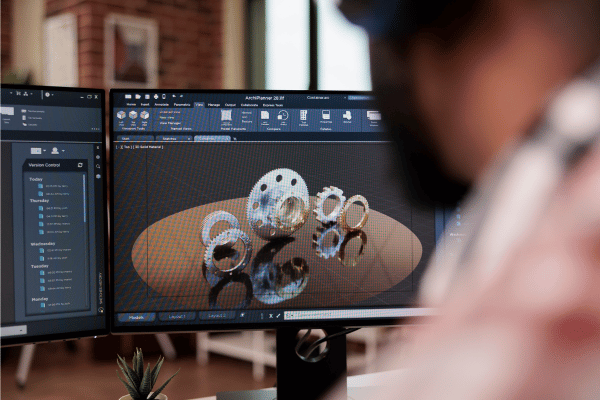
モノづくりにおける設計開発の効率化は、競争力を保つ上で欠かせない要素です。その一助となるのが、MBSEというアプローチです。MBSEは、設計対象のシステムを「モデル」という統一された形式で表現することで、部門や分野を横断した関係者間の認識を揃え、開発プロセスの手戻りを防ぎます。
この記事ではMBSEの概要やメリット、実践方法、国内事例を紹介します。
目次
MBSE(モデルベースシステムズエンジニアリング)とは?わかりやすく解説
MBSEとはModel-Based Systems Engineering(モデルベースシステムズエンジニアリング)の略で、複雑な開発に対応するための技法および開発プロセスを指します。MBSEはシステムズエンジニアリングの一部で、「拡張されたシステムズエンジニアリング」とも捉えられるものです。
<MBSEの特徴>
MBSE は、様々な工学的領域、様々なチームにわたる開発の対象となる製品の要求とアーキテクチャを、モデルを用いて整理することで開発の複雑さを管理、低減している
(引用:独立行政法人情報処理推進機構「モデルベースシステムズエンジニアリング導入の手引き」)
MBSEでは対象となるシステムをさまざまな観点からモデル図にし、システムの要求分析や設計、検証を効率的に行うさまざまな種類のモデルを用いてシステムズエンジニアリングを進めます。対象に対してコンピュータを用いて効率的・効果的にシステムズエンジニアリングを行う手段であり、大規模で複雑な対象に対しても実施できるのが特徴です。
モデルの例としては、検討対象を視覚的に分かりやすい図表で表現したシステムモデルや、妥当性・成立性を定量的に検証するシミュレーションモデルなどがあります。
MBSEによる製品開発では、複雑なシステムをモデル化して整理した形で可視化し、複数の分野が連携して要求分析から検証まで開発工程を進めていきます。MBSEは製品の全体像を見ながら、さまざまな専門家のコミュニケーションを円滑にして業務効率や質を高める存在です。
システムズエンジニアリング(Systems Engineering)とは?
システムズエンジニアリングとは、システムの開発を成功に導くための複数分野にまたがるアプローチおよび手段です。利害関係者の要求に沿った品質の製品やサービスを提供するために、関連する問題を考慮しながら設計してシステムの検証と妥当性の確認を行います。設計にあたってはビジネスとすべての顧客の技術的要求を考慮します。
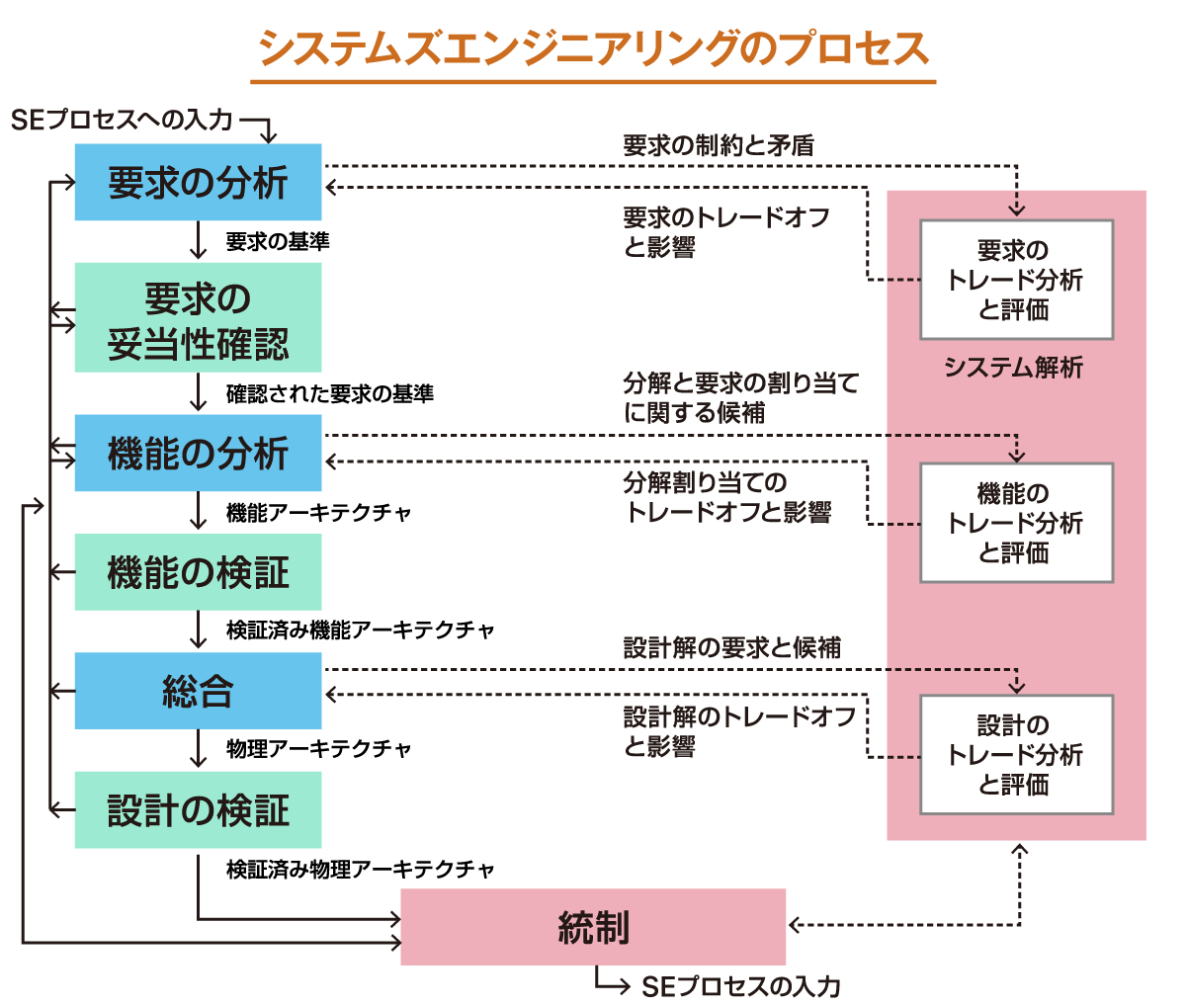
システム開発では、製品やサービスを一つのシステムとして捉え開発します。システムのライフサイクルは、システム開発の開始から終了まででなく、システムの運用、破棄までを含みます。システムズエンジニアリングはシステムのライフサイクル全般をカバーするものです。
日本ではSEという言葉をシステムエンジニア、システムエンジニアリングとしてよく使います。また、ITシステム、ソフトウェア開発を指すことがあります。しかし、複数形のシステムズエンジニアリングはSEとは異なります。システムズエンジニアリングの「システム」とは、目的を遂行するためのさまざまな機能を作り出すために、さまざまな機能や部品が相互に関係しながら集まっていることを指します。ITシステムだけでなく、人や組織もシステムの一種です。
モデルとは「情報の構造体」を指す
MBSEにおける「モデル」とは「情報の構造体」を指し、設計や分析結果、判断基準などシステムそのものの情報だけでなく担当者や日程、コストなどの情報も含まれます。デジタルの立体データ「3Dモデル」や解析で使用する「解析モデル」だけでなく、システムの要件や機能を表す記述もモデルに含まれます。
これらの情報を、関係性を考慮しながら構造化し、コンピュータに入力して管理することがMBSEにおける「モデル」にあたるものです。
MBSEとMBDの違い
MBDとは(Model Based Systems Development)の略です。MBSEについて語るときによく登場する言葉で、日本語にすると「モデルベース開発」です。
MBSEはモデルを用いてシステムズエンジニアリングを行いながら製品開発などを進めることを指します。MBSEは製品のライフサイクル全般に関わる、プロジェクト全体をよりよく管理するための概念です。
一方、MBDは製品の設計開発のためにコンピュータ上で行うシミュレーション手法です。いわゆる仮装試作、バーチャルプロトタイプの手法で、MBDはMBSEの一部といえます。
関連記事:MBDとは?CAEとの違いやメリット・デメリットを解説
MBSEを支える技術
MBSEの運用をさらに高度化するために、様々な技術が活用されます。その一つが、情報の意味をコンピュータが理解できるように処理する「セマンティック技術」です。
この技術を活用することで、異なるツールで作成されたモデル間のデータ連携をスムーズにしたり、膨大なモデル情報の中から必要な知識を効率的に抽出したりすることが可能になります。
モノづくりでMBSEが注目される理由
現代のモノづくりにおいて、MBSEがなぜこれほどまでに注目を集めているのでしょうか。ここでは、製品の複雑化への対応と、開発効率化への要求という2つの主要な要因に焦点を当てて解説します。
製品の複雑化への対応
近年、自動車、航空宇宙、家電製品など、あらゆる分野で製品の複雑化が急速に進んでいます。AI、IoT、ロボティクスといった先端技術の導入により、製品は単一の機能を持つものから、複数のシステムが連携し、複雑な振る舞いをする「システム・オブ・システムズ」へと進化しています。
このような複雑なシステム開発では、従来のドキュメントベースの手法では、各要素間の依存関係や相互作用を網羅的に把握することが困難でした。結果として、設計ミスや手戻り、開発期間の長期化といった問題が発生しやすくなります。MBSEは、システム全体をモデルとして表現することで、複雑な関係性を可視化し、設計段階での問題の早期発見・解決を可能にします。
開発効率化の要求
グローバル競争が激化する中で、製造業は常に「より速く、より安く、より高品質な製品」を市場に投入することが求められています。これまでの開発手法では、設計変更や仕様変更が発生した場合、関連する全てのドキュメントを修正する必要があり、これが開発期間の長期化やコスト増の大きな要因となっていました。
MBSEを導入することで、モデルを修正するだけで関連する情報が自動的に更新され、ドキュメントの整合性を保つことができます。これにより、手戻りの大幅な削減、開発プロセスの短縮、そしてコスト削減を実現し、競争力の強化に繋がります。
モノづくりにおいてMBSEを用いるメリット・デメリット
MBSEは多くの利点をもたらしますが、同時に導入時の課題も存在します。ここでは、MBSEの主なメリットと、導入時に直面しうる課題、そしてそれらを克服するためのベストプラクティス、さらにはROI(投資対効果)の考え方について解説します。
MBSE導入の主なメリット
MBSEをモノづくりに導入することで、以下のようないくつものメリットを享受できます。
1.手戻りの削減と開発期間の短縮
システム全体をモデルで可視化することで、設計段階でのミスや矛盾を早期に発見できます。これにより、開発の後工程での手戻りが大幅に減少し、結果として開発期間の短縮に繋がります。2.品質の向上
モデルによる厳密な定義と整合性チェックにより、システムの仕様がより正確かつ明確になります。これにより、開発される製品の品質が向上し、市場での不具合発生リスクを低減できます。3.関係者間のコミュニケーション円滑化
複雑なシステムでも、共通のモデルを通じて視覚的に情報を共有できるため、開発チーム内はもちろん、顧客やサプライヤーといった関係者間の認識齟齬を解消し、コミュニケーションを円滑にします。4.知識・ノウハウの形式知化と再利用性の向上
開発過程で得られた知識やノウハウがモデルとして蓄積されるため、属人化を防ぎ、将来のプロジェクトでの再利用が容易になります。これは、設計資産の有効活用にも繋がります。5.トレーサビリティの確保
要求から設計、実装、テストに至るまで、開発プロセスの各フェーズがモデル上でリンクされるため、高いトレーサビリティを確保できます。これにより、仕様変更時の影響範囲分析や、問題発生時の原因特定が容易になります。
導入時の課題・デメリット
MBSEの導入は、多くのメリットがある一方で、いくつかの課題も存在します。
1.初期投資の大きさ
MBSEツールや関連する教育、組織体制の再構築には、まとまった初期投資が必要です。2.人材育成とスキル習得の難しさ
モデルベース開発には、従来のドキュメントベース開発とは異なるスキルや考え方が求められます。モデリングスキルを持った人材の育成や確保が課題となることがあります。3.組織文化の変革
既存の開発プロセスや組織文化が、MBSEの導入に適応できない場合があります。部門間の連携強化や、開発プロセスの見直しが不可欠です。4.ツールの選定と連携
MBSEツールは多岐にわたり、自社の開発プロセスやシステムに最適なツールを選定し、既存のツールとの連携を確立することが重要です。
課題解決のベストプラクティス
上記の課題を克服し、MBSE導入を成功させるためには、以下のベストプラクティスを参考にすると良いでしょう。
ベストプラクティス | 概要 |
---|---|
段階的な導入 | 小規模なプロジェクトや一部の部門からMBSEを導入し、成功体験を積み重ねてから全社展開していくことで、リスクを低減し、スムーズな移行を促す |
トップマネジメントのコミットメント | MBSE導入は組織全体の変革を伴うため、経営層の強いリーダーシップとコミットメントが不可欠 |
専門家による支援 | MBSEの専門知識を持つコンサルタントやエンジニアの支援を得ることで、導入プロセスを円滑に進め、課題解決に役立てる |
継続的な教育とトレーニング | 定期的な教育プログラムやワークショップを通じて、エンジニアのモデリングスキル向上を継続的に支援 |
適切なツールの選定と活用 | 自社のニーズに合ったMBSEツールを選定し、その機能を最大限に活用することで、導入効果を最大化 |
ROI(投資対効果)の考え方
MBSE導入のROIを評価する際には、単にコスト削減だけでなく、以下のような定量的・定性的な側面を総合的に考慮することが重要です。
評価項目 | 定量的な効果 | 定性的な効果 |
---|---|---|
開発期間 | 手戻り回数、開発サイクルの短縮日数 | タイム・トゥ・マーケットの短縮、競合優位性向上 |
品質 | 不具合発生率、テスト工数の削減 | 顧客満足度の向上、ブランドイメージの向上 |
コスト | 人件費(工数削減)、テスト費用、検証費用削減 | リスク低減、コンプライアンス順守 |
知識・ノウハウ | ナレッジベースの構築、再利用可能な資産の増加 | 技術力の向上、人材流出リスクの低減 |
MBSE導入によって、開発期間の短縮、品質向上、コスト削減など、多岐にわたる効果が期待できます。これらの効果を定量的に評価することで、投資の正当性を証明し、さらなる投資を促進することができます。
MBSE導入の前提条件・準備
MBSEを成功裏に導入するためには、いくつかの重要な前提条件と周到な準備が必要です。ここでは、組織体制の整備、必要なスキル・人材、そして具体的な導入計画の立て方について詳しく解説します。
組織体制の整備
MBSEは単なるツールの導入ではなく、開発プロセス全体の変革を伴います。そのため、それに適した組織体制の整備が不可欠です。具体的には、以下の点が挙げられます。
MBSE推進チームの設置
MBSE導入を主導し、関係部署との連携を図る専門チームを設置することが有効です。このチームは、導入計画の策定、ツールの選定、標準プロセスの定義、メンバーへの教育などを担当します。部門間の連携強化
システム開発に関わる設計、開発、テスト、製造などの各部門が密接に連携し、共通のモデルを基盤とした情報共有を行うための体制を構築します。役割と責任の明確化
MBSEを導入することで、各メンバーの役割や責任が変化する場合があります。混乱を避けるためにも、新たな役割を明確に定義し、周知徹底することが重要です。
必要なスキル・人材
MBSEを円滑に運用するためには、特定のスキルを持った人材の育成や確保が必要です。
システム思考
個々の要素だけでなく、システム全体を俯瞰し、その相互作用や振る舞いを理解できる能力は、MBSEにおいて最も重要です。モデリングスキル
SysMLなどのモデリング言語を用いて、システムの要求、構造、振る舞いを正確に記述できるスキルが求められます。コミュニケーション能力
モデルを通じて異なる専門性を持つメンバーと円滑にコミュニケーションを取り、共通認識を形成する能力は、MBSEプロジェクトの成功に不可欠です。MBSEツール活用スキル
導入するMBSEツールの操作方法や機能を習熟し、効果的に活用できるスキルも重要です。
社内での育成が難しい場合は、外部の専門家を招いたり、MBSEに関するトレーニングプログラムを活用したりすることも有効な手段です。
導入計画の立て方
MBSE導入を成功させるためには、現実的で段階的な導入計画を立てることが重要です。
1.現状分析と課題特定
まず、現在の開発プロセスを詳細に分析し、MBSE導入によって解決したい具体的な課題を明確にします。
2.目標設定
MBSE導入によって達成したい具体的な目標(例:開発期間20%短縮、不具合発生率10%削減など)を設定します。
3.パイロットプロジェクトの選定
最初から大規模なプロジェクトに適用するのではなく、比較的規模が小さく、成功の見込みが高いパイロットプロジェクトを選定し、そこでMBSEを試行導入します。
4.ツールとプロセスの選定
パイロットプロジェクトでの経験を踏まえ、自社のニーズに合ったMBSEツールを選定し、標準的な開発プロセスを定義します。
5.トレーニングと教育
選定したツールとプロセスに基づき、開発メンバーへのトレーニングと教育を実施します。
6.段階的な展開
パイロットプロジェクトでの成功と改善点を踏まえ、段階的にMBSEの適用範囲を広げていきます。
7.効果測定とフィードバック
定期的にMBSE導入の効果を測定し、その結果をフィードバックすることで、プロセスやツールの改善を図ります。
この計画的なアプローチにより、リスクを最小限に抑えつつ、MBSE導入による最大の効果を引き出すことが可能になります。
MBSEによる設計開発の実践方法
製造業においてMBSEのアプローチを実践する方法の一例を、具体的な手順とともに紹介します。ここでは、設計開発の平準化・効率化を図るために、ベテラン技術者の経験や勘に頼っていた設計検討のプロセスをモデル化したいときを例に解説します。
1.技術構造とプロセス構造をそれぞれ構造化する
MBSEの活用を始めるにあたり、まず必要なのは、製品の技術構造とプロセス構造を分けて構造化し、それぞれの関係性を整理することです。このプロセスは、設計資料の確認やベテラン技術者への聞き取りを通じて行います。
技術構造では、製品モデルに関する情報を構造化し、製品仕様から性能特性、サブシステム特性、部品特性に至るまでのトレーサビリティを整理することが求められます。一方、プロセス構造では、タスクモデルに関する情報を構造化します。どの特性値をどのような手段で決めていくかを明確にすることが重要です。
2.それぞれの情報構造をモデル化する
次に、整理した技術構造とプロセス構造をそれぞれモデル化します。モデル化には、MBSEツールを用いてシステムモデリング言語の「SysML(シスエムエル)」で記述していきます。このステップにより、製品の設計開発プロセスが視覚化され、共有や検証が容易になります。
3.特性値や検討タスク間の関係性をマトリクスで表記する
特性値や検討タスク間の関係性をマトリクスで表記します。
技術構造の場合、モデル化によって得られたシステムの特性間の関係性に関する情報を基に、特性値をマトリクスで表記します。このマトリクスは、製品の性能特性、サブシステム特性、部品特性を網羅し、それらがどのように連携して全体の製品性能を構築するかを一覧できる道具です。
一方、プロセス構造については、モデル化した検討タスクや特性値の情報をもとに、検討タスク間の関係性をマトリクスで明示します。これにより、各タスクが製品のどの特性に影響を与えるのか、また、どのタスクが他のタスクと依存関係にあるのかを一目で把握することが可能です。
これらのマトリクス表記により、設計開発のプロセスがより明瞭になり、それぞれのタスクが全体の中でどのような役割を果たしているのかを理解しやすくなります。また、これによって意思決定の根拠が明確になり、設計開発の効率化が図れます。
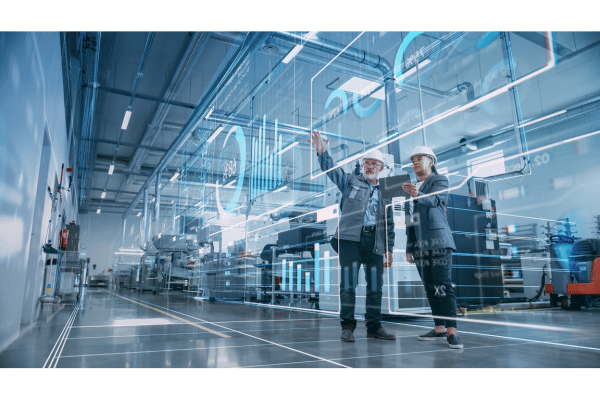
MBSEに関する国内事例
モノづくりDXの事例の中からMBSEに関連のあるものを紹介します。
【事例1】トヨタ自動車株式会社
トヨタ自動車株式会社では3D CADデータなど既存のデジタルデータを一元管理でき、部署間の情報共有基盤となる「工場IoT」を構築しました。今後は工場IoTの考え方をエンジニアリングチェーン、サプライチェーンに拡大し、開発・市場・工場をデジタル化により連携したいとしています。
課題・取組内容
<背景・課題>
3D CADデータや試作時の特性データなど、個々の情報のデジタル化を行い、技術開発・生産準備に成果を上げてきた。しかし、実際の製造・お客様から得たデータの技術開発へのタイムリーなフィードバックに苦戦していた。 Industry4.0や非自動車メーカーの台頭等の社会変化を受け、危機意識を持ち、全社的なデジタル化を検討した。
(引用:PwCコンサルティング合同会社「製造業DX取組事例集」)
<取組内容>
効率や費用対効果重視の風土を鑑み、まず「工場IoT」から着手した。「工場IoT」においては、工場横断の共有プラットフォームを2~3年かけて段階的投資。製造側はデジタル技術を使ったトヨタ生産方式として、各社員が小規模なテーマを立案し、実行し、効果を出すというボトムアップの取り組みを行い、人材の育成も併せて進めた。
(引用:PwCコンサルティング合同会社「製造業DX取組事例集」)
施策・成果
<工夫>
デジタル活用で各社員が困らないように、社内部署による組織的な教育支援、BI・AIなどの便利ツールをプラットフォーム上に用意。
デジタルを活用し安心して効果を出せるよう、予め十分なセキュリティ対策された環境を構築。
データの収集や蓄積にも「必要なものを、必要な時に、必要な分だけ」というトヨタ生産方式の考え方に則るようにし、ムダなデジタル化をせず、費用対効果を出した。
(引用:PwCコンサルティング合同会社「製造業DX取組事例集」)
<成果>
最初に生産部門と連携し、情報システム部門にて「工場IoT」のプラットフォームをセキュアに準備。各事業部・工場にてそれを使った現場プロジェクトを立ち上げ、取組の数を増やしていくことで、トータルで費用対効果を上げた。
「工場IoT」で得られた成果を受け、エンジニアリングチェーンやサプライチェーンを含むデジタル化への適用を打ち出し、品質向上や商品力向上、法規への対応等、付加価値向上に関わるデジタル化に着手し始めた。
(引用:PwCコンサルティング合同会社「製造業DX取組事例集」)
今後の課題
諸外国との比較調査の結果、自動車業界の変革期とも重なり、マーケティングや販売系の強化の必要性、ハードだけでなくソフトの価値の高まりへの対応など、デジタル化を使って新たに着手すべき課題が見えてきた。市場、工場、開発のサイクルを回せる基盤強化をしていきたい。 デジタル化とセキュリティ対策強化は同時並行で進めなければならないが、自社だけでなくサプライチェーン全体の理解と実施が必要である。
(引用:PwCコンサルティング合同会社「製造業DX取組事例集」)
【事例2】富士通株式会社
富士通株式会社は、バーチャル空間上で設計、製造、品質保証の各部門がコミュニケーションを図り、データ共有やデザインレビューを行える「仮想大部屋」というシステムを構築しました。仮想大部屋はFTCPを構成する要素の一つです。仮想大部屋では、過去に蓄積された製品データやクレーム情報などすり合わせを行うことで、開発現場にも製造・保守のノウハウを蓄積することが可能になります。またVR、AR技術を用いて製品データを立体的に表現することで、モックアップを施策することなくデザインレビューを行えます。
課題・取組内容
<背景・課題>
製品開発における課題として、市場環境変化による製品の多様化およびカスタマイズ化への対応、納期の短縮化への対応、製品の複雑化・高密度化への対応、技術継承の継続強化があった。
製造現場における課題として、日本でものを作ることへのこだわりから、ノウハウ伝承、人不足への対応があった。
全社的な課題として、調達・管理コスト削減、設計者の高齢化・サイロ化による個人差低減、災害対応によるBCP強化のための事業部間の連携強化が必要だった。事業部ごとに特定の製品を特定の工場で生産しており、事業部間の連携や共通したルールは存在しなかった。
(引用:PwCコンサルティング合同会社「製造業DX取組事例集」)
<取組内容>
「富士通生産方式(FJPS)」として、人に依存しないものづくりを目指す、自ら必要なツールを作る、プロセスをコンカレント化することを富士通グループ全体の活動として推進した。
「FJPS」のうち、製品開発における課題解決のため、設計のデジタル化プラットフォームである「FTCP」を構築した。
(引用:PwCコンサルティング合同会社「製造業DX取組事例集」)
施策・成果
<工夫>
開発期間短縮のため、AI, CADの一部などはオープンソースを活用した。
「FTCP」上のツールを継続的に活用するため、以下の取り組みを行った。
・図面作成や製品評価検証に係るルールの整備
・製品毎の試作回数制限や3Dデータシミュレーションを義務付けた製品開発フローの整備
・社内プラットフォームの使用履歴の事業部毎の監査・評価、全社的な比較
(引用:PwCコンサルティング合同会社「製造業DX取組事例集」)
<成果>
製品開発プロセスの手戻り減少、品質向上、納期短縮を達成した。
設計段階における不具合抽出、製造しやすい設計の追求が可能になった。
製品開発プロセスのうち、設計から製造に至る部分において、製造技術部門の業務がデジタル化され、負荷が低減された。
一部は顧客への提供を開始しており、このうち「仮想大部屋」を導入したいというニーズに対しては、使用するにはまず既存データの整流化など使用のための準備が必要であることを説明したうえ、ローデータの統計的処理や業務のプロセス化など導入前の支援的なサービス提供も始めている。
(引用:PwCコンサルティング合同会社「製造業DX取組事例集」)
今後の課題
自社内向け設計基盤として構築したことが起点であるため、顧客への提供時も顧客の既存プロセスにカスタマイズしたものを作る、という提案になりがちである。一社にとどまらない連携など、周辺環境が変化した際にも組み替えて使えるような汎用性の高いシステム化が求められる。
製品開発件数が減ってきており、このようなプラットフォームの維持にもコストがかかるため、中長期的な検討が必要である。
(引用:PwCコンサルティング合同会社「製造業DX取組事例集」)
MBSEに関するよくある質問(FAQ)
ここでは、MBSEに関するよくある質問にお答えします。
Q.MBSEとMBDの違いは何ですか?
A.MBDは特定の技術領域(主に制御系)における詳細設計と実装に特化しているのに対し、MBSEはより広範なシステム全体の概念設計から要求管理までをカバーする、より上位の概念と言えます。
MBSEとMBDはどちらも「モデルベース」という言葉が使われており、混同されがちですが、その対象範囲と目的が異なります。MBD(Model-Based Design:モデルベースデザイン)は、主にソフトウェアや制御システムの設計・開発フェーズで利用される手法です。MATLAB/Simulinkなどのツールを用いて、制御アルゴリズムや物理モデルを構築し、シミュレーションや自動コード生成を行うことで、設計から実装、テストまでの効率化を図ります。
一方、MBSE(Model-Based Systems Engineering:モデルベースシステムズエンジニアリング)は、システム開発ライフサイクル全体の上流工程(要求定義、システム設計、アーキテクチャ設計など)に重点を置いた手法です。システム全体の複雑さを管理し、異なる専門分野間の連携を円滑にすることが主な目的です。SysMLなどのモデリング言語を用いて、システムの機能、構造、振る舞いを多角的に記述し、開発プロジェクト全体の関係者間で認識の共有を促します。
Q.MBSEとはどういう意味ですか?
A.MBSE(Model-Based Systems Engineering)は、日本語では「モデルベースシステムズエンジニアリング」と訳され、システム開発のあらゆるフェーズにおいて、「モデル」を中心に据えて開発を進めるアプローチを指します。
従来のシステム開発では、仕様書や設計書といった「ドキュメント」が情報の中心でした。しかし、これらのドキュメントは、システムの複雑化に伴い、記述量が増大し、整合性を保つのが困難になるという課題がありました。
MBSEでは、システムをテキストベースのドキュメントではなく、SysML(Systems Modeling Language)などの標準化されたモデリング言語を用いて、視覚的なモデルとして表現します。このモデルは、システムの要件、機能、構造、振る舞いといった様々な側面を多角的に記述することができ、開発チームや関係者間で共通の理解を促進します。モデルを通じてシステムの全体像を早期に把握し、設計段階での問題や矛盾を検出できるため、手戻りを大幅に削減し、開発期間の短縮と品質向上に貢献します。
具体的には、要求分析から設計、実装、テスト、運用、そして廃棄に至るまで、システムライフサイクル全体にわたってモデルを活用します。これにより、開発の各段階における情報の整合性が保たれ、変更管理が容易になるメリットがあります。
Q.PLMとMBSEの違いは何ですか?
A.PLMは製品ライフサイクル全体の情報管理と最適化を目指す経営戦略・システムです。一方、MBSEは製品の設計段階でモデルを用いてシステムの複雑性を解決する手法です。MBSEで作成されたモデルはPLMの一部として管理され、互いに補完し合います。
PLM(Product Lifecycle Management:製品ライフサイクル管理)は、製品の企画・開発から生産、販売、サービス、そして廃棄・リサイクルに至るまで、製品のライフサイクル全体にわたる情報を一元的に管理し、最適化を図るための経営戦略、またはそれを支援するシステムを指します。PLMの主な目的は、製品に関連するあらゆるデータ(CADデータ、BOM情報、ドキュメント、部品情報など)を一元管理し、部門間やサプライヤーとの連携を強化することで、製品開発の効率化、品質向上、コスト削減を実現することです。
一方、MBSE(Model-Based Systems Engineering:モデルベースシステムズエンジニアリング)は、前述の通り、システム開発の上流工程においてモデルを中心に据える手法です。システムの要求定義やアーキテクチャ設計など、製品の「設計思想」や「機能」をモデルとして表現することに焦点を当てています。
両者の関係性は、PLMが製品開発全体のプロセスと情報の「管理」を目的とするのに対し、MBSEは特に製品の「設計」における複雑性をモデルを用いて「解決」する手法であると言えます。MBSEで作成されたシステムモデルは、PLMシステムに取り込まれ、製品情報の重要な一部として管理されることで、製品ライフサイクル全体を通じたトレーサビリティと整合性を確保します。つまり、MBSEはPLMを構成する重要な要素の一つとして機能し、PLM戦略全体の成功に貢献すると考えられます。
MBSEの導入によりモノづくりに関する多くの悩みを解決に導ける
設計情報の散逸、部門間の連携不足、そしてベテランからの技術継承の困難さ。これらは、多くのものづくり企業が直面する根深い課題です。
MBSEは、これらの課題に対して「モデル」という信頼できる情報源を提供します。モデルを中心にコミュニケーションが生まれ、設計思想が形式知として蓄積されていく。このサイクルこそが、組織の開発力を根底から引き上げます。
MBSEは、次世代のものづくりに挑むすべての企業にとって、強力な羅針盤となるでしょう。
【注目コンテンツ】
・100年企業のグローリーがMES導入を3年間で全社展開を成功させた秘訣とは
・エンジニアの精鋭部隊が集結した合弁会社「DTダイナミクス」設立で生産性が3倍に。内製化支援と技術移転、成功の秘訣とは
・日本の高スキル人材の活躍の場は世界にある アクセンチュアが「ものづくりを変革する」で描く製造業の未来とは