課題・要望
- 自社技術の外販にあたり、導入先ごとに事前の膨大なデータ収集が必要となる点が、顧客にとって導入のハードルになっていた
- 約200台ある工作機械の稼働状況確認や予知保全が十分ではなかった
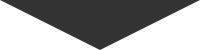
システムの開発力に加え、新たな価値を創出する提案力で企業成長をサポート
解決策・効果
- 事前のデータ収集が不要なシステムを開発することにより、外販可能性が高まった。また、異なる視点からの提案により新たな商品化へのロードマップも描くことができた
- 工場の自動化を推進するシステムの開発により、中長期的な戦略構築にも寄与
インタビュー
シリコンやガラス、セラミックスなど、「硬脆性材料(こうぜいせいざいりょう)」と呼ばれる加工難易度の高い素材の加工技術に定評があり、国内のみならず世界各国からの注文に対応する芝技研。
特に半導体や宇宙開発関連の研究開発部門で圧倒的な実績を挙げている同社の課題とその解決方法、さらに今後の企業戦略について、取締役副社長の福島大二郎さんにお話を伺いました。

株式会社 芝技研
取締役副社長 SE部統括本部長
福島 大二郎 様
―素材加工技術力の高さを強みとする芝技研さんですが、具体的にどのような技術なのでしょうか?
芝技研は約40年間にわたってシリコンやガラス、セラミックスなどの研削加工を手がけてきました。これらの素材は「硬脆性材料」と呼ばれており、細かいひびや欠けができやすいという特徴があります。
弊社の主力製品である半導体部品を例に挙げると、厚さ1cmのシリコン板に直径0.4mmのごく小さな穴を1,000~3,000個ほど等間隔に開けるといった作業を行います。精密部品ですからミクロンレベルの欠けやひびも許されません。
また、時には非常に高価な素材を加工することもあります。そうした場合は素材を壊さないように慎重に作業を進めるため、1つの製品が完成するまでに数カ月間かかることも珍しくありません。そして、その期間中、素材を破損させないことが重要です。
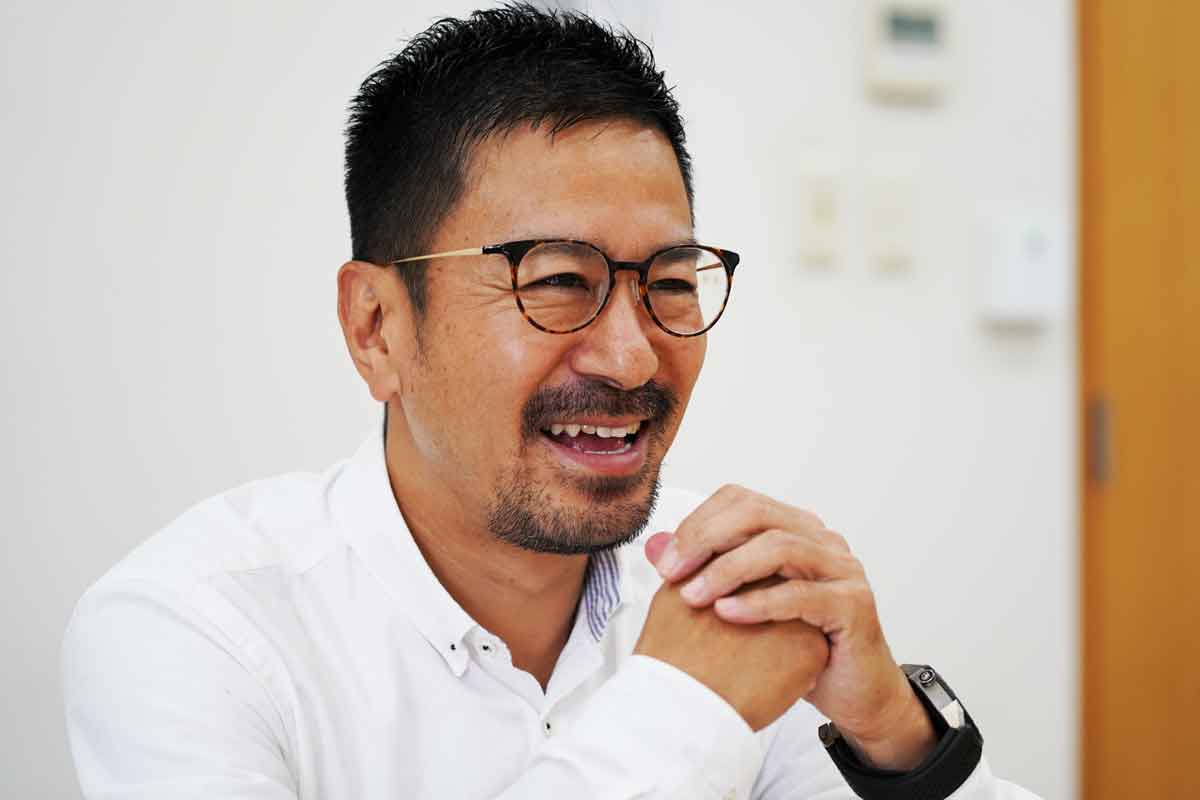
―素材を破損させないために、どのような工夫をされているのでしょうか?
加工精度を落とさないためのポイントは、工具の切れ味にあります。工具はダイヤモンドの粒でできていますが、何度も使うとどうしても切れ味が低下してしまうのです。切れ味の悪い包丁を使うと素材の断面を押しつぶしてしまうのと同じで、工具も切れ味が低下すると材料を壊してしまいます。
そこで弊社は、約20年前に「DLT(加工負荷フィードバック装置、Detect Load Technology)」を開発しました。加工中の工具や素材に掛かる負荷をリアルタイムに検知する装置です。
この装置を活用し、一定の値以上の負荷が発生した際に自動的に工具を交換する仕組みを構築することで、不良品発生率は格段に下がり、加工のスピードも向上しました。同様の加工をしている会社は他にもありますが、DLTによる歩留まりの良さは圧倒的だと自負しています。
―そうしたなかで、どのような課題が発生していたのでしょうか?
従来、DLTについては外部に開示してきませんでした。しかし、オープンイノベーションが叫ばれる市場に対応し、新規開拓にもつなげるため、弊社の技術もオープン化していこうという方針に変わりました。
DLTを外部に公開して以来、「硬脆性材料」加工の領域だけでなく、それ以外の金属加工の領域でも興味を持ってもらえるようになり、おかげさまで様々な企業からお声がけをいただいています。
ただ、引き合いが増えるにつれて課題も見えてきました。DLTを導入するためには、素材ごとに異なる閾値(※)を設定する必要があります。そして、そのためにかなりの分量のデータを事前収集しなければならないことに、お客様が難色を示されたのです。
弊社でもDLTを開発した際、「硬脆性材料」の閾値を導き出すために試作を重ね、大量のデータを収集しました。しかし、この方法ではコストも時間もかかってしまいます。
こうした課題を解決するために、何らかのシステムを開発しなければならないと考えていました。しかし、弊社にはそのノウハウがありません。そこで、製造業に強いIT企業とパートナーシップを結びたいと考えていたときに出会ったのがCCTさんでした。
(※)素材又は工具の破損、品質不良等が発生する加工負荷の基準値
―パートナー選定にあたっては、他のIT企業も検討されたのでしょうか?
もちろん、情報収集はかなり綿密に行いました。積極的に展示会にも足をはこび、そこでCCTさんを知ったのです。依頼の決め手となったのは、製造業に対する幅広い知見でした。
弊社はグループ全体で約200台の工作機械を保有しており、それらの稼働状況を可視化し、予知保全を行う必要性を感じていました。製造業の分野に強みを持つCCTさんであれば、DLTの閾値に関する課題解決はもちろん、予知保全に関するノウハウもお持ちなのではないかと期待していました。
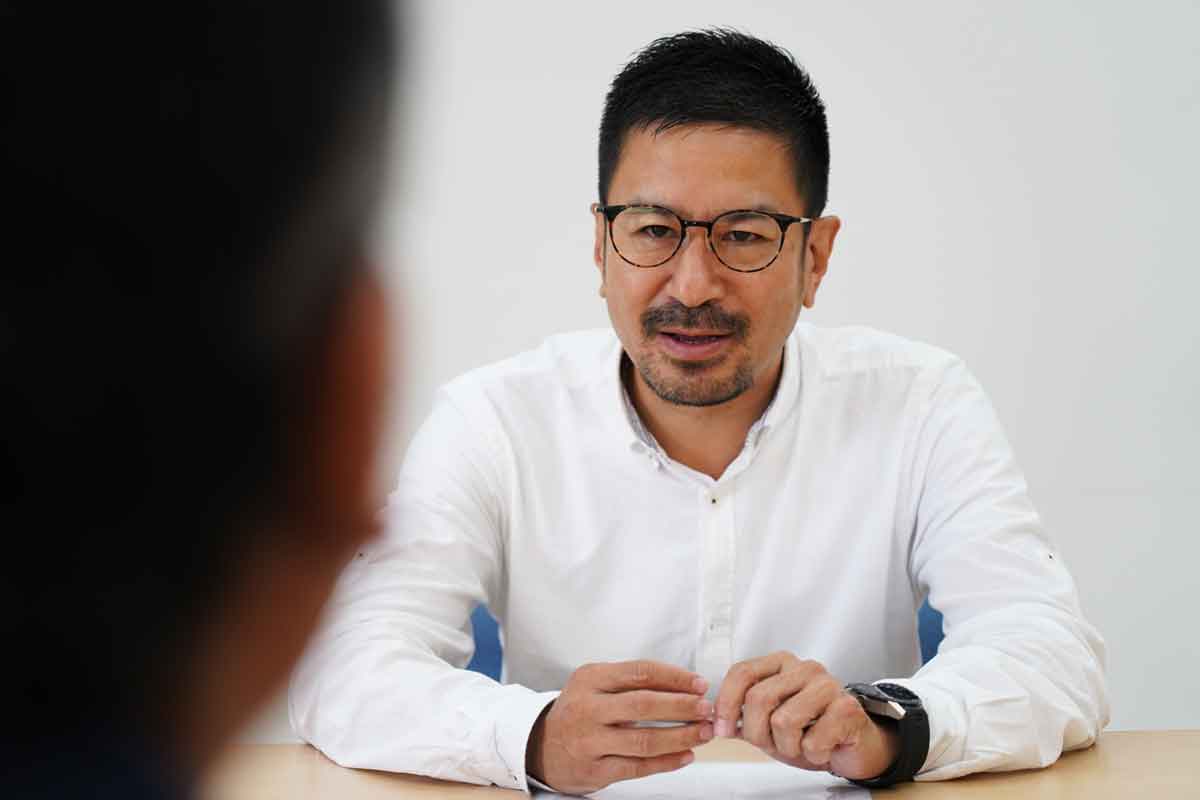
―その期待に応えることはできましたでしょうか?
はい。まず驚いたのは、非常にニッチな領域であるにもかかわらず、依頼直後からかなり深い部分まで業務を理解してもらえたことです。エンジニアだけでなく、営業担当者も技術的な部分について相当なレベルで理解していて、打ち合わせの場ですぐにレスポンスが得られました。また、弊社の要望を聞くだけでなく、CCTさんから様々なご提案をしてくれたのもありがたかったですね。
弊社もスピードと提案力をとても大切にしていますので、CCTさんは同じマインドを持つパートナーとして頼りになると感じています。閾値のデータ収集を不要にするシステム開発がスムーズに進んでおり、予想以上に早く実用化できそうです。
―現場での対応力はいかがでしょうか?
そもそも、弊社は工作機械も自社開発ですから、ゼロから設計・開発をしていくのが通常のフローです。常にチャレンジングな開発になりますから、簡単にうまくいくとは思っていません。
デバッグを繰り返して完成度を高めていきますので、CCTさんにはかなり細かい要求もしています(笑)。こうした要求にも、ちょっとした手直しを含め、メールレベルから現場対応まで速やかに柔軟な対応をしてくれるので助かっています。
―先ほど、CCTから提案させていただいたとのお話がありましたが、具体的にどのような提案が役に立ったのでしょうか?
まず、データの保存方法です。DLTで検知する工具の負荷に関するデータ量は膨大です。そのため、ストレージに蓄積するとすぐに容量が足りなくなってしまいます。それを知ったCCTさんは、すぐにクラウドへ送るシステムを構築してくれました。結果として、弊社の業務効率は飛躍的に向上しましたね。
さらに、DLTの異なる活用法も提案してくれました。そもそもDLTは加工負荷フィードバック装置ですが、CCTさんはさらに一歩進んで「切れ味変化の予兆検知をしてみてはどうか」というのです。
実際に正常時と異常時のデータを踏まえ、切れ味が変動する予兆を解析していただいたのですが、CCTさんの技術力の高さに驚きました。事前の予兆検知が可能になれば、今以上に歩留まりを上げることができますし、DLTの応用タイプとして異なる展開も可能となります。
―具体的にどのような展開でしょうか?
実際の加工作業となると、どうしても職人的な感覚が必要な場面もあります。たとえば、ちょっとでも異音を発したらすぐに機械を止めるといった具合に、技術者が近くにいなければなりませんでした。
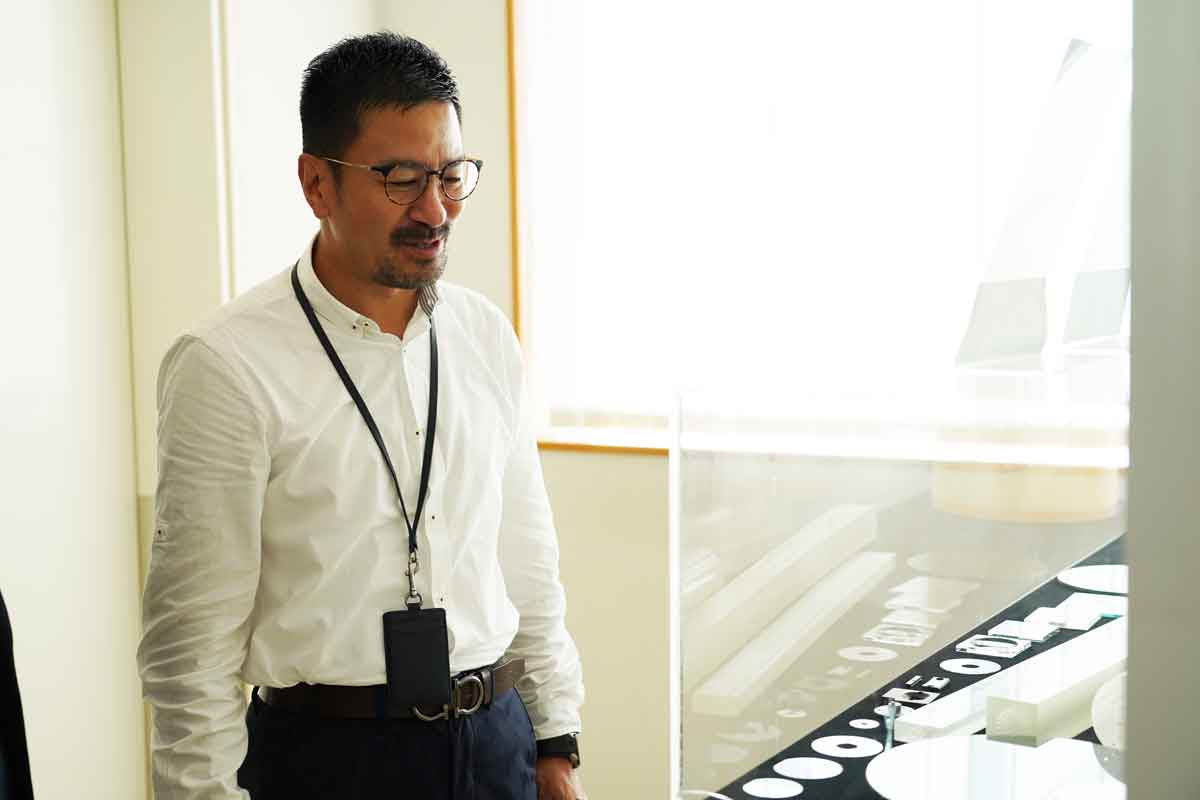
―ありがとうございます。最後に、今後の展望とCCTに期待することを教えてください。
そして、ゆくゆくはそれを商品化したいですね。少子高齢化と人口減少が進むなか、業務効率化と生産性向上の双方を実現できるシステムを提供することで、グローバルな規模で社会貢献できると確信しています。
その夢を実現するため、CCTさんにはこれからもいろいろな無理をお願いしてしまうかもしれませんが(笑)、ぜひ末永くお付き合いしてほしいと思っています。