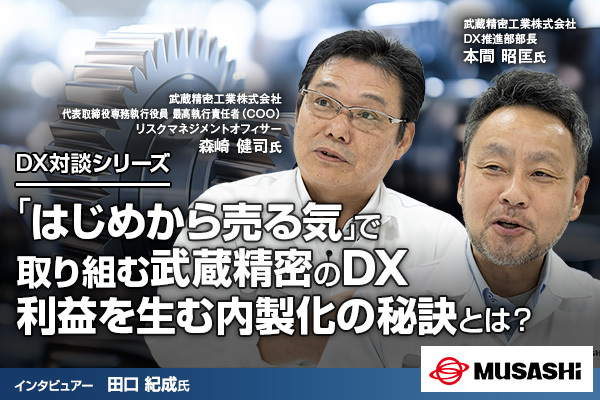
自動車部品の製造販売を手がけ、世界14ヵ国にグローバルに展開する武蔵精密工業株式会社。1938年創業の同社は、戦争や大きな災害、リーマンショックや新型コロナウイルスなど、事業継続の壁となる困難な状況や時代の変化にぶつかるたびに、新たなチャレンジを行い、成長を続けてきました。
「ものづくりDXのプロが聞く」は、Koto Online編集長の田口紀成氏が、製造業DXの最前線を各企業にインタビューするシリーズです。今回は、武蔵精密工業の代表取締役専務執行役員、最高執行責任者(COO)の森崎健司氏と、DX推進部部長の本間昭匡氏に、武蔵精密工業が取り組む「稼ぐ力」の強化、外販も視野にいれた業務効率化やスマートファクトリーの取り組みなどについて、お話を伺いました。
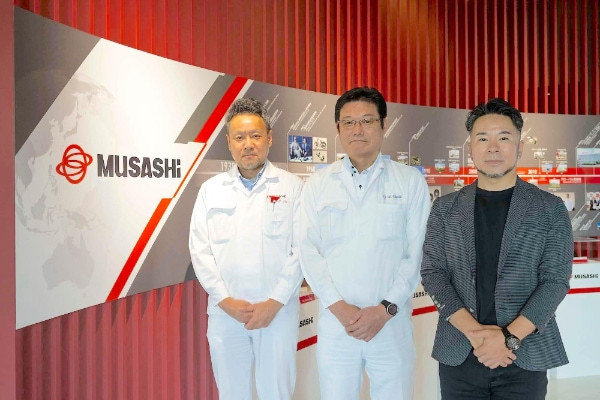
1985年、九州武蔵精密(株)入社。海外事業課主幹やMusashi Auto Parts India Pvt. Ltd.副社長などを経て、2016年、武蔵精密工業(株)入社。以後、執行役員 生産・工機事業統括や日本地域CEOなどを歴任。2020年、常務執行役員就任。2022年、専務執行役員就任。現在は、COO(最高執行責任者)やリスクマネジメントオフィサーとして、コア事業や製造部門全体の統括を担当している。
1988年にITエンジニアとしてのキャリアをスタート。空運業や電気機器メーカーなど様々なお客様のプロジェクトに携わり、インフラの構築、システムの運用・保守、アプリケーション開発、セキュリティ対策など幅広い分野で従事。2018年武蔵精密工業(株)入社。2021年、同社ITソリューション部(現:DX推進部)部長に就任。DX推進部の部長として、同社のDX基盤を整備・推進を担当している。
2002年、株式会社インクス入社。3D CAD/CAMシステム、自律型エージェントシステムの開発などに従事。2009年に株式会社コアコンセプト・テクノロジー(CCT)の設立メンバーとして参画後、IoT/AIプラットフォーム「Orizuru」の企画・開発等、DXに関して幅広い開発業務を牽引。2014年より理化学研究所客員研究員に就任、有機ELデバイスの製造システムの開発及び金属加工のIoTについて研究を開始。2015年にCCT取締役CTOに就任。先端システムの企画・開発に従事しつつ、デジタルマーケティング組織の管掌を行う。2023年にKoto Onlineを立ち上げ編集長に就任。現在は製造業界におけるスマートファクトリー化・エネルギー化を支援する一方で、モノづくりDXにおける日本の社会課題に対して情報価値の提供でアプローチすべくエバンジェリスト活動を開始している。
目次
航空機、ミシン、自動車部品と変遷する主力商品、決断と挑戦で危機を乗り越え成長してきた歴史
田口氏(以下、敬称略) 最初に改めて、御社の事業内容について教えてください。
森崎氏(以下、敬称略) 当社は自動車の部品の製造・販売を主力の事業としており、創業1938年、今年86周年を迎えます。本社は愛知県豊橋市にありますが、14ヵ国、36拠点とグローバルに事業を展開し、1万6,000人以上の従業員がいます。
戦時中だった創業当時は航空機の部品を製造していましたが、終戦を迎えて需要が一気に落ち込んだことを受け、ミシン部品の製造に転換、一時は全国シェア65%を占めていました。大きく会社の方向性を変えるきっかけとなったのが、当社の創業者とHonda(本田技研株式会社)の本田宗一郎氏との出会いです。本田氏と一緒に事業をやっていこうと決断し、ミシンの部品製造をすべてストップ。そしてオートバイの部品製造を始めました。以降は自動車部品の製造をコア事業として事業活動を続けています。
さらに、また転機が訪れます。2008年のリーマン・ショックのころ、現在の4代目社長が、今後を見据え自分たちのオリジナルブランドを作る必要があると考えたんです。世界的な大不況の中であえて投資をし、研究開発の棟を新たに作りました。その時に生みだした多様なデファレンシャル(自動車の差動装置)が今の主力部品の一つにもなっています。
その後も東日本大震災や新型コロナウイルスなど、さまざまな危機、時代の変化がありました。自分たちのアイデンティティとして、常に決断し新たな挑戦をすることでそうした危機を乗り越え、成長してきた会社であると自負しています。
田口 ありがとうございます。そうした御社の理念を100周年に向けて言葉に掲げているとお伺いしました。
本間氏(以下、敬称略) はい。私たちの考え方を表したムサシフィロソフィー、そしてそのフィロソフィーを基軸に100周年に向けた旗印として、「Musashi 100th Year Vision」を作っています。
100年ビジョンは、「Go Far Beyond・Break barriers and go on adventures!」、枠を壊し冒険へ出かけようという意味で、創業100周年を迎える2038年に向けて、限界や常識という枠を壊し、今までの延長線上ではない新しい未来を創造していこうという想いを込めています。
これらを打ち出した背景には、経営陣が抱いた大きな危機感があったと聞いています。EVの台頭によって自動車業界は100年に一度の大変革期を迎え、経営層は「このまま何もしなければ時代から取り残される」と考えたそうです。合わせて、SDGsやESGが注目を集めるなど、社会の中における企業の存在意義が改めて問われるという時代や環境の変化もありました。
そうした背景を踏まえ、これまで続けてきた自動車部品メーカーという枠を飛び越えて、テクノロジーで社会を支えるエッセンシャルカンパニーを目指すという信念のもと、このビジョンやフィロソフィーが出来上がりました。この考え方に沿って、今当社では既存事業の深化、そしてさまざまな新規事業創出に向けた取り組みを進めています。
既存事業の深化と新規事業の創出、効率化も「始めから売る気」で内製化
田口 既存のコア事業について、先ほど電気自動車の台頭というお話がありましたが、実際には、メディアで言われているほど需要は伸びていないと感じています。今後どう変化していくのかまだわからない中で、既存事業に関する業務の効率化や開発プロセス改善などもまだまだ必要となるのではないかと思うのですが、その点はいかがでしょうか。
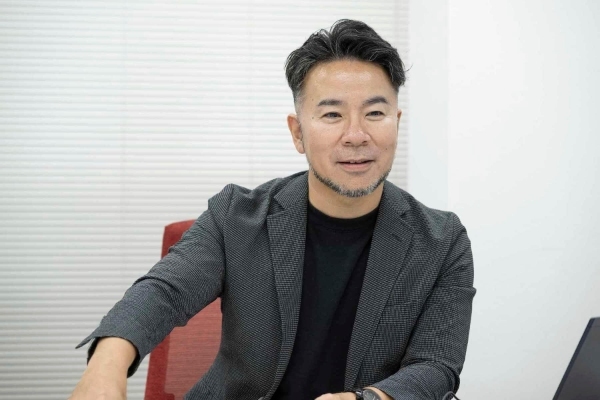
森崎 既存事業に関しては、今の形を維持しながらいかにして「稼ぐ力」を作るか、という観点で業務の効率化を図り、労務費や設備費などを削減していくための取り組みを続けています。
例えば紙一枚出すにも、人手が必要です。紙を減らそうと言うだけではダメなので、当社の製造事務所からはコピー機をなくしたんです。そうすると人はどうすればいいか考えますよね。今は現場にタブレットを240台ほど配り、そこに必要なデータを入れて承認作業をしています。紙を出す時間も人手も不要になりますし、資源の有効利用にもつながります。
工場現場での効率化も進め、人ではなくてもできる作業を機械でできるようにするなどした結果、2016年に600人いた現場の直接作業をしている社員は、現在460人ぐらいに減っています。それでも、当時よりも売り上げは20%上がっています。
いろいろと取り組んでいますが、まだまだやるべきことはたくさんあります。そうした無駄の削減だけではなく、量産立上げプロセスの最適化、得意技術の追求、サプライチェーンの最適化などによって、コア事業の拡大と収益性の向上に取り組んでいます。
田口 新規事業についてはいかがでしょうか。
森崎 新規事業もいろいろな分野で取り組んでいます。例えばSmart Industryの領域では、「AI外観検査装置」を自社(子会社)で開発し、販売も拡大しています。製品の不良など人が見てOK、NGを判断していた検査を、AIのカメラを使って、アルゴリズムで、ここまではOKと判断できるようなものですね。ほかにも、e-Mobility、Energy Solutionなど、さまざまな分野での事業展開を進めています。
田口 いろいろな業務効率化のシステムやアプリなどを取り入れる際は、生業にしている他社に外注する、内製化するなどいろいろな方法がありますが、御社の場合はどのような形ですすめているのでしょうか?
本間 基本的に内製化しています。外部にお願いしているものはほとんどありません。そもそも機械装置を作っている会社なので、作ることができるんです。しかも、当社に何が必要か、何が欲しいかというのは自分たちが一番よくわかっています。例えば業務アプリを導入してオプションがたくさんあっても、不要なものばかりになってしまうなど、無駄が多くなってしまうんです。
森崎 それから、自社の業務改善のために作り上げたものが、外にも売ることができるレベルになれば、新たな事業になりますよね。先ほどのSmart Industryの検査機器もそうですし、工場内で物を運ぶAGVも自社で作って販売しています。例えば内部の効率化目的で何かを作るときも、人間が何時間かけて行っていた作業が、このシステムを入れるとどのくらい削減でき、労務費がいくら下がるというコスト計算から、装置1台あたりの原価も当然見積もりをとっています。はじめから売る気で作っているんです。
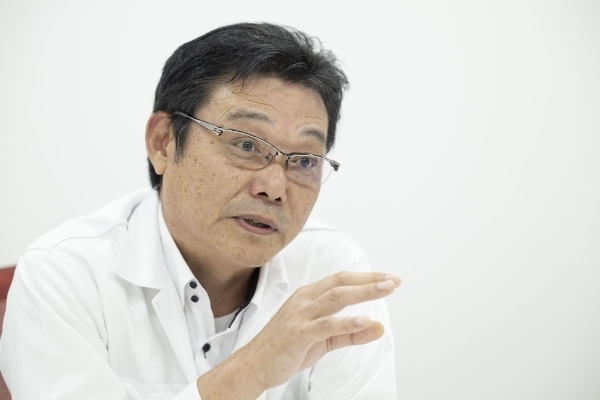
田口 そうすると、いわゆるシステムインテグレーターのような形でそれを事業にしようと取り組んでいらっしゃるんですね。業務効率化に必要なツールなどの内製化は、継続的なメンテナンスやアップデートも自分たちでやらなければならないなど、ときにコストセンターになってしまうことがあります。しかしそれが利益を生んでプロフィットセンターに位置づけることができるのだとしたら、また話が変わってきます。そういう意味でいくと、内製化も稼ぐ力になりますね。
森崎 さらに今目指しているのが、工場の見える化です。生産状況をすべて把握できるようなシステムを作り上げて、それを販売したいと考えています。まずは自社の各地の工場に実装し、足場を固めているところです。
今は自社の工場での導入ですが、信号を飛ばして、電気の出力や生産数量、サイクルタイムなどをすべてモニターで見ることができるようになっています。例えば私が出張していても、海外から工場の様子をスマホで見ることも可能です。それから、工場内のあらゆる場所にカメラが設置されていて、ほとんど工場内で映らない場所はありません。手元も映っているので、どういう作業をしてるかもわかります。このシステムを入れることで、現地でのマネジメント業務に人を充てる必要がなくなりますし、工場内で作業する人たちの安全にもつながります。
「こんなのできないかな」というリクエストに技術者が食いつき、楽しみながら試行錯誤
田口 そうしたスマートファクトリーの取り組みも、自社のためだけではなくさらに外販を目指してやっているんですね。製造業として一定の地位を築き、売り上げも伸びている中で、そうした新しい事業が次々生まれるような今の状況、それこそシステムインテグレータになろうとするぐらいの動きがなぜできているのでしょうか。背景やきっかけとしては何かあったのですか。
森崎 一つには、世の中全体の人手不足があります。当社は立地的にも人材の確保にハードルがあり、自動化や効率化を進めざるを得ないという背景がありました。それから、当社の社長も私も、無駄が嫌いなんですね。あそこでなぜ遠回りするんだろうとか、なぜ紙を出すんだろうとか気になって、じゃあ、歩かなくていい、紙を出さなくていいものを作ろうと考えるんです。さらには、自分のところに技術があるのに、なぜよそに頼むのかと思い、結果として内製化になる。ケチなんですね(笑)。
田口 エンジニアからすると、非常にやりがいのある、魅力ある環境ですよね。
本間 はい、私もメンバーも、楽しみながら仕事をさせてもらっています。私はもともと外部のIT会社に勤めていて、最初は派遣という形で武蔵精密工業の情報システム部門で仕事をしていました。それまでIT関係の企業に常駐することはありましたが、製造業で仕事をするのは初めてでした。その際に現社長の考え方に共感し、こういうところで働きたいと強く感じました。
その後、声をかけて頂き入社したのですが、やはり大きな魅力に感じたのは、新しいことをトップが率先してやる文化です。新型コロナウイルスが拡がるずっと以前から、まだ東海地区の製造業でほとんど導入実績のなかった仮想デスクトップやMicrosoft 365(旧Office 365)を使い始めています。
今、社内で使っているビジネス用メッセージアプリのSlackも、恐らく製造業ではかなり早く使い始めたと思います。おもしろいデータがあって、Slackの利用状況率を毎月見ているんですが、トップ20の中に、社長と森崎が絶対に入っているんです(笑)。若手を差し置いて、経営のトップ2がランキングの常連なんですね。新しいものを取り入れてみんなに使ってほしいと考えている自分の立場としては、もう楽しくてしょうがない。トップが使い倒しているのであれば、当然ながら現場にも浸透します。そこはすごく大事だと思います。
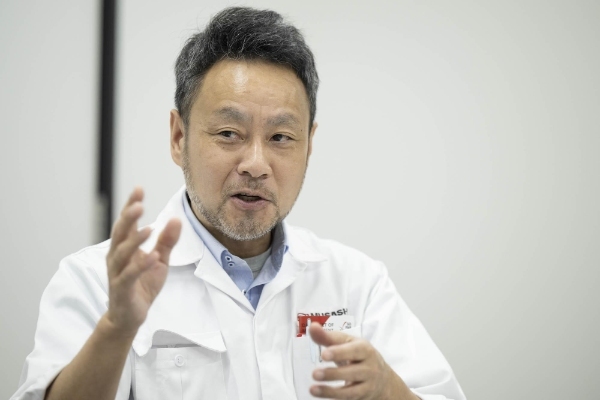
森崎 社長も私も、そういうものが大好きなんです。毎晩、寝るまでTikTokを見ています。製造業の自動化に関するおもしろい動画など、いろいろとヒントがあるんですよ。
常にこれは無駄だな、あれをもっと便利にできないかなと考えて、思いついたら「本間さん、こんなのできないかな」と声をかけています。以前、日本拠点の直接部門全体を見る担当をしていたときに、遠方とのコミュニケーションに手間がかかるため、なんとかもっと手軽につながることができないかと相談したら、事務所をつなげるものを作ってくれました。
本間 Zoomが日本でサービスを開始して間もない頃、それを利用した各工場の製造事務所の見える化を提案したんです。日本全国で音と映像を常につなぎっぱなしにして、リアルタイムのホットラインとして活用できる仕組みです。現在、九州も山梨も京都も、空間が技術的につながっていて、事務所の中で何をやっているか、いつでもわかる状態になっています。ホットライン越しに遠くの事務所に「あれどうなってる?」と聞けば、そのまま、全員に聞こえます。
田口 リクエストに対して、それを実現する方法はさまざまなものがあると思うのですが、その中でどれを選択するか、どうやって作るか、どのように決まっていくのでしょうか。
本間 部署の中に、それぞれのテクノロジーに長けたメンバーがいるので、各メンバーが専門性を生かしてアイデアを持ち寄って作り上げていきます。こんなおもしろいリクエストがあって、これを実現するためにはどうやったら最短で最廉価で実現できるか考えようと持ちかけると、みんな技術者なのですぐに食いついて、調べて提案を持ってきてくれるんです。
例えば工場内に各場所の温湿度を記録するセンサーを設置しているのですが、その時もインフラメンバーは、インフラはこうあるべき、セキュリティはこうすべき、アプリのメンバーは、BIをこういう形で実装すればできるはず、という具合に具体的な提案をしてくれました。IoT機器の基盤やセンサーを買ってきてIoT機器を作り、製造技術にお願いして3DプリンターでIoT機器用のケースを作ってもらい、完成したIoT機器を結線して、クラウドをつなげてテストして……。温度や湿度がとれた、できたとなったら実際に工場に置いてみよう、どこに置くべきか配置を考えよう、という繰り返しですね。みんな楽しんで、おもしろがって取り組んでいます。
全従業員のデジタルリテラシー向上の目的も兼ね、誰でも自分たちの手でアプリを作れるようにもなっています。例えばコロナ禍には社内のどこの部署で誰が感染しているか、何人感染者がいるのかがすぐにわかるアプリが数日で開発されて、とても重宝しましたね。
目指すは工場の「完全無人化」、ガバナンスを効かせながら継続したチャレンジを
田口 それぞれがたくさんのアプリなどを作り出すと、管理も大変だと思うのですが、何か意識していることはありますか。
森崎 たくさん作ったのはいいけれど、どこに何があるかわからないという状態は避けなければなりません。それらは台帳で管理していて、作成者が目的や概要を書き込むルールになっています。現在実際に使用されているアプリは47件あって、それらは全部一覧で見ることができる状態です。また、そもそもどこのデータなのか、正しいデータはどこから来ているのかを把握することも重要です。当社はSAPも導入済みなので、作る際は必ずSAPシステムからデータを持って来るというのも決まりになっています。
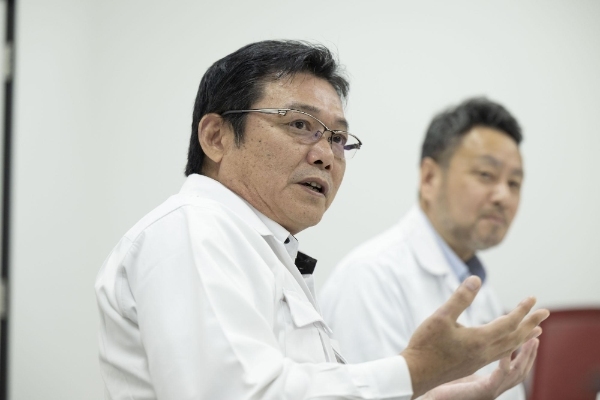
本間 SAP導入の際も、当社の場合はトップを含め、徹底的に課題を潰し込んで今の形を作り上げました。そこが中途半端で、例えば拠点ごとの固有の仕様にしてしまったために同じプロセスでも言葉が合わないなど、SAPを入れたはいいけれど活用ができていない企業も少なからずいらっしゃるのではないでしょうか。当社はグローバルで同じ英語版のSAPのテンプレートをそのまま使い、プロセスもテンプレートに合わせることで、最終的に活用できる形にすることができました。大切なのは、何が正しい元のデータなのかを明確にして統一することです。同じデータを使わないと、ダッシュボードを作っても意味がなくなってしまいますからね。
田口 それこそ、トップの固い意志がないとできないですね。最後に、今後に向けてやりたいこと、将来の展望について、お聞かせください。
本間 やってみたいことはたくさんありますが、守るところは守って、ガバナンスを効かせながらチャレンジすることが必要だと考えています。あれもこれもはできないので、プライオリティを決めながら、必要なものに取り組んでいきたいと考えています。
また、技術者が楽しむ、おもしろいと感じるかどうかも重要です。せっかく自分たちで作る力を持っているのに、一番おいしいところを外部に出して中に技術が残らない状態にならないよう、その点は今のやり方を変えずにやっていきたいと思います。
森崎 今後に向けて今注力しているのは、他に先駆けてモデルとなるような、工場の無人化です。「無人化」とよく言いますが、現在はまだ、どこかで誰かが入る必要があるんです。人間がいないとできない作業がたくさん残っているので、そこを克服することができれば、真の無人化が実現するはずです。恐らくどこもできていない完全無人化を目指して、細かなIoT化を進め、つなげ、そしてハードの自動化や監視などを含め一歩一歩進んでいきたいと思います。そしてさらに、それを外に売れる形にして、新たな事業の柱にしていきたいですね。
これからも楽しく、枠を壊した冒険を続けて、事業を成長させていきたいと思います。
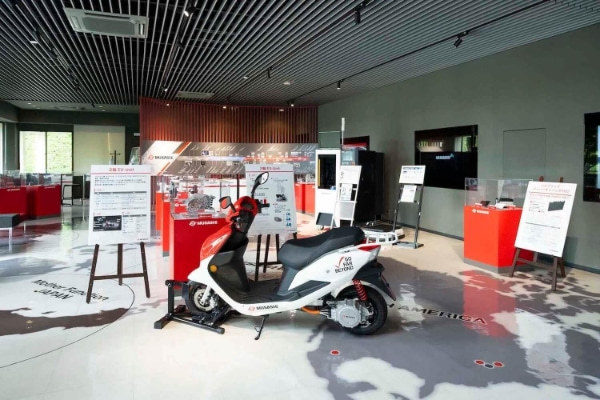
【関連リンク】
武蔵精密工業株式会社 https://www.musashi.co.jp/
株式会社コアコンセプト・テクノロジー https://www.cct-inc.co.jp/
【注目コンテンツ】
・DX・ESGの具体的な取り組みを紹介!専門家インタビュー
・DX人材は社内にあり!リコーに学ぶ技術者リスキリングの重要性
・サービタイゼーションによる付加価値の創造と競争力の強化