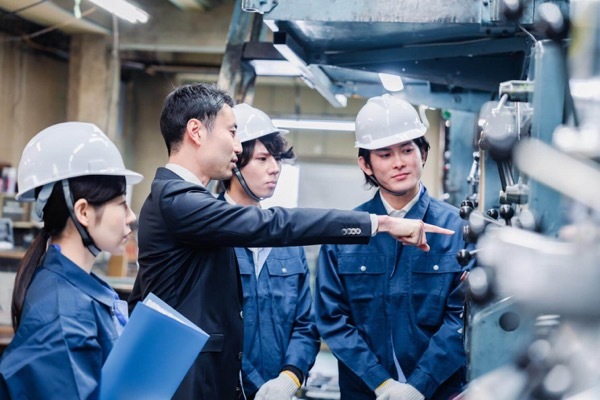
製造業にとって設備の稼働率向上と製品の品質維持は、重要な課題です。しかし従来の保全方法では、設備劣化や予期せぬ故障による生産停止が避けられず、目標達成が困難な状況も少なくありませんでした。
TPM(Total Productive Maintenance)は、「全員参加の生産保全」と呼ばれる日本発の管理技術です。生産システムのロスを削減し、継続的な生産性向上と収益の確保、生産性向上を実現する保全手法といえます。本記事では、TPMの概要や8つの柱、導入効果などについて詳しく解説します。
目次
TPM(Total Productive Maintenance)とは
はじめにTPMについて定義や概要、歴史を解説します。
TPMの定義|「全員参加の生産保全」とは
TPM(Total Productive Maintenance)とは、和訳すると「全員参加の生産保全」となります。生産現場のすべての従業員が、生産設備の保全活動に積極的に参加し、設備の寿命を延ばし、生産性の向上を目指す活動です。TPMの特徴は、生産性の向上と現場のロス削減を目指すアプローチ方法として現場で働く「人」や「設備」を中心としている点です。
設備に計画的なメンテナンスを実施することで、生産活動を円滑にし、最終的には「ロスを削減し生産効率を高める」「品質の高い製品の製造を継続できるようにする」といったことを目標としています。1971年にTPMを提唱した公益社団法人 日本プラントメンテナンス協会(JIPM)は、TPMを以下のように定義しています。
「生産システム効率化の極限追求(総合的効率化)をする企業の体質づくりを目標にして、生産システムのライフサイクルを対象とし、“災害ゼロ・不良ゼロ・故障ゼロ”などあらゆるロスを未然防止する仕組みを現場現物で構築し、生産部門をはじめ、開発、営業、管理などの全部門にわたって、トップから第一線従業員に至るまで全員が参加し、重複小集団活動によって、ロス・ゼロを達成すること」
(出典)公益社団法人日本プラントメンテナンス協会:「TPM」とは?
以下の表は、TPMを導入して達成が期待できるもの、導入の目安となる項目をまとめたものです。
【表】TPMで達成できるもの
目的 | 内容 |
---|---|
設備の寿命を延ばす | 定期的な点検や清掃、小さな故障の早期発見・修理によって設備の寿命を延ばす |
生産性を向上させる | 設備の故障を減らして稼働率を高めることで生産性を向上させる |
製品の品質を向上させる | 設備の良好な状態を維持することで不良品の発生を防ぎ製品の品質向上につなげる |
ロス・ゼロの達成 | 災害や不良、故障などあらゆる「ロス」を未然に防止する |
コストの削減 | 設備の故障による損失や不良品発生によるコスト削減に貢献する |
従業員の育成 | 保全活動への全員参加を通じて従業員のスキルアップとモチベーションの向上を図る |
TPMの世界への広がり
もともとTPMは、1950~1960年代に米国から「PM(Preventive Maintenance:予防保全)」として入ってきた理論が基本となっています。ほかにもPM(Productive Maintenance:生産保全)、CM(Corrective Maintenance:改良保全)、MP(Maintenance Prevention:保全予防)など、さまざまな生産現場における設備管理や保全に関する理論と実践方法を学んできました。
これら米国流PMなどからの学びを経て、日本流の生産予防保全として生み出されたのがTPMです。それ以来、TPMは導入した生産現場や企業での大きな成果が認められ、発展を続けました。2024年現在、TPMは、すでに50年以上の歴史があります。
日本だけでなく世界中に広がりを見せており、製造業や生産現場だけにとどまらない、あらゆる業種への応用や活用が可能なマネジメント手法として注目を集めています。日本式のTPMは、米国流PMがもとになっていますが、以下の点で異なります。
【違い1】
米国流PMでは「設備の使い方」「具体的な保全の仕方」など現場に落とし込める統合的な内容にはなっていません。TPMは、この点を発展させています。
【違い2】
米国流の場合、オペレーター(製造各工程での操作などを行う従業員)は保全に関わりません。自分の領域となる機械の運転操作だけに従事します。保全は、保全担当が行う仕組みです。一方、TPMはオペレーター自身が自分の担当する設備の日常保全(清掃や点検など)も行います。これを自主保全といいます。定期的な機械の検査や修理のみ専門員が行います。
【違い3】
日本式TPMの最大の特徴は、複数の小集団を組織し、この小集団を「柱」(Pillar)と呼びます(「8本の柱」で後述)。柱ごとの「全員参加」で生産保全を行う点が、米国流PMとは異なります。発展するTPMは、現在は国内だけでなく、国際規格での標準化も進められています。
- JIS Z8141:2001(日本産業規格)での定義
- IATF16949:2016(国際規格)でシステムとしての構築を要求中
- TPMに関するPAS1918(公開仕様書)の発行(BSI:British Standards Institution=英国規格協会による。2022年7月)
TPMの発展
前述のとおり、TPMは生産現場のメンテナンス、設備活用のための自主保全やその効率化が原点です。この改善行動や理念は、企業の力を高め、そこで働くさまざまな業務に従事する社員のモチベーションを高めます。つまり組織能力全体を高められる手法といえるでしょう。
そのため近年においてTPMは、生産現場での活用にとどまらず「企業の継続的発展を支える」ことが期待でき「業界や分野を限らず」応用できる新しい経営モデル、またそれを構築する手段として進化しています。解釈が拡張され、“Total Production Management”、すなわち「全員参加の生産経営」という名称も生まれています(略称は同じ「TPM」)。
TPMが注目されている理由
TPMが世界規模で注目を集める理由としては、主に以下の4つが考えられます。
(1)近年の市場の競争激化と競争力強化の必要性
(2)設備の高経年化や多様化に対応する管理適正化、高度化の必要性
(3)サステナビリティへの対応と企業価値の最大化
(4)従業員全体のモチベーションや業務への意識改革
(1)近年の市場の競争激化と競争力強化の必要性
現代は、IT化やDX戦略などにともない従前と比較して企業の経営方法自体が変化しています。市場の変化スピードも速く、情報を適切に早く取得し分析しなければ市場競争に勝ち残ることは難しい状態です。TPMの目的は「ロスをなくすこと」です。これを実現することで生産体制の安定化や製品品質の向上、コストの削減などが実現します。結果的に自社の競争力強化が期待できます。
(2)設備の高経年化や多様化に対応する管理適正化、高度化の必要性
IT化やデジタル技術の進化により、新しい技術や設備を導入する製造現場も少なくありません。しかし一方で過去から現在も稼働し続けているレガシーシステムが多数あることも日本の製造業での問題となっています(2025年の崖問題)。
レガシーシステムと呼ばれる古いシステムは、現在の規格システムとの連携が難しく、しかし慣れた機械でまだ動くものを廃棄もできず(コストの問題もある)……という工場が多いことが現状です。この問題は、TPMとはまた別の軸になるものですが、少なくともTPMの活動により設備や現場の課題が見え、改善へと的確に動き出す可能性があります。
(3)サステナビリティへの対応と企業価値の最大化
SDGs(持続可能な社会)を標榜するインダストリー5.0、Society5.0などの策定が世界規模で進んでいます。現代の企業は、自社のことだけを考えるのではなく関係するステークホルダーすべてに利益を還元し、それが循環かつ持続するサステナビリティ経営を求められています。
このサステナビリティは、企業の評価指標にもなっており、企業価値を高めることにつながるため、積極的に取り組む企業が増加傾向です。TPMは、保全活動が主体になるため、もともとサステナビリティの考え方とは相性が良い一面があります。TPMに取り組むことで投資家などからの評価が高まる可能性もあるでしょう。
(4)従業員全体のモチベーションや業務への意識改革
TPMは「全員参加」がその主軸のため、他人ごとにせず自分たちの現場や設備を自分たちで理解し保守する活動です。また「自主保全」のためにTPMでは、従業員や参加する人すべてのモチベーションを高めることが重要になります。
部門や役職に関係なくTPMでの「柱(活動の単位となる小集団。後述)」は、さまざまなメンバーが参加します。そのためお互いの考え方の違い、業務への理解などが深まり、ひいてはモチベーションの向上につながるのです。
TPM活動における16大ロス
TPM活動を導入しようと考える生産現場では、なにかしら課題を抱えています。TPMでは「設備や⼯程が理想的に稼動している状態」と「現在の稼動状態の差分(ギャップ)」を「ロス」ととらえています。ロス削減には、まずロスを明らかにし、それがどのような種類のロスなのかを定義することが必要です。
ここでは「TPM活動における16大ロス」について「設備の効率化を阻害する8大ロス」「人の効率化を阻害する5大ロス」「原単位の効率化を阻害する3大ロス」に分けて解説します。
設備の効率化を阻害する8大ロス
設備の効率化を阻害する要因として、以下の8つのロスが挙げられます。
1.故障ロス
設備の故障によって発生するロスです。突発的な故障だけでなく慢性的に発生している小さな故障も含まれます。故障による時間的なロス(生産時間の減少)だけでなく不良品発生による物量的なロスも発生します。
2.段取り・調整ロス
製品の切り替え時や設備の調整に要する時間的なロスです。段取り時間そのものだけでなく段取りミスによる不良品発生や再作業なども含まれます。
3.刃具交換ロス
刃物や工具などの交換に要する時間的なロスです。交換作業そのものだけでなく交換前の刃具の摩耗による加工精度低下や交換後の刃具の調整に要する時間なども含まれます。
4.立ち上がりロス
設備を始動してから安定した生産状態になるまでの時間的なロスです。製品の初期不良や設備のウォーミングアップに要する時間などが含まれます。
5.チョコ停・空転ロス
短い時間での設備停止(チョコ停)や設備が稼働しているものの製品が生産されていない状態(空転)による時間的なロスです。人為的なミスや小さなトラブルが原因となることが多い傾向があります。
6.速度低下ロス
設備速度の低下で発生する時間的なロスです。故障のほか、機械の摩耗や潤滑油不足などが原因となることもあります。
7.手直し・不良ロス
製品の不良や、仕様から外れた製品を修正するために必要な時間的なロスです。不良品そのものの廃棄による損失も含まれます。
8.シャットダウン(SD)ロス
設備の定期的なメンテナンスや大規模な修理のために設備を停止する時間的なロスです。停止時間そのものだけでなく再起動に要する時間や生産の遅延による損失も含まれます。
人の効率化を阻害する5大ロス
TPMでは、設備だけでなく人に関わるロスも生産性を低下させる大きな要因としてとらえられています。人の効率化を阻害する5大ロスは、以下のとおりです。
9.管理ロス
管理ロスとは、作業者が作業そのものを行うのではなく作業に関する指示を待つ時間や材料待ち、故障修理待ちなど作業が中断される時間的なロスのことを指します。待機時間をスケジュール管理などでうまく調整することが必要です。
10.動作ロス
動作ロスとは、作業者が無駄な動作などをすることで生じるロスのことです。原因としては「作業手順が非効率的」「作業場所や作業レイアウト、動線が合理的に配置されていない」「工具や材料の配置が不適切」などが挙げられます。改善策としては、作業手順の標準化や作業場のレイアウト改善、工具や材料の配置の最適化、従業員へのモーションスタディの実施などが考えられます。
11.編成ロス
編成ロスとは、生産ラインにおいて作業者が複数作業を同時にこなせず、作業の順番待ちが発生したり、作業が中断されたりすることで生じるロスのことです。ベルトコンベアのラインバランス崩れによるロスも含みます。複数作業を同時進行しているときに起こりやすい傾向です。作業ラインのバランス調整や作業者の教育・訓練、作業順序の最適化などを行う必要があります。
12.自動化置き換えロス
自動化できる作業を人が行っていることで生じる時間やコストのロスです。製造だけでなく物流のロスなども含みます。自動化については、さまざまな定義がありますが、製造現場では必要な自動化を進めることでロスが減り効率性が上がることが一般的です。ただしそれも保全がなされており、自主保全を行う従業員のモチベーションが高いことが前提となります。
13.測定調整ロス
製品の品質を確保すること、つまり不良品発生を防ぐためには測定や調整が必要であり、それに要する時間的なロスを指します。不調品の発生が多発すると測定に時間がかかりますが、そもそも不良品が発生する場合、さまざまな要因が考えられます。ロス全体の改善を行い、不良品を削減する工夫が必要です。
原単位の効率化を阻害する3大ロス
原単位とは、製品1単位を生産するために必要な資源(原材料、エネルギー、労働力など)の量のことです。原単位が小さいほど生産が合理化されていると評価されます。原単位を下げることはコスト削減に直結するため、多くの企業が取り組んでいます。原単位の効率化を阻害する要因としては、大きく3つのロスが挙げられます。
14.歩留まりロス
歩留まりロスとは、投入した原材料に対し最終製品として回収できる割合が予定より低い場合に発生するロスのことです。歩留まりとは、製品製造にかかる原材料や部品、素材送料に対して、どれだけの出来高が得られたかを表します。
15.エネルギーロス
エネルギーロスとは、生産活動において消費されるエネルギー発生に関連するロスのことです。ムダなエネルギーを使用していないかのチェックを行い、必要十分な量を標準化・最適化することでロスを低減できます。
16.型・治工具ロス
型・治工具ロスとは、製品を製造するために必要な型や治具の消耗、交換、および副資材のコスト過多によって発生する金銭的ロスのことです。長年同じ型などを使っているとどうしても経年劣化を起こします。型・治工具の破損などを可能な限り抑え、交換や修理のサイクルを延ばせばロスを縮小できます。
なお3大ロスの改善については、4M(製造業における4つの要素:「Man(人)」「Machine(機械)」「Material(材料)」「Method(方法)」)で「Machine」(16大ロスでは「設備」にあたる)に分類されることもあります。しかしTPMでは、原単位のロスに分類されており、その点が4M分類とは異なります。
【関連記事】
4Mとは?4M分析と製造業の品質管理に関わる各要素を解説
ロスを防ぐTPM活動の8本柱とは
TPMの8本柱の内容をそれぞれ端的に示すと、以下の表現となります。
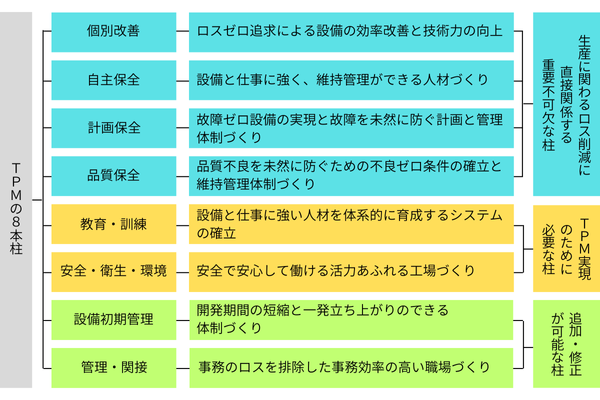
TPMでは、その具体的な活動において生産に関わるすべての部門や職域でその枠を越えた小集団のチームを作って行います。この小集団活動をTPMでは「柱(Pillar)」と呼びます。主な柱は、以下の8本です。
<8本の柱>
(出典)公益社団法人 日本プラントメンテナンス協会
生産に関わるロス削減に直接関係する柱(重要不可欠な柱):「個別改善」、「自主保全」、「計画保全」、「品質保全」
TPMを実施するためには必要な柱: 「教育・訓練」、「安全・衛生・環境」
企業や工場において、適宜追加・修正が可能な柱:「設備初期管理」、「管理・間接」
TPM活動の基本「自主保全」の7ステップ
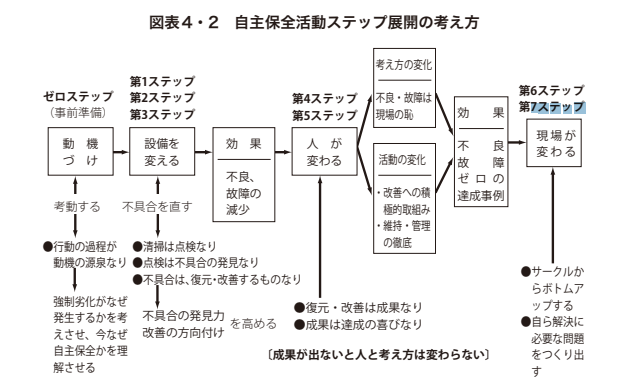
自主保全では「現場のオペレーターが自分の扱う機械の日常的な状態維持も自主的に行う」というのが基本的な考え方になります。具体的には、設備の清掃や点検、簡単な修理といった具合です。公益社団法人日本プラントメンテナンス協会によると自主保全の基本は、以下のとおりです。
① 設備の故障や品質不良は、設備に携わっているすべての人がその考え方や行動を変えれば、“不良ゼロ”“故障ゼロ”にすることができる。
② 設備が変われば人が変わり、人が変われば現場が変わる。
③ 職制主導のもとに、活動は全員参加で段階的にステップ方式で確実に行い、レベ
ルアップを図っていく。
「操作担当者が保全も行う」というのは、なじみが薄いかもしれません。実際、前述のようにTPMのもととなった米国流PMでは、“自主保全”という考え方はなく、扱う人とメンテナンスを行う人は分業です。日本式TPMでは、この自主保全を7つのステップに分けて段階的に進めることで効果的に設備の維持管理を行うことができます(なお事前準備段階のゼロステップを入れると8段階になります)。
第1ステップ~第3ステップ:設備を変える(清掃・点検・不具合発見)
設備の清掃や点検を行う段階です。またこの活動のなかで不具合を発見する力を身につけます。見つかった不具合などを改善することで不良や故障原因の減少につながります。
第4ステップ~第5ステップ:人(の意識)が変わる
第1~3ステップを行い、設備や環境が変わる「成果」が出ることで、その場で実際に働く人の意識が変わります。「故障や不良品が多発することは現場の恥だから維持管理や毎日の清掃などを行う」という意識改革です。これは、誰かに言われてやらされるのではなく自主的にその人がそう考えて行動することで、より高い効果が期待できます。
すでに最初の3ステップまでで成果が出ていると、“おのずと人の意識は変わる”というのがTPMの考え方です。このステップで人の意識が変わり行動が変わると結果として不良品ゼロやムダなコストの削減など新しい「成果」が出ます。
第6~第7ステップ:現場が変わる
自主保全活動が活発化し標準化する段階です。このステップになると最初に課題となっていたものは、おおむね改善され、ほとんどの人が達成感を感じ業務へのモチベーションが上がっています。またより広い視点で企業の利益を出すためにどうすればよいかを考えられるようになるでしょう。それぞれが新たな課題を見つけ出し、それを解決するために動くことで、現場がより良くなっていきます。
【参考】TPMとTPSの関連性
TPMとTPS(トヨタ生産方式)は、どちらも製造業の現場における効率化と品質向上を目指す手法です。TPSは、生産システム全体を最適化した「ジャスト・イン・タイム(必要なモノを必要なときに必要なだけ作る)」と「ニンベンの付いた自働化(異常がわかればすぐ止めることで不良品を作らない)」を2本柱で成り立っており、ムダを徹底的に排除することを目指す考え方です。
一方、TPMは全員参加の設備保全によって設備の寿命を延ばし、ロスをゼロにし、生産性を向上させることを目指します。TPSが目指す全体最適化を実現するために、TPMは不可欠な要素であり一種の補完関係ともいえるでしょう。また両者とも最終的には「顧客満足度の向上」「コスト削減」「企業全体の競争力強化」という共通の目的を持っています。
TPSの考え方を導入してムダを徹底的に排除することで、TPM活動の効率化が図れるでしょう。同時にTPM活動により設備保全が進み、継続して稼働率が向上するとTPSの目指すジャスト・イン・タイム生産方式の安定稼働に貢献できると考えられます。
【関連記事】
7つのムダとは?トヨタの生産方式が指摘する「ムダ」と具体的な排除方法
まとめ
本記事では、TPM(全員参加の生産保全)について解説しました。TPMは、単なる保全活動ではなく企業全体の生産性向上を目的とした取り組みです。「機械を運転するオペレーターがその機械の保全の一部も担う」という日本で生まれた理論です。TPMを導入することで、企業は持続的な成長を実現することが期待できるでしょう。
(参考)
公益社団法人 日本プラントメンテナンス協会:「TPMとは」
同上:『次世代TPM実証研究レポート「経営に資する生産革新実践プログラム」』
※「TPM」は、公益社団法人日本プラントメンテナンス協会の登録商標です
【注目コンテンツ】
・DX・ESGの具体的な取り組みを紹介!専門家インタビュー
・DX人材は社内にあり!リコーに学ぶ技術者リスキリングの重要性
・サービタイゼーションによる付加価値の創造と競争力の強化