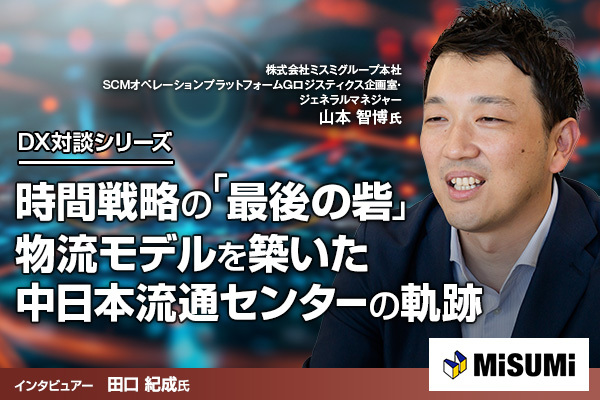
工場の生産設備や検具などに用いる機械部品を製造販売し、800垓にも及ぶ天文学的な品揃えを誇る株式会社ミスミグループ本社。
今回は、Koto Online編集長の田口紀成氏が、ミスミグループならではの物流DXに取り組んできた中日本流通センターについて、生産性を上げる改善の軌跡や具体的な取り組み内容を聞きます。
お話を伺うのは、ミスミグループ本社SCMオペレーションプラットフォームGロジスティクス企画室ジェネラルマネジャーの山本智博氏。中日本流通センターの中に初めてカメラが入り、実際に稼働している自働化されたラインや設備・システムのサポートを受けた作業の様子など、ミスミグループの物流を支える仕組みに迫ります。
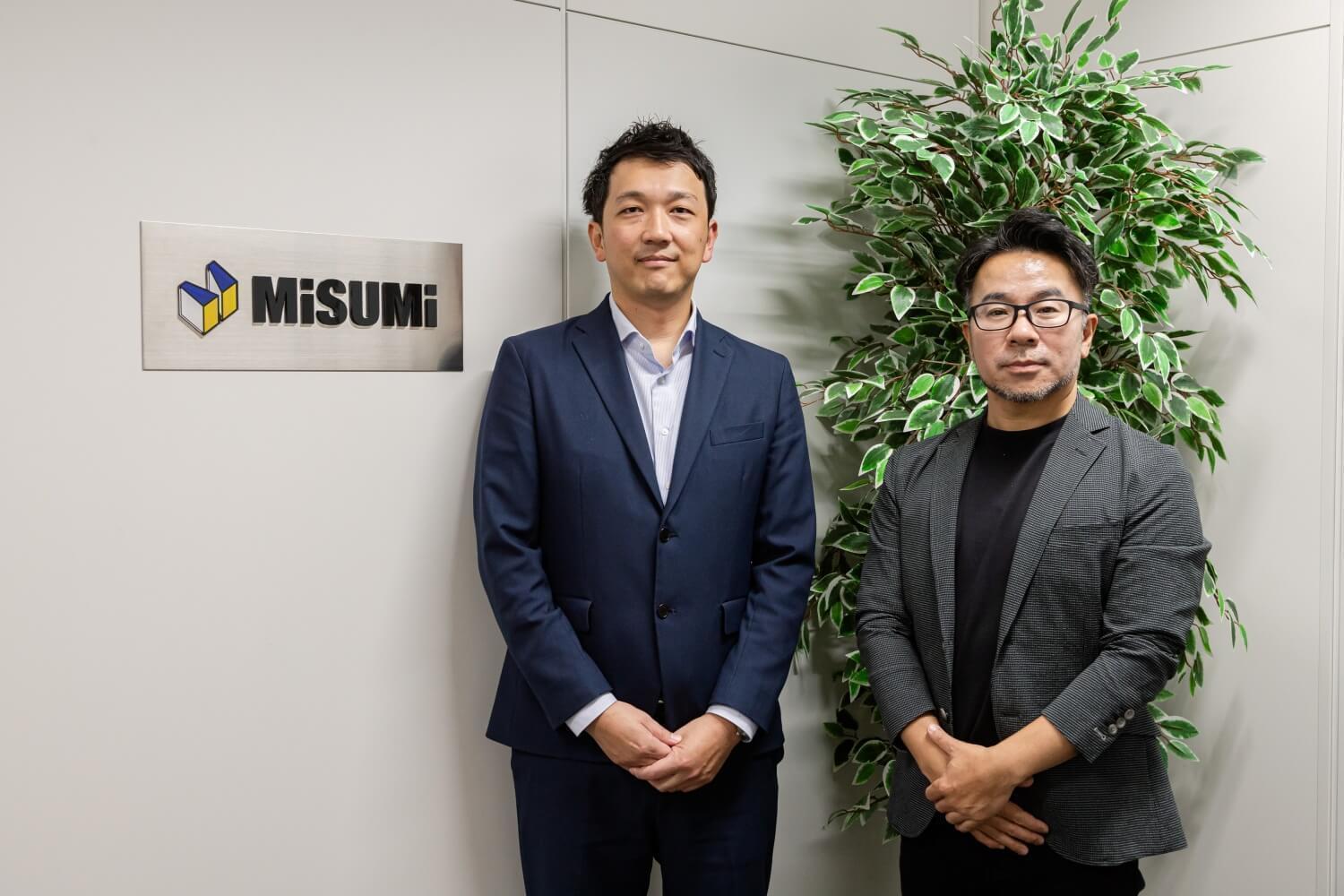
2013年ミスミグループ本社入社。インドネシアやインド、中国など各国海外倉庫の設立を経て、
2018年に責任者として中日本流通センターの立ち上げを行う。
現在は、サプライチェーンや物流現場のDX企画推進の責任者として、物流の生産性向上を牽引する。ミスミ入社前は、製造業のコンサルティング会社でロジスティクス戦略や生産と物流の現場改善などを担当。
2002年、株式会社インクス入社。3D CAD/CAMシステム、自律型エージェントシステムの開発などに従事。2009年に株式会社コアコンセプト・テクノロジー(CCT)の設立メンバーとして参画後、IoT/AIプラットフォーム「Orizuru」の企画・開発等、DXに関して幅広い開発業務を牽引。2014年より理化学研究所客員研究員に就任、有機ELデバイスの製造システムの開発及び金属加工のIoTについて研究を開始。2015年にCCT取締役CTOに就任。先端システムの企画・開発に従事しつつ、デジタルマーケティング組織の管掌を行う。2023年にKoto Onlineを立ち上げ編集長に就任。現在は製造業界におけるスマートファクトリー化・エネルギー化を支援する一方で、モノづくりDXにおける日本の社会課題に対して情報価値の提供でアプローチすべくエバンジェリスト活動を開始している。
目次
時間戦略を掲げるミスミグループにとって物流は「最後の砦」
愛知県稲沢市にあるミスミグループ本社の中日本流通センターは、物流のモデル開発と国内拠点の再編などを目指して構想され、2020年11月に完成しました。敷地面積は約3万3,000平方メートルで、サッカーコート5つ分に相当。この巨大な物流倉庫で国内の出荷量の約3割をカバーします。
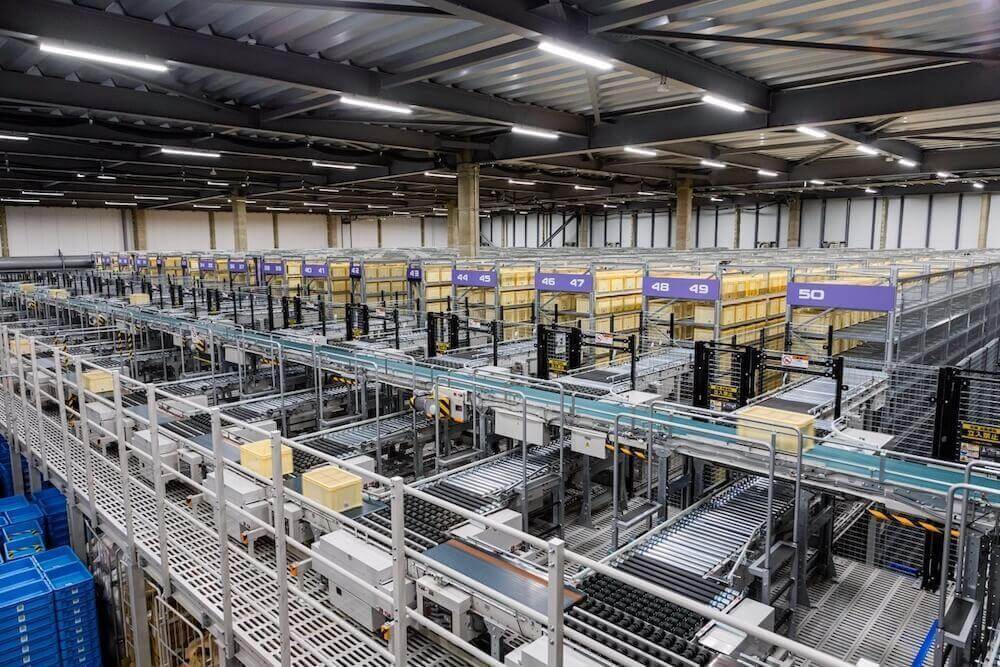
製造業に価値ある時間を創出するという「時間戦略」を掲げるミスミグループにとって、物流は「最後の砦」。受注から顧客に商品を届けるまで、ミスミの代名詞である「確実短納期」を実現するため、中日本流通センターはミスミ内でつないできたバトンを顧客につなぐというミッションを担っています。
ミスミグループでは、その事業内容や商品の品揃えの多さから、物流の在り方も他の企業とはさまざまな点で異なっています。
大きな特徴の一つは、いわゆる流通ビジネスとして商品を保管するDistribution Center(DC)の役割と、メーカーとして受注製造したものを工場から受け取り出荷するTransfer Center(TC)の役割との、両方を1ヵ所で担っている点です。このDC機能とTC機能は、本来異なる倉庫で担うのが一般的ですが、ミスミグループでは顧客の利便性を考えてあえて同居させ、同じ顧客の注文に対しては、自社で製造したものも他社の製品も一つの箱に荷合わせをして、バラバラに届かないようにまとめて配送しています。
また、多種多様な商品を1個単位から受注しているため、JANコード(商品に割り当てられる流通コード)を保有しておらず、機械化・デジタル化が難しいという特徴もあります。加えて、週次、月次、年次で受注の数にも大きなバラつきがあるため、物流としての業務量にも大きな波があり、効率化も簡単ではありません。
こうしたミスミグループの事業特性、量と複雑性の増加への対応が遅れ、2017年ごろは特に国内の物流業務が限界に近づきつつあったと言います。
その状況を打破し、ミスミグループの新しい物流モデルを作ろうと計画されたのが、この中日本流通センターの設立です。「自働化モデルの先導」「BCP対応」「顧客利便性向上」の3つの目的を掲げた中日本流通センターですが、立ち上げから5年が経った現在、当初の目標はすべて達成し、さらなる改善に取り組んでいます。特に倉庫としての生産性は従来モデルと比べておよそ2倍となり、ここで培った物流モデルを海外拠点にも展開しています。
事業特性に合ったきめ細かな工夫で効率的な作業や高い生産性を実現
こうした成果を実現し、高い生産性を維持するために、現場ではどのような工夫がなされているのか。実際のセンターの様子を、株式会社ミスミ中日本流通センター センター長代行の齊藤拓之さんに案内していただきました。
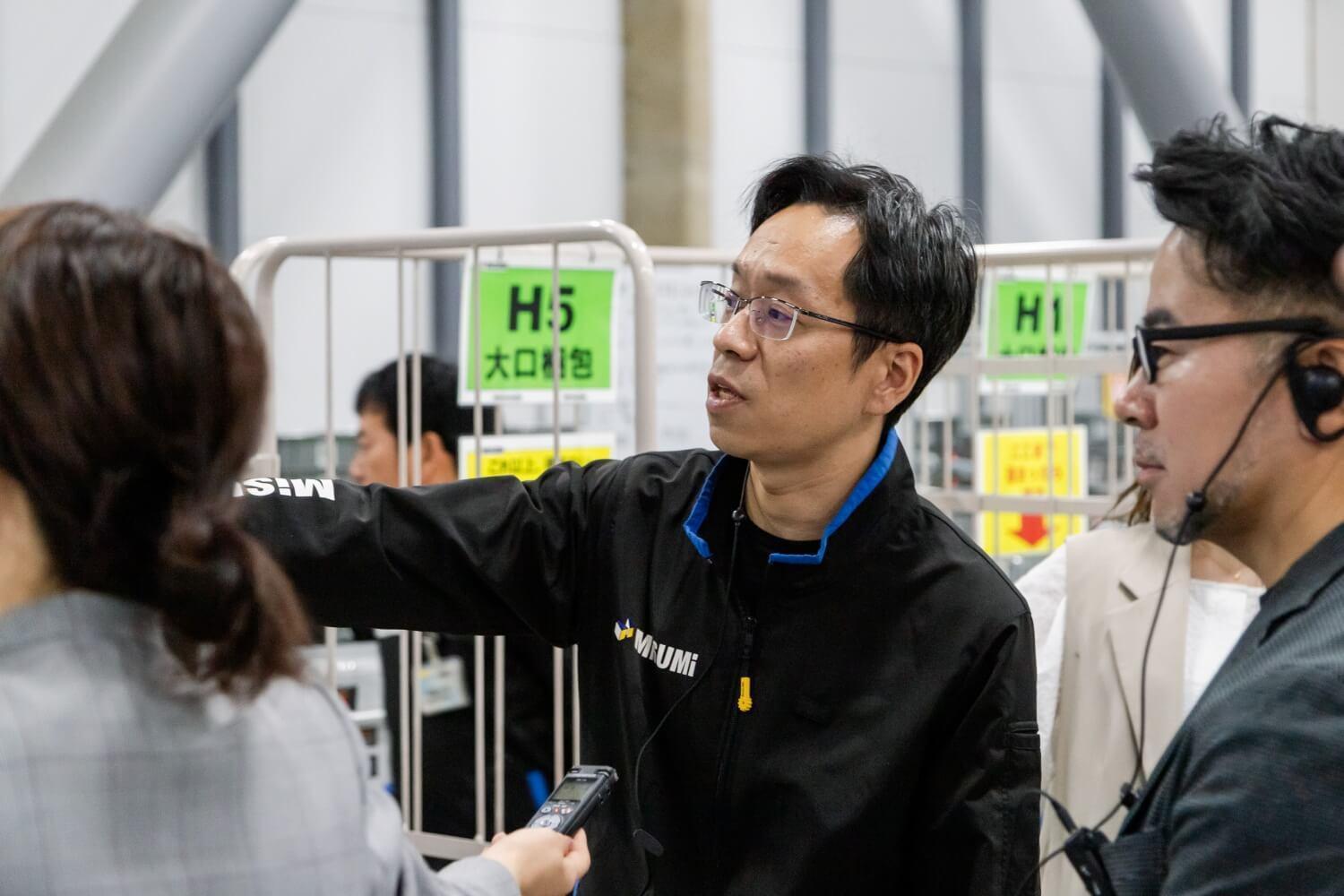
この流通センターでは、取り扱う商品、業務の特性に沿ったさまざまなきめの細かい工夫を重ね、より効率的で質の高い物流を実現しています。
例えば、ミスミグループでは多種多様な商品を取り扱っており、荷合わせする場合の組み合わせや全体の大きさもまちまちとなるため、商品の梱包作業にも独特の難しさがあります。梱包する箱は20種類ありますが、小さすぎる箱を選ぶと詰め直す手間が発生し、確実にすべてが入るよう大きすぎる箱を選ぶと運送費がかさんでしまうため、どの箱に入れるべきかを判断するのに大きな労力がかかっていました。
箱の選定作業の負荷を減らすため、現在は、揃った商品がコンベアで流れてくる様子を上からカメラで撮影し、縦横のサイズ・容積を測定して最適な箱のサイズを機械的に判断しています。そして、梱包に適した箱の種類が画面に表示され、梱包者はLEDで知らされた場所にある指示通りの箱に詰めるだけで梱包が完了する形になっています。この仕組みを導入したことで梱包作業が効率化され、さらには無駄な配送を減らすことで、運送費の削減やドライバー不足に悩む運送業に対する貢献にもつながっているといいます。
さらに、ミスミグループではパックやケースという一般的な販売単位ではなく、1個から受注をしているため、間違いなく商品の数を揃えるのも簡単ではありません。
一つひとつを人手で数えると膨大な手間がかかり、ミスも発生しやすくなってしまいます。ここでは重量によって自動で数を算出するため、流れてくる可能性のある6万点の商品について0.01グラム単位で重要データを計測 しすべて取得。商品の種類は箱に貼ってあるバーコードを読み取って検知します。その商品の1個あたりのデータと、商品が置かれたときの総重量から、自動で数を算出する仕組みです。また、一回一回バーコードを読み取る動作をなくすために、箱を開けるとそのままバーコードが読み取れるように、細かな位置を合わせた作業台も内製しているということです。
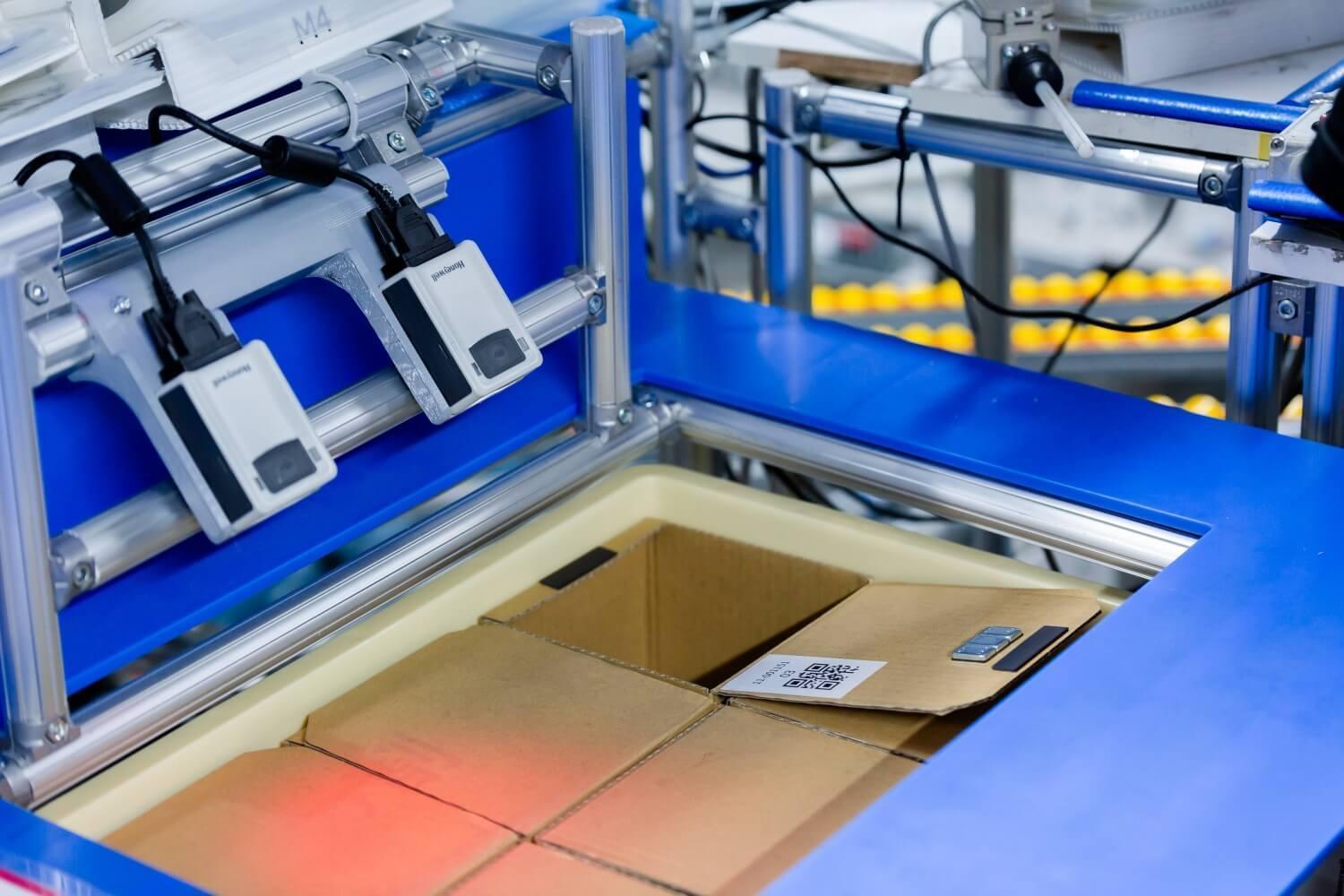
さらに、小さすぎるものや重量が安定しないものなど、重量だけで数を算出することが難しい商品については、影によって判定しています。
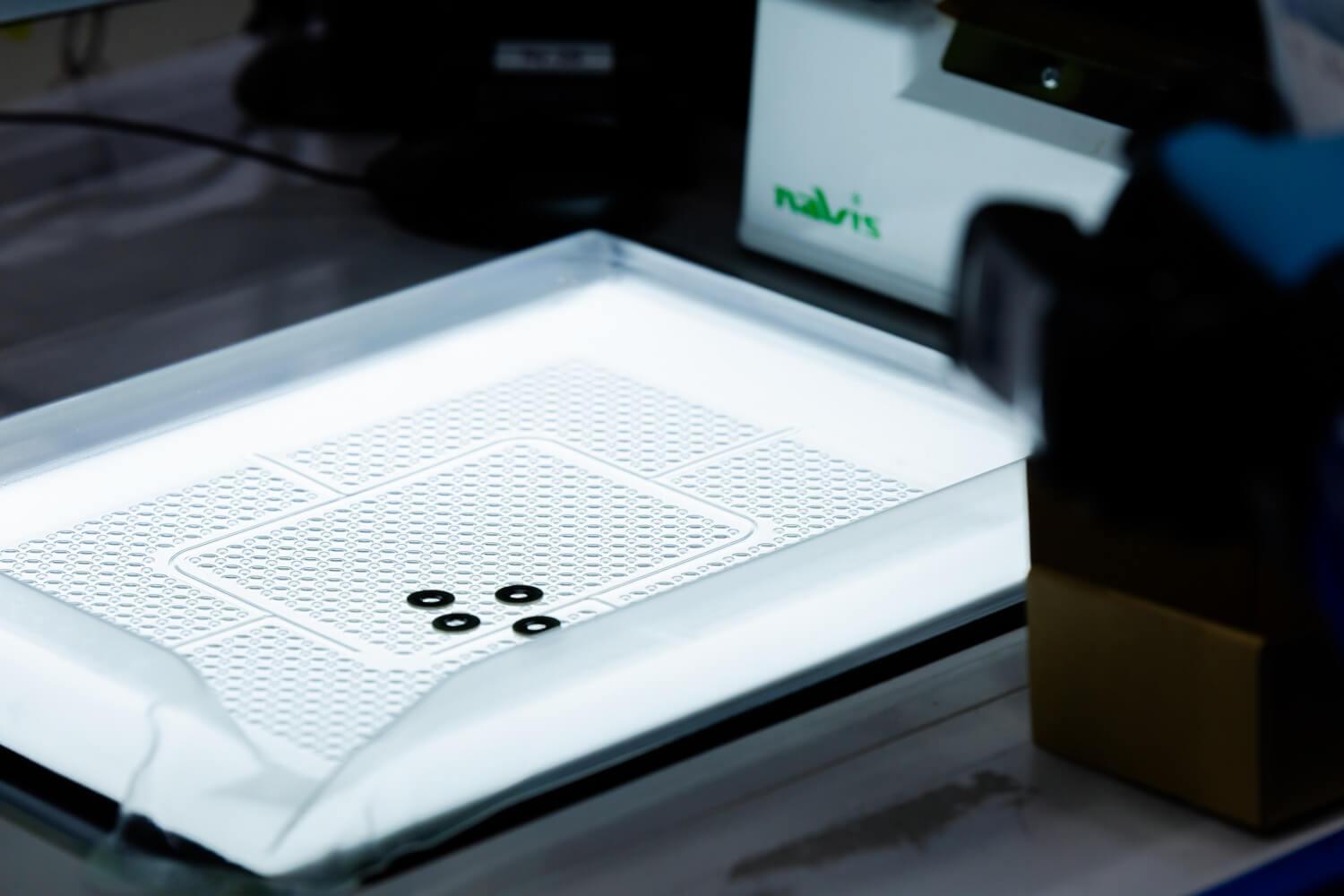
影で判定する仕組みは上の画像のように、下から光を当て、上に設置されたカメラで影の数をカウントします。このツールは、もともと検品などで異なる形の部品が混ざっていないかなどを判定するために開発されたものですが、ミスミグループでは重量が安定しない商品を効率的に数える目的で活用を検討、試行錯誤を繰り返した結果、うまく機能し、導入につながったということです。
齊藤氏は「何か作業をしていて不便だなと思うことがあると、もっと簡素化できるのではないか、楽にできないかと、ソリューションを探していろいろな工夫を重ねてきました。トライアンドエラーで、もちろんエラーもたくさんありましたが、そうした試行錯誤の中で、課題解決にフィットしたやり方やツールが見つかり、現場のさまざまな改善につながっています」と話しています。
自分たちで考え、戦略を組み立てる……ミスミのDNAが生きた改善
さまざまな工夫をこらし、ミスミグループとしての新たな物流モデルを築いてきた、中日本流通センター。立ち上げからこれまでの約5年間で、どのように改善を進めてきたのか、そして今後目指していくミスミの物流とは、どのような姿なのか。中日本流通センターのセンター長を務め、現在はミスミグループ本社で物流全体の戦略づくりなどを担当する、山本智博氏にお話を伺いました。
田口氏(以下、敬称略) 最初に、山本様のご経歴をお伺いできますか。
山本氏(以下、敬称略) 私はもともと製造業のコンサルティング会社でロジスティクス戦略や生産と物流の現場改善などを担当し、その会社を4年間勤めた後、2013年にミスミに入社しました。ミスミグループ本社に入って最初に担当したのは、海外の倉庫の設立です。当時は東南アジアの拠点がまだ少なかったこともあり、インドネシアやインド、中国など、各国で倉庫の立ち上げに携わりました。その後、中日本流通センターの立ち上げの際にセンター長となり、本社や現場のみなさんと新しい物流モデルを作るためにいろいろな改善に取り組んできました。現在は本社に戻り、DXによって物流の現場のみならず、サプライチェーン全体の効率化に関する仕事をしています。
田口 2013年に入社なさって、そこから4年ほどでセンター長に就任しているんですね。その時すでに、生産性の高い物流の新しいモデルを作るというお題はあったかと思うのですが、どのように成し遂げるのか、Howの部分はどのように進めてきたのでしょうか。
山本 センター長就任のお話をいただいたときは、私にとってまさに青天の霹靂で、びっくりしたことを覚えています。もともと設計自体にはまったく携わっていませんでしたし、知ってはいたものの「どうやら中日本に倉庫が立ち上がるらしい」くらいの距離感で、正直遠い立場だったんです。現地でもセンター長の候補を探したらしいのですが、なかなか人がいなかったこともあり、現場の経験をさせてみようとの上司の親心でお話をいただいたのだと解釈しています。
それまで携わってきた海外での仕事は、5〜10名規模の倉庫を立ち上げるというものがほとんどでした。そのため、自動倉庫や物流DXを実践した経験は、正直あまりなかったんです。ただ、前職では生産現場の改善が主な仕事だったため、倉庫の現場で生産性を上げることに関してはある程度の経験がありました。設備の選定などの大枠は本社側ですでに決めてくれていたのですが、その上で、過去の経験も生かしながら現場のみんなと試行錯誤して細かな作業設計を組み立てていった形です。
例えば、ここの人は手を上げて物を取っていて大変そうだなと思ったら、いろいろな道具を買ってきて自分が最も効率よく動ける棚を作ったり、この島とこの島が離れているので導線がスムーズじゃないなと思ったら、もともと引いていたコンベアを途中から切って動かし、ほかの場所とつなげたり……最初の1、2年は、ずっとそうしたことをやっていました。
田口 自働化につながるロジックなどはどのように組み立てたのでしょうか。例えば先ほど見せていただいた梱包作業の仕組みですが、梱包に最適な大きさの箱を実にスムーズに、かつ機械的に選択していました。異なる形状の複数の商品を荷合わせしていて、大きすぎても無駄につながるため、実用化は簡単ではなかったかと思うのですが、何かノウハウがあったのでしょうか。
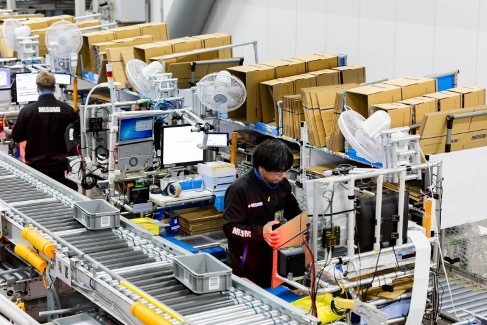
山本 当社のユニークさは、天文学的な商品の種類があり、サイズもマチマチであるということです。但し、その梱包する箱を選択する容積計算のロジックは実はすごく単純化しています。いわゆる積算体積で、どういう立方体になるかを計算し、あわせて、一番長い辺がどこになるかを管理しています。積み上げた容積がこれだけあって、一番長いところがここだから、この箱が合うといったロジックを組みました。ただ、いきなり正解が出せたわけではなく、ロジックで判断するとこのサイズ、人間が選ぶとこのサイズ、というのを試して確認し、熟練の従業員並み、さらには人間より優れたスピードと選択ができるようになってからリリースしています。当時はそのような形でロジックを作り上げていきましたが、もし今やるなら、AIを試してみるかもしれないですね。
オープンな物流業界を実現し、製造業全体のプラスに
田口 前職でもロジスティクスの世界にいらっしゃったと伺いましたが、ミスミグループ本社に来て、御社ならではの物流分野における特徴、独自性みたいなものを感じた点は、何かありますか。
山本 世の中にある先端技術と、現場の地道な改善を融合させながら効率を上げていくことが、大きな特徴の一つだと思います。具体的には、どうしても設備に置き換えられない人作業は、人作業へのデジタルサポートを徹底しています。それらの改善は、現場で実際に作業をしているからこそ思いつく改善点もあります。反面、現場改善ばかりに頼っていると、世の中のテクノロジーをうまく活用できず、置いていかれてしまいます。どちらかに頼りすぎないというか、ほどよいバランスなのだと感じます。
ミスミは物流倉庫の中の運営も、外部の専門会社に任せるのではなく自前です。そもそもが自分たちで生産性を上げていく思想のため、自主的に戦略と改善を組み立てる土壌がもともとあるのではないでしょうか。また、物流に限らず、当社では社員が自ら戦略を描いてビジネスプランを作り、自ら実行する育成手法をとっています。この流通センターにおいても、本社の経営企画からおりてきたものを実行するのではなく、自分たちで物事を考えて、戦略と組み立てる、そして改善を繰り返して人が育つというサイクルがあり、この点はミスミ独自の良いDNAが生きている点でしょう。
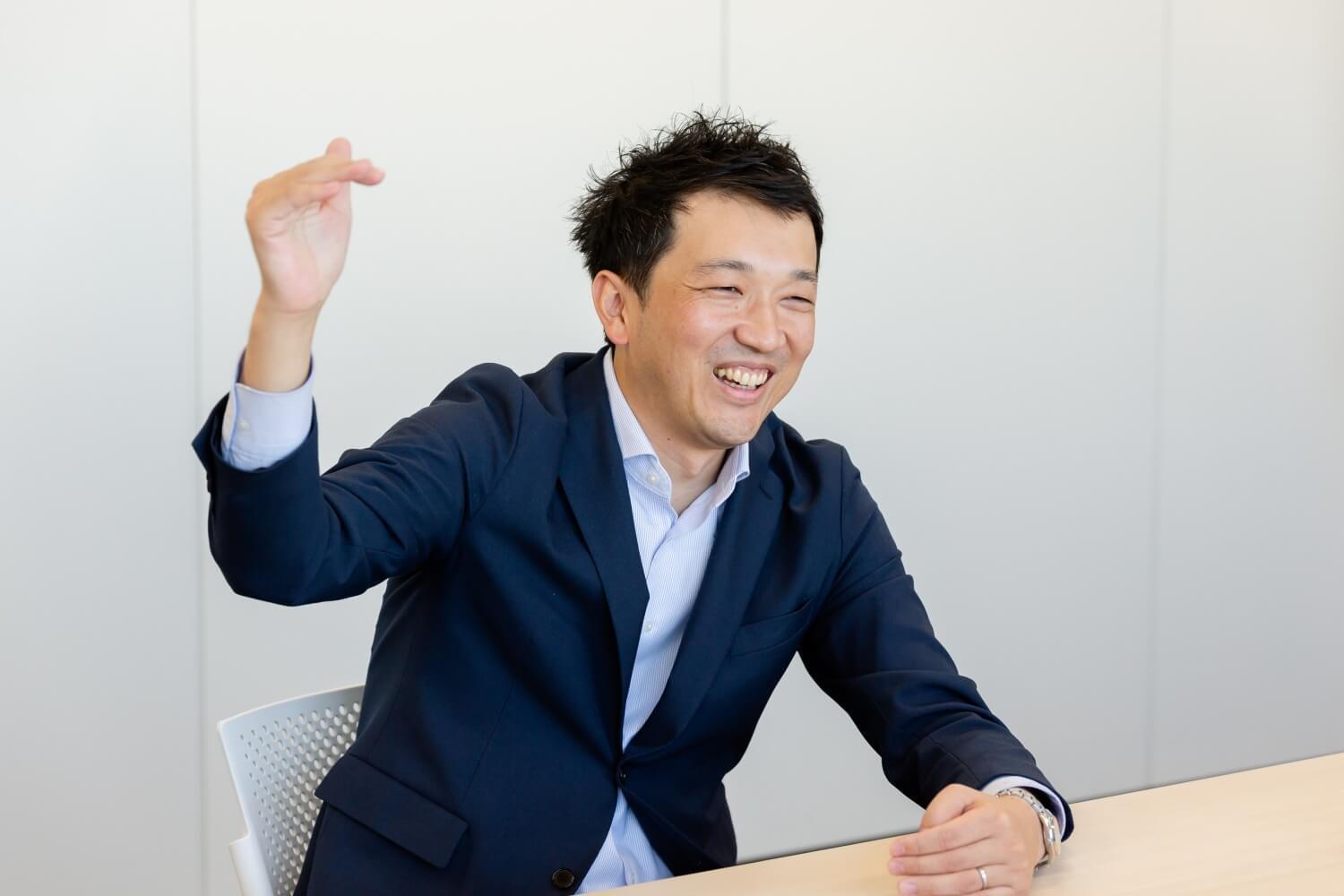
田口 そうして改善を積み上げて、新しい物流スタイルを作り上げてきたんですね。ここで生まれた工夫や改善は、他の拠点にはどのように展開しているのでしょうか。
山本 商品を入荷して、荷合わせをして、ピックアップして、梱包して……という基本的な作業の流れは、規模は違えどどこの倉庫でも同じです。もちろん、使えるものは使う方針でほかの拠点にも展開をしています。例えば自働化を計画している中国からは、現地の人が来てしばらくこのセンターに駐在し、実際に見た上で合うものを持ち帰ってもらい、さらに進化させた倉庫を立ち上げています。それから、手元レベルの改善については、共有会や指導会などで共有したり、本社で動画やマニュアルのライブラリーを作って、グローバルに使えると思った人が自主的に取り入れられるようにしています。
田口 今後、新たに導入してみたいことや、将来の展望について、考えているものはありますか。
山本 現在、倉庫に入荷される在庫品の発注管理の進化に取組んでいます。倉庫の外からDXを仕掛けて、倉庫だけではできない効率性の向上を実現したいと思います。また、もちろん倉庫内のDX、例えばWMS(Warehouse Management System・倉庫管理システム)についても、さらに投資を続けて改善をしたいと思っています。
もう一点、物流に限らずサプライチェーンとして考えたときに、当社だけで可能な改善ももちろんありますが、前の工程や他社さんとのつながりで、製造業全体をより良くできることがまだまだあると思っています。どちらかというと、物流はあまり外と交わる機会がありませんし、自分たちの中の様子をほかに見せない、発信が苦手という傾向があります。そこをクリアして、もう少し外と連携をとることができれば、結果としてみんなにメリットの大きい取り組みが実現できるのではないでしょうか。
田口 確かに、その通りですよね。いろいろな工場や物流倉庫を見せていただく機会が多いのですが、異なる会社で似たようなものを作っているケースが多々あります。オープンにしていくことで改善のスピードが上がり、より良い物流の世界が実現できるかもしれないですね。
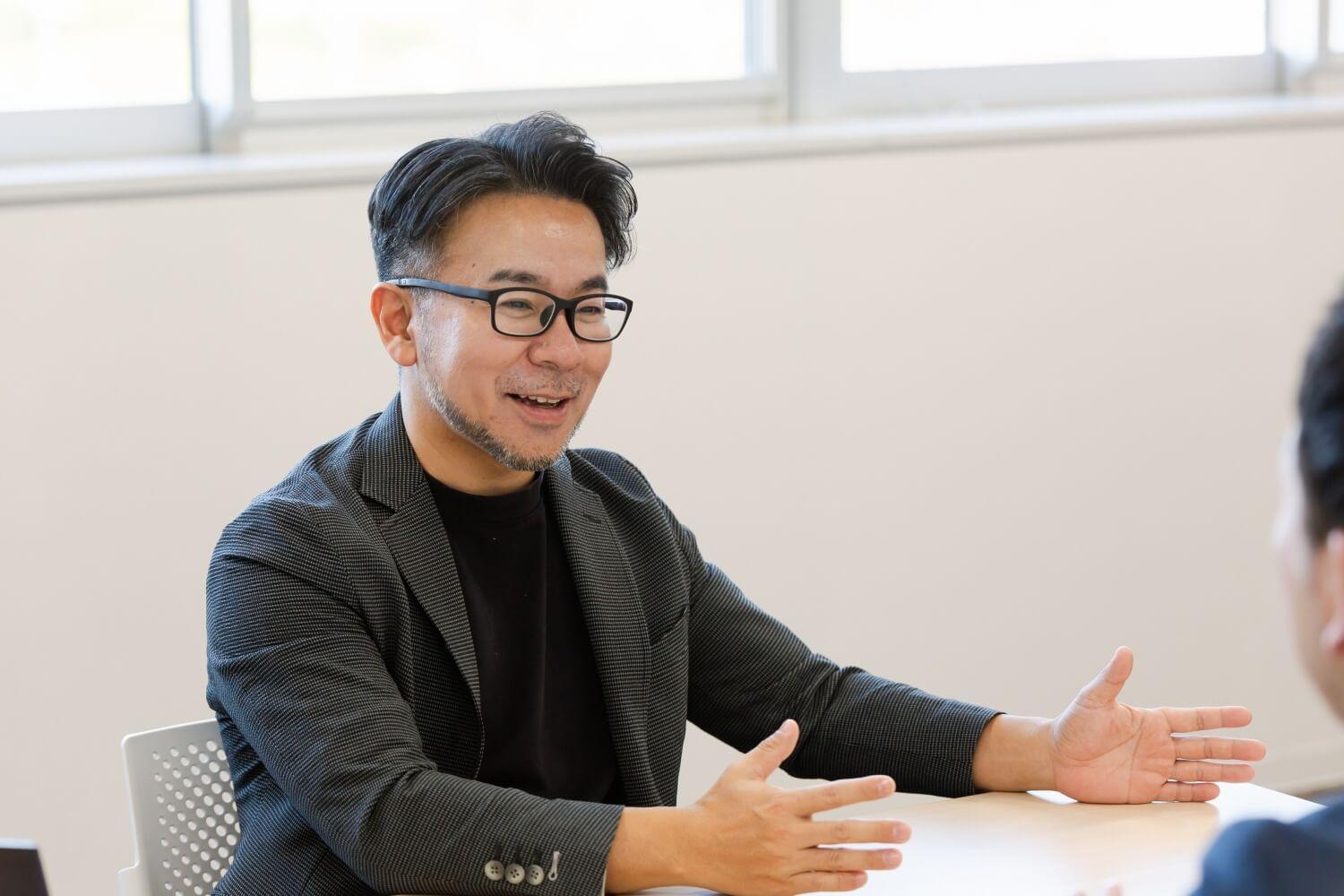
最後に改めて、中日本流通センター立ち上げからこれまでの5年間を振り返り、このセンター設立が御社にとってどのような取り組みだったのか、感じたことをお聞かせいただけますか。
山本 ミスミ全体としては、国内では十数年ぶりの物流センターの立ち上げであることに加えて、ミスミの使命であるモデル進化を前提とするため、難易度が非常に高いプロジェクトでした。倉庫内・バックオフィスの制度も含めて、すべてのことをイチから設計をする必要があり、現場の業務の標準書に加えて、働きやすい環境を意識した人事制度も構築しています。また私も含めて、こうした新しい倉庫の立ち上げは経験のない人間ばかりでした。トライアンドエラーを繰り返しいろいろな挑戦をする中で、本社も現場も人が育っていったように思います。
この5年間で作り上げてきた考え方、新しい物流モデルは国内外にあるほかの倉庫にも展開されています。この取り組みに関係した社内外のすべての皆さんに、改めて感謝を伝えたいですね。
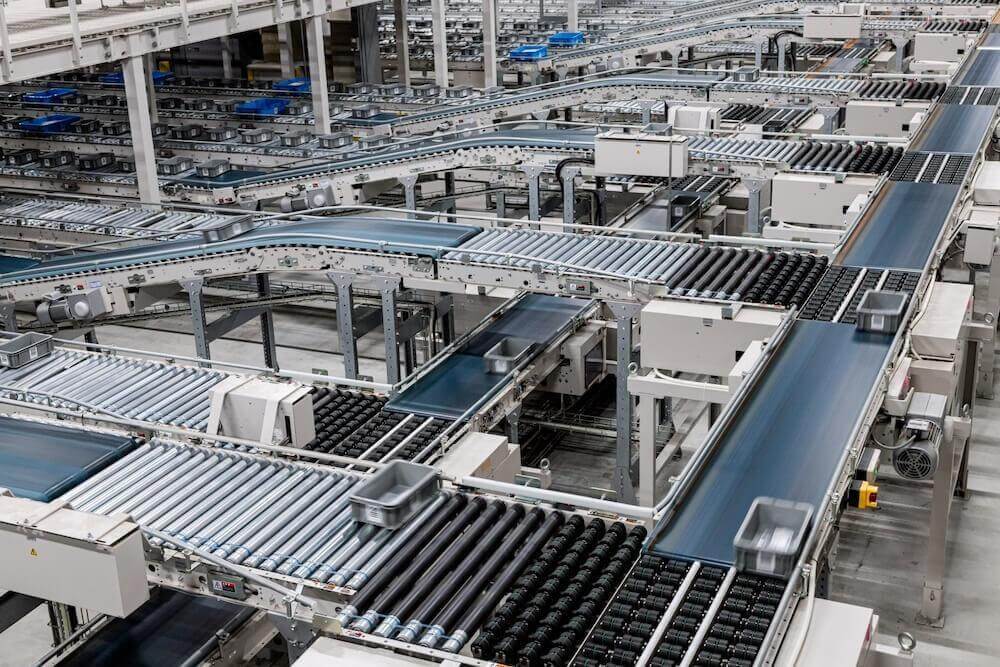
【関連リンク】
株式会社ミスミグループ本社 https://www.misumi.co.jp/
株式会社コアコンセプト・テクノロジー https://www.cct-inc.co.jp/
【注目コンテンツ】
・DX・ESGの具体的な取り組みを紹介!専門家インタビュー
・DX人材は社内にあり!リコーに学ぶ技術者リスキリングの重要性
・サービタイゼーションによる付加価値の創造と競争力の強化