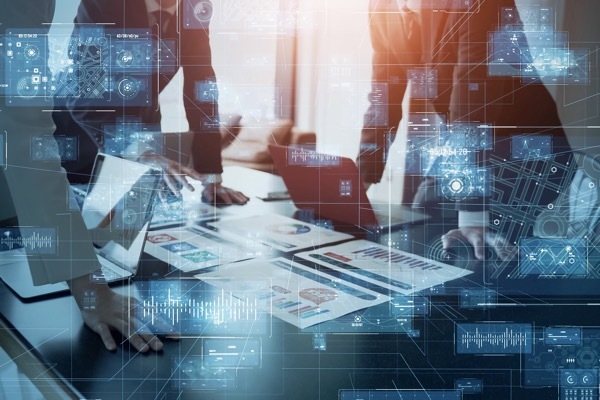
製品の品質を維持しながらも、無駄なコストを抑え、競争力を高めたい――。多くの製造業や建設業で共通するこの課題に対する有効な方法の一つがバリューエンジニアリング(Value Engineering:VE)です。
VEは、単なる「コスト削減」ではなく、「機能」と「コスト」のバランスを科学的に見直し、真に価値あるものづくりを実現するための体系的アプローチです。
この記事では、VEの基本的な考え方から、実際の導入プロセス、業界別の活用事例、成功のコツに至るまでをわかりやすく解説します。
目次
バリューエンジニアリング(VE)とは?価値向上とコスト削減を両立する手法
バリューエンジニアリング(VE)とは、製品やサービスが本来果たすべき「機能」を定義し、それを達成するために必要なコストを最小化することで、全体としての「価値(Value)」を最大化する手法です。1947年に米国ゼネラル・エレクトリック(GE)のローレンス・マイルズによって提唱されたこのアプローチは、今や製造業や建設業、さらにはサービス業や行政の現場にも広く応用されています。
VEでは、「価値=機能÷コスト(Value = Function ÷ Cost)」という考え方を基本とします。ここでいう機能とは、製品が備えるべき役割や性能を指し、単に安くすることだけを目的とするのではなく、必要十分な機能を保ちつつ、過剰品質や無駄な仕様を見直していくことに重点が置かれます。
日本でも1960年代には導入が始まり、その考え方や手法が体系的に広められてきました。VEは単なる「コスト削減施策」ではなく、製品設計やプロセス改善の場において全社的な価値向上を実現する戦略的アプローチとして位置づけられています。
バリューエンジニアリング(VE)の基本的な考え方
VEの中心にあるのは、「機能」を明確に定義し、その機能を果たすための最も合理的な手段を検討するというプロセスです。この際、以下のような視点での問いかけが重要になります。
- その機能は本当に必要か?
- 他の手段で同じ機能を果たせないか?
- より安価、簡便、迅速に実現する方法はないか?
こうした問いを通じて、製品やサービスの構成要素を細かく分析し、価値に直結しない要素を削ぎ落とすことができます。
バリューエンジニアリング(VE)における「4つの価値改善パターン」
VEは「コストを下げる」だけではありません。むしろ重要なのは、機能とコストのバランスを見直すことで、製品やサービスの「価値」を最大化することです。
そのため、VEでは次のような4つの改善パターンが存在します。
パターン | 機能 | コスト | 備考 |
---|---|---|---|
1 | 向上 | 維持 | - |
2 | 維持 | 引き下げ | - |
3 | 向上 | 引き下げ | 最も理想的な改善 |
4 | 大幅向上 | 微増 | 高付加価値型 |
これらはすべて「価値の向上」という目的を共有しており、「どの方向の改善が最も合理的か」は、製品やプロジェクトの目的・顧客ニーズ・市場環境などによって判断されます。
たとえば、BtoB向けの産業機器であれば、少しコストが上がっても機能性や信頼性を重視するパターン4が有効な場合もあります。一方で、消耗品のようにコスト競争力が重要な商材では、パターン2を徹底的に追求するという方針も合理的です。
このように、VEは単なるコストダウンのための手法ではなく、価値を中心に据えて意思決定を行う設計・経営思考であることがわかります。
バリューアナリシス(VA)との違い
VEと似た言葉に「バリューアナリシス(VA)」がありますが、両者には導入タイミングに違いがあります。一般的には以下のように区別されます。
項目 | バリューエンジニアリング(VE) | バリューアナリシス(VA) |
---|---|---|
タイミング | 開発・設計段階(これから作るもの) | 量産・運用段階(すでに在るもの) |
目的 | 価値の作り込み(予防的アプローチ) | 価値の改善(是正的アプローチ) |
つまり、VEは設計段階での予防的な価値最適化、VAは既存の仕様を改善するための見直しという位置づけになります。日本ではこの2つをあわせて「VE活動」と総称する場合も多く、実務上は明確に分けずに活用されるケースも少なくありません。
バリューエンジニアリング(VE)の本質は「価値の最適化」
VEの特徴は、コストだけに着目せず、「必要な機能を最小限のコストで実現する」点にあります。ここで重要なのが「価値は上げながら、コストは下げる」という発想です。
過剰な品質や複雑な構造は、ユーザーにとって本質的価値をもたらさないこともあります。VEでは、こうした無駄な要素を排除し、本当に顧客にとって価値ある機能にリソースを集中させる考え方が求められます。
バリューエンジニアリング(VE)の5つの基本原則
VE活動をより効果的に進めるためには、プロセスだけでなく、その根底にある「考え方の原則」を理解しておくことが不可欠です。日本VE協会では、VEの成功を支える考え方として以下の「5つの基本原則」を提示しています。
・使用者優先の原則
製品やサービスの価値は、使う人にとって意味があるかどうかで決まります。顧客視点に立ち、必要とされる機能は何かを見極めることが出発点です。
・機能本位の原則
表面的な仕様や形状に惑わされず、「本来果たすべき機能とは何か」を軸に考えることがVEの基本です。
・創造による変更の原則
過去のやり方や慣習にとらわれず、柔軟で創造的な発想によって改善案を生み出すことが重要です。
・チームデザインの原則
一人の知識や経験だけでは見落としも生じます。多様な専門性をもつメンバーで構成されたチームでこそ、より実行性の高い改善策が生まれます。
・価値向上の原則
コストを下げるだけでなく、製品やサービスの「価値」を高めることこそがVEの本質です。コスト削減はあくまで手段であり、目的ではありません。
これらの原則を意識することで、VEは単なるコスト削減活動ではなく、顧客にとっての価値を見直す創造的な改善活動として、組織に深く根づいていきます。
バリューエンジニアリング(VE)の活用場面
バリューエンジニアリング(VE)は、製品やサービスの設計段階だけでなく、調達、生産、保守といったあらゆる工程において有効です。VEの最大の特徴は「機能とコストの見直し」という視点を、特定部門だけでなく全体最適の観点から導入できる柔軟性にあります。そのため、製造業・建設業・行政などさまざまな現場で活用されており、課題の本質をあぶり出す手法としても重宝されています。
ここでは代表的な活用場面を、業種・工程ごとに整理してご紹介します。
製品設計・開発におけるバリューエンジニアリング(VE)
最もVEが力を発揮するのは、製品企画・設計段階での活用です。この段階では、まだ仕様が確定しておらず、材料や構造、機能の見直しが容易なため、VEの成果を大きく引き出しやすくなります。
たとえば次のような局面でVEが導入されます。
- 製品原価の大半が決まるともいわれる設計段階で、コスト構造を最適化する
- 顧客要求を分析し、仕様の「過剰品質」や「不足機能」を見直す
- 部品点数の削減や共通化によって、組立工数や管理コストを低減する
VEの考え方を企画初期から導入することで、製品の「過剰品質」や「不要機能」によるコスト増を抑制し、後工程での無理な原価低減施策に頼る必要がなくなります。
生産工程や調達部門におけるバリューエンジニアリング(VE)
VEは製品開発に限らず、既存製品の生産工程や部材調達の見直しにも効果を発揮します。この場合はVA(バリューアナリシス)的なアプローチと組み合わせて用いられることも一般的です。
具体的な活用例として、
- 高コスト部品を代替材や別構造で見直す
- 組立工程における手順の簡素化・モジュール化を行う
- 外注品や購入部品の仕様交渉にVE的視点を活用する
などが挙げられます。調達コストや製造リードタイムといった現場課題を、単なる数字ではなく「機能」の視点で捉え直すことが、具体的な改善策を見つける鍵となります。
建設業や公共事業におけるVE提案(VE提案型入札)
建設業界においてもVEは広く導入されており、特に公共工事では「VE提案型入札方式」などが制度化されています。これは、発注者が提示した設計条件に対し、受注側がVEを活用してコスト削減・性能向上などの改善提案を行う方式です。
たとえば、
- 橋梁や道路工事で、設計条件に沿った上での構造簡略化案を提示
- 使用材料や施工方法の変更による工期短縮・コスト低減
- 維持管理コストまで含めたLCC(ライフサイクルコスト)視点での提案
などが評価対象になります。国土交通省や自治体による導入事例も多く、VE提案が採択されれば落札評価点に反映されるため、建設業界における競争力強化の武器にもなります。
このように、VEは製品開発にとどまらず、調達・生産・施工まで幅広く応用できる「価値思考のフレームワーク」です。導入のタイミングや目的に応じて柔軟に活用することで、コストと品質、納期のバランスを最適化する全社的改善策としての効果が期待できます。
参考:民間の技術力を活用する新たな入札・契約方式について(国土交通省)
バリューエンジニアリング(VE)の実施プロセス
バリューエンジニアリング(VE)を現場で実践するには、段階的かつ論理的なプロセスに沿って進めることが重要です。VEは思いつきのコストカットとは異なり、再現性のあるフレームワークとして確立されており、チームによる協働や多角的な分析を通じて、本質的な価値向上を目指します。
VE活動の実践プロセスには、大きく2つの視点があります。ひとつは、VEの国際的な標準モデルである「ジョブプラン(Job Plan)」、もうひとつは、より実務に即した形で構造化された「3つの基本ステップと10の詳細ステップ」です。ここでは両者をあわせて紹介します。
バリューエンジニアリング(VE)活動の6ステップ(ジョブプラン)
ジョブプランは、VE活動の基本枠組みであり、以下の6段階で構成されます。日本VE協会をはじめ、国内外の多くの企業や団体で採用されている標準的な進行フローです。
- 情報段階(Information)
対象の製品・工程について基本情報を収集し、VEの目的や制約条件を明確にします。 - 機能定義段階(Function Analysis)
対象が果たす機能を整理し、機能とコストの関係を分析します(機能系統図やFAST図を使用)。 - アイデア発想段階(Creative)
代替案や改善アイデアをブレインストーミングなどで多面的に出し合います。 - 評価段階(Evaluation)
出されたアイデアを実現性・効果・コストの観点から評価し、絞り込みます。 - 開発段階(Development)
選定案の詳細設計やコスト試算を行い、実施可能な形に落とし込みます。 - 提案段階(Presentation)
改善案をまとめ、社内で提案・承認を得て導入を図ります。
このプロセスを踏むことで、属人的な改善ではなく、組織全体としての価値最適化を目指すVE活動が可能になります。
現場で活用しやすい「3つの基本ステップと10の詳細ステップ」
VEの基本構造はジョブプランに準拠していますが、現場での実践においては、より細かく段階を整理した「3つの基本ステップと10の詳細ステップ」が活用されることもあります。
特に中小企業や行政機関、現場の改善活動において有効で、各ステップに設定されている“問いかけ”を活用することで、VE初心者やチームメンバー間の思考整理や合意形成を支援するツールとして機能します。
基本ステップ | 詳細ステップ | 主な問いかけ |
---|---|---|
機能定義(分解) | ① 情報収集 | それは何か? |
② 機能定義 | その働きは何か? | |
③ 機能の整理 | 何のために? どのようにして? | |
機能評価(分析) | ④ 機能別コスト分析 | そのコストはいくらか? |
⑤ 機能評価 | その価値は? | |
⑥ 対象の選定 | どの機能を見直すべきか? | |
代替案作成(創造) | ⑦アイデア発想 | 他に同じ働きをするものは? |
⑦ 概略評価 | 技術的に実現可能か? コストは? | |
⑨具体化 | 実施に向けて課題はないか? | |
⑩詳細評価 | 最適な代替案として確立できるか? |
このアプローチは特に中小企業や行政機関、現場の改善活動において有効であり、VEの進行に迷わないためのガイドラインとして実務者から高く評価されています。
バリューエンジニアリング(VE)で用いられる代表的な分析ツール
VEの各ステップでは、分析やアイデア創出を支援するツールを組み合わせて活用します。とくに以下の3つは実務でよく使われる基本ツールです。
FAST図(Function Analysis System Technique)
「なぜ?どうやって?」の論理を用いて機能の階層構造を整理し、目的と手段のつながりを明確にする手法です。複雑な構造を持つ製品やシステムの見える化に役立ちます。
機能系統図(Function Tree)
中核となる機能を起点に、補助的・派生的な機能を整理していく図です。チームでの共通理解の出発点として使用され、何を改善すべきかを構造的に把握することができます。
コスト分析シート(Function-Cost Matrix)
各機能にどれだけのコストがかかっているかを定量的に把握し、価値に見合わないコストがかかっている部分を特定するための表形式ツールです。代替案の選定根拠として活用されます。
このように、VEは明確なプロセスとツール群に支えられた改善活動であり、属人的な判断に頼らず、チームで「価値の再設計」に取り組むための体系的アプローチです。
VE導入に際しては、まずは小規模なテーマから着手し、こうしたプロセスの習熟を通じて、段階的に組織全体へ展開していくのが効果的です。
バリューエンジニアリング(VE)のメリットと導入の注意点
バリューエンジニアリング(VE)は、機能とコストのバランスを見直すことで、製品やサービスの「真の価値」を高める手法です。そのため、VEは単なるコスト削減策にとどまらず、企業全体の競争力や顧客満足度を高める総合的な改善アプローチとして、多くの現場で活用されています。
一方で、VEの導入にあたっては注意すべき点も存在します。VEの本質を正しく理解しないまま実施すると、成果が出なかったり、かえって社内の反発を招いたりすることもあるためです。ここでは、VEの代表的なメリットと、導入時に陥りやすい課題・注意点をあわせて解説します。
バリューエンジニアリング(VE)の主なメリット
VEはコストを「削る」だけの手法ではありません。正しく活用すれば、以下のような多面的なメリットが得られます。
コスト構造を最適化できる
不要な機能や過剰な品質にかかるコストを見直すことで、製品のコスト構造を根本から改善できます。
顧客価値に直結した製品開発ができる
「誰のための、どんな機能か?」を明確にすることで、商品企画や開発段階における判断の軸が定まり、顧客価値に直結した仕様設計が可能になります。
部門間の連携を強化できる
VE活動では部門横断でのチーム編成が基本です。機能とコストを全社的に捉えることで、縦割りの壁を越えた意思疎通が生まれます。
社員の創造性と問題解決力を高められる
VEのプロセスを通じて「本質を捉える力」が養われ、組織の改善意識が向上します。
顧客満足度と競争力を向上できる
必要な機能に絞って製品を磨き上げることで、価格競争力を保ちつつ、品質や使いやすさといった顧客価値を高めることができます。
このように、VEは「モノづくりの体質改善」を促す手法であり、一時的な原価低減策とは異なる“構造改革的な改善”を実現できます。
バリューエンジニアリング(VE)導入時の注意点|よくある誤解と失敗パターン
VEの効果は大きい一方で、導入初期にはいくつかの落とし穴があります。代表的な注意点は以下の通りです。
「VE=安易なコスト削減」と誤解される
VEの目的はあくまで価値の最適化です。コストだけに注目すると、顧客ニーズや品質の本質を見落とし、逆に信頼を損なう可能性もあります。
属人的・思いつき主導で進めてしまう
VEはプロセスとツールに基づく分析活動です。確立された手順を無視して思いつきで仕様を変えたり、誰かの経験に頼ったりするだけでは、再現性のある改善にはなりません。
部門間の対立を招いてしまう
コストや仕様の見直しは、ときに他部門の利益や慣習と衝突します。VEでは部門横断チームを編成し、全社共通の価値向上という目的に向かって丁寧な合意形成を図ることが成功の鍵です。
「やりっぱなし」で終わる
VE提案が採択されたあと、実行・フォローアップがされないままになってしまうと、改善は現場に定着しません。実行計画を立て、PDCAを回してこそ、成果は現場に定着します。
評価軸が定まっていない
機能評価や代替案の選定基準を明確にしておかないと、主観的な判断になりやすくなります。評価基準の明文化と合意形成が重要です。
VEを成功させるには、単にツールやフレームワークを導入するだけでなく、企業文化や組織の在り方と整合させながら進めることが求められます。はじめから完璧を目指す必要はありません。まずは小さなテーマからスタートし、VEの思考やプロセスに慣れることが、成果を積み重ねる近道となります。
バリューエンジニアリングの事例
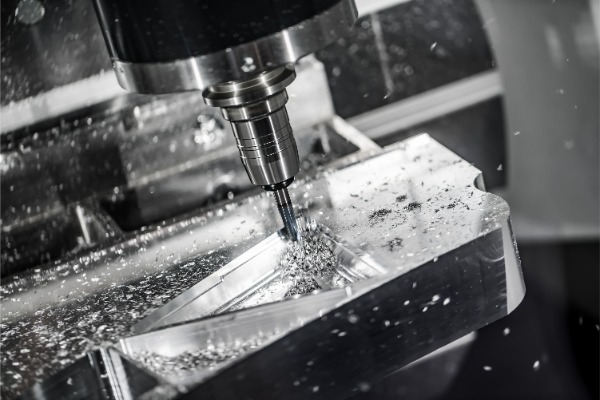
バリューエンジニアリング(VE)の代表的な事例
ここからは、VEの基本原則がどのように活かされ、成功につながったのか、3つの代表的な事例を通して見ていきます。
切削工具の事例
【課題】
高価な特殊材料で作られた金属加工用の切削工具は、摩耗するたびに切れ味が落ちるため、まだ使える部分が残っていても、工具全体を交換する必要がありました。そのため、部品コストが非常に高くなるという課題を抱えていました。
【VEによるアプローチと解決策】
VEではまず、「その工具が果たしている『機能』は何か?」という本質を問い直します。この工具の機能は、①金属を削る機能(刃先)と、②工具を機械に固定する機能(本体)に分解できます。
本当に特殊材料が必要なのは、摩耗する①の刃先の部分だけです。そこで、「バラのとげは先端だけが鋭い」という自然界の仕組みからヒントを得て、刃先の部分(チップ)だけを交換可能にするというアイデアが生まれました。
信号機の事例
【課題】
従来の電球を使った交通信号機は、社会インフラとして不可欠な一方、消費電力が大きく、電球の寿命も短いため、電気代や定期的な交換・メンテナンス費用といったライフサイクルコスト(LCC)の高さが問題視されていました。
【VEによるアプローチと解決策】
この課題に対し、「信号機の機能=安全に交通を制御する光を提供する」を維持・向上させつつ、トータルコストを削減する視点で改善が検討されました。そこで採用されたのが、光源を電球からLEDへ変更するというアプローチです。
この変更は、「機能の向上」と「コストの削減」という二つの側面で大きな成果を上げました。
まず機能面では、LEDの光が持つ高い指向性によって西日などの影響を受けにくくなり、ドライバーや歩行者の視認性が大幅に向上。これにより、交通安全へ大きく貢献しました。
さらにコスト面では、消費電力が約85%削減されて電気代が大幅に減少したほか、電球の6~8倍という長い寿命のおかげで交換頻度が激減し、保守費用も劇的に圧縮することに成功しました。
バックスタンドの屋根
【課題】
大規模なイベント施設で、観客席を覆う屋根の設置が計画されました。しかし、従来工法で柱のある恒久的な屋根を建設するには、莫大な費用と長い工期が必要になるという課題がありました。
【VEによるアプローチと解決策】
この課題に対し、「屋根の本当の機能=観客を雨や日差しから守ること」と再定義し、この本質的な機能をいかに低コストかつ迅速に実現できるか、という一点に集中してアイデアを模索しました。
その結果、「屋根は柱で支えるもの」という固定観念を覆す、「巨大な膜を空気の圧力でドーム状に浮かせる」というアイデアが生まれました。この空気膜構造方式がもたらしたメリットは、単なるコスト削減にとどまりません。
大量の鉄骨が不要になることで建設コストと工期が大幅に圧縮されたのはもちろん、何よりも大きな価値は、内部に柱が一切存在しない壮大な無柱空間を実現したことにあります。
これにより、観客の体験価値は最大化され、イベントの自由度も向上するなど、施設の可能性そのものを大きく広げることに成功しました。
バリューエンジニアリング(VE)の資格
バリューエンジニアリング(VE)は、体系化された手法であると同時に、社内の文化や習慣に根づかせてこそ真価を発揮します。しかし、VEをこれから導入しようとする企業や自治体にとっては、「どこから始めればよいか」「誰に任せるべきか」「どうやって社内に浸透させるか」といった悩みも少なくありません。そのような中で、公益社団法人日本バリュ-・エンジニアリング協会が主催する人材育成制度を活用するのも一つの方法です。
・VEリーダー(VEL)
社内で初めてVEを実践する担当者向けの基礎資格です。VEの考え方やプロセス、機能定義の基本などを習得します。
・VEスペシャリスト(VES)
VEプロジェクトを自ら計画・推進できる実践者向けの資格です。FAST図やコスト評価など、より高度な分析力が求められます。
・CVS(Certified Value Specialist)
VE活動の指導やコンサルティングができる、国際的にも通用するVEの専門家としての最上位資格です。
各資格は研修+試験(筆記・実技)によって取得でき、VE活動を社内に根づかせる際の人材育成プログラムとして活用されています。
参考:VEの資格(公益社団法人日本バリュ-・エンジニアリング協会)
バリューエンジニアリング(VE)は単なるコストダウンではない
バリューエンジニアリング(VE)は、単なるコスト削減の手法ではありません。
その本質は、「機能」と「コスト」の関係を論理的に捉え直し、顧客にとって本当に必要な価値を、最も合理的な方法で実現するという設計思想にあります。
製造業や建設業に限らず、VEは中小企業や自治体、サービス業など幅広い分野で活用されています。必要なのは、VEの考え方を理解し、小さくても確実な一歩を踏み出すことです。
まずは、自社の製品やサービスについて「これは本当に必要な機能か?」「他に合理的な手段はないか?」と問い直してみてください。
その問いこそが、VEの第一歩であり、持続的な価値創造の起点となります。
【注目コンテンツ】
・100年企業のグローリーがMES導入を3年間で全社展開を成功させた秘訣とは
・エンジニアの精鋭部隊が集結した合弁会社「DTダイナミクス」設立で生産性が3倍に。内製化支援と技術移転、成功の秘訣とは
・日本の高スキル人材の活躍の場は世界にある アクセンチュアが「ものづくりを変革する」で描く製造業の未来とは