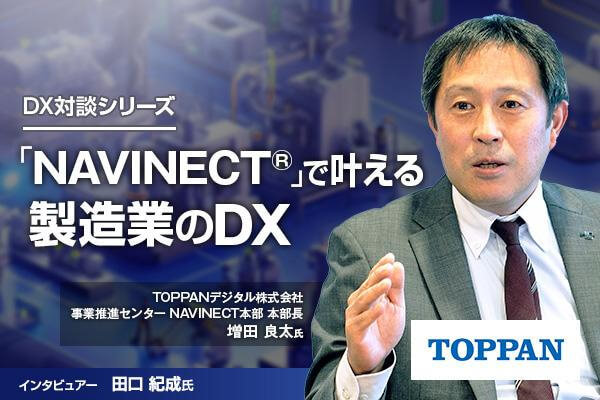
製造業のDXに対する取り組みについて、コアコンセプト・テクノロジー(CCT)CTOでKoto Online編集長の田口紀成氏が対談する本企画。第21回のお相手は、東京都文京区に本社を構えるTOPPANデジタル株式会社の増田良太氏です。
TOPPANグループは、昨年10月に持株会社体制に移行し、凸版印刷から「TOPPANホールディングス株式会社」へと社名を変更しました。 現在はTOPPANホールディングス株式会社を中心とし、凸版印刷の主要部門を母体として継承したTOPPAN株式会社、情報系事業を手掛けるTOPPANエッジ株式会社、グループ全体のDX事業戦略を推進するTOPPANデジタル株式会社など、各分野に特化し事業を行っています。
TOPPANグループではDXとSXを中期経営計画のコンセプトに掲げており、そうした中で生まれたのが製造業のDXを支援するソリューション「NAVINECT®(ナビネクト)」です。2019年に販売を始めてから多くの企業で採用されており、製造現場の業務効率化に貢献しています。今回は、同サービス責任者の増田氏に、開発の経緯やサービスの特徴などについてお聞きしました。
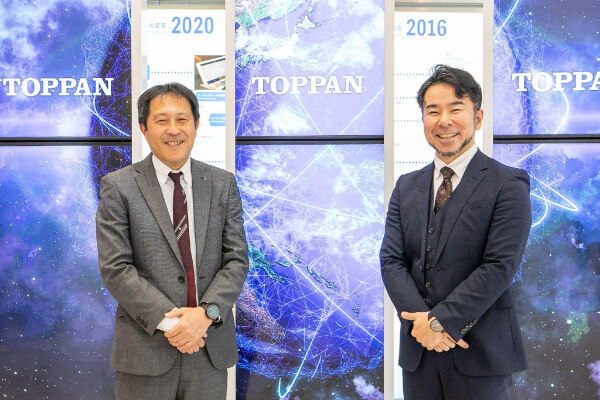
1997年凸版印刷入社。精密部品や液晶パネルなどの高付加価値・小ロット多品種のエレクトロニクス製品を製造する工場や高速大ロットのフィルム加工工場など、国内外の10拠点以上の多種多様な工場の設備導入・立ち上げに携わる。2011年より、これまでに開発・導入した製造システムの全社展開を担当し、凸版印刷28工場(グループ企業含む)の製造DXシステム導入~運用に携わり、各工場での導入効果~変革までを実現。19年からは凸版印刷の各工場に導入したシステムをベースとした製造DXソリューションを「NAVINECT®」という名称でクラウドベースに再整備・追加開発し、販売を開始。本部長として「NAVINECT®」の開発・拡販の指揮にあたる。
2002年、明治大学大学院理工学研究科修了後、株式会社インクス入社。自動車部品製造、金属加工業向けの3D CAD/CAMシステム、自律型エージェントシステムの開発などに従事。2009年にコアコンセプト・テクノロジーの設立メンバーとして参画し、3D CAD/CAM/CAEシステム開発、IoT/AIプラットフォーム「Orizuru(オリヅル)」の企画・開発などDXに関する幅広い開発業務を牽引。2014年より理化学研究所客員研究員を兼務し、有機ELデバイスの製造システムの開発及び金属加工のIoTを研究。2015年に取締役CTOに就任後はモノづくり系ITエンジニアとして先端システムの企画・開発に従事しながら、データでマーケティング&営業活動する組織・環境構築を推進。
DXを通じた社会課題の解決が目的
田口氏(以下、敬称略) 最初に御社の概要をお聞かせください。
増田氏(以下、敬称略) 当社はTOPPANグループの事業会社の1つで、グループ全体のDX事業戦略策定、DX事業の創出・推進、DXに関わる研究・開発、ITインフラの提供といった役割を担っています。DXの推進を通じて社会課題の解決を目指すのが目的であり、現場課題に合わせたデジタル化の支援、コンサルティングなどを通じて、お客様のDXを加速させるソリューションを提供しています。
田口 御社は、グループ全体でDXを推進しているそうですね。全社をあげて社会や企業のデジタル化を支援するとともに、デジタル変革を推進するコンセプト「Erhoeht-X® (エルヘートクロス)」を掲げています。
増田 エルヘートとは、TOPPANグループ創業の原点である当時の最先端印刷技術「エルヘート凸版法」のことであり、この印刷技術のマインドと先進のデジタルを融合させるという想いを込めました。このコンセプトをもとに、セキュアビジネス、ハイブリッドBPO、マーケティングDX、デジタルコンテンツ、製造・流通DXの5つの重点カテゴリーに対してサービス・ソリューションを提供しています。
田口 今日の対談のテーマである「NAVINECT®」は、製造・流通DXのカテゴリーに対するソリューションですね。
増田 おっしゃる通りです。どのような社会課題を解決するのかというと、労働人口の減少への対策は大きく挙げられます。同時に脱炭素をはじめとするSXへの対応、デジタルを活用した製造履歴による安全への保証なども求められるようになりました。すべきことは増えていくのに人は減るなか、対策は急務であり、こうした課題の解決をテーマに掲げています。
田口 TOPPANグループおよび御社が取り組む背景についてもお聞かせください。
増田 我々はもともと製造業であり、アナログと融合した形でデジタル化を進め業務の効率化を図ってきました。ここで得たノウハウを大企業だけではなく、資金や技術面で導入に苦心している中小企業にも提供したい考えがあります。
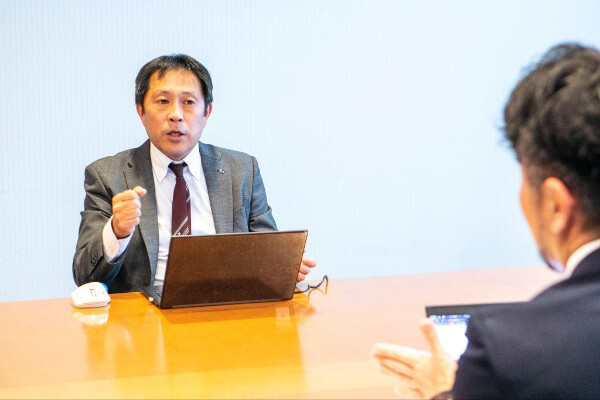
田口 幅広く事業を展開する中、製造DXにはどのくらいの人数を割いているのですか。
増田 現在、約100名程度で、そのうちの半数以上が工場出身の技術者です。技術者出身の彼らが今はITの専門家になっており、私自身も設備技術員としての歴のほうが圧倒的に長いです。このように、社内人材のリスキリングを強化し、IT専門の人材を集め育成に努めています。デジタルとものづくりを完全に理解した人材なくしては、現場目線の製造DXのサービスは作れないからです。
田口 現場経験やITスキル習得などのリスキリングを進めながら人材育成の強化を図りつつ、外部のパートナーとも協力しながら規模を大きくし運営しているという理解でよろしいですか。
増田 そうですね。
デジタルを活用した生産性向上のため自社工場でDXを推進
田口 増田さんは技術出身とおっしゃっていましたが、これまでの経歴をお聞きしたいです。
増田 私は1997年に凸版印刷へ入社し、当初は液晶ディスプレイや半導体部材の工場で技術者としてキャリアをスタートさせています。液晶ディスプレイのカラーフィルターへの関わりが深く、製造設備の設計から導入、プロセスの構築までを担当していました。なかでも私は検査機・測定器が専門の画像処理技術員として腕を磨き、当時は画像処理の特許なども出しています。こうしたなか、ディスプレイサイズの大型化に伴い品質管理システムを作り始め、DX系のシステム開発にも携わるようになりました。
田口 DXにはかなりはやくから着手したということですか。
増田 2010年くらいに始まっていますが、その前の10年間でも近しいシステムは作っていました。ただしフルオーダーなので外に出せるような仕組みではなく、完全にエレクトロニクス専門なので超高額なものです。半導体産業は巨額の設備投資を行い工場を新設するので、システムに対する投資も規模が大きく違っていました。
田口 お話しいただいたバックグラウンドを経て、「NAVINECT®」へどうつながっていったのでしょうか。
増田 TOPPANグループはエレクトロニクス以外に従来の印刷、情報コミュニケーション、さらには包装材をはじめとする生活・産業事業を大きく手掛けてきましたが、2010年前後にはデジタル印刷機が登場し、電子出版も本格的に普及し始めました。包装材の設備も性能がよくなり、コモディティ化が加速していき、こうした脅威を背景にデジタルを活用した生産性の向上は喫緊の課題で、当社も群馬工場を皮切りに現場のDXに取り組み始めたのです。
ERPは最初からデジタルでしたが、MES層やSCADA層はアナログを残しており手作業が多く、圧倒的な省人状態でモノを作りたいというのが、当初の発想でした。群馬工場は早い段階からエネルギーのリサイクルを始めており、先端設備とITを使ったDX拠点として白羽の矢が立ったわけです。装置からデータを取りペーパーレス化するといった取り組みから始め、次第に制御やAIを活用した分析などに広がっていき、10年が経過するころには凸版印刷の自社工場28ヵ所でDXの導入から運用まで実現していました。
そして、2019年から各工場で導入したシステムをベースとした製造DXソリューションを「NAVINECT®」の名称でクラウドベースに再整備・追加開発し、販売を始めたのです。
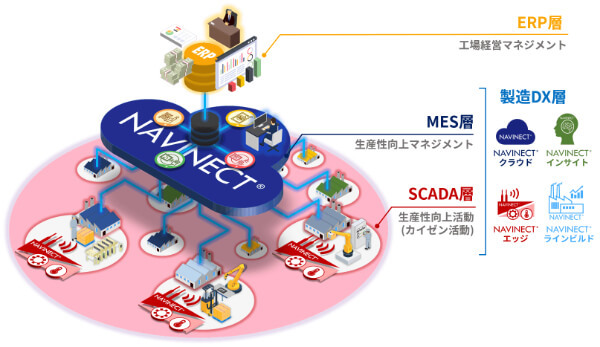
ⓒTOPPAN Digital Inc .
田口 当初はDXというキーワードもなく、現場では反発もあったのではないでしょうか。
増田 印刷工場も包材工場も実績を入力するという意味でのMESは入っていましたが、IoT化するにあたりすべて刷新しました。端末もタブレットやタッチモニターを使いますが、製造現場のベテランたちからは字が小さい、読みづらいという声はありました。しかし、我々DXの担当者たちは製造現場の機械の隣でプログラミングを作るような姿勢で、厳しい言葉をかけられるなか、さすがに可哀そうだと思い味方になってくれる人も増えるようになり、徐々に浸透していきました。
IoTが想定されていない設備からデータを取ったりセンシングすることにはあまり苦労しませんでしたが、どれだけ現場が楽になるのか、活用したいと思ってもらえるかという点を追及することには苦心しました。ただ、気づいてもらうと一気に普及するので、意識改革のほうが重要だと思います。
田口 そのために工夫していることはありますか。
増田 導入時に大切にしているのは、コミュニケーションをしっかり取ること、システムのイレギュラーに対して事前にどこまで考えているかということです。使える状態にして持っていくことも重要視しており、インプットのシステムを作る時はアウトプットもしっかり作り込んでから持っていきます。
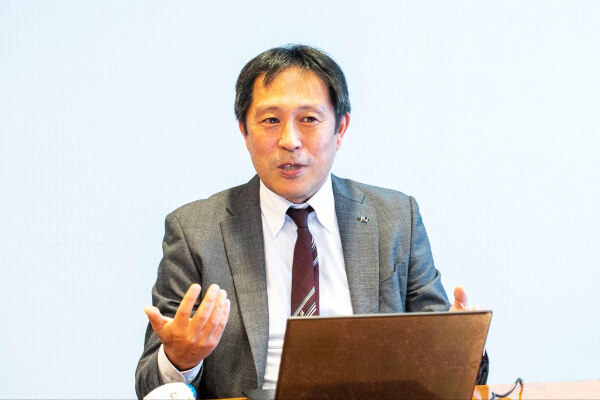
MESとSCADA領域に導入する製造業DX支援サービス
田口 「NAVINECT®」を外販するに至った経緯についてお聞かせください。
増田 これまではモノを扱ってきましたが、製造DX以外にもマーケティングなどデジタル分野も手掛けており、DXでも社会貢献ができると考えたことが大きいでしょう。製造DXに関してはエレクトロニクスから始まると20年の歴史があり、商材や事業に合わせ自分たちで作ったアプリケーションだけで100種類を超えています。
販売するにあたりカテゴライズと共通化から始め作業は大変でしたが、いろいろな生産方式に対してオーダーメイドで作った後に統合化したので、たくさんの製造業の業務に適用できるアプリケーションを作っていたことが、外販に踏み切る決断につながりました。
田口 どういった業界で多く採用されているのですか。
増田 自動車系の製造現場です。エレクトロニクス系は相性が良いことから、従来からシステムを入れている企業が多く、自動車業界が目立ちます。自動車系の製造現場です。エレクトロニクス系は相性が良いことから、従来からシステムを入れている企業も多く、特に自動車業界が目立ちます。
田口 販売するにあたり、どのような点に注力しましたか。
増田 業務に特化した小さいアプリケーションをたくさん作り、サブスクリプションとして提供することで、大手企業だけではなく、中小企業まで導入できることを目的にしました。お客様が取捨選択できれば、スモールスタートを切ることができます。また、当持のシステムはWindowsで動くことが前提だったので、クラウド志向へ一気に切り替えました。最後は連携です。当社は装置メーカーと組んでラインも販売するなどの連携が得意で、RFIDなどICタグ系のデバイスも扱っているので、この点も強く意識しました。
田口 「NAVINECT®」の概要について、さらに詳しくお聞かせください。
増田 製品自体は製造業のDXツールで、100あったアプリケーションを8種類までパッケージ化した形で提供しています。製造業のシステムはERPと製造を実行するMESと監視・制御を行うSCADAにわかれますが、「NAVINECT®」はMESとSCADA領域に導入するものです。具体的には、次の4つの製品を提供しています。
NAVINECTクラウド:“現場記録作業のペーパーレス化”“在庫管理のデジタル化”“工場内ワークフローのデジタル化”などを4つのクラウドサービスとして提供。
NAVINECTエッジ:装置情報の取込・集計・処理・監視・可視化、装置の制御、作業指示などをデジタル化する5つのパッケージを提供。
NAVINECTインサイト:製造現場のさまざまな情報をBIツールを活用して収集し、専門スタッフやAIによって分析を行う製品。他拠点との情報共有を実現し、拠点ごとの情報を比較して確認することも可能。
NAVINECTラインビルド:製造現場の設計や設備導入・再構築・運用サポートをコンサルティング。アプリケーション開発や生産装置の提案まで製造現場のDXをトータル的にサポート。生産方式に合わせたソリューションも提供。
ポイントは3つあり、1つは自社工場で20年の実績を持つパッケージを入れているという点です。これをオンプレミスでもSaaSでも提供することができます。2つ目はシステムアーキテクチャの話で、クラウドに切り替えたことは大きいです。現在、スマートファクトリーを構想している数多くのお客様から引き合いを頂いております。そのようなお客様は10年程度は刷新せず利用することを想定されますので、リモート製造のことも考えると、こういったアーキテクチャが強みになっています。
3つ目は、ラインビルドエンジニアがいるということです。彼らはシステム構築だけではなく自社の工場の立ち上げを通じてさまざまな製造現場を経験しており、変えづらい昔ながらの習慣や設備の配置問題など、多くの課題を改善に導いてきました。経験が豊富で、現場目線でお客様の悩みを解決できることは、最大の強みかもしれません。
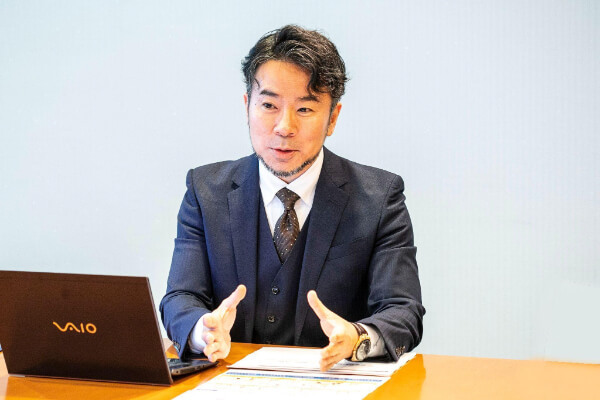
事業規模を問わず100社以上で導入実績
田口 これまでの導入実績はいかがでしょうか。
増田 大企業から中小企業まで幅広く100社以上、自動車業界が最も多く、その他に半導体、樹脂など幅広い業界で導入いただいています。事例としてはMESが多いのですが、在庫システムや環境システムなども見られます。スモールスタートのペーパーレスというより、利用用途を決めコーディネートとして入れるケースが多くを占めています。
反響としてはライン監視・制御を自動化することで省人化できたという製造IoTに関する声であったり、アラートが出たときに原因がすぐにわかった、クレームの発生要因が特定しやすくなったという声をいただいています。アプリケーションに関しては、最初はとっつきにくかったが使い続けていくと運用にマッチしているとわかったという声もよく耳にしています。
製造DXを始めるお客様は、最初の一歩として、ペーパーレスを検討する場合が多いです。しかし実際に導入すると、IoT連携を行わなければ狙った投資対効果、あるいは、生産性向上は狙えないことに気づきます。そういった点に対しスムーズに対応できる点も評価されています。導入面ではラインビルドエンジニアが製造現場とのパイプラインに入るので助かるとよく言われます。
田口 製造現場まで入ってくるコンサルタントやSIerは少なく、そう考えると御社のエンジニアは距離が近く、長いお付き合いをするうえでもメリットがあると思います。
増田 製造現場への説明会から始めることも珍しくありません。
田口 今後の課題はありますか。
増田 DXに対する投資は二極化しており、「NAVINECT®」の受注金額も大きく分かれます。高額投資のお客様はスマートファクトリーが狙いで、少額投資のお客様はスモールスタートから始めたいわけですが、一方で中間層の投資は少ないのが現状です。製造設備においては、1,000万円の設備投資に対して1,100万円儲かるなど想定通りのリターンを期待できますが、DXは投資額が低いと費用対効果が出づらく、一定の領域を超えるといきなり利益に直結します。この理屈を誤解している方も多く、どのように理解を促していくかは課題の1つでしょう。
また、DX(デジタルトランスフォーメーション)の手前には、第一段階のデジタイゼーションと第二段階のデジタライゼーションがあります。スモールスタートで効果を上げる場合は、デジタライゼーションまで進めることがとても重要になります。例えばペーパーレスであれば、入力をデジタル化するデジタイゼーションよりも、そのデータを活用し、意識決定の仕組みやワークフローに構築するデジタライゼーションが重要です。
ところが、スモールスタートの場合、そこまで具体的に考えず『将来のデータ分析』に活用するとしてデータを眠らせているケースがあります、分析ではなく日々の業務への活用を考えれば効果が得られるのに、データをそのままにしているのです。結果、解約につながることになり、これも課題として感じています。
田口 DXについて課題を抱える製造業に対して、「NAVINECT®」をどう使ってほしいと考えていますか。
増田 「NAVINECT®」には「ナビゲーションコネクト」という意思を込めており、つなげることを前提にした仕組みとなっています。ですから、装置や資材、人、システムなどをつなげてお使いいただきたいと思います。
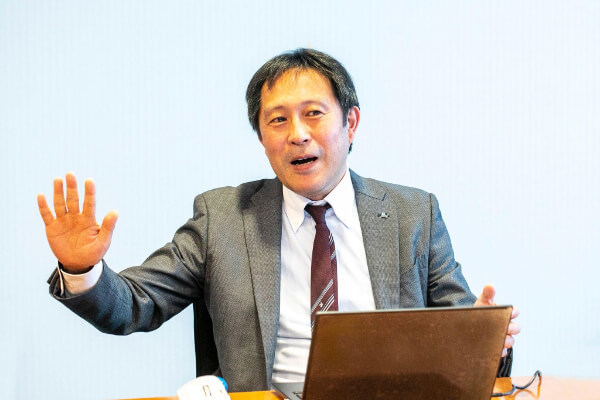
田口 今後の展望についてはいかがですか。
増田 2025年にかけて、クラウド型のスマートファクトリー対応パッケージを形にしたいと考えています。国内製造業は海外に比べてものづくりに対するこだわりがあり、オーダーメイド志向が強いのが特徴です。「NAVINECT®」でもスマートファクトリーシステムのようなシステムを入れることはよくありますが、オーダーメイドだとカスタム比率が高く導入コストは高額になり、それは違うのではないかと感じています。
労働人口が減るなか、大企業はともかく中小企業はITエンジニアの確保が難しく、オーダーメイドのシステムを運営し続けることができなくなる可能性が高いでしょう。ベンダー側も、1つの会社のためにバージョンアップし続けるのは厳しいに違いありません。また、ERPがほぼクラウドであるのに対して、製造系システムがいつまでもオンプレミスでいられるかも問題です。当社としてもクラウドでスマートファクトリーへの対応を進めたいと考えています。
田口 最後にKoto Onlineの読者にメッセージをお願いします。
増田 国内製造業は労働人口減少に伴う人手不足、属人化からの脱却に対応しないといけません。SXとして脱炭素をはじめとする環境問題、安全に対する保証も課題であり、これらを実現するのにDXによる変革は絶対に必要です。成功のカギは経営層やITエンジニアの存在もありますが、我々は現場でものづくりに関わる方々が握っていると考えています。「NAVINECT®」は現場にこだわり、ものづくりに関わるすべての人と力を合わせ工場の課題を解決することで生産性向上を叶えるのが目的です。ご興味を持っていただけると幸いです。
田口 今日のお話で、TOPPANグループのDXを通じた社会課題の解決、さらには具体的な施策を理解することができました。ありがとうございました。
【関連リンク】
TOPPANデジタル株式会社 https://www.digital.toppan.com/ja/
「NAVINECT®」 Webサイト https://navinect.jp/
株式会社コアコンセプト・テクノロジー https://www.cct-inc.co.jp/
【注目コンテンツ】
・DX・ESGの具体的な取り組みを紹介!専門家インタビュー
・DX人材は社内にあり!リコーに学ぶ技術者リスキリングの重要性
・サービタイゼーションによる付加価値の創造と競争力の強化