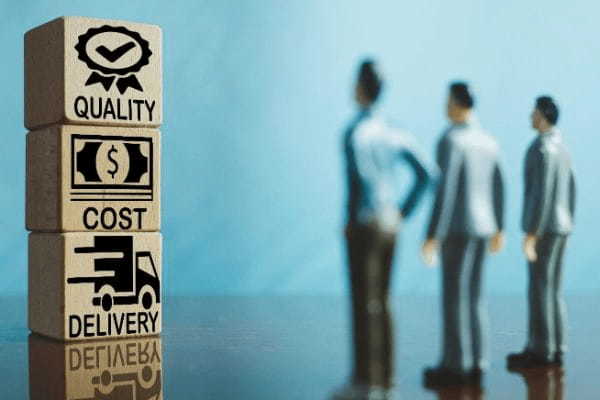
さまざまな企業の業務改善に関するキーワードに「QCD」があります。とくに製造業では、生産する商品の品質や納期、コストに直結し、企業の競争力を左右する重要な概念です。
本コラムでは、「QCDとは何か?」という基本から、製造業における優先順位の考え方、改善手順、さらにQCDDなどの派生用語まで幅広く解説します。製造業に携わる方にとって、QCDの理解と改善は避けて通れないテーマです。ぜひ参考にしてみてください。
目次
QCDとは
QCDとは、Quality(品質)・Cost(コスト)・Delivery(納期)の単語の頭文字をとった言葉です。
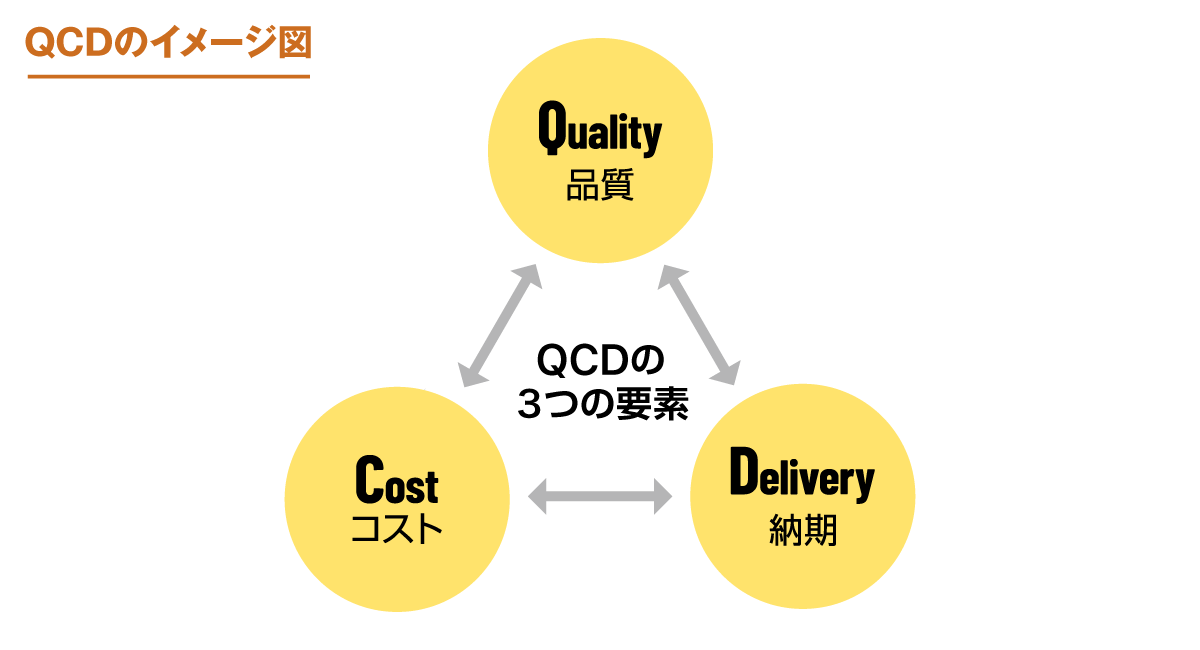
製造業では、顧客満足を高めるために品質の高い製品を作る必要がありますが、同時にコストの管理や納期の厳守も欠かせません。
品質を重視するあまりコストが膨らめば利益が減少し、納期が守れなければ顧客の信頼を失います。この3つの要素をバランス良く管理することが、製造業のQCDの基本です。
品質(Quality)
製品の品質は顧客満足に直結する要素です。一定の基準をクリアしていれば顧客の課題を解決でき、信頼性やリピート購入にもつながります。
一方、品質の低い製品が出荷されると、企業全体の評価やブランドに悪影響を及ぼします。製造業においては、重大な品質問題は安全リスクや訴訟にも発展しかねないため、多くの企業でQCDの中でも最優先されています。
コスト(Cost)
製品の原材料費、設備投資、人件費、光熱費などの総費用を指します。高品質な製品を作っても、過剰なコストがかかれば利益を確保できません。 コスト削減は利益を最大化する手段であり、競争力を高める鍵でもあります。ただし、過度なコスト削減は品質や納期に悪影響を及ぼすリスクがあるため、バランスが重要です。
納期(Delivery)
納期とは、顧客が希望する期日までに製品を届けることです。製品の完成だけでなく、配送も含めてスケジュール通りに進める必要があります。
納期の遅れは信用失墜につながり、逆に前倒し納品も顧客の事情によっては歓迎されないことがあります。リードタイムの短縮には、生産プロセスの見直しや物流の最適化が欠かせません。
QCDの相関関係
QCDの3要素は相互に影響を与える関係にあります。たとえば、品質を向上させれば検査や設備投資が増え、コストや納期に影響が出る可能性があります。
コストを削減しようとすれば、原材料の質や検査工程が簡素化され、品質が下がるリスクもあります。納期短縮を目指せば、工程の省略が必要になり、品質やコストに影響が及ぶこともあります。
このように、QCDの3要素はトレードオフの関係にあることが多いため、バランスの取り方が非常に重要です。
QCDの優先順位
製造業におけるQCDの優先順位は業種や顧客の要望によって異なりますが、一般的には「品質 > 納期 > コスト」とされることが多いです。
品質が基準を満たさなければ、どれほど安く早く納品しても意味がありません。次に重視されるのが納期です。いくら品質が良くても、期日を守れなければ信頼を失います。コストは企業側の問題であり、顧客に直接影響しないケースが多いため、3番手に位置づけられる傾向があります。
そのため、企業によってはその優先順位から「QDC」と表現することもあります。
QCDのバランス・優先順位を決めるコツ
QCDは各要素が密接に絡み合っていることから、優先順位の決め方に迷うことがあるでしょう。例えば品質とコストについては、トレードオフの関係にあることが一般的です。ここでは、QCDのバランスや優先順位を決めるコツについて解説します。
まずはQCDの中でも品質を最優先に据えましょう。いかに低価格で、かつ早期に納品されたとしても、顧客の求める品質を満たしていなければビジネスとして無意味であるためです。また、品質が低いことによって、顧客からの信用がなくなるとQCD以前にビジネスの土俵にも上がることができません。最低条件として、顧客が定める品質基準を満たせるような品質管理を心がけましょう。
次に、コストと納期について考えます。コストと納期は顧客の置かれた事情によって優先順位が変わるため、慎重に検討することが重要です。例えば、顧客が製品を必要とする時期が明確に決まっている、あるいは今すぐにでも必要といった場合には、多少コストがかかったとしても納期を優先する必要があります。一方で、顧客側の予算上限が決まっているケースなどではコストが最優先となります。コストと納期の優先順位を検討するにあたっては、顧客との丁寧なコミュニケーションを通して、顧客の潜在的なニーズを把握するようにしましょう。
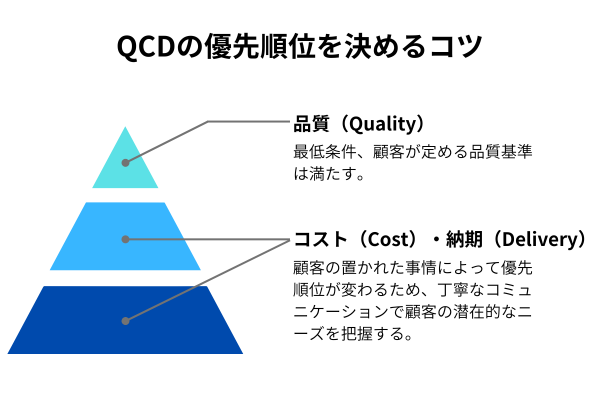
最後に、顧客の要望や市場環境といった外的要因のみならず、自社の製造現場にも目を配ることが重要です。例えば、過剰なQCDの追求によって現場に負荷がかかっていないか、自社内での業務効率化によってQCDのバランスを改善できないかといった観点があります。業務プロセスや材料の調達方法、物流ルートの見直しなどを通じて、QCDを全面的に向上できるケースもあるでしょう。
QCDの測定指標(KPI)と評価方法
ここでは、各要素における主要な測定指標と、それらを評価するための方法について解説します。
1.品質(Quality)
品質は、顧客満足度やブランドイメージに直結する最も重要な要素の一つです。製品やサービスの欠陥、不良率、顧客からの評価などを数値化して測定します。
・主な測定指標(KPI)
<不良率 / 欠陥率>
定義:生産された製品や提供されたサービスのうち、品質基準を満たさないものの割合。
算出方法:(不良品数 ÷ 総生産数)× 100% または (欠陥発生件数 ÷ 総サービス提供件数)× 100%
評価方法:目標値(例:ppm単位での目標設定)との比較、経時的な推移の分析。不良原因の特定と改善活動の効果を評価します。
<顧客クレーム件数 / 顧客不満率>
定義:顧客からの製品・サービスに対する苦情や問い合わせの件数、またはその割合。
算出方法:(クレーム件数 ÷ 総販売数または総顧客数)× 100%
評価方法:クレーム内容の分析(製品不良、サービス対応など)、件数の推移を監視し、改善策の有効性を評価します。
<歩留まり率>
定義:投入した原材料や部品から、良品として完成した製品の割合。
算出方法:(良品生産数 ÷ 投入総数)× 100%
評価方法:生産プロセスの効率性や品質安定性を評価します。歩留まり率が高いほど、無駄が少なく品質も安定していると判断できます。
関連記事:歩留まりとは?意味や計算方法、改善策まで徹底解説!
<初回生産良品率 (FPY: First Pass Yield)>
定義:生産ラインに投入された製品が、一度の工程で手直しなしに良品となる割合。
算出方法:(初回で良品と判定された製品数 ÷ 総投入製品数)× 100%
評価方法:各工程における品質の作り込み度合いを評価し、ボトルネックや不良発生源を特定します。
・評価方法
-各KPIの目標値を設定し、定期的に実績値と比較します。
-不良発生時の原因分析(例:5 Whys分析、特性要因図)を徹底し、根本原因を特定して再発防止策を講じます。
-顧客からのフィードバックを積極的に収集し、製品・サービスの改善に繋げます(例:アンケート、NPS)。
2.コスト(Cost)
コストは、製品やサービスを提供する上で発生する費用全体を指し、収益性や競争力に直結します。生産コスト、品質コスト、在庫コストなどを測定します。
・主な測定指標(KPI)
<製造原価 / 生産コスト>
定義:製品を製造するために直接的または間接的にかかった費用の総額。
算出方法:材料費 + 労務費 + 経費(製造間接費)
評価方法:目標原価との比較、単位あたりの原価の推移を監視し、コスト削減活動(例:VE活動、ムダの排除)の効果を評価します。
<品質コスト>
定義:品質の不備によって発生するコスト(例:不良品廃棄費用、手直し費用、クレーム対応費用)や、品質を維持・向上させるためのコスト(例:検査費用、品質管理費用)。
算出方法:予防コスト + 評価コスト + 内部失敗コスト + 外部失敗コスト
評価方法:品質問題が引き起こす隠れたコストを可視化し、予防活動への投資が、将来的な失敗コストを削減する効果を評価します。
<在庫維持コスト / 棚卸資産回転率>
定義:在庫を保管・管理するためにかかる費用(倉庫費用、保険料、陳腐化損など)、および在庫がどれだけ効率的に販売されているかを示す指標。
算出方法:(年間売上原価 ÷ 平均棚卸資産)
評価方法:過剰在庫はコスト増につながるため、棚卸資産回転率を高めることで、在庫コストの削減効果を評価します。
<生産性(労働生産性 / 設備生産性)>
定義:投入した労働力や設備から、どれだけの成果(生産量、付加価値)が生み出されたかを示す指標。
算出方法:(生産量または付加価値 ÷ 投入労働時間または設備稼働時間)
評価方法:効率的な生産体制が構築されているかを評価し、コスト削減に寄与しているかを判断します。
・評価方法
-原価計算システムを活用し、各コスト要素を詳細に把握します。
-ベンチマーク分析を行い、競合他社や業界平均との比較から、コスト競争力を評価します。
-継続的な改善活動(カイゼン、リーン生産方式など)を通じて、コスト削減の進捗を評価します。
3.納期(Delivery)
納期は、顧客への製品・サービスの提供スピードと正確性を示し、顧客満足度や市場での競争優位性に影響します。リードタイム、納期遵守率などを測定します。
・主な測定指標(KPI)
<納期遵守率 / 納期達成率>
定義:約束した納期通りに製品を納品したり、サービスを提供できたりした割合。
算出方法:(納期通りに納品された件数 ÷ 総納品件数)× 100%
評価方法:顧客からの信頼度を測る重要な指標であり、高い遵守率は顧客満足度の向上に直結します。
<リードタイム>
定義:注文を受けてから製品が顧客に届くまでの総時間(受注リードタイム)、または原材料が生産工程に投入されてから完成品になるまでの時間(生産リードタイム)。
算出方法:各工程の開始から完了までの時間を測定。
評価方法:リードタイムの短縮は、市場変化への迅速な対応や顧客への提供価値向上に繋がります。ボトルネックの特定と改善により、短縮効果を評価します。
関連記事:リードタイムとは?意味や短縮方法についてわかりやすく解説
<在庫日数 / 在庫回転期間>
定義:平均在庫が販売されるまでにかかる日数。
算出方法:(平均在庫金額 ÷ 1日あたりの売上原価)
評価方法:短いほど在庫が効率的に活用されており、納期遅延リスクの低減にも寄与します。
<生産計画達成率>
定義:事前に立てた生産計画に対して、実際にどれだけ生産目標を達成できたかの割合。
算出方法:(実際の生産量 ÷ 計画生産量)× 100%
評価方法:生産体制の安定性や計画の精度を評価し、納期遅延の根本原因を探る手がかりとなります。
・評価方法
-サプライチェーン全体を可視化し、各工程での遅延要因を特定します。
-生産管理システムやSCM(Supply Chain Management)システムを導入し、リアルタイムでの進捗状況を把握します。
-予測精度を高めるための需要予測システムを導入し、生産計画の最適化を図ります。
QCDの各要素は互いに関連し合っており、一方を改善することで他方に良い影響を与えることもあれば、逆に悪影響を与えることもあります。例えば、品質を徹底的に追求しすぎるとコストが高騰したり、納期が遅れたりする可能性があります。
そのため、KPIを設定する際には、企業戦略に基づき、各要素のバランスを考慮することが不可欠です。定期的にKPIの実績を評価し、目標とのギャップを分析することで、PDCAサイクル(Plan-Do-Check-Act)を回し、継続的な改善活動に繋げることが、QCDを最適化し、企業の持続的な成長を実現するための鍵となります。
製造業におけるQCD改善の重要性
製造業においては、品質・コスト・納期のいずれの要素も重要であり、各要素をバランス良く管理することでさまざまなメリットを得られます。ここでは、QCDを改善する重要性を解説します。
商品の品質改善・利益率の向上
製造業は作り出した商品が売れることで利益が生まれます。高品質な製品は顧客満足度を高め、リピートや紹介を促します。一方、品質が悪ければ顧客のニーズを満たすことはできず、売り上げにつながりません。そのため、QCDの改善はいずれの製造業が抱える課題であり、利益確保の要です。
商品の品質の水準が向上すれば売り上げアップを図ることができ、コストを削減できれば支出を抑えられて利益率も改善するでしょう。QCDはそれぞれの要素がお互いに影響を及ぼし合っているため、バランス良く改善する必要があります。このように、QCDを改善することにより商品の品質や利益率の向上が見込めます。
生産プロセスの最適化
QCDを改善するためには、生産プロセスの無駄を削減するなど全体の見直しが必要です。例えば、原材料の見直しや生産効率が高まる機械・システムの導入、作業員のスキルアップなども生産プロセスの効率化をもたらします。
そのためには、まず現状の生産プロセスの状況を把握する必要があります。生産工程を可視化するシステムを導入すると、各工程の不良品率や時間当たりの生産数などの数値を得られるでしょう。もし目標に達していない数値があれば、改善することにより生産プロセスを最適化できます。
顧客・取引先との信頼構築
QCDの品質と納期は、自社だけでなく顧客や取引先も関係します。品質を改善することで、商品を使用するユーザーの満足度は高まるでしょう。ミスがなく安定して高品質な商品を納品していれば、顧客からの信頼を得られます。
同様に納期を守ることは、商品が完成した後に出荷を担当する配送業者とも良好な関係を築けるでしょう。また、原材料を調達する際も自社の倉庫に余裕がなければ納品できません。生産プロセスを見直し、計画通りに生産・出荷できるようになれば、原材料も遅延することなく納品できるようになるでしょう。
そのため、QCDの向上を目標に生産プロセスを改善することは、既存の取引先からの信用を得やすくなり、今後のビジネスの長期的な発展が見込めます。
QCDの管理方法
QCDを適切な水準に保てば、企業は容易に利益を確保できます。そのため、品質・コスト・納期の徹底管理が必要です。ここでは、QCDの管理方法について要素ごとに紹介します。
品質の管理
品質管理の主な方法は一定の基準を設け、その基準を満たしているか生産プロセスの各ポイントでチェックします。プロセスごとに細かくチェックすることで品質を保ちやすくなるでしょう。また、製品の品質だけでなく生産設備の確認も重要です。
現在では、多くの製造工程が機械化・自動化されているため、その設備に問題が発生すると商品の品質にも影響します。他にも、エラーが多く発生している工程を優先的に見直すことにより、効率良く生産プロセスを改善できるでしょう。
ただし、チェック体制を厳格化しすぎると、コストと納期を圧迫する可能性があるため注意が必要です。
コストの管理
コストの管理では、まず現在の生産プロセスで発生している費用を洗い出します。原材料の費用だけでなく、人件費や生産設備の費用を可視化・明確化しましょう。また、生産プロセスに無駄が生じていると、コストの増大を招きます。生産プロセスの見直しや改善もコスト削減をもたらします。
ただし、必要以上にコストを削減し、原材料や生産設備、作業員の人数が必要数を下回ると品質や納期に影響が出る可能性があるため、注意しなければなりません。そのため、コストを管理する際は、品質と納期のバランスも考える必要があります。
納期の管理
納期を管理するためには生産スケジュール全体を把握する必要があります。そのためには、原材料の調達から生産工程、配送スケジュールなどサプライチェーン全体の動きを押さえることが重要です。
また、実際の生産スケジュールは、各工程での遅延リスクを踏まえて設定すると良いでしょう。生産工程では、各プロセスでスケジュール通りに作業が進んでいるかを確認します。プロセスに無駄があるとリードタイムが伸びることになるため、不要な工程を削減するなどの改善が必要です。
QCDと5S
QCDを適切に管理するための基本的な考え方に「5S」があります。これは整理・整頓・清掃・清潔・しつけの単語の頭文字をとった言葉であり、とくに整理・整頓の2Sが重要とされています。
例えば、工場内に不要な道具・備品・原材料などがあると、5Sの清掃・清潔の効率が悪くなります。整理・整頓の徹底によって必要なものだけに絞れば、5Sを実現しやすくなります。
5Sが実施できていない生産環境の場合、事故が生じやすく、不良品率も高くなる傾向があります。例えば、清潔でない現場であれば、製品にホコリやごみが付着する可能性が高くなり、品質に影響を及ぼします。
生産プロセスが非効率になれば、コストは大きくなりやすいです。必要な道具を探すのに時間がかかるなど、小さなことでも時間が発生することによってリードタイムが膨張し、納期に影響が出ることもあります。
QCDを改善するためには、システムの導入など大きな変革を実施するよりも先に、5Sを徹底するようにしましょう。
関連記事:5Sとは?業務効率化への一歩を踏み出すアイデアを解説
QCDを改善する手順
QCDを改善するためには、いくつかの手順に沿って実施する必要があります。適切な方法で課題を解決することによってQCDは向上するでしょう。ここでは、QCDを改善する手順の一例を紹介します。
1.現状を把握し課題を発見する
QCDを改善するためには、まず現状の生産工程を把握し課題点を発見します。重要なことは、自社にとって最適なQCDの優先順位を決定し、そのバランスを考えることです。そのためには、品質・コスト・納期のそれぞれの状況を把握します。
例えば、商品ユーザーへのヒアリングや、生産プロセスによる不良品率の算出によって品質をチェックできます。その結果が目標値を下回っていれば、問題を提起して課題を明確にすることが必要です。
2.改善策を作成する
課題が明確になった後は改善策を考えます。改善策を考える際は、計測可能な目標や基準を設定することが重要です。品質であれば顧客満足度や不良品率であれば計測可能です。
それを踏まえた上で、現状の数値を明確化して改善するためのアイデアを出し、それを実現するための具体的な行動を改善策として立案します。また、コストであれば金額、納期であれば日数など具体的な数値を設定しやすいでしょう。
3.改善策の実施し検証する
改善策を立案した後はQCDを改善できるように実施します。このとき重要なことは、実際に数値が改善しているのかを検証することです。しかし、改善策を実施してもうまくいかないこともあります。そのため定期的に結果を検証し、改善策を修正するなどPDCAサイクルを回す必要があります。このようなプロセスを繰り返すことでQCDを改善できるでしょう。
QCDの改善に役立つ生産管理システム
製造業におけるQCDを改善するためには、現状の生産プロセスを適切に管理する必要があります。そのときに役立つのが生産管理システムです。ここでは、QCDの改善に役立つ生産管理システムについて紹介します。
生産におけるさまざまな情報を管理する
生産管理システムは製造現場の在庫の数量や生産スケジュール、コストなどを一元管理する仕組みです。現状の生産体制をExcelなどで管理する場合、同時に編集できないことからリアルタイムに更新できず、全社的に共有することが難しくなるでしょう。そこで、1つのシステムを使い効率良く状況を共有し管理できれば、効率化を図りやすくなります。
主な機能には、生産計画や生産数などの数値を把握する生産管理機能や、受注状況や出荷、請求、売り上げなどを管理する販売管理機能、各プロセスの稼働状況や生産プロセスを管理する工数管理機能などがあります。
余剰在庫やコストの削減につながる
生産管理システムを活用することにより、生産・在庫・販売の状況が明確になります。必要な量の原材料を調達し倉庫の保管状況も把握できるため、無駄を省き余剰在庫が発生しにくくなります。また、工数を把握することにより、過不足を管理しやすくなるでしょう。
必要最低限の人員に抑えることで人件費の削減につながります。他にも、生産プロセスにおける無駄を削減することは、リードタイムの短縮も実現しやすくなりやすいでしょう。生産施設の規模が大きい場合でも、管理しているさまざまな情報を一元管理できる点も大きなメリットです。
ITシステム導入の必要性
経済産業省・厚生労働省・文部科学省の3省で共同作成している「2025年版 ものづくり白書」によると、デジタル技術を導入・活用した企業のうち約9割(「効果を感じている」「やや効果を感じている」を合わせた数値)もの企業がデジタル技術導入・活用の効果を感じたと回答しています。
▽デジタル技術導入・活用の効果
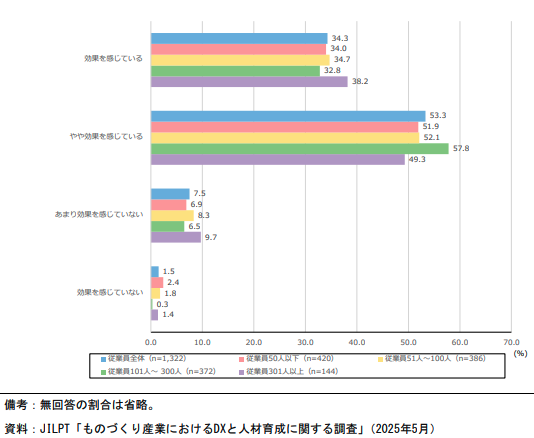
既に生産システムを利用している場合でも、生産プロセスを一元管理できるものに見直したり、より自社に適したものを導入したりすることで、よりQCDの改善に役立つでしょう。
近年では、AIやIoT技術を活用することによって、不良品などのエラーを防止したり、工程を自動化したりすることにもつながります。結果として品質の向上や人件費(コスト)の削減につながるため、QCDも改善するでしょう。
QCDの派生語
QCDは、時代の変化や業界の特性に合わせて、新たな要素を加えて進化しています。ここでは、代表的な派生用語と考え方を紹介します。
QCDS
QCDの派生語として広く使われているのが、QCDSです。この追加された「S」は、文脈によって意味合いが異なり、主に2つの使われ方があります。一つは、安定した生産活動の土台として従業員の安全な労働環境を守る「安全性(Safety)」で、特に製造業や建設業で重要視されます。もう一つは、製品そのものだけでなく顧客対応やアフターサービスまで含めて品質と捉える「サービス(Service)」であり、長期的な顧客満足度を維持するために不可欠な要素とされます。
QCDE
QCDEは、従来のQCDに「環境(Environment)」の視点を加えた考え方です。近年、SDGsやESG投資といった世界的な潮流を受け、企業が環境に与える影響を管理することは、社会的責任(CSR)を果たす上で不可欠な要素となりました。具体的な取り組みとしては、生産工程における省エネルギー化、廃棄物削減やリサイクルの推進、有害化学物質の管理などが挙げられます。これらの活動は、環境規制を遵守するだけでなく、企業のブランドイメージ向上や資源コストの削減にも繋がり、結果としてQCD全体の最適化にも貢献します。
QCDF
QCDFは、QCDに「柔軟性(Flexibility)」という指標を加えたフレームワークです。顧客ニーズの多様化や製品ライフサイクルの短期化が進む現代市場では、需要の変動や急な仕様変更へいかに迅速に対応できるかが企業の競争力を大きく左右します。この柔軟性には、生産量の増減に素早く対応する「量的柔軟性」や、異なる製品を効率的に作り分ける「品種柔軟性」など、様々な側面が含まれます。高い柔軟性を確保することで、販売機会の損失を防 ぎ、顧客満足度の向上に直接繋げることができます。
その他の発展形
上記以外にも、複数の要素を組み合わせた以下のような考え方もあります。
QCDR | QCD+R:Risk(リスク) |
QCDD | QCD+D:Development(開発・発展) |
QCDSE | QCD+S:Safety(安全性) E:Environment(環境) |
QCDSM | QCD+S:Safety(安全性) M:Morale(やる気) |
QCDRS | QCD+R:Risk(リスク) S:Sales(セールス) |
QCDDM | QCD+D:Delivery(納期) D:Development(開発) M:Management(管理) |
PQCDS | QCD+P:Products(品種/生産性) S:Safety(安全性) |
PQCDSME | QCD+P:Productivity(品種/生産性) S:Safety(安全性) M:Morale(やる気) E:Environment(環境) |
QCDSE
QCDSEは、従来のQCDの概念に「S:Safety(安全性)」と「E:Environment(環境)」を追加した用語です。QCDSEにおいては、労災防止の対策を通じた職場の安全確保、周辺環境や近隣住民への配慮などが求められます。特に、現場で事故が起こるリスクがあり、騒音や振動などによって周辺環境に悪影響を与える可能性がある建設業で重視される考え方です。
QCDSM
QCDSMは、従来のQCDの概念に「S:Safety(安全性)」と「M:Morale(やる気)」を追加した用語です。QCDSMにおいては、従業員のモチベーション向上を促すことでQCDにもプラスの影響を与えることを目的としています。やる気は従業員個々の感じ方に依存する部分があるため、的を絞った対策は難しい部分ですが、職場の生産性や離職率にも影響する重要な要素といえるでしょう。
QCDRS
QCDRSは、従来のQCDの概念に「R:Risk(リスク)」と「S:Sales(セールス)」を追加した用語です。QCDRSは、従業員の成果評価、プロジェクト管理において重要視される5つの要素を含んでいます。QCDRSの中でも特に「R:Risk(リスク)」については、ビジネスのあらゆる現場で発生することから新人教育の中でQCDRSの考え方を取り上げる企業もあります。
QCDDM
QCDDMは、従来のQCDの概念に「D:Development(開発)」と「M:Management(管理)」を追加した用語です。QCDDMは、調達を行う際のサプライヤー評価の基準として用いられています。「D:Development(開発)」はサプライヤーが持つ技術力や先進性、「M:Management(管理)」はサプライヤーの財務的な安定性、リスク管理体制などから判断することが一般的です。
PQCDS
PQCDSは、従来のQCDの概念に「P:Products(品種)」と「S:Safet(安全性)」を追加した用語です。PQCDSは、過去の大量生産と大量消費を前提とした価値観を改め、市場に必要とされるものに絞って生産するマーケットインの考え方へ意識改革を図る際に提唱される考え方でもあります。
「P:Products(品種)」が最前に置かれているのは、顧客が必要とする品種を生産することがQCDよりの前提条件であることを意味します、また、Pは「Productivity(生産性)」と解釈されることもあるでしょう。
PQCDSME
PQCDSMEは、先述のPQCDSの概念に「M:Morale(やる気)」と「E:Environment(環境)」を追加した用語です。PQCDSMEにおいては、従来のPQCDSに加えて、働きやすい職場や従業員がやる気を持てる環境を実現する必要があります。PQCDSMEは求められる要素が多岐に渡ることから、実現に向けた客観的な評価指標を準備し、定期的に施策の効果測定を行うことが重要です。
【FAQ】QCDに関するよくある質問
Q.QCDの優先順位はどう決めるべきですか?
A.QCDの優先順位は、企業の経営戦略、製品・サービスの特性、市場環境、顧客ニーズによって決定すべきです。
例えば、高級ブランド品では「品質(Q)」が最優先されますが、消耗品では「コスト(C)」や「納期(D)」が重要になることもあります。競合他社の動向も考慮し、自社の強みと顧客が何を最も求めているかを明確にすることで、最適な優先順位を決定し、経営資源を集中させることが重要です。
Q.QCDとQCDSの違いは何ですか?
A.QCDは「Quality(品質)」「Cost(コスト)」「Delivery(納期)」の3つの主要な経営指標を指します。一方、QCDSはこれに「Safety(安全性)」または「Service(サービス)」を加えたものです。
特に製造業や医療、交通といった人命に関わる分野では、製品やサービスの安全性を確保することが最優先されるため、QCDSとして安全性に着目します。また、顧客対応やアフターサービスが重視される業界では、サービスを含めてQCDSと呼ぶことがあります。
Q.QCD改善の効果測定方法は?
A.QCD改善の効果測定には、具体的なKPI(重要業績評価指標)を設定し、改善前後の数値を比較します。品質(Q)では不良率や顧客クレーム件数、コスト(C)では製造原価や生産性、納期(D)では納期遵守率やリードタイムなどがKPIとなります。
これらのデータを定期的に収集・分析し、目標値との差異や経時的な変化を追うことで、改善活動の成果を客観的に評価できます。
Q.中小企業でのQCD導入方法は?
A.中小企業でのQCD導入は、まず現状把握から始めます。品質、コスト、納期の課題を特定し、小さな範囲から改善活動をスタートさせることが重要です。
例えば、特定製品の不良率低減、特定の工程でのムダ排除、納期遅延の根本原因分析など、実現可能な目標を設定します。従業員全員が当事者意識を持ち、PDCAサイクル(計画・実行・評価・改善)を継続的に回すことで、徐々に全体的なQCDレベルを向上させることが可能です。外部の専門家や補助金制度の活用も有効です。
自社に適した方法でのQCD改善を
QCDは多くの製造業にとって重要課題であり、QCDの水準を高めることにより企業としての利益が増えるなどのメリットが多くあります。一般的には、生産する商品の品質が最優先であり、次に納期が優先されるケースが多いです。
また、企業によってはQCDSなど前出のようなQCDの派生語を使うこともあります。QCDを改善するためには、まず現状を把握して課題を見つける必要があります。改善策を考えて実行し、また改善するというサイクルを繰り返しましょう。一方で5Sを徹底することにより、生産現場の環境を改善できます。
さらに、ITシステムを有効活用することにより、生産プロセスを可視化でき改善しやすくなるでしょう。自社に適した方法でQCDを改善してみてください。
【注目コンテンツ】
・100年企業のグローリーがMES導入を3年間で全社展開を成功させた秘訣とは
・エンジニアの精鋭部隊が集結した合弁会社「DTダイナミクス」設立で生産性が3倍に。内製化支援と技術移転、成功の秘訣とは
・日本の高スキル人材の活躍の場は世界にある アクセンチュアが「ものづくりを変革する」で描く製造業の未来とは