下げてくれます。教育コストを最小限に抑えたい場合や、多拠点展開を想定している場合は特に重視すべきポイントです。
・測定結果のデータ管理・統合
取得した測定データは、測定機本体だけでなく社内の品質管理システムやMES、ERPなどとの連携も検討する必要があります。CSV出力だけでなく、自動でレポート生成や統計処理ができるソフトウェアがあると、レポート作成の手間を大きく削減できます。
・CADとの互換性
CADとの連携も重要な要素です。多くの三次元測定機は、IGES、STEP、Parasolidなどの標準的な3D CADフォーマットに対応していますが、自社で使用しているCADとの互換性を事前に確認しておくことで、測定データの比較や設計との整合性確認がスムーズになります。
価格とコストパフォーマンスの考え方
三次元測定機の導入を検討する際、価格は大きな判断要素の一つですが、単純に“いくらかかるか”という表面的なコストだけで判断するのは危険です。実際には、以下のような複数の要素を含めたトータルコストとして捉えることが重要です。
コストを検討する際の主な視点
- 本体価格以外の初期費用(設置・周辺設備・ソフトウェアライセンス)
- 年間保守・校正費用
- 教育や操作研修にかかる時間・コスト
- 現場導入後の作業効率化による削減効果(ROI)
- 操作性・保守性・技術サポート体制によるランニングコストへの影響
特に、現場でどれだけ活用されるか=費用対効果(ROI)を評価することが重要です。「せっかく高性能な機器を入れたのに、現場で使いこなせず宝の持ち腐れに…」というケースは少なくありません。
ROI(投資対効果)をどう捉えるか?
- 検査時間が何割短縮できるか
- 測定精度が向上することで不良率・再加工がどれだけ減るか
- データ活用により、生産全体の品質がどう向上するか
こうした観点を数値化・定量化しながら、機器選定と導入規模を見極めることが、賢い投資判断につながります。
メーカー選定時に見るべきポイント
三次元測定機のメーカーは国内外に多数ありますが、価格やカタログスペックだけで比較せず、以下のような視点から信頼性や導入後の支援体制も含めて総合的に検討することが大切です。
確認すべきポイント | 内容 |
技術サポートの質 | 操作指導・トラブル対応の体制、サポート拠点の有無 |
ソフトウェア連携の柔軟性 | CAD/CAMや品質管理システムとの互換性 |
保守・校正体制 | 国内での定期校正、代替機の提供など |
導入実績 | 同業他社や同規模の企業での導入例があるか |
教育・研修体制 | 初心者向けトレーニング、マニュアルの整備状況 |
操作性 | UIの分かりやすさ、現場での習熟度の早さ |
価格はあくまでスタート地点。自社の業務や工程に本当にフィットするか、運用まで見据えた導入設計が成功のカギです。導入後の活用レベルや継続的な支援体制まで含めて、信頼できるメーカーや代理店との対話を重ねることが、最適な一台と出会うための第一歩となります。
三次元測定機は「測定」から「価値創出」へ
三次元測定機は、単なる寸法確認のための機器ではなく、製品品質を支え、製造工程全体の効率化やDX推進を支援するポテンシャルがある存在です。
接触式・非接触式の違いや装置構造ごとの特性を正しく理解し、自社の製品特性や測定環境に合った機器を選ぶことで、測定精度の向上はもちろん、工程改善やコスト削減といった経営面にも効果が広がります。
導入には慎重な検討が必要ですが、目的を明確にし、信頼できるパートナーと連携することで、三次元測定機は確かな投資対効果を生み出してくれるはずです。
【注目コンテンツ】
・DX・ESGの具体的な取り組みを紹介!専門家インタビュー
・DX人材は社内にあり!リコーに学ぶ技術者リスキリングの重要性
・サービタイゼーションによる付加価値の創造と競争力の強化