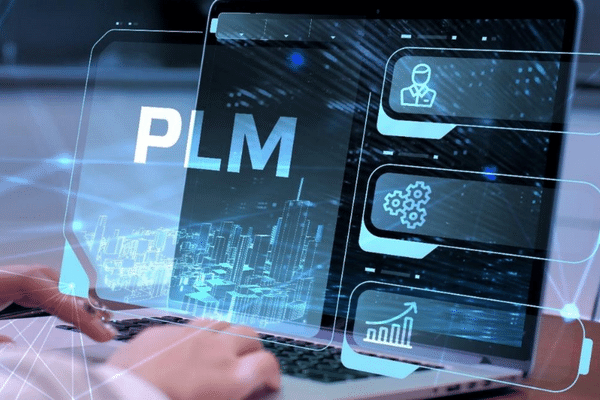
変化の激しいの時代を生き抜くために、製造業には製品開発力の強化が求められており、改めて注目を集めているのが、PLM(Product Lifecycle Management=製品ライフサイクルマネジメント)です。従来は部門ごとに分断されていた製品情報を、PLMを通じて統合・共有することで、開発期間の短縮や品質向上、コストの適正化といった効果が期待されます。
この記事では、PLMの概要から導入によって得られるメリット、導入時の注意点、さらには業界別の活用事例まで、わかりやすく解説します。
目次
PLM(製品ライフサイクルマネジメント)とは?
PLMとは、「製品の企画・開発から設計、製造、保守、廃棄に至るまでの全ライフサイクルを一元的に管理する手法・システム」です。日本語では「製品ライフサイクルマネジメント」「製品ライフサイクル管理」とも呼ばれ、特に製造業界を中心に活用が広がっています。ここでは、PLMの概要や成り立ち、PDM・ERPとの違いを解説します。
PLMの概要
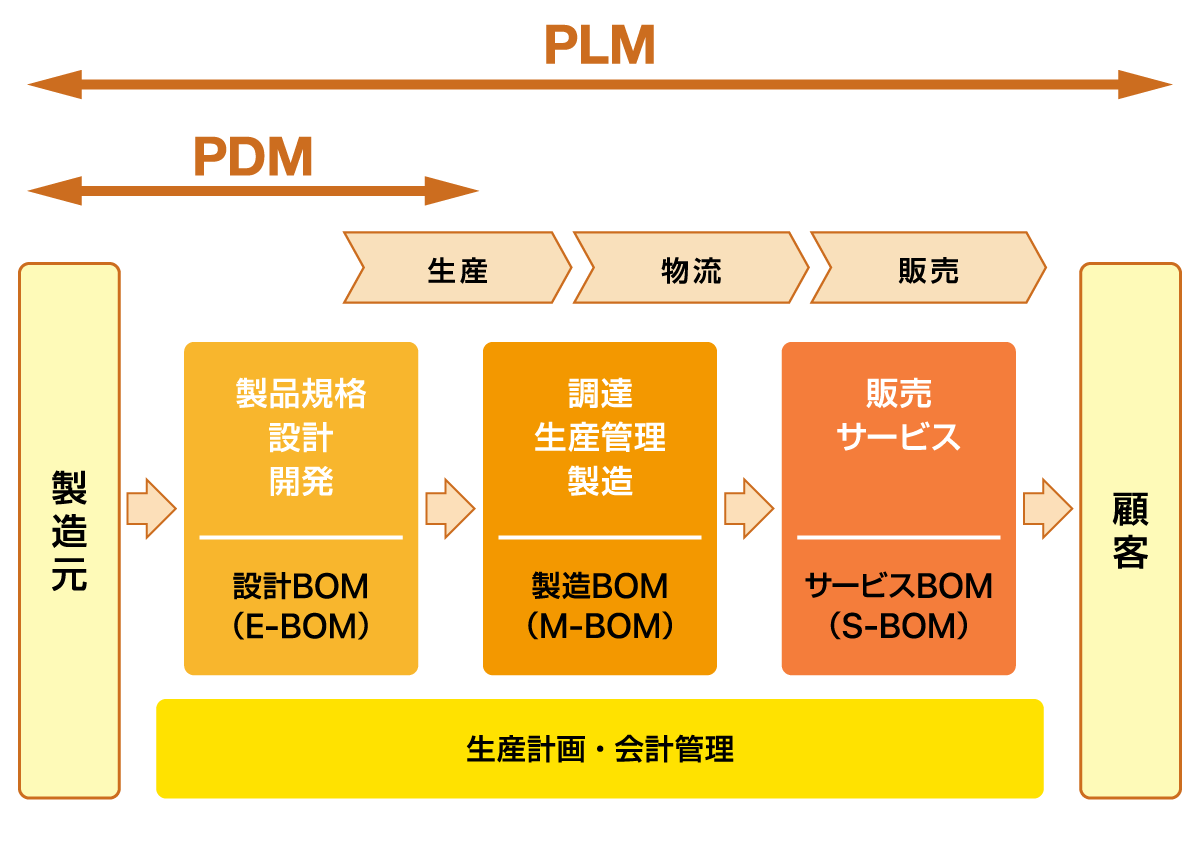
PLMは、あらゆる製造業にとって重要なQCD(品質・コスト・納期)の要素をさらに向上させることが目的となります。
QCDを継続的に向上させるためには、設計部品表やCADデータ、図面などの設計関連情報を一元管理し、さらにそれらを含めて、製品ライフサイクル全体で発生する情報を一元的に管理し、その情報を設計や開発部門だけでなく、モノづくりに係るすべての部門で共有することが大切です。このことを繰り返しながら、製品開発力の強化や業務効率の向上を実現していきます。
QCDとは
QCDとは、製造業やサービス業で重要視される3つの基本指標「品質(Quality)」「コスト(Cost)」「納期(Delivery)」の頭文字を取った言葉です。
製品やサービスを提供する際、企業はこの3つのバランスを最適化することが求められます。QCDは、単に効率を追求するだけでなく、顧客満足と競争力を高めるための重要な視点とされています。
要素 | 内容 | 重視する理由 |
---|---|---|
Q(品質) | 製品やサービスの性能、信頼性、安全性など | 顧客満足度やブランド価値に直結 |
C(コスト) | 材料費、人件費、製造・管理コストなど | 利益確保と価格競争力の源泉 |
D(納期) | 納品のスピードと正確さ | 顧客の信頼と取引継続に不可欠 |
たとえば、高品質でもコストが高すぎると市場での競争に負ける可能性があり、納期が遅れれば顧客の信頼を失います。そのため、QCDは三位一体で考えるべき概念とされ、製造プロセス改善やプロジェクト管理、外注先選定など、あらゆる現場で活用されています。
PLMの成り立ち
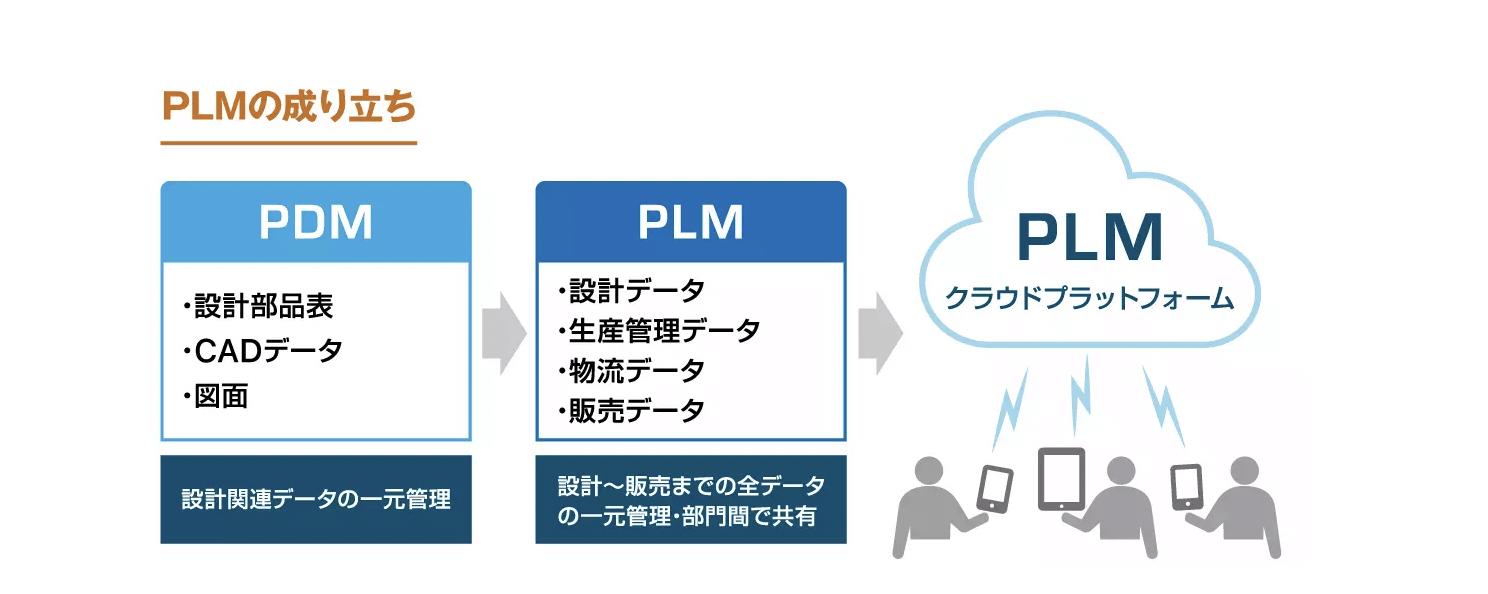
もともと多くの製造業では、PLMよりも前に、1990年代初頭から、設計部品表やCADデータ、図面などの設計関連情報を一元管理する「PDM(Product Data Management=製品情報管理システム)」に着目し、関連のシステムを導入していました。
しかし2000年代に入りグローバル化が進展する中で、さらにコンプライアンスを順守しようという意識が高まり、設計や開発部門だけが情報共有しているだけでは、競争に勝てないという考え方が主流となりました。そこでPLMの概念とそれを具現化するシステムの導入が盛んに進められるようになったのです。
その後、PLMシステムは単体のパッケージソフトウェアとして導入されていましたが、近年では、SaaS(Software as a Service)などのクラウドサービスとして提供され、さらに時代の流れに合わせて多様な技術を簡単に組み込めるようクラウドプラットフォームとして提供されています。
PLMとPDM・ERPとの違い
前述した通り、設計図面・CADデータ・BOM(部品表)といった設計データを一元管理するシステムです。一方、PLMはPDMの機能を包括しながらも、製品のライフサイクル全体に関与します。
- PLM(Product Lifecycle Management):製品ライフサイクル全体のデータを一元管理するシステム
- PDM(Product Data Management):CADやBOMなど設計段階での工程管理をするシステム。ワークフローや図面管理、BOM管理などの機能がある。
両者の大きな違いは、管理対象となるデータの範囲です。PDMが設計プロセスのデータのみを管理するのに対して、PLMでは製品ライフサイクル全体のデータを管理します。取り扱う製造工程やデータの範囲が異なるものの、PLMシステムにPDM機能が備わっていることもあり、明確な線引きはないのが現状です。
たとえば、ある製品をPDMで検索すると設計図面やCADデータしか閲覧できません。しかし、PLMではそれらに加えて、その製品の製造方法や在庫状況、顧客情報といったあらゆるデータを閲覧できます。
ERP(Enterprise Resource Planning=基幹業務システム)は、財務・人事・在庫管理など、企業全体のリソースを一元管理するシステムです。一方、PLMは製品に関わる「技術的プロセスの最適化」に焦点を当てており、ERPとは補完関係にあります。
つまり、PLMはPDMよりも広範な範囲をカバーし、ERPとは連携することでより強力な企業基盤を築くことができます。これらの違いを理解しておくことで、自社に必要なシステムを正しく選定しやすくなります。
<PLMとPDM・ERPとの違い一覧表>
項目 | PLM(製品ライフサイクル管理) | PDM(製品データ管理) | ERP(基幹業務システム) |
---|---|---|---|
管理対象 | 製品の企画〜廃棄までの全ライフサイクル | 製品の設計データ・図面・部品構成 | 財務・会計・在庫・生産など企業全体の業務 |
主な目的 | 製品情報とプロセス全体の最適化 | 設計データの一元管理と整合性維持 | 経営資源の最適配置と業務効率化 |
関係部門 | 開発・設計・製造・品質・保守など全体 | 主に設計・開発部門 | 管理部門(財務・経理・人事など) |
特徴 | 部門横断で製品情報を連携・共有 | 技術データの保管・検索・バージョン管理に特化 | 経営資源の全体最適を目的とした業務統合 |
他システムとの関係 | PDMやERPと連携して全体最適化を図る | PLMの一部として組み込まれることが多い | PLMと連携して製品情報を活用するケースあり |
PLMの主な役割
企業が持続的に競争力を維持・強化するために、PLMが担う役割は多岐にわたります。ここでは、PLMの代表的な4つの役割を解説します。
製品データの一元管理
PLMの基本機能のひとつが、「製品に関するデータの一元管理」です。製品開発では、CAD図面、仕様書、部品表(BOM)、試験結果など、膨大な技術情報が発生します。従来、これらのデータは部門ごとにバラバラに管理されていましたが、PLMを導入することで、全社的に統一されたプラットフォームで共有・更新できるようになります。
これにより、以下のようなメリットが得られます。
・データの重複・ミスの削減
・最新情報への迅速なアクセス
・設計変更の影響範囲の把握
特に、製品のライフサイクルが長く複雑な業界では、情報の信頼性と透明性を高めるために欠かせない仕組みです。
開発プロセスの可視化と最適化
PLMは、製品の企画から設計、試作、量産、保守に至るすべての工程を可視化し、プロセス全体の流れを一元的に管理します。各ステージにおける進捗状況や課題をリアルタイムで把握できるため、無駄や手戻りを防ぎ、開発の効率化を実現します。
また、標準化されたワークフローやチェックリストを導入することで、属人化した作業を防ぎ、業務品質を均一に保つことが可能になります。結果として、製品開発のスピードと精度が両立され、競争力のある製品づくりにつながります。
部門間のコラボレーション支援
PLMは、設計・製造・調達・品質管理・営業など、製品に関与するすべての部門間の情報共有と協業を促進します。従来は、部門ごとに独自の管理方法が取られ、情報の断絶が課題となっていましたが、PLMの導入により一貫性のある情報基盤が整い、シームレスな連携が可能になります。
たとえば、設計変更が発生した際には、調達や製造にも自動的に通知され、対応の遅れやミスを防止できます。PLMは、部門横断での「チームとしてのものづくり」を支える重要なツールなのです。
変更管理と品質管理の強化
製品開発においては、仕様変更や設計ミスへの迅速な対応が求められます。PLMは、変更管理(Change Management)機能を備えており、変更内容・理由・影響範囲を明確にし、承認フローの自動化も可能です。これにより、変更に伴う混乱や品質リスクを最小限に抑えることができます。
さらに、PLMは過去の設計データや不具合情報を蓄積・分析することで、品質改善に役立つナレッジベースを構築します。トレーサビリティ(追跡性)の確保も容易となり、万が一の不具合発生時にも迅速な原因究明と対応が可能です。
PLMを導入するメリットと効果
PLMは単なるデータ管理システムではなく、製品開発全体の最適化と経営効率の向上に直結する仕組みです。ここでは、PLMを導入することで得られる具体的な効果について解説します。
開発期間の短縮とコスト削減
PLMにより開発プロセスが可視化・標準化されることで、無駄な作業や手戻りが大幅に削減されます。設計変更の情報も迅速に関係部門へ共有され、対応スピードが向上します。これにより、開発期間が短縮され、製品の市場投入までのリードタイムが短くなります。
また、BOMの一元管理や設計の再利用が可能となり、材料費や工数の削減にもつながります。結果として、コスト競争力のある製品をより早く市場に提供できるようになります。
製品品質の向上とトレーサビリティ強化
PLMは品質管理とトレーサビリティを強化するための基盤としても機能します。製品に関するすべての情報が履歴として記録され、どの工程で何が行われたかを後からでも追跡できます。これにより、不具合発生時の迅速な原因特定と再発防止が可能となります。
また、過去の失敗事例や設計変更履歴を活用することで、品質改善のサイクルが回しやすくなり、継続的な品質向上が実現します。
市場投入までのスピードアップ
製品ライフサイクルの短縮化が進む中、企業にとって「いかに早く市場に出すか」が重要な競争要因になっています。PLMは開発フローを効率化し、関係部門間の情報伝達を迅速にすることで、製品の市場投入スピードを大きく向上させます。
特にグローバル市場では、需要の変化にスピーディーに対応することが求められます。PLMはその俊敏性を支える重要な基盤となります。
グローバル対応と多拠点展開支援
PLMは多言語・多通貨・タイムゾーン対応など、グローバルな製品開発にも対応しています。海外拠点を含めた複数の拠点間でリアルタイムに情報を共有できるため、地域間の情報格差をなくし、統一された開発環境を構築できます。
たとえば、日本で設計された製品の製造を東南アジアで行う場合でも、同じPLMプラットフォームを通じて最新の設計データや変更情報を即座に共有できるため、手戻りや品質のバラつきを防ぐことができます。
PLMシステム導入の注意点(デメリット)
PLMシステムは製品開発の効率化や品質向上に大きな効果をもたらしますが、その導入には慎重な準備と正しい運用が不可欠です。ここでは、PLM導入時に企業が注意すべきポイントを具体的に解説します。
現場の業務プロセスに合ったシステムを選定する
PLMシステムは多機能である半面、全ての企業に「汎用的に合う」わけではありません。自社の業務プロセス、部門構成、製品の性質などに適したシステムでなければ、導入後にかえって混乱を招くリスクがあります。
導入前には以下の点を確認しましょう。
・自社の製品ライフサイクルのどの段階を重点管理するか
・現場で使われている既存システムとの連携は可能か
・操作性やカスタマイズ性が十分かどうか
「大企業が導入しているから安心」という視点だけではなく、自社の現場課題にフィットするかを重視することが成功の鍵です。
社内の運用体制と教育体制を整備する
PLMは単なるITシステムではなく、組織の業務そのものを改革するための仕組みです。導入にあたっては、社内に適切な運用体制と教育体制を整える必要があります。
特に重要なのは次の点です。
・導入を推進するプロジェクトチームを設ける
・各部門のリーダーや現場担当者を巻き込む
・システムの利用方法や概念に関する研修を実施する
PLMは全社的に運用されて初めて効果を発揮します。特定の部門だけが理解している状態では、情報共有の断絶が起き、せっかくの仕組みも形骸化してしまいます。
既存システムとの連携とデータ移行を慎重に進める
多くの企業では、既にERPやPDM、Excelなどで情報管理がなされている状態からPLMへ移行します。このとき、既存データの移行や他システムとの連携をどう設計するかが極めて重要です。
注意すべき点は以下の通りです。
・既存データのフォーマットや品質を事前にチェックする
・データ移行時に重複や欠落がないよう検証環境でテストを行う
・ERPなど他の基幹システムとAPI連携が可能かを確認する
システム連携がスムーズにいかないと、業務が分断されたり二重入力が発生したりと、非効率な運用になってしまいます。
導入効果を測定し、継続的に改善する仕組みを構築する
PLMは導入して終わりではなく、運用開始後も継続的な改善が求められます。導入効果を数値で「見える化」する仕組みを設け、PDCAサイクルを回すことが重要です。
たとえば、以下のような指標を定期的にモニタリングします。
- 設計変更対応のリードタイム短縮率
- 設計ミスや不具合の発生件数
- プロジェクト進行にかかる工数削減効果
これにより、導入効果の定量評価が可能になり、経営層や現場の納得感を高めることができます。また、ユーザーからのフィードバックを基に、操作性や業務フローの見直しを行うことで、PLMの定着率をさらに高められます。
PLMの実行に必要な機能
PLMには、一般的に次のような機能が必要とされています。
機能名 | 概要 |
---|---|
ポートフォリオ管理 | 製品の全体戦略や企画の優先順位を管理し、リソース配分を最適化する。 |
要件管理 | 顧客や市場からの要求事項を製品仕様として整理・管理する。 |
図面管理 | 製品の設計図や仕様書をバージョン管理しながら一元管理する。 |
CADデータ管理 | CADソフトで作成された3D/2Dデータを安全かつ効率的に共有・管理する。 |
シミュレーション管理 | 設計段階での試作や動作検証結果(CAEなど)を管理・共有する。 |
設計BOM(E-BOM)・ 製造BOM(M-BOM)管理 | 設計時の部品構成(E-BOM)と製造現場向けの構成(M-BOM)を統合的に管理する。 |
設計変更管理 | 製品設計の変更履歴や影響範囲を記録・追跡し、関係者へ共有する。 |
開発スケジュール管理 | 製品開発の各工程の進捗状況やマイルストーンを可視化・管理する。 |
製造工程表管理・製造条件管理 | 製造手順や条件を標準化・文書化し、品質と生産性を確保する。 |
品質管理 | 不具合の分析や検査データを管理し、品質向上と是正措置を支援する。 |
原価管理 | 製品ごとの原価構成を把握し、開発・製造のコスト最適化を行う。 |
取引先・購買部品管理 | 部品や材料のサプライヤー情報を管理し、調達の効率化を図る。 |
サービス部品管理・保守管理 | 製品納入後の交換部品やメンテナンス履歴を一元管理する。 |
技術文書の作成・管理 | マニュアル、手順書、法規対応文書などを作成・管理・配信する。 |
実際には、このように多岐に渡る機能を1つのシステムですべて備えることは難しいため、複数のシステムを組み合わせたプラットフォームがPLMとして提供されています。また、PLMに求められる機能や業務内容は企業によって大きく異なるため、何らかのカスタマイズを加えた上で導入するケースが多くなっています。
業界別PLM活用事例|自動車・医療機器・アパレル
PLMは業界や企業ごとの課題に応じて、柔軟に活用されています。ここでは主要な業界別に、どのようにPLMが導入・活用されているのか、実際の事例や効果とともに紹介します。
自動車業界:設計〜量産までの高速化
自動車業界では、年々短くなる製品ライフサイクルと複雑化する部品構成への対応が求められています。PLMを導入することで、企画・設計・試作・量産までの各フェーズにおけるデータの一元管理が可能となり、意思決定の迅速化が実現されています。
たとえば、部品構成(BOM)の管理をPLM上で統合することで、設計変更の影響範囲が即時に共有され、手戻りや品質問題のリスクが大幅に削減されています。さらに、3D CADやCAEとの連携により、仮想検証による開発期間の短縮にもつながっています。
具体的には、自動車部品メーカーの東亜工業株式会社がPLMを導入し、開発プロセスの効率化を図った事例があります。
医療機器業界:厳格な品質管理と規制対応
医療機器分野では、ISO13485やFDA規制など、製品開発において厳格な文書管理とトレーサビリティが求められます。PLMはこれらの要件を満たすための基盤として活用されており、設計データと変更履歴、品質記録を一元的に管理可能です。
特に、リスクマネジメントやコンプライアンス文書の管理機能を持つPLMシステムを活用することで、監査対応がスムーズになり、製品開発から市販後サポートまでの透明性が高まります。グローバル展開企業では、拠点間の情報共有も効率化され、開発スピードの向上にもつながっています。
富士フイルム株式会社では、各国で異なる法規制・規格に適合するために医療機器向けの品質管理システムとしてPLMを活用しています。
アパレル業界:企画~販売までの短期化と在庫最適化
ファッションやアパレル業界では、トレンドの移り変わりが激しく、企画から販売までのリードタイム短縮が最大の課題です。PLMの導入により、デザイン、素材、パターン、コスト情報などを一元管理することで、商品開発サイクルの高速化が実現されています。
また、過去の販売実績や顧客データと連携させることで、より精度の高い需要予測が可能となり、在庫最適化や廃棄ロス削減にも貢献しています。海外生産拠点との情報共有や、デジタルサンプルによる商品企画も加速しています。
株式会社オンワード樫山では、全ブランドを対象にPLMシステムを導入し、企画・生産情報をサプライチェーン上で共有することで商品開発力を高めています。
海外PLMソリューション活用例
日本国内でも、グローバル展開を進める製造業を中心に、海外ベンダーのPLMソリューションが導入されています。たとえば、Dassault Systèmesの「3DEXPERIENCE」や、Siemensの「Teamcenter」などは、高度なデータ連携機能と業界別テンプレートを備えています。
日本のスポーツブランドであるアシックスは、3DEXPERIENCEプラットフォーム・オン・ザ・クラウドを導入し、製品の詳細情報を消費者に提供することで、購入意思決定を支援しています。また、マクニカは、クラウドベースのPLM(Siemens Teamcenter)を活用し、製品ライフサイクル全体でのデータ連携と業務プロセスの改革を進めています。
PLMの導入手順と5つのポイント
PLMの導入はさまざまなメリットをもたらしますが、より効果を高めるポイントが5つあります。
1.必要な機能と課題の洗い出し
PLMの導入手順の最初のステップは、組織内の要件や課題を明確にすることです。業務全体の課題と現状の環境の機能を洗い出し、必要な機能と導入によって解決するインパクトをまずは把握することから始めましょう。
そのためには、現行のプロセスやボトルネックを分析し、改善すべき領域を特定します。具体的なニーズが明らかになったら、必要な機能をリストアップします。
2. サービスの比較検討
必要な機能を洗い出したら、コスト、機能、サポートなどの項目について、複数のサービスを比較検討します。
PLMの導入には、複数のサービスプロバイダやソフトウェアベンダーの比較検討が欠かせません。各プロバイダの提供するサービス(機能、カスタマイズ性、拡張性、価格、導入サポートなど)を評価し、組織の要件に最も適したソリューションを絞り込んでいきます。そのほか、将来的なサポートが継続されるかどうかも重要です。アップグレードの可能性も考慮します。
製造業ではほかにも、さまざまな業務システムを使用します。ほかの業務システムと連携がしやすいように、拡張性が高いPLMを導入しておくとよいでしょう。
3.スモールスタートを意識して導入する
PLMの導入は企業全体に関わる大きなプロジェクトになります。失敗しないためには、慎重に導入を進めていかなくてはなりません。そこでおすすめなのが、スモールスタートです。
最初からすべての部門でPLMを使おうとすると、現場が混乱してしまって思うように活用できない可能性が高まります。また、実際に使い始めてから自社の業務に合わない機能が見つかったり、必要な機能が足りないことに気づいたりするケースも多いです。
そのため、最終的な目標を描きつつも、まずは1つの部門で機能を絞って導入し、改善や機能追加を繰り返しながら別の部門に横展開していくと失敗しにくくなります。
4.ほかの業務システムと連携させる
PLMは、ERPやSCMといったほかの業務システムと連携させることでより導入効果が高まります。ERPやSCMも製品のデータを必要とするため、個別にデータを管理するよりもPLMのデータを共有した方が効率的です。また、ERPで管理している経営資源の情報やSCMで管理している取引先情報なども、製品開発にとって重要なデータになります。
5.組織への浸透の促進、社員への教育、継続的な評価と改善
PLMの導入には組織全体へのPLMの浸透、情報共有しやすいコミュニケーションの環境づくりは不可欠です。プロジェクトのスケジュールとリソースの適切な管理、データの移行、社員のITスキルや情報セキュリティスキルの向上のためのトレーニングの実施も重要なポイントです。PLMの導入はその場限りで終わるものではなく、継続的なプロジェクトであり、導入後も定期的な評価と改善が必要です。
PLMとDXの関係:未来のものづくりを支える基盤
DX(デジタルトランスフォーメーション)の文脈においても、PLMは中核的な役割を果たしています。データ活用、業務プロセスの効率化、さらにはスマートファクトリーへの進化を支える基盤として、PLMが果たす役割はますます重要になっています。
PLMはDXの起点になる
DX推進において最初に直面する課題は、「現場にあるデータの分断」です。設計、製造、品質、購買など、部門ごとに異なるフォーマットやシステムで情報が管理されている状態では、業務のデジタル化は進みません。
PLMはこうした情報の“ハブ”として機能し、製品に関するすべてのデータを一元的に統合します。これにより、全社横断での情報活用が可能になり、業務の標準化・自動化といったDXの第一歩を実現できます。
IoT、AI、クラウドとの連携がもたらす変革
近年のPLMは、クラウド化やIoT、AIとの連携を強化しており、リアルタイムでのデータ収集や分析が可能になっています。たとえば、IoTセンサーから取得した製品の使用状況をPLMに連携させることで、予知保全や次期製品へのフィードバックが実現されます。
また、AIを活用した不良品の自動検出や、過去の設計データからの類似品検索なども進化しています。クラウド基盤上でPLMを展開することで、拠点間のデータ同期や在宅勤務でも支障のない設計・開発が可能になるなど、柔軟な働き方との相性も良好です。
将来的なスマートファクトリーへの布石としてのPLM
スマートファクトリーは、設備や人・物がネットワークでつながり、自律的に稼働する工場です。その基盤となるのが、製品情報と生産情報のリアルタイムな統合と連携であり、まさにPLMが担う領域です。
PLMによって製品仕様や設計意図が製造現場に正確に伝達され、生産設備がその情報をもとに自律的に動くことで、個別生産と大量生産の両立が可能になります。また、工場内のセンサーやロボットからのフィードバックもPLMに反映され、継続的な最適化サイクルが実現されます。
PLM導入で課題解決を
今回は、これからの製造業を支えるデータ基盤となり得るPLMについてご紹介しました。PLMを導入することで、製造業は製品開発力の強化や業務効率の向上といったメリットを得られるだけでなく、さらなるDXに取り組む基盤も整えることができます。製造業の方々が抱える課題を解決できるPLMの導入を検討してみてください。
【注目コンテンツ】
・エンジニアの精鋭部隊が集結した合弁会社「DTダイナミクス」設立で生産性が3倍に。内製化支援と技術移転、成功の秘訣とは
・新たな建築プロセスを目指す「設計BIMツール」開発、400年の歴史を誇る竹中工務店が描く理想の建築業界とは
・事業の進化、組織の改革、THKの変革を支える「二項動態」の考え方