(本記事は、一般社団法人日本能率協会監修の『日本のものづくりが向かう未来』=東洋経済新報社、2024年1月24日刊=の中から一部を抜粋・編集しています)
部品調達にAIとクラウドを導入することで、作図や見積もり、納品待ちの時間を大幅に短縮できる。この「調達DX」を実現したのが、ミスミグループ本社(以下、ミスミ)のプラットフォームサービス「meviy」だ。同サービスの産みの親である常務執行役員の吉田光伸氏と、グループ内で変種変量生産・確実短納期を支える駿河生産プラットフォームの代表取締役社長遠矢工氏に話を聞いた。
吉田 光伸
株式会社ミスミグループ本社 常務執行役員 ID企業体社長
遠矢 工
株式会社ミスミグループ本社 生産プラットフォーム 代表執行役員
株式会社駿河生産プラットフォーム 代表取締役社長
ミスミと駿河精機経営統合の背景
ーミスミが駿河生産プラットフォームを子会社にした経緯は?
吉田 ミスミは1963年に創業された。「生産間接材」と呼ばれる、スマホや自動車などの製品を生産するための設備や装置に必要な機械部品の製造と販売を手掛ける。機械部品の品揃えは世界最大級であると自負している。我々が提供する一番の価値は、顧客時間価値だ。「確実短納期」を実現することで、インダストリアル・オートメーション産業のさまざまなムダ、工数を削減する。
顧客時間価値の提供のため、2つのイノベーションを同時に実現したのは、約40年前のことだ。
一つは「カタログ販売」。従来、機械部品は特注品として一つずつ図面を描いて設計・注文しなくてはならなかったが、そのうちの半数を規格品としてカタログにまとめた。カタログ内には、サイズ違いや材質違いの部品や、確定納期・価格も明記してある。規格品は3000万点、サイズ違いや材質の違いなどを組み合わせると商品バリエーションは800 垓 (1兆の800億倍)を超える計算だ。標準納期は注文から2日目出荷、納期遵守率は99.96%。お客様には「ミスミのカタログがないと工場が動かない」と言っていただく機会も多い。
もう一つのイノベーションが「標準化」。途中まで加工した「半製品」を、最終仕上げ工場にストックしておくことで、注文後「安く早く」納品できる。
その後ミスミはグローバルに成長し、海外展開も進めた。だが、2000年代初頭までのミスミは専門商社であり、ものづくりの機能を持たなかった。転機は2005年、駿河精機(現駿河生産プラットフォーム)と経営統合したことだ。それ以降ミスミは、メーカーとしての道を歩み始めた。
遠矢 静岡県に本社を置く駿河生産プラットフォームが、ミスミグループ全体のマザー工場という位置付けだ。2005年にミスミと経営統合するまで、当社はミスミのクリティカルサプライヤーの一つだった。そのため、ミスミが掲げる確実短納期も、当時から実現できていた。その生産機能をミスミのビジネスプロセスの中に取り込むことで、より大きな時間価値をお客様に提供できるようになる。コストの面でも、製販一体で改善が進み、競合他社に対し優位になる。また、ミスミがグローバル展開をするにあたっても生産機能を内包する必要があった。その点、駿河生産プラットフォームは、統合前からベトナム、中国、米国に進出しており、ミスミのグローバル展開との相性はよかった。現在グループの生産拠点はグローバル22拠点まで拡大した。
吉田 狙いとしてより大きかったのは海外での生産体制の構築だった。外部のサプライヤーに「中国に進出してください」とお願いするのも、自力ではなかなか難しい。かといって、製品を日本から輸出するようでは納期が長くなってしまう。グローバル規模で時間価値を提供するには、生産も営業も物流もセットで、グループが持つ必要があった。
「ミスミ生産方式」を協力メーカーに横展開
遠矢 もう一つ、経営統合の狙いをあげるとするなら、変種変量でも確実短納期を可能とする「ミスミ生産方式」を、つくり込むためだ。生産機能を自社に組み込めば、その試行錯誤がしやすくなる。現場ではまずリードタイム削減にこだわり、継続的な生産性向上と原価低減につなげる。そこから加工技術のデジタル化・自働化でモデルが強化された。
また、駿河生産プラットフォームをモデルケースとして、他のサプライヤーに「ミスミ生産方式」を展開する道も開けた。駿河生産プラットフォーム1社では、すべての商品の製造に対応しきれないため、他の協力メーカーとの連携は欠かせない。駿河生産プラットフォームがやっていることをレファレンスし、ときにはまねし、システムの一部も共有してもらう。これにより、生産プロセス全体の改革と原価低減が進んだ。
サプライヤーでは、在庫品であれば確実短納期も比較的容易だが、我々は受注製作品が大半。そのボリュームも膨大となると、組める会社は非常に少なくなる。限られた数社としっかりアライアンスを組み、サプライチェーンを磨き込んでいった。
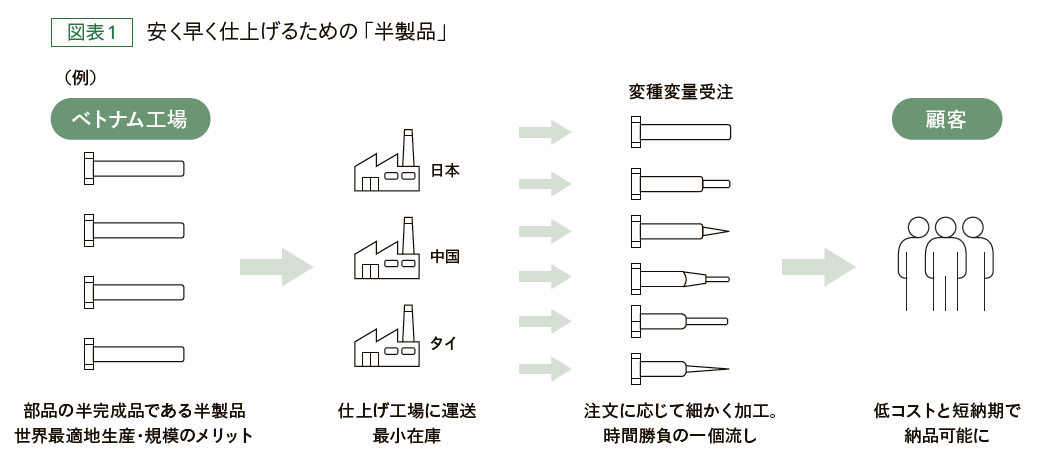
吉田 駿河生産プラットフォームとミスミが経営統合することで、生産機能を手の内化でき、経営の選択肢が大きく広がった。海外展開したい、納期を短くしたいときの動きが早くなり、競争力の源泉となった。
ミスミは2022年に、後でお話しする「meviy」のシステム開発・保守・運用を行う会社としてDTダイナミクスを立ち上げたが、こちらも狙いは同じだ。外部の企業に依頼するよりも、意思疎通の面でも納期の面でもスピードが速くなる。2005年時点では生産機能が競争力の源泉であったが、現在はそれに加えITが競争力の源泉になると考え、DTダイナミクスによってITを手の内化したというわけだ。
遠矢 無論、経営統合後のプロセスがスムーズに進んだわけではない。むしろ、失敗の連続だった。経営統合を機に去った従業員もいれば、残った従業員もいる。駿河生産プラットフォームとして蓄積してきたものづくりのやり方もある。ミスミ生産方式をつくり込むにあたっては、かなりの抵抗があった。最初の3年間は、正直鳴かず飛ばずだった。だが「生産改革はトップダウンで進めるべき」という方針は一貫していた。歴代のトップが現場に降り、改革の陣頭指揮をとった。
即時見積もりと最短1日目出荷が可能に
ーミスミと駿河生産プラットフォームが開発した部品調達プラットフォーム「meviy」とは、どのようなものか。

吉田 ミスミは従来からITをうまく使う会社だ。データ通信による受注を開始したのも90年代初頭であり、業界ではトップランナーだった。大量のトランザクションをさばく高度な基幹システムも整えている。
その最新事例が、2019年から本格展開をスタートした、ミスミと駿河生産プラットフォームが開発した「meviy」だといえる。meviyには2つの革新がある。一つは「AI自動見積もり」。お客様が3D設計のデータをアップロードすると、AIが部品の形状を読み取る。これまでは職人が行っていた価格と納期の計算をAIが数秒で行う。これにより、見積もり業務が大幅に効率化され、お客様が機械部品調達にかけていたコストを大幅に削減した。
もう一つは「デジタルものづくり」の革新だ。従来のミスミ生産方式をさらに推し進めた。具体的には、お客様がアップデートした設計データから、加工機を動かす製造プログラムを自動生成。それが工場へ転送され、製造を行うまでのプロセスも、ほとんどを自動化した。この2つの革新により、即時見積もりと、受注から最短1日での出荷が実現した。
meviyは、日本の製造業が抱えている課題を解決するものだ。製造業は、いまだ日本の基幹産業であり、国際競争力も強い。その一方で、労働生産性は下落の一途をたどっている。生産年齢人口は減少し、働き方改革によって業務量も減った。「多くの人間が、多くの時間働く」これまでの戦い方からの転換を迫られている。「量から質へ」と働き方を変え、生産性を向上させなければ、日本の製造業は生き残れない。
そこで有効な手段となるのがDXだが、製造業にはDXを阻む構造的な問題があった。
設計- 調達- 製造- 販売というバリューチェーンを見ると、設計はCADで、製造はロボット化で、販売はeコマースでデジタル化が進んでいる。ところが調達だけデジタル化が遅れている。象徴的なのがファックス利用率だ。数年前、ミスミのお客様約5100名を対象に調査したところ、約98%がいまだにファックスを利用していた。
こんな試算も行った。1500の部品からなる設備を調達しようとすると、作図の手間に750時間、見積もりの手間に25時間、見積もりの返事と製品が届くまでの待ち時間に168時間かかっていた。1500点の部品を調達するのに、トータルで約1000時間、125日も費やしていることになる。仮に、日本の製造業38万社が1社あたり1台ずつ前述の設備を調達すると、年間3.8億時間。時給をもとに換算すると、年間2兆円の間接コストが調達領域だけでかかっている。
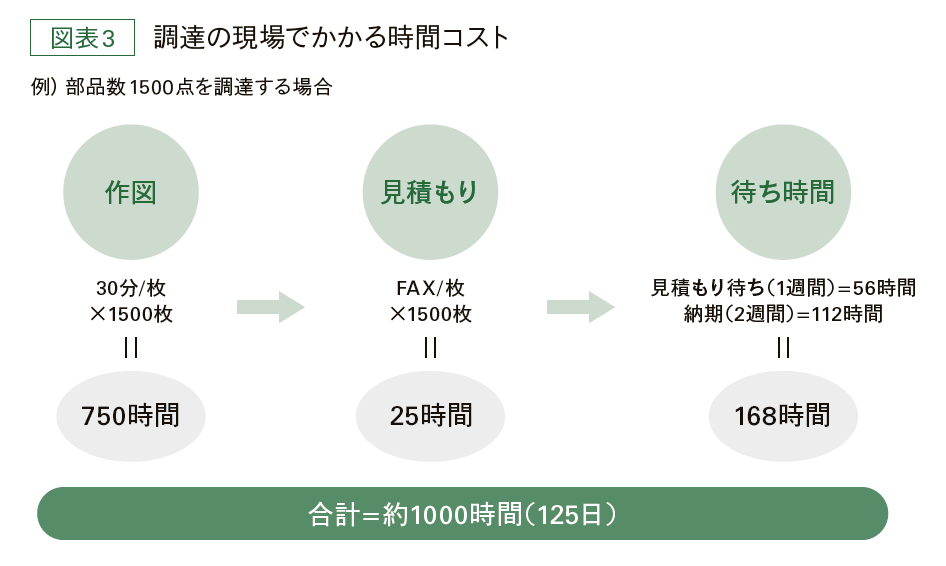
調達領域が、製造業の生産性向上のボトルネックになっている。この課題に対するソリューションとして「meviy」は生まれた。即時見積もりと、最短1日目出荷を実現することで、前述の部品調達にかかっていた約1000時間を約80時間に短縮し、新たに約900時間をお客様に提供できる....
この続きは、一般社団法人日本能率協会監修の『日本のものづくりが向かう未来』からお読みください。
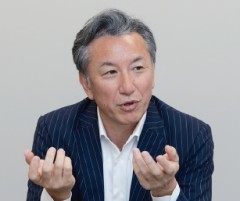
吉田 光伸(よしだ・みつのぶ)
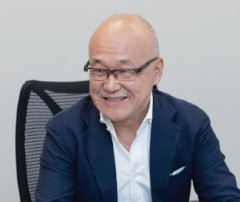
遠矢 工(とおや・たくみ)